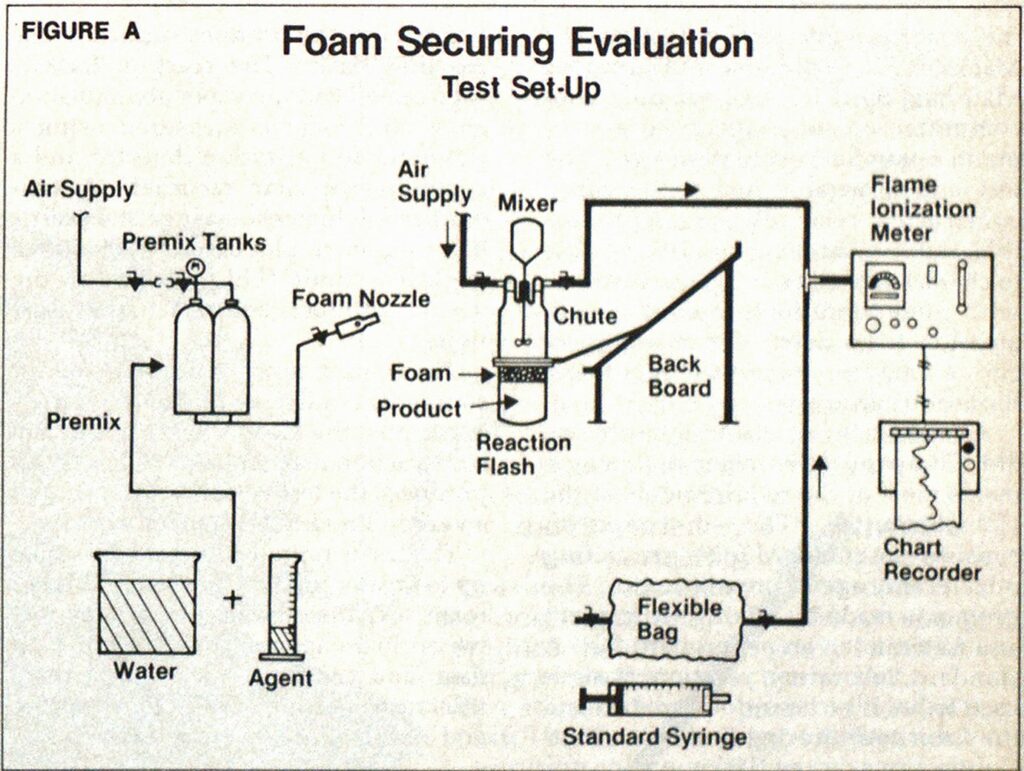
Evaluation Test for Foam Agent Effectiveness
EXTINGUISHING AGENTS
A simple testing method is proving a viable means of calculating the needed foam depth and application time to secure a hazardous material spill or vapor leak.
There are 300-billion pounds of hazardous materials manufactured each year, and each year thousands of spills occur on both land and water.
The problems of hazardous material spills have been characterized by the hundreds of statistics available on the subject. Although the statistics are sometimes contradictory, they do, when combined with the attention given to hazardous material procedures in fire and safety publications, point out the immensity of the problem.
Of the spills occurring, 82% happen during transportation and a large percentage are due to equipment malfunction. Spills occur approximately five to six times more frequently than fire incidents. The ability of mechanical firefighting foams to extinguish flammable liquid fires by means of vapor suppression leads to their logical use in the mitigation of vapors from hazardous material spills.
The use of foams on hazardous material spills reduces the chance of ignition during cleanup operations, reduces the toxic effects of the vapors on response personnel, and reduces the environmental impact of the spill. Many standards writing organizations have recognized these abilities of foam agents and have written general recommendations for the use of foams on hazardous material spills. These recommendations, however, generally fall short of the needed details because of a lack of specific information in the area of concern. What’s needed is a standard method to evaluate different foam agents and to gather predictive data.
Handling a hazardous material spill incident is complicated and dangerous. A great number of factors to be considered are well-documented and include:

- hazardous product identification
- evacuation
- command and responsibility
- logistics
- containment
- decontamination
- cleanup.
We are concerned here with a small part of the overall problem, that of securing the spill from possible ignition, reignition, and vapor suppression both during incident control and cleanup. The responsibility for these phases of the problem usually rests with the fire company that handles initial response duties. If these crews are to effectively secure the spill using foam, they must consider several factors:
- product nature
- spill size
- spill depth
- foam agent to use
- foam expansion
- rate of application
- application time
- foam depth for various securing times
- ambient condition effects
- available foam equipment.
With this information, the municipal crews can make an effective attack on the spill situation using the same materials and equipment with which they commonly fight flammable liquid fires. Any test data should ideally be consistent with the handline equipment used by municipal departments.
Description of test
To answer the above considerations and to supply data on various foam agents, the American Society for Testing and Materials F20 Committee on Hazardous Materials Spill Control set up a subcommittee on foam agents to recommend a standard evaluation test. The test and apparatus had to be easily constructed, relatively safe, reproducible, stable to ambient conditions, able to characterize all foam agents, correlate with field conditions, and, above all, measure foam depth versus vapor securing time for various foam agents and hazardous products.


A small scale test was designed by the 3M Company (see schematic) which meets most of the requirements of the F20 Committee. The test equipment consists of a standard foam generating nozzle and agent premix tank. The premix is made by mixing foam agent and water in the proper proportions. A standard laboratory reaction flask is used to hold the hazardous product and the foam cover during evaluation tests. Connections on the flask top allow for air flow across the foam surface, a stirrer for wind stimulation along with vapor/air mixing and a glass rod penetrator for foam blanket disruption. The total apparatus uses a foam chute to direct the foam stream from the backboard onto the product surface in the reaction flask. The reaction flask is then sealed and the vapor accumulation above the foam is measured using a Davis flame ionization detector and a common strip chart recorder. A standardized volumetric syringe and plastic bag are used to plot baseline 20% lower explosive limit (LEL) levels for the various products before actual evaluations.
The equipment is constructed of standard, readily available laboratory apparatus; the glass and stainless steel construction makes it adaptable to most products; the test vessel is closed and in a vented hood for enhanced safety.
The test is reproducible; can be scaled up to greater product depths and higher foam expansions; differentiates between foam agents; correlates to field data; and can be used to study foam thickness, product depth, wind speed, and simulated foam entry variables.
Test results
The early data gathered using this standard test method indicated that the test was capable of differentiating between many variables found in the field. Variables such as temperature and wind speed could be studied. For these tests, 70°F and simulated 1 mph wind velocity were chosen as best representing field conditions. In the field, higher temperatures would result in more severe vaporization, and higher wind conditions would tend to disperse vapor more readily.
Tests comparing protein foam (PF) to aqueous film forming foam (AFFF) on undisturbed spills showed the advantages of the vapor sealing aqueous film on water insoluble hydrocarbons (graph 1). Also, personnel entry into the foam blanket or other foam disruption was simulated by piercing the foam with a glass rod. This showed the advantages of the fluid AFFF over the less mobile PF (graph 2). Comparisons between the newer polymer-based alcohol type concentrate (ATC) foams showed that they performed similarly to AFFF on undisturbed and disturbed water insoluble hydrocarbons (graphs 3 and 4).
The use of the ATC foams on polar solvents (which are water soluble) indicates acceptable performance, but there is faster foam destruction on polar solvents than there is on hydrocarbons as would be expected with a water soluble product. The effect of disturbing the foam in puncture tests demonstrates the importance of not entering or disrupting foam blankets (graph 5) used to mitigate spill emergencies of polar solvents.


After these preliminary evaluations were completed, the test method was used to fully characterize one particular foam agent. This agent was one of the ATC foams since these agents have the widest application to both water soluble (polar solvents) and insoluble liquid (hydrocarbons) hazards. The products studied were all flammable liquids (similar results are expected with less flammable but more toxic products).

The test data gathered demonstrated that the depth of foam applied to the spill’s surface has a straight line relationship when plotted versus the securing time for vapor/air to reach the 20% LEL level for the different flammable liquids (graph 6). The data also showed a very close correlation between the 20% LEL securing time and large scale field tests of 10 square feet and 50 square feet. These large scale tests also confirmed that simple reapplication of a similar amount of foam gives a similar and equivalent securing time as that achieved with the primary application of foam.
When combining the straight line relationships of foam depth to securing time (as seen in graph 6) with the graph depicting foam generation by air-aspirating foam handline equipment (graph 7) firefighters can calculate the depth of foam required to secure a given product and the time a standard foam handline nozzle must be used to reach this depth on any given size spill. These predictive graphs, of course, give guidelines for securing time that should be verified by the use of an LEL or flammable vapor detector in the field.
General predictive method
The hazardous materials studied in this program are able to be grouped into three distinct areas when the vapor pressure of each is plotted, versus the water solubility of the various products. The fact that three distinct groups are evident (graph 8) suggests that a general predictive method may exist for products other than those tested directly.
With non-polar liquids, the polymer film does not form as it does with polar products, leading to faster penetration of the vapors into the foam.


