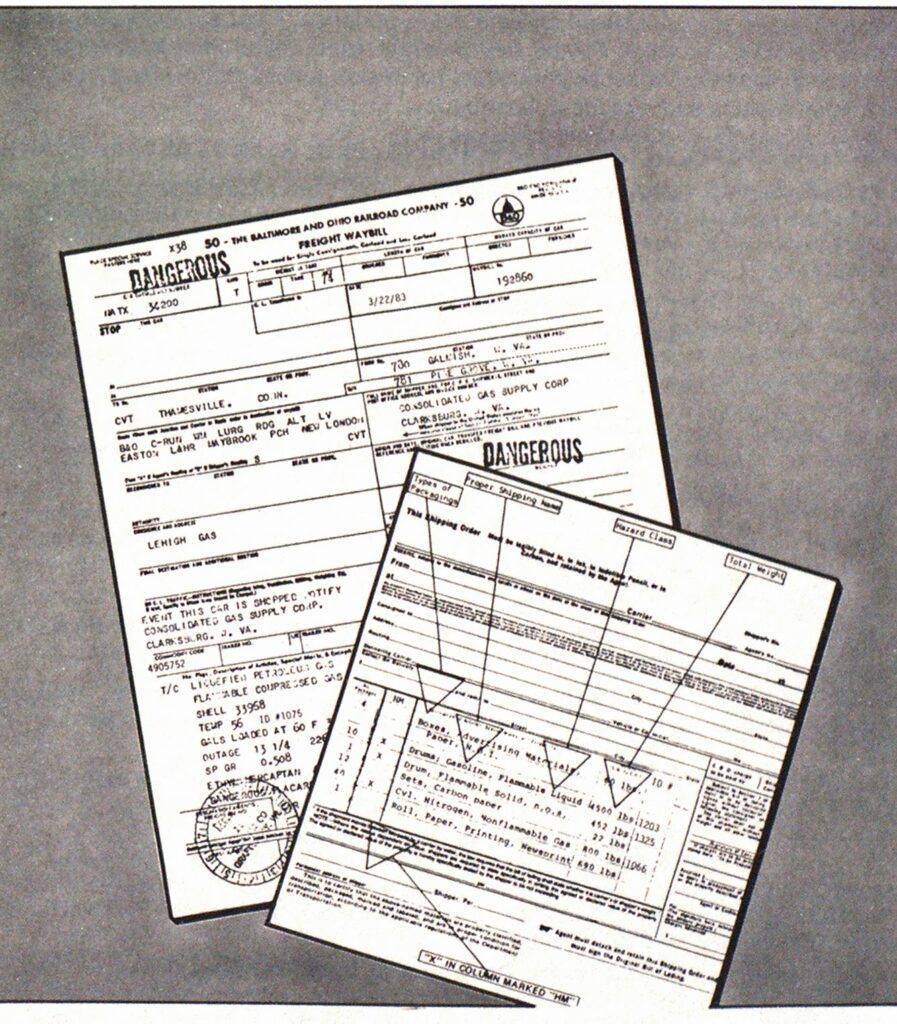
CONTROLLING HAZARDOUS MATERIALS INCIDENTS DURING TRANSPORTATION
HAZARDOUS MATERIALS
This article is the first of a series that will deal with the controlling of hazardous materials incidents. Since transportation is one of the most significant stages, this first article will deal with the general problems encountered during transportation incidents. Then, future articles will deal with the specific problems of the various modes of transportation, including rail, truck, pipeline, barge or boat, and air.
HIGHWAY TRANSPORTATION
A large number of trucks move hazardous goods across the United States. Under U.S. Department of Transportation regulations, these trucks must be placarded under certain circumstances which depend upon the hazard and quantity of the product. Trucks do not indicate when they are empty of product and, therefore, the same placard is used whether the truck is full or empty. Also, it must be remembered that for most categories of chemicals, only 1000 pounds or more of the material must be placarded.
Under the new placarding system, if there is bulk transportation of a specific product, the placard will contain a 4-digit number and may identify the product. Some 4-digit numbers are generic in nature and do not provide the name of the specific chemical.
Shipping papers on the truck are known as the bills of lading and are kept in the cab by the driver. When the driver leaves the cab, the shipping documents are kept on the seat or in a pocket on the door. The hazard category, the 4-digit identification number, and the product shipping name will be included in the bill of lading.
Planning for highway incidents involves:
- Development of a resource list containing information on available containment equipment and special extinguishing equipment.
- Location of water supply sources within relay distances of the hose lines.
- Purchase of topography maps from the U.S. Coast and Geodetic Survey.
- Location of access routes, particularly roads with limited interchanges or impossible dividers.
- Development of a list of materials that commonly move through the community by truck.
- Conducting drills around the various types of trucks which move through the community.
- Preparation of sewer maps and drainage locations.
RAIL TRANSPORTATION
Many products are shipped by rail, with one of the major causes of accidents being derailment. Because of the forces involved during the derailment, the cars and containers become breached and their contents released. However, there are other reasons for train accidents.
Rail transportation of hazardous materials requires that a placard be displayed on all four sides of the rail car. As in truck transportation, the general hazard placard is used, except for bulk transportation, which also required a 4-digit identification number.
The shipping document for rail transportation is known as a waybill. There is one waybill for each rail car and it indicates the product identification number and general hazard. In addition, some railroads show a number known as the Standard Transportation Commodity Code (STCC). This number, which always has 49 as its first two digits will produce a suggested action for a spill, leak or fire when provided to either CHEMTREC or the railroad.
Preplanning for a rail incident involves:
- Development of a telephone list for the rail yards that send and receive trains. Include the closest dispatcher for the railroads, the main office for the railroads and the number to call for information on the train.
- Development of a survey form to determine the chemicals carried by rail through the area.
- Location of water supplies along the railroad right-of-way.
- Preparation of sewer maps for the area.
- Development of access routes to all portions of the trackage in the area.
- Purchase of topography maps for the area surrounding the tracks.
- Conducting drills or training on the types of rail cars, their safety devices and the spill control devices that are available.
- Development of a resource list of equipment and personnel needed to control a rail incident.
PIPELINES
The pipeline system is a mostly underground network that carries over 25 percent of the total freight tonnage. Pipelines carry many products including oil, refined petroleum products, natural gas, liquefied petroleum gas, as well as liquid fertilizers such as anhydrous ammonia. In fact, pipelines carrying refined petroleum products could carry at any given moment kerosine, leaded gasoline or jet fuel.
Should a pipeline break occur, the product being carried at that moment is a major factor in the handling of the incident. For example, the higher the flash point of the liquid, the less chance of ignition. As a result, the specific product needs to be determined very quickly.
There are no shipping papers, as such, for the pipelines. The only way to determine what is being carried in a petroleum pipeline is to contact the pipeline company. In addition to planning the fire department’s response area, the products carried in designated pipelines can be determined in advance. The locations of pipelines in an area can be determined by the markings at major road crossings or at railroad crossings.
Planning for pipeline incidents involves:
- Development of a telephone list for all of the pipeline companies in the area, including the distributors of natural gas to homes and commercial establishments.

- Development of pipeline location maps showing adjacent exposures.
- Location of access to the pipeline’s entire right-of-way.
- Purchase of a topography map for the pipeline’s right-of-way.
- Location of water supply along the pipeline’s right-of-way.
- Development of various approach routes in case the rupture blocks the normal route.
- Conducting of drills and training on a simulated pipeline leak in area of high hazard.
WATER TRANSPORTATION
Water transportation involves the movement of hazardous materials by barges, tankers, freighters and container ships. Problems arise at major cities on waterways where these ships dock as well as communities adjacent to the waterways that are endangered by a spill, leak or fire.
The difficulties of handling a water transportation incident arise from the following:
- Flammable products flow downstream and can be ignited far from the original site.
- A fire can flow downstream and ignite exposures alongside the waterway as well as other exposures in the waterway (ships, docks and bridges).
- Difficulty in reaching the incident ei-
- ther because it is away from shore or is inaccessible on board a ship.
- Difficulty in controlling the spill or leak.
- Language problem if the crew members do not speak English.
- Large quantities of the product that are contained in the vessel.
- Movement of a vapor cloud which is heavier than air along a river valley.
The shipping documents for vessels are kept by the master of the vessel on the bridge or in the pilot house. These documents are known as the dangerous cargo manifests and contain the name of the product as well as its location on board the vessel.
Another warning device is used on unmanned barges. In this instance a cargo information card, detailing the hazards of the specific product being carried, is placed on the barge near a warning sign that indicates the barge is carrying dangerous cargo. In addition, the dangerous cargo manifests and another copy of the cargo information card are carried in the pilot house of the tow vessel.
Planning for a water incident should include.
- Preparation of maps for any dock areas, including the location of any built-in fire protection systems and water supply systems.
- Purchase of topography maps showing the water systems in the area.
- Preparation of maps of the shoreline showing all exposures.
- Development of a telephone list for all of the shipping companies using the waterway.
The Magnitude of Risk
The 1981 National Transportation Safety Board (NTSB) Annual Report provided the following facts which are of interest:
- The interstate highway system is 42,000 miles long.
- There are 450 individual railroads in the United States.
- There are 1.8 million railroad cars and locomotives.
- There are 63 U S. scheduled airlines.
- There are 2600 jet aircraft.
- There are over 211,000 private and business aircraft.
- A total of 2 billion tons of product move through the nation’s pipelines in a year.
- There are over 500 ships in the U S. merchant fleet and many of foreign registry.
- Development of a telephone list for all of the federal, state and local agencies who can supply information and assistance.
- Development of a resource list of personnel and equipment that can be supplied to help control and contain the incident.
- Development of a standard words list in the languages of the crews that staff the vessels.
- Development of a list of the vessels, their size, owners, and crew and passenger size that regularly use the port facility.
- Development of construction crosssection drawings of the vessels that regularly use the port facility.
- Development of a list of all the onboard fire suppression and alerting systems.
AIR TRANSPORTATION
The air transportation of hazardous materials can occur on small planes and commercial freight carriers, as well as on passenger-carrying planes. The movement of hazardous materials by air is very closely regulated by the Department of Transportation, Materials Transportation Bureau (MTB). Areas that are regulated include the size and quantity that can be carried on different types of planes and packaging requirements.
Aircraft incidents with hazardous materials can occur at the freight/baggage facility of an airport, at the plane itself while on the ground, or at an aircraft crash site. The location of potential incidents will determine the type of planning that must be done.
Obviously, the placarding regulations which apply to trucks and trains would be impossible for transportation by air. However, placards are applied to the large baggage containers which are used on airplanes. Both at an incident at the airport as well as at one offsite, the placards may be visible and give a clue to the presence of a hazardous material.
However, the specific commodities being carried on an aircraft and which are being shipped as freight are listed on the airbill. This document is carried by the pilot in the cockpit, with a record also being retained at the airport shipping point.
In an off-site crash, locating the shipping documents may be impossible. In this case, the airport from which the plane left must be contacted to determine the commodities being carried as freight.
On passenger-carrying aircraft there is no listing of the materials being checked as baggage. As a result, hazardous materials, even though not legally allowed, will be found in the baggage.
For these reasons hazardous materials must be suspected at all crash sites, and personnel working at the site should continue to wear full protective clothing.
Fire departments with small municipal or private airports must also prepare for handling hazardous materials incidents. In particular, etiologic (biomedical) agents and radioactive materials are carried on small planes which could use these airports. Also, other small quantities of hazardous materials can be carried, so the fire department must make preparations for handling these types of incidents.
An on-site incident involving a military aircraft will be secured and handled directly by the military personnel. However, at an off-site crash, it may be some time before the military personnel arrive on the scene. In this instance the local fire department must be able to recognize and deal with the fact that ordnance may be on the plane.
Planning for an air transportation incident requires:
- Preparation of a list of small, municipal, commercial or military airports in the general vicinity of the fire department.
- Preparation of a list of hazardous commodities which are commonly shipped through these nearby airports.
- Development of a resource list of nearby airport freight handlers and freight haulers who can provide information on the commodities being carried. Location of water supplies in the vicinity of the airport.
- Development of access routes to areas surrounding the airport.
- Purchase of topography maps for the areas surrounding the airport.
- Conducting drills or training on the types of aircraft using the local airport.
Summary
Successful handling of a hazardous materials transportation incident involves a great deal of planning on the part of the fire service. Sitting back and waiting for the incident to occur will result in mistakes, injuries to the public safety personnel who respond, and needless exposure to the general public. As a result, the fire department’s development of hazardous materials response plans are absolutely essential.
Planning by itself is not sufficient to ensure that a department is ready to respond on a hazardous materials incident. Once the plans have been developed, drills and training must be conducted on a regular basis. After each training session, the activities must be critiqued and the plans revised.
Critiques must also be conducted after actual hazardous materials incidents. Then the plans can also be reviewed and revised to reflect the most current information. □ □