BY JOSEPH KNITTER
Over the past few years, we’ve seen changes to how people desire and consume fast food. During COVID, when restaurants were shut down for in-person dining and retail grocery stores experienced the onset of food shortages, restaurants quickly pivoted to accommodate additional demand on their drive-through and carry-out services.
- Fighting Fires in Fast-Food Restaurants
- Training in a Fast-Food Restaurant
- What Would You Do? Fast Food Restaurant Fire
- What Building Do You Fear the Most?
Restaurant owners began to rethink their spaces. They realized quickly that they would have a new focus on enhanced technology. This “new” brick-and-mortar restaurant design often had a smaller footprint due to the need for reduced dining areas and the demand for more delivery and carryout, often referred to as DELCO.
Even with all these changes, the food preparation area remains the focus for fire suppression forces. The result of an increased demand for pickup and delivery is an increased need for additional food prep space and additional risk of fire.
Fast Food Is Everywhere
Very few first-due or mutual-aid response areas across the United States are absent of some type of restaurant, with those we consider fast-food spots being the most common and most visible.
In 2021, the United States had an estimated 197,600+ fast-food restaurants, with McDonald’s, Burger King, and the stores of the Yum! Brands (KFC, Taco Bell, and Pizza Hut) accounting for the majority share. While their presence and daily operations usually cause very little concern for the fire service, it’s what happens when they are on fire that raises concerns. Other than those in malls, shared locations, and older locales, most of these establishments are freestanding buildings built with the latest in lightweight, engineered lumber technology and techniques.
Even a small fire in these occupancies can have a tremendous impact on the community. Inevitably, the cascading effects hit the restaurant owners, employees, suppliers, and customers. This creates not only a loss of revenue but often the loss of a community gathering point as well. One restaurant in my community hosts a group of retirees every weekday morning who gather for coffee and stories.
To understand the risks and hazards associated with these buildings and the operational considerations and tactical approaches recommended for fighting fires in them, we must first understand the materials being used in their construction and how they are put together.
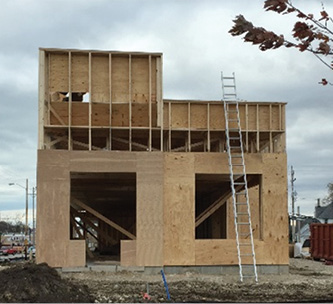
(1) Photos by author.
Engineered Lumber Products
While they’re a big part of present-day construction, engineered lumber products are by no means new to the construction industry. Historical reports show plywood was used in Russia prior to the 20th century. Plywood is often called the original engineered wood product because it was one of the first to be made by bonding together cut or refashioned pieces of wood to form a larger composite unit that is stronger and stiffer than its individual components. Its popularity, however, didn’t gain a stronghold on the American market until being reintroduced in 1905 in Portland, Oregon, as the city prepared to host its Lewis and Clark Centennial Exposition (photo 1).
In the late 1970s and early 1980s, the principles behind the design of plywood gave rise to what has come to be known as oriented strand board (OSB). Instead of solid sheets of veneer, OSB is made of small wood strands that are glued together in cross-laminated layers. Cross-laminating layers of wood veneer is said to improve on the inherent structural advantages of wood by distributing along-the-grain strength of wood in both directions.
While structurally sound under ideal and laboratory test conditions, the performance of engineered lumber products when subjected to high-heat conditions or direct-flame impingement remains questionable. According to the Fire Facts Guide, produced by the Weyerhauser Corporation, “One-dimensional charring tests of structural composite lumber products including LVLs (laminated veneer lumber), PSLs (parallel strand lumber), and LSLs (laminated strand lumber) confirmed that charring of these products in the standard fire-endurance test may be considered comparable with solid wood.” The obvious question is, when was the last time you fought a one-dimensional fire or responded to a report by the proverbial Mrs. Smith, saying that her neighbor’s house was being charred? And they may be considered comparable? I guess that also means that they may NOT be considered comparable.
In a similar publication, Important Fire Safety Information Regarding Fire Rated Building Assemblies and Components of Fire Rated Assemblies (Georgia-Pacific Building Products), several statements remove any question as to the reliability of fire testing. For example, the publication states, “Because actual fires vary both from lab conditions and from fire to fire based on a wide variety of factors … fire tests are not representative of actual fire conditions.”
It also states, “Fire tests do not assess individual materials or products for their fire-resistance characteristics.” And finally, it says, “In the event of an actual fire, you should immediately take any and all action necessary for your safety and the safety of others without regard for any fire rating of any product or assembly.”
It’s about time. Someone who is not in the fire service has finally realized and admitted that products being tested in laboratories are not going to perform the exact same way under real fire conditions.
The number of engineered lumber products in use in today’s building construction industry is vast. From engineered sheet products like plywood and OSB, to floor and roof structures made of truss assemblies and engineered I-joists, to extended overhang and parapet assemblies constructed wholly of trusses, these items are primarily reliant on proper design, construction, and field installation (photo 2).
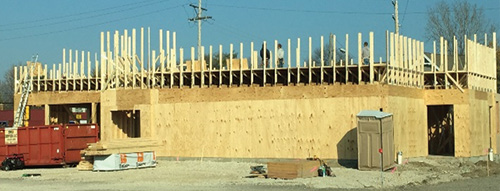
(2)
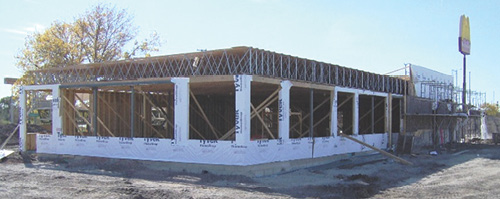
(3)
The Wood Truss
I attended a conference where veteran Miami-Dade (FL) Fire Rescue Captain Bill Gustin stated, “While we no longer have vertical balloon construction, we certainly have horizontal balloon construction.” What he is referring to is the extensive lengths that engineered I-beams and trusses can run without fire-stopping or barriers. I have witnessed installations that ranged from 30 to 40 feet, as shown in photo 3.
In this article, we will concentrate on the simple wood truss. Due to the need to accommodate the variety of roof pitches and location of lumber members, wood trusses are typically custom made. As a result, they often require complex cutting patterns of the wood members prior to manufacture. Each member must fit snugly in place to provide the utmost in strength to fulfill its role as a gravity resistance system (as referred to by the “Ol’ Professor” Frank Brannigan) and support the roof of the building.
Truss design is typically facilitated by a computer design program intended for building components that generate fabrication instructions indicating the size, grade, and precise cutting patterns for each of the chord and web members. Truss design must consider factors including the truss geometry; the loads used in the truss design; the species, size, and grade of all wood members; the truss bearing and uplift requirements; and the truss-member bracing requirements (photo 4).
In addition to these design elements, the type, size, location, and orientation of the gusset or truss connector plates are also indicated in the computer drawings. Once the pieces have been cut and arranged using a template, identical gusset or truss plates are placed on opposing faces at the joints and pressed into the lumber using hydraulic presses or rollers.
Once the pressing of the plates is complete, the trusses are checked for plate-tooth penetration and moved to a storage area. It’s worth noting that manufacturers often provide very specific truss storage instructions and that both delivery services and contractors often ignore said instructions.
It’s fairly common knowledge that trusses are strong in the vertical position, but they can be damaged at the plate joints if bent in the lateral direction. As such, manufacturers recommend the following:
- They should be unloaded in bundles.
- They should be stored on level ground but never in direct contact with the ground.
- They should always be protected from the elements.
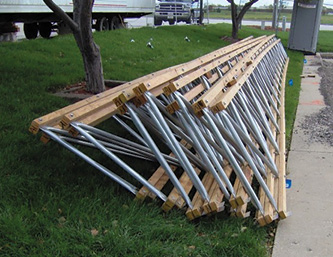
(4)
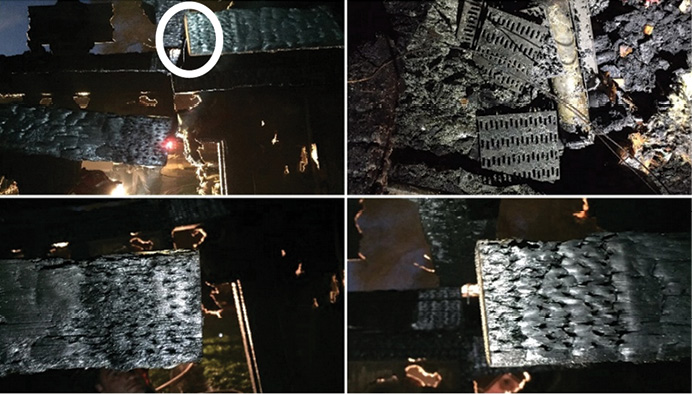
(5)
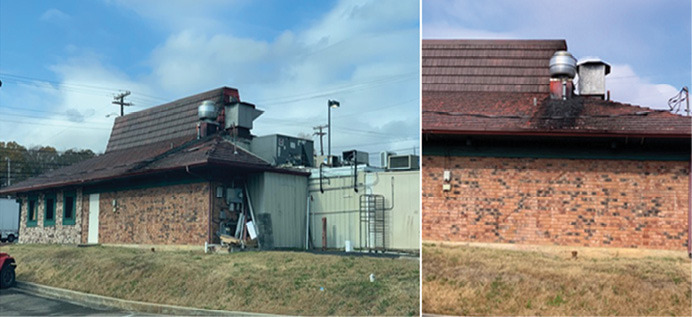
(6)
Connector Plates
One area that deserves more attention is how it’s all held together. Truss connector plates are usually made of galvanized steel and manufactured by high-speed stamping machines that punch out the plate teeth and shear the plate to its required size.
Plate manufacturers are known to carry out a series of tests to determine the design properties for each type of plate, based on its intended use. Many sizes and gauges of connector plates are manufactured. The most common plates use 16-, 18-, or 20-gauge (U.S. standard gauge) sheet steel. Because each connector plate is designed specifically for an intended use, the dimensions of the individual teeth are also specific to the design of the truss. The dimensions are also dependent on the size of the web and chord members and intended structural load to be supported.
Although they’re designed and tested to hold structural components together under ideal laboratory conditions, the question remains: How they will perform and hold up under high-heat and direct-flame impingement conditions? I trust those of us in the fire service know the answer to that question.
Gusset or truss plates are known to fail as they accumulate the heat from the fire, causing pyrolysis around the teeth of the fastener and the eventual disconnect from the wood they are connecting. Once the fastener releases from the truss, gravity takes over and the truss is subject to failure and collapse. And, like a house of cards, once the trusses begin to fail, they continue to do so until there is a catastrophic collapse, resulting from the fact that the support structure is designed as a system. The system depends on all its components to maintain its structural integrity.
Photo 5, taken at a residential garage fire, demonstrates the typical failure of a standard wooden truss assembled using steel gusset or truss plates as fasteners. The “clean” board end (highlighted by the white circle) indicates that the bottom chord of the truss eventually failed and separated, but only after the fire had been extinguished (photo 5, top left). And the truss plates, which appear undamaged, were found in the debris on the floor of the garage (photo 5, top right). Photo 5 bottom left and right clearly show the intrusions where the “teeth” of the steel connector plates were once embedded into the 2-inch × 4-inch members of the bottom chord.
Common Causes of Fast-Food Restaurant Fires
Finally, no article about fires in fast-food restaurants would be complete without at least a brief mention of one of the most common causes of fast-food restaurant fires—cooking and grease buildup. Obviously, the buildup of cooking by-products (grease) on the roof would lead one to believe the housekeeping inside the restaurant would be no different. The roof design of this restaurant leads one to believe it is a former Pizza Hut that has been repurposed, in this case, to a sushi restaurant (photo 6).
Regular inspection and cleaning orders are a must, and proper housekeeping efforts must be continuously encouraged and enforced inside the restaurant. This includes the inspection and cleaning of grease-removal system ductwork and appliances like upblast ventilators.
Opponents of interior fire attack will say, “If there’s no threat to human life, stay OUT!” I, however, am in no way advocating that an interior attack can’t be initiated in these buildings. But I will say that it must be on your terms and conditions and not those of the media, the property owners, or the public. Remember, there is no property worth the life of a firefighter. If all occupants are out of the building and the risk to human life has been removed, a cautious, interior attack, supported by a continuous size-up, can be initiated.
Freestanding buildings constructed with lightweight materials that are occupied as fast-food restaurants are everywhere, and more are going up every day. Good fireground commanders understand how the restaurants are built, how these fires start, how the buildings come apart when attacked by high-heat conditions or direct-flame impingement, and what operational expectations and tactical approaches are appropriate.
Remember: It is easier to justify to a property owner why you went defensive than it is to explain to a grieving family why you didn’t.
JOSEPH KNITTER is a 41-plus-year veteran of the fire service. He retired as chief of the South Milwaukee (WI) Fire Department in 2022, where he served for 37 years. Knitter has an associate degree in fire science and a bachelor’s degree in fire service management. He is a graduate of the Executive Fire Officer Program through the U.S. Fire Administration National Fire Academy. In addition, he is a WI state-certified fire officer II, fire instructor II, and fire inspector, as well as a certified Pro Board incident safety officer. Knitter also previously taught fire certification classes for Milwaukee Area Technical College and incident management for the State of Wisconsin’s division of emergency management. He lectures on instructor development and leadership throughout the area.