By CHRISTOPHER THOMAS
As part of skills development, firefighters have traditionally gotten to know the types of construction they may face. Once, this meant knowing local variations such as the triple-deckers of the Northeast, the row houses of the Middle Atlantic states, and the shotgun houses of New Orleans. More recent variations have spread across much of the country, such as the ranch and Cape Cod styles of single-family houses and garden apartment complexes for multiple dwellings.
- The Fuse 47 Fire: The Dangers of Noncompliant Buildings Under Construction
- Lumberyard in the Sky: Fire Retardant Treated Lumber
- The Roundtable: Lightweight Wood-Frame Mixed Occupancies
Buildings of Today
In this vein, the past 20 years have seen the rise of a new type of multiple dwelling. Like the garden apartment, it is seen nationally due to the national standardization of building codes. It goes by a variety of names. Most call these five-over-ones and podium buildings (photo 1).
These names derive from the fact that the original buildings built in this style could be built to a maximum of five stories of fire-protected wood construction over a one-story concrete podium (photo 2). Confusingly however, not all these buildings rise to their maximum potential height.
Rather than five stories, some may be three or four stories over a one-story base. Further complicating matters is the fact that building codes now allow for a two-story concrete podium, meaning that many five-over-ones are now five-over-twos. Alternatively, some buildings feature a wood-frame structure wrapped around a concrete parking garage. To simplify, and to give this type a readily recognizable name, I am proposing we call this type of structure the millennium box.
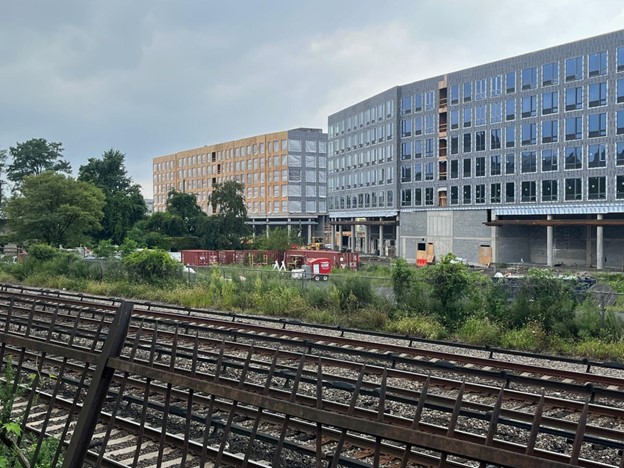
(1) This millennium box features a distinct division between the two-story concrete podium and the wood-frame structure above. The building on the left shows the plywood-covered exterior of a millennium box prior to cladding installation. (Photos by author.)
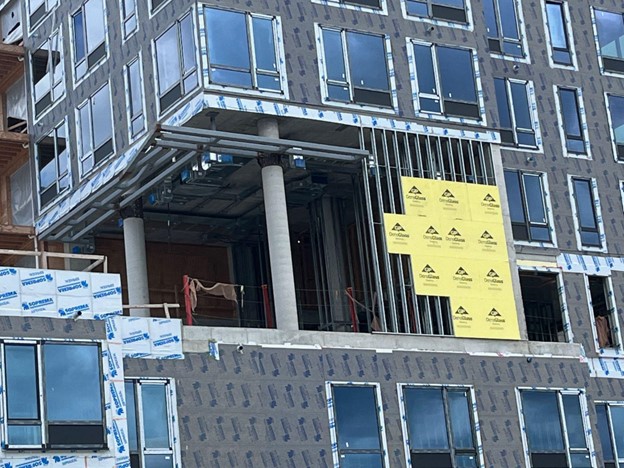
(2) The concrete podium is treated as a separate Type I structure for code purposes. It should only feature fire-retardant materials.
A Construction Challenge
As best as can be found, the millennium box concept dates to 1996. As is often the case, the design arose from the desire to build as big a building as possible, as cheaply as possible, while still complying with code requirements. For builders, this created a problem. Today, the International Building Code (IBC) (as adopted by cities and states) regulates the construction of buildings, including their size, based on the materials they are constructed from. Wood-frame buildings can be built at a lower cost. However, when land costs are relatively high, a higher-density project is needed to offset the land costs.
In this case, the smaller wood-frame buildings allowed by code might not produce enough of a return to justify the project. A building with noncombustible exterior walls is permitted to be larger but costs more to construct. This reduces the returns on the project. The goal was to design a building that could achieve the relatively high density permitted in a noncombustible exterior building but at the price point of a wood-frame building.
From this challenge emerged the millennium box. In an article for Bloomberg News, author Justin Fox traced the roots of the design to an affordable housing project in California.1 According to his retelling, architect Tim Smith was sitting on a beach reading a copy of the building code when he realized that under the code, fire-retardant-treated wood (FRTW) was considered noncombustible. With FRTW for exterior structural elements, developers could build a structure that featured many of the cost advantages of wood with significantly more square footage than would be permitted if the exteriors were constructed of regular lumber.2 Understanding how this works requires a brief examination of how the IBC evaluates types of construction.
Construction Types
The 2021 version of the IBC recognizes five construction types that are defined in Sections 602.2 through 602.5 of the code.3 Here’s an overview of all five construction types recognized by the IBC.
- Types I and II. The podiums that support some millennium boxes are of Type I construction. Types I and II are building construction types where the building elements themselves are noncombustible, with very few exceptions.
- Type III. Traditionally found in older districts, Type III construction features exterior walls of noncombustible construction but allows interior building elements to be constructed of combustible materials. This most often takes the form of a structure with masonry exterior walls and wooden floor and roof joists. Type III buildings commonly have exterior walls of brick, stone, or concrete block.
- Type IV. Type IV construction involves heavy timber, and it is not directly relevant to this article.
- Type V. Type V construction permits interior and exterior structural elements to be made of any material permitted by the code, including wood. Type V construction is the most common type of construction. It is the cheapest and easiest type of structure to construct. For that reason, wood remains the single most popular choice of framing material, being used for 73% of the multifamily units completed in 2022.4 For the builder, however, one of the downsides of Type V construction is that the combustible nature of the interior and exterior components causes the total size and height of the structure to be limited to significantly less than what would be allowed if other materials were used.
How the Millennium Box Fits In
What makes the millennium box permissible is section 602.3 of the IBC. This section allows for the use of fire-treated lumber for exterior components.2 Therefore, using FRTW for the exterior made a wood-frame building legally equivalent to a Type III building with brick exterior walls with zero combustibility.
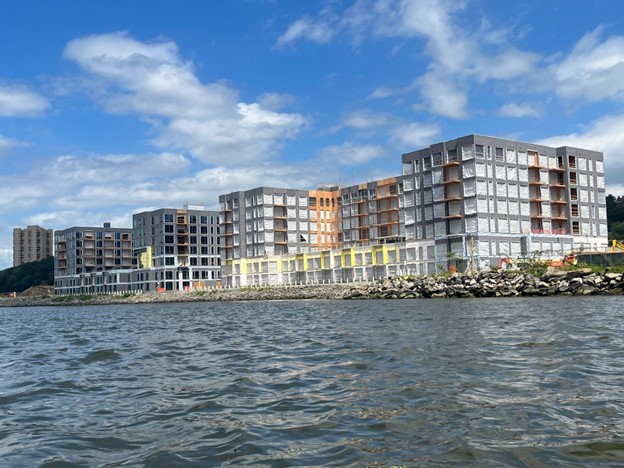
(3) This view demonstrates the scale and proximity of new structures. These two structures are scheduled to be joined by four additional similar buildings on this site. Note the dwelling units located in the concrete podium facing the water.
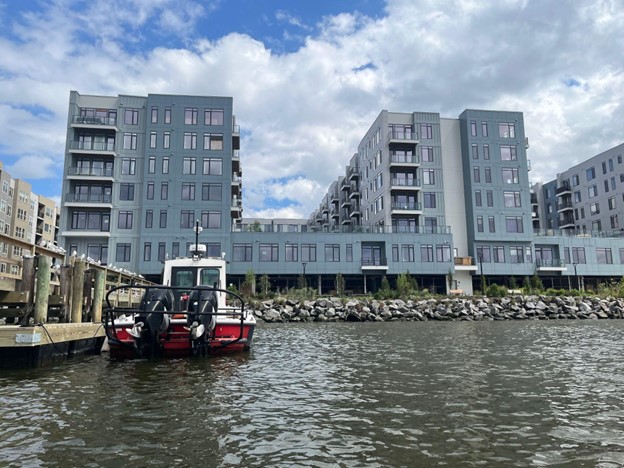
(4) Inaccessibility of courtyard facing units by ladder trucks.
This section thereby allowed the resulting structure to be substantially larger than an ordinary Type V wood-frame structure. In the case of a sprinklered S1-type apartment building (Occupancy Class R-2), the maximum square footage allowed in a Type III-B building is 64,000 square feet, as compared to 28,000 square feet for a comparable Type V-B building.5
Although the exact square footage permitted depends on the specifics of the building, the permitted square footage in a Type III-B building is generally at least double what is allowed in a comparable Type V-B building.
By raising the wood-frame structure over a concrete base, which is often used as a garage, the building can satisfy parking requirements while simultaneously reaping the benefits of lower-cost wood-frame construction. Lower floors may also be used as commercial space, community amenities, or even further housing. The resulting project can reach densities of up to almost 200 units per acre.1
The need to satisfy parking requirements leads to yet another consequence. The relatively expensive concrete base found in these buildings means that expenses are best offset by increasing the scale of the building (photo 3). The original five-over-one building as designed by Tim Smith is approximately 100 units, but new millennium boxes can be significantly larger.
One such structure in my response district has almost 450 units. The combination of a concrete parking garage base with framed apartments above also means that the shape of the wood-frame structure is often not the same as the shape of the base.
Apartments require windows, while the garage does not. The result of this difference is that the residential space is often shaped like a C or an E, with an open courtyard in between (photos 4 and 5). Because this space is elevated above the garage, apparatus access to this space ranges from limited to nonexistent, and ground ladder placement can be difficult at best. A similar issue arises in buildings wrapped around a parking garage, where the garage limits ladder access to apartments facing the garage.
Understanding FRTW
FRTW is wood that has been chemically treated so that its flame spread rating has been reduced. According to the Web site fireresistantwood.org, a trade group representing producers of fire-retardant wood, the formulations “are proprietary, but are mostly comprised of organic or inorganic salts or chemicals.”6 The Web site also notes that there are different types of treatment for wood intended for interior vs. exterior uses.6
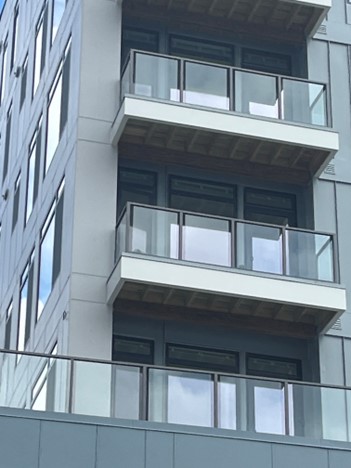
(5) Wood framing supports these decks. Although this is intended to be covered, it could be severely exposed in the event of a propane grill fire. As a general rule, grills are not permitted on decks such as these, but past experience has shown that residents don’t always adhere to codes.
Flame spread ratings are defined in Section 803.1.2 of the IBC.7 This code groups building materials into three classes of flame spread based on the material’s ability to resist combustion when exposed to fire in a specifically designed test scenario. The classes are A, B, and C and are based on a numeric scale. Here’s how their flame spreads break down:
- Class A materials: 0-25.
- Class B materials: 26-75.
- Class C materials: 76-200.
A rating of 0 indicates that a product does not support combustion in any way. Common examples of a 0 fire spread material include brick fiber cement exterior materials. Any material with a fire spread rating from 0-25 is considered a Class A material. All materials in this range are considered functionally equivalent for code purposes. FRTW has been chemically treated to have a Class A rating. Fire-treated wood therefore has significantly reduced combustibility compared to untreated wood, but it does not necessarily have a 0 rating like brick.
Unsurprisingly, untreated wood has significantly higher flame spread ratings. For comparison, ratings for commonly used construction materials include a rating of 90 for Douglas fir and 150 for oriented strand board.
FRTW does not necessarily differ in appearance from untreated wood. It is, however, required by section 2303.2.4 of the IBC to be labeled as fire-retardant wood.2 Specifically, the wood must indicate all of the following:2
- The identification mark of the approving agency.
- Identification of the treating manufacturer.
- The name of the fire-retardant treatment.
- The species of wood treated.
- The flame spread and smoke developed index.
- The method of drying after treatment.
- Conformance with appropriate standards.
Lumber intended to be used on the exterior must be labeled as such. Fire-retardant wood is also available as both lumber and plywood sheets.
One important consideration that has become more prevalent within the category of FRTW is that there are two different, unequal categories of FRTW. The first is pressure-treated FRTW. This is not the same as pressure-treated lumber. It is the result of pressure being used to force the salts or other fire treatments into the core of the wood itself.8 Basically, the process is like the process used to create ordinary pressure-treated lumber, but the chemicals are different.
The second category is topically treated FRTW.9 This is wood that has been surface treated with fire retardant but not pressure treated. Topically treated FRTW has value, particularly for buildings constructed in the wildland urban interface (WUI), but it is not an equivalent, nor a substitute, for pressure-treated FRTW.9
This important distinction has not always been clear to builders and code officials, and this lack of clarity has increased the risk of inadequately treated lumber being used where pressure-treated FRTW would be required.
Another issue that has emerged with FRTW is quality control. Given various treatment processes, it can be difficult for builders and inspectors to determine whether a given product meets the standards required.10 There have also been anecdotal reports of mislabeled lumber being used as FRTW, whether accidentally or intentionally.
Although FRTW construction can allow a building to achieve a Type III designation, the actual construction method does not vary significantly from typical frame construction. Buildings are generally constructed using platform construction.
As is typical in modern construction, lightweight components are a regular feature. The use of fire-retardant wood should, at least theoretically, make the new millennium boxes equal in fire safety to traditional, Type III, ordinary brick-and-joist construction. This, however, means that millennium boxes have many of the same vulnerabilities associated with traditional Type III multiple dwellings.
Key Vulnerabilities
The two most critical vulnerabilities associated with traditional Type III multifamily dwellings are the existence of void spaces and the use of untreated lumber for interior components (photo 6).
Fire spread in void spaces is a well-known risk in firefighting.11 In some newer buildings, this risk has been somewhat mitigated by sprinklers in voids. But, like any system, it must function properly to be effective. Voids are also required to be fire-stopped by code; however, fire-stopping is subject to failure, especially as buildings age and modifications are made.
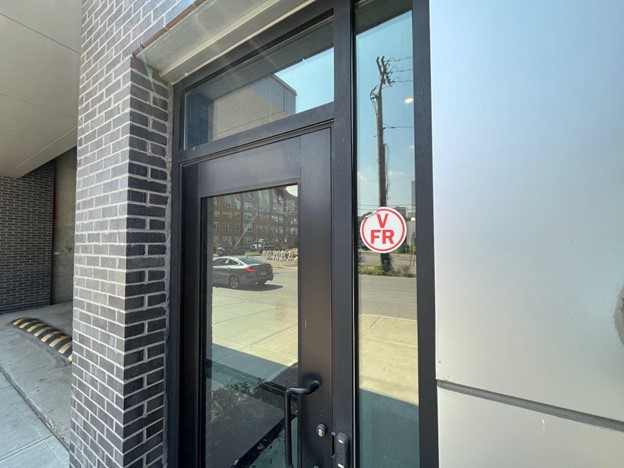
(6) Wood truss indicators for untreated interior structural framing components.
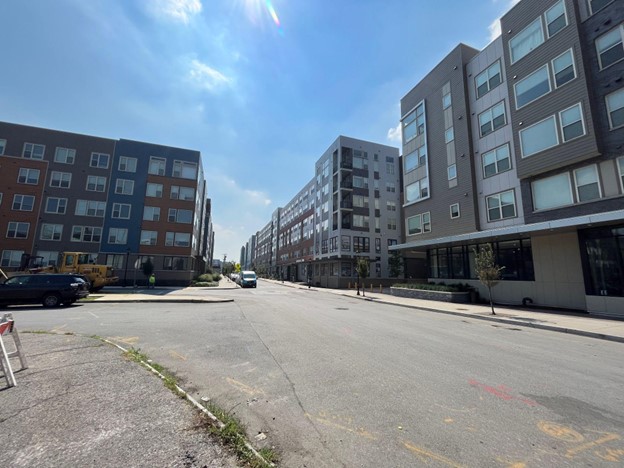
(7) Scale of development in a formerly industrial area. The proximity of large buildings could be problematic at a major fire, especially during the construction phase.
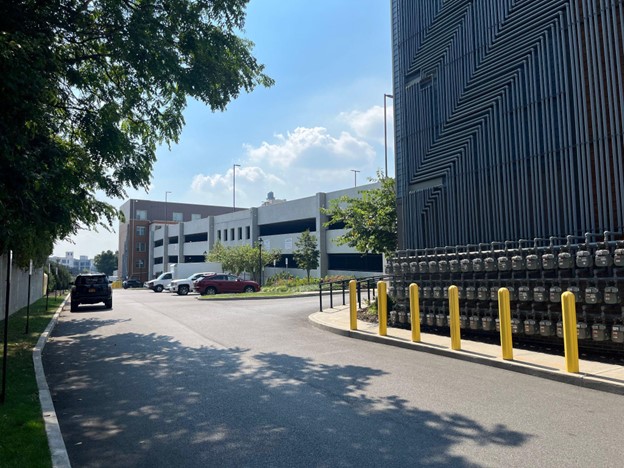
(8) This building wraps around its parking structure. The two wings shown are opposite ends of a U-shaped structure surrounding the parking structure on three sides. This arrangement severely limits the ability of units to ladder apartments facing the parking garage. Also, the bottom right shows gas piping from individual meters to apartments in one half of the building. The other wing has a similar bank of meters.
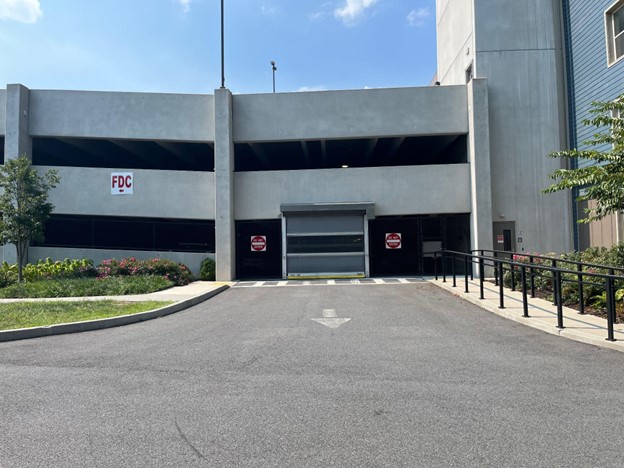
(9) Millennium boxes in redeveloping areas often have security measures that could delay fire department access to emergencies.
Sprinkler requirements are generally covered under NFPA 13.12 Although a discussion of sprinkler code requirements is beyond the scope of this article, it is worth noting that sprinkler requirements vary, and buildings as large as four stories of wood over a one-story concrete podium may be covered under the provisions of the much less restrictive NFPA 13R code.12 NFPA 13R is a sprinkler design schedule intended for use on residential multifamily structures below a specified threshold.
According to the NFPA, it is intended solely to achieve life safety, as compared to the more stringent NFPA 13, which is intended to achieve both life safety and property protection.13 It should not be confused with NFPA 13D, which is the sprinkler design schedule intended to be used in one- and two-family houses. Further, void spaces may or may not be sprinklered in older millennium boxes.
The second problematic issue is the use of untreated lumber for interior structural components. Although fire risk is always present, sprinklers and other fire protection measures such as the use of gypsum drywall have limited fire risk in completed structures. That has not, however, been the case in structures under construction. We’ve seen numerous major fires in millennium boxes under construction, often resulting in the complete destruction of the structure.
One recent example is the May 2023 fire that resulted in the complete destruction of a 239-unit building under construction in Charlotte, NC, and the death of two workers.14
The track record for completed millennium boxes has been better. The 2015 Edgewater Avalon fire in Edgewater, NJ, can be described as a “success” simply because no lives were lost.15 However, this massive fire did destroy the occupied 240-unit complex, displacing more than 500 people. Ironically, it was the site of an earlier millennium box building that had burned while under construction in 2000.15 Although this fire displaced more than 500 residents, there was no loss of life or even significant injuries.
The Challenge of Scale
Safety concerns aside, perhaps the largest problem for the fire service in millennium boxes is simply the scale of the structures (photo 7). Whether buildings of this size are completed or still under construction, fires can be problematic for understaffed or minimally staffed fire departments. Some millennium boxes are in major cities with large fire departments, but these buildings can be found outside of major cities as well. And, as demand for housing continues to exceed supply, these structures are being found in more and more smaller cities as well as in suburban areas.
Due in part to zoning codes and a growing desire for walkability, many of these structures are found close to downtown areas or adjacent to transit stations. Frequently, this means that new construction is also near existing structures. This raises significant concerns regarding the ability of minimally staffed and understaffed fire departments to adequately respond to fires in structures of this size.
These concerns are warranted not only for fire incidents but for other types of emergency incidents as well. A recent water leak in my district involved a broken four-inch supply line that flooded nearly 80 apartments. Although this was a relatively minor incident and many of the tenants were able to remain in their units, it imposed a significant burden on local emergency management. A more critical incident could easily displace hundreds of residents at one time.
Going forward, fire departments and emergency management agencies in districts with millennium box-type construction need to plan for responses that may exceed the traditional parameters they are used to. Districts that may also respond as mutual aid to these buildings should be familiar with what they are expected to do and who they will be working with. The time to begin developing these relationships is now.
As firefighters and fire officers, this leads to a few important considerations, including the following:
Is the fire extinguishable?- Given the scale of new construction, a well-advanced fire in an unfinished millennium box may be inextinguishable for all practical purposes. As interior structural members are not required to be fire treated, and if compartmentalization is not yet in place, the gallons per minute available may not be able to overcome the Btus produced by the fire. This will dictate the strategies and tactics used. Depending on the situation, an early decision to focus on life hazards involving workers and exposure protection may be warranted.
- Careful consideration should also be given to establishing brand patrol units to ensure that secondary fires are not being ignited by embers from the original fire (photos 8 and 9).
- Even a defensive posture at a millennium box fire will require significant resources. Greater alarms or mutual aid should be called early. The large amount of fire and the large areas that will have to be examined for possible fire spread mean that sectoring of the incident and the development of a command staff will be required. Buildings under construction may also be expected to fail quickly, making the role of safety officers critical in incidents of this type.
The Big Picture
Within the fire service, we may have limited ability to affect what types of construction projects are approved in our districts. Large-scale projects such as millennium boxes will require new approaches. And even smaller departments will be required to improve their interoperability and sectoring skills to successfully operate at incidents of this magnitude.
ENDNOTES
1. Fox, Justin, “Why America’s New Apartment Buildings All Look the Same,” Bloomberg News, February 13, 2009. bloom.bg/3sZ37jl.
2. Thompson, Douglas S., “Five -Story Wood Frame Structure Over Podium Slab,” WoodWorks, bit.ly/3sV1aV8.
3. “Chapter 6 Types of Construction: Section 602,” 2021 International Building Code, International Code Council, 2021. https://bit.ly/3Rps5lu.
4. “Highlights of 2022 Characteristics of New Housing,” United States Census Bureau, 2022. bit.ly/3N88HXA.
5. “Table 506.2 Allowable Area Factor,” 2021 International Building Code, International Code Council, 2021. bit.ly/3T1Z00o.
6. “How Fire Retardant Wood Works,” Western Wood Preservers Institute, 2023. bit.ly/46BxIRG.
7. “Chapter 8 Interior Finishes: Section 803.1.2,” 2021 International Building Code, International Code Council, 2021. bit.ly/3GmDMmt.
8. Rhodes, David, “Lumberyard in the Sky,” Fire Engineering, Volume 162, Issue 5, May 1, 2009. bit.ly/3Rl7Kxk.
9. “Wood Fire Treatments: Pressure Treated vs. Topically Applied,” Montana Timber Products, February 24, 2023. bit.ly/47BMOrH.
10. “Best Practice in Fire-Retardant-Treated Wood Code Enforcement,”FRTW, Hoover Wood Treated Products Inc., December 13, 2017. frtw.com/?p=26.
11. Brannigan, Francis L., and Corbett, Glenn P, Brannigan’s Building Construction for the Fire Service, 6th Edition, National Fire Protection Association, 2019.
12 “NFPA 13 vs. NFPA 13R in Podium and Mixed-Use Construction,” National Fire Sprinkler Association (NFSA), November 17, 2020. bit.ly/3RlQR5T.
13 Hart, Jonathan, “Fire Sprinkler Considerations for Podium Construction,” National Fire Protection Association, December 14, 2021. bit.ly/3sV1YJE.
14 Hodgin, Carrie, “Charlotte Firefighters Battling Massive Construction Site Fire,” WXII-12, May 18, 2023. bit.ly/3GksrDq.
15. Mueller, Mark, and Sullivan, S.P., “‘It Was Like Déjà Vu:’ 15 Years Apart, Edgewater Fires Devastate Residents,” NI.com, January 23, 2015. bit.ly/46EacUn.
CHRISTOPHER THOMAS is a 23-year veteran of the fire service. He is an assistant chief with the Yonkers (NY) Fire Department. He is also a fire instructor with the Westchester County Department of Emergency Services in New York. He is a graduate of St. John’s University School of Law and has a master’s degree in security studies from the Center for Homeland Defense and Security at the Naval Postgraduate School.