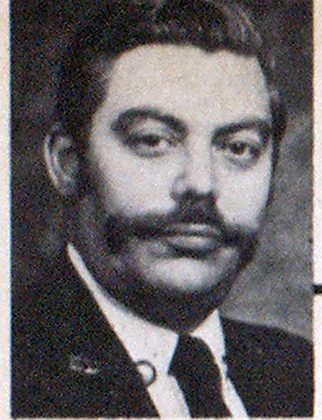
Haz-Mat Risk Assessment
DEPARTMENTS
Chief Warren Isman: ON HAZARDOUS MATERIALS

One of the major issues on hazardous materials facing a fire chief is determining the extent of the problem in his area. The types of chemicals that are used in the community, as well as those that are transported through the community, need to be determined and cataloged. The process of performing this cataloging is known as a hazardous materials risk assessment.
Many fire departments are now jumping on the bandwagon of organizing a hazardous materials response team because it is currently the “in” thing to do. Fire departments with funding difficulties are committing resources to these specialized teams without knowing if a need exists.
Fire service administrators often do not realize the commitments that are necessary when the decision is made to establish a response team. In addition to the very obvious needs of having a response vehicle and control equipment, consideration must be given to the initial training, retraining, maintenance, and the cost of replenishing expendable items.
Before making such a significant commitment, the fire chief must be convinced that there is a sufficient potential for an incident requiring an immediate response from a local team.
Now, what is involved in a risk assessment? First, the various modes of transportation in the community need to be reviewed: road, rail, water, pipeline, and air.
If there are no pipelines in the area, then no further risk analysis of that particular mode of transportation is necessary. If, on the other hand, a major interstate route passes through the district, then truck transportation could present a significant problem. So, a catalog of the modes of hazardous materials transportation needs to be conducted.
The next step in the risk assessment process is to determine the routes used in transporting the material. Pipelines, waterways, and railroads operate in fixed beds, so their locations can be easily mapped. Air routes can be developed from information supplied by the Federal Aviation Administration as well as the local airport authority. Truck routes can be determined by observation and by recording the companies that regularly travel through the community and contacting them to determine the common travel routes.
The third step in the process is to determine the types and quantities of materials that are transported. This involves contacting the various federal agencies that regulate hazardous materials to provide copies of transportation records. In addition, the transportation companies, shippers, and manufacturers should be contacted and asked to provide information on the products moved through the area. In gathering this information from these private companies, an attempt should be made to determine the day of the week and time of day when these products are transported.
Determination of fixed storage and manufacturing locations is the fourth step in the risk analysis process. This step can be accomplished through a review of the pre-planning records, zoning applications, and construction permits in the jurisdiction.
The next step is to determine the specific chemicals that are manufactured, used, stored, disposed of, or transported through the community. In addition to the chemical name, the fire department will need to know the quantities, storage or transportation containers, as well as any built-in protection systems.
The sixth step in the process is to establish the specific hazards associated with each of the identified chemicals. This involves researching the products through information supplied by the manufacturer, reference texts, and chemical abstract services which can be accessed by computer. One of the major sources of information is the material safety data sheets that are prepared by every manufacturer for each chemical. These sheets provide medical information, protective clothing requirements, and information on handling fires and spills.
Now, as the seventh step, a scenario for potential types of incidents needs to be developed. How close to the railroad tracks is a hospital, nursing home, retirement community, apartment building, or school? What would happen if a truck with one particular chemical overturns in various locations in the community? Are there any areas where an accident would seriously impact the environment, such as near reservoirs or rivers?
With the potential types of incidents identified, the eighth step is to make a determination of the probability of an incident occurring in these locations. This determination is made using past local data for accidents, as well as national data on the increases or decreases in specific types of incidents. Federal records, newspaper articles, and discussions with the shippers or manufacturers are good data sources.
Obviously, these eight steps are easier to write about than accomplish. There is not a great deal of information available on specific products moving through any given area. However, regulations to provide such information have been adopted by some states.
The cost of conducting such a risk analysis must also be considered. Because there is little information already available, it will take a great deal of effort and commitment to satisfactorily complete the study. However, these drawbacks should not deter the fire department from undertaking this risk analysis before deciding to establish a hazardous materials response team. A rough analysis of the problems can be done quickly and without great cost.
In the U.S. Department of Transportation’s publication “Community Teamwork: Working Together to Promote Hazardous Materials Transportation Safety,” the following steps are recommended for doing a risk assessment on a limited budget:
- Focus on general classes of materials rather than on specific chemicals.
- Identify the major transportation corridors rather than specific streets.
- Describe the risk in general terms such as low, moderate, or high rather than in specific terms.
- Seek local industry’ support.
- Incorporate the hazard identification program in inspections.
- Next month, I will again focus on risk assessment with a discussion of the sources of information on hazardous materials movement through your area.