An alarm ringing at a commercial bakery in New Haven, Connecticut, highlighted the need for a comprehensive review of our response plan to this facility. The first-due engine was investigating a fire alarm sounding because of a water leak in January; they smelled a strong odor of ammonia. Crews ensured no one was in the building and evacuated to the outside. The truck officer on the alarm called for more resources and a hazmat response. As this call unfolded, there were tangible lessons at each stage of the event that you can apply to your next response.
Hazardous material (hazmat) response takes more than just looking up chemicals in a computer program and in the U.S. Department of Transportation Emergency Response Guidebook (ERG). Although these are great tools, they don’t have all the answers. Successfully mitigating a hazardous release takes training, skills, and knowledge. Some knowledge comes from preplanning and having the information available. The first time you are at a building should not be at a hazmat release; you must absolutely know what hazards are in your first-due area.
Establish Command
The incident commander (IC) established command and announced the location of the incident command post (ICP). In choosing an ICP location, ensure that it is upwind and offers a good field of vision. Note if the facility has a windsock or a flag on a pole that can aid in determining wind direction and speed, or dispatch may be able to provide that data.
RELATED
ANHYDROUS AMMONIA TRAIN DERAILMENT
Not every IC is comfortable mitigating a hazmat incident; that’s all right as long as you assign competent personnel to critical positions. The Occupational Safety and Health Administration (OSHA) requires that a hazmat incident IC be trained to the operational level. After you have addressed life safety, accounted for all civilians, and conducted primary searches to the extent allowable in turnout gear, transition from the operational mode of rescue to the technician mode of mitigation. Appoint a safety officer who has a background in hazmat incidents.
The System
Once you learn what specific hazmat your incident involves, develop an incident action plan (IAP). If ammonia has been identified at a fixed facility, understand the chemical’s physical state and how the system that uses it operates, which enables you to make sound tactical decisions during an incident. It may be stored as a compressed gas, a compressed liquefied gas, or a gas in solution.
Next, determine if the piping system is a closed loop system (e.g., a refrigeration system) or if the ammonia is consumed during an industrial process. If the ammonia is consumed, there is a greater risk of release. The more humans interact with a system (open and close valves or make and break hose connections), the more likely an accident is. We will focus on anhydrous ammonia (without water/not in solution) that is a compressed liquefied gas in a closed-loop refrigeration system.
Anhydrous ammonia absorbs a tremendous amount of heat when it converts from a liquid to a gas, which is why it is used in refrigerant systems. Refrigerant grade anhydrous ammonia is a clear, colorless liquid or gas, free from visible impurities. It is at least 99.95-percent pure ammonia. It cannot have more than 33 parts per million (ppm) of water and no more than 2 ppm of oil. Preserving the ammonia’s purity is essential to ensure proper refrigeration system function.
Impurities can be introduced to the system during installation if done improperly or during recharging or repairs through bad valve stem packings or other component failures. These impurities can cause a failure to the piping. Because of ammonia’s low boiling point, if water is accidentally introduced, the water will freeze and expand, causing pipes to crack. If there are more than a few ppm of oxygen in liquid ammonia or a few thousand ppm of oxygen in gaseous ammonia, it can promote stress corrosion cracking in steels, which may result in a component failure or catastrophic failure of bulk storage vessels.
Additionally, if the compressor system fails to shut down, it can cause excess pressure in the system, activating the system pressure relief valve. Using copper, zinc, or many other metal alloys that will react with ammonia in the system will result in a failure. This reaction is exacerbated if moisture is present.
Once you have identified the presence of an anhydrous ammonia refrigerant system, your preplan should include the following:
- Facility representative 24-hour contact information.
- System maintenance personnel 24-hour contact information.
- System size, generally in pounds of product.
- System diagram.
- Alarm system (if present) and type.
- Detection (qualification type only indicates the presence of ammonia).
- Measurement (quantification type, generally displays the ammonia concentration in ppm).
- Compressor electrical disconnect locations.
- Piping isolation valve locations.
- Emergency dump capabilities, if present.
A great resource for preplanning anhydrous ammonia emergencies in your jurisdiction is the online TRANSCAER Anhydrous Ammonia Safety Training course at https://www.transcaer.com/training/online-training-courses/anhydrous-ammonia-safety-training#emergency-response.
Response
Operate just as you were trained—the awareness level precedes the operations level and the operations level precedes the technician level. Once on scene, use your awareness skills, which are what save responders. If your eyes and respiratory tract are burning, you are a victim, not part of the solution to the emergency.
- Speak with company representatives; are all employees accounted for?
- Is there an alarm system?
- Where is the alarm sensor located?
- Does the sensor quantify the concentrations of anhydrous ammonia present?
- Is there a vapor cloud?
- A vapor cloud will be present with a liquid or high-volume vapor release. However, in an arid region, this may not be a reliable indicator.
- If the release is a low-volume vapor release, a vapor cloud likely will not be present. However, if the release is confined to a room in the facility, it may still quickly reach immediately dangerous to life or health (IDLH) levels.
- Listen for the sound of escaping gas.
Once the awareness skills have identified a release of anhydrous ammonia, set up your isolation zone upwind from the hazard. Though the ERG is not intended for fixed facilities with vessels that are not in transport, the information can be useful. When directed to the ERG Initial Isolation and Protective Distances Table, use the portion of the chart that is closest to the volume of the system at your incident. Most times, because of size similarity, use the chart for agricultural nurse tanks (Table 1).
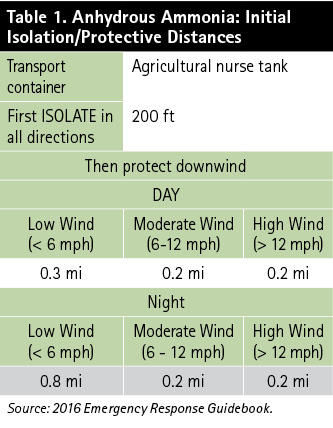
Operational Skills
Life safety is always the first priority. Know how to ensure your safety while operating in turnout gear, know how to use the correct metering devices and detection papers, and have a plan for an aggressive primary search and emergency decontamination of a victim. First-due companies must be trained in civilian rescue at hazmat emergencies, an operational level skill in which all firefighters must become proficient.
On arrival, firefighters are dressed in turnout gear, which is a nonencapsulated splash protective garment that provides protection against incidental splashes and fire. Generally, first-due companies do not have the luxury of a chemical vapor protective garment (i.e., Level A). You must know the difference between the entry for rescue and the entry for technician level skills. You also must be able to determine if civilians are in peril at every hazmat event.
Sometimes, responders must perform a primary search without any chemical research. Knowing the chemical’s name and researching its applicable chemical and physical properties are not essential for the rescue entry. Using and trusting your equipment (turnout gear and meters/detection) coupled with knowing when to discontinue rescue and retreat to a safe location ensure your protection from the hazards. Being properly equipped means operating in turnout gear with self-contained breathing apparatus (SCBA) with the face piece on your face using a four-gas meter, pH paper (wet and dry), fluorine paper and potassium iodide (oxidizer) (wet and dry), a thermal imaging camera (TIC), and a gamma radiation pager. Each item confirms that a responder is operating in a safe atmosphere or should discontinue efforts because the atmosphere is hostile. This article primarily concerns the combustible gas indicator [flammability/lower explosive limit (LEL) sensor], pH paper, and the TIC.
- If the LEL sensor indicates a flammable atmosphere, discontinue efforts. Follow your department’s standard operating procedures (SOPs) for LEL action levels. However, if you are indoors and not at the source, any indication on the LEL sensor should require an automatic withdrawal because it is very possible the gas is in the flammable range, somewhere between you and the source.
- The pH paper detects the corrosive aspect of ammonia. For ammonia, dry pH paper will have a colorimetric change to a greenish/blueish hue well before there is a risk to skin. With wet paper, the change will be a deeper blue. If either occurs, withdraw to a safe area.
- The TIC will indicate a temperature change. A release of a liquefied gas or gaseous product from a failed container or system component will be observed as a decrease in temperature (black or blue, depending on your TIC). If you observe an increase in temperature (white or red, depending on your TIC), the failure is a result of a chemical reaction rather than a failed container or component; withdraw immediately. It is unknown if the release point opening is large enough to keep up with the possibility of continued increasing pressure and volume in an already weakened system.
- Move quickly but cautiously while observing your detection equipment.
- If there is a known victim and the LEL sensor or pH paper indicates an unsafe atmosphere, consider changing the atmosphere with positive pressure ventilation (PPV) and reattempt the rescue efforts. You must be absolutely sure that the venting ammonia is not impacting other people. When making the second rescue attempt, follow the above guidance.
Technician Level
The technician level skills are completed as the incident dictates. You must coordinate closely with those in the hot zone and the ICP. The entire New Haven (CT) Fire Department is trained to the hazmat operational level. Additionally, it operates a technician level hazmat response team (HMRT) that is part of Special Operations Command.
Working with Outside Agencies
Early notification of outside agencies and outside resources is critical to minimize the lead time needed for these resources and technical experts to arrive on scene. Some notifications are dictated by law, usually by your state department of environmental protection. Transitioning from a single incident command structure to a unified command structure with all the stakeholders is crucial with large-scale or high-risk hazmat incidents.
State Emergency Response Coordinators
In Connecticut, the Department of Energy and Environmental Protection Emergency Response Unit (DEEP ERU) represents the state in petroleum, chemical, and weapons of mass destruction (WMD) hazmat emergencies. The DEEP ERU is a Type I HMRT and will assist with entry and release mitigation and work with the responsible party to begin remediation. If the responsible party is unknown or is unable or unwilling to hire an environmental contractor for chemical remediation, the DEEP can provide an environmental contractor when needed and will seek cost recovery from the responsible party. In Connecticut, DEEP is also a part of the State Emergency Response Commission (SERC), which can provide additional assistance in determining the size of the anhydrous ammonia system if the facility has not appropriately coordinated with the Local Emergency Planning Committee (LEPC) but has submitted the required Tier II state reporting.
Additional on-scene capabilities include a mobile forward command post with a weather station, satellite communications linking to the state Emergency Operations Center, drone surveillance with wireless metering capability, AreaRAE© real-time plume modeling coupled with CAMEO and a mobile chemistry laboratory staffed with a chemist, GeoProbes© for subsurface soil and ground water investigations, inland and marine surface water booming equipment, and a boom deployment boat.
For intentional criminal events, DEEP ERU is linked to a task force comprised of the Federal Bureau of Investigations WMD coordinators, crisis management and special agent bomb technicians, the Connecticut State Police hazmat technicians from the Emergency Services Unit (Bomb Squad) and Fire Investigations and Explosion Unit, and the Connecticut National Guard 14th Civil Support Team. This task force will work with local and regional assets to bring resolution to an emergency. The DEEP ERU is also the link to the U.S. Environmental Protection Agency (US EPA) and the U.S. Coast Guard (USCG).
Federal On-Scene Coordinators (FOSC)
Also, in accordance with the Federal Emergency Planning and Community Right to Know Act (EPCRA) Section 304 Extremely Hazardous Substances regulation, the reportable quantity for federal reporting is 100 pounds or approximately 18 gallons of liquid. The responsible party or property owner is required to notify the National Response Center (NRC) within 15 minutes of discovering the release, which incites a notification process to the US EPA and the USCG. Either or both agencies may respond depending on the geographical jurisdiction in which the incident lies. For this incident, the DEEP notified the NRC and coordinated over the phone with the FOSC. The US EPA elected not to respond but stayed in the loop by telephone.
Technical Specialists/Company Representatives
Product or container specialists (i.e., technical specialists) are a critical resource at working hazmat incidents. These individuals may be employed by the facility in question, a contractor for the facility in question, a contractor for the DEEP, or other specialized resources accessed through community relationships.
Ideally, meeting the technical specialists for a fixed facility before an incident is key. Trust but verify—just because someone works for the company does not mean he is competent. At this incident, the on-site technical specialist told us that he was trained and certified, but a CT DEEP interview revealed that his certification and fit testing were out of date.
The company representative brought the safety data sheet book to the ICP. When the safety officer asked a firefighter to look up the product, the firefighter said he could not find the product. Disappointed, the safety officer handed the book to the company technical specialist and, after fumbling through it, the expert acknowledged that the most dangerous product at this facility was not in the book. Having the company technical specialist help with research is a great way to build trust and interpret his level of competency.
We assigned a keeper firefighter to stay with the technical specialist so we would know where to find him. We call it placing someone in the bull pen. A company representative at the ICP may a second later wander off, get a phone call, or go to get something you asked for. Ensure this person knows you expect him to stay in a set location. If there are multiple representatives, it could be like herding cats; it is better to be looking at them, not looking for them. The best practice is to assign a keeper.
Other Local/State Representatives
Additionally, in Connecticut, the release of an extremely hazardous substances (EHS) also requires notifying the LEPC; in many towns, notifying the fire department satisfies this requirement.
Realize when dealing with any incident involving food storage or food processing (in this case, a large bakery), you must to notify the local or state health department and possibly the state consumer protection agency. Depending on the setting, both have the authority to determine whether the food is to be condemned. Also, the health department often issues a final determination for when the building can be reoccupied.
Regulations
Under Section 112(r) of the Clean Air Act (CAA) and Title 40 of the Code of Federal Regulations (CFR), Part 68, owners and operators of stationary sources are required to develop risk management programs for each regulated substance in a process. Compliance with 40 CFR 68 is required if the facility has more than the threshold quantity of a regulated substance in a process (including storage) at any given time. The threshold quantity for anhydrous ammonia (CAS#7664-41-7) is 10,000 pounds.
Ammonia refrigeration systems under 10,000 pounds are subject to CAA 112(r)(1); General Duty Clause. You may find more information about the General Duty Clause at https://bit.ly/327YzqD.
The EPA also administers the EPCRA. Facilities that handle or store EHSs above a 500-pound threshold are required to report these chemicals under EPCRA Section 312 (Tier II Report). If an ammonia refrigeration facility has 10,000 pounds or more in its system during any calendar year, it is subject to EPCRA Section 313 reporting (Toxic Release Inventory Form A or Form R). EPCRA also requires that facilities subject to Section 312 and/or Section 313 coordinate with their LEPC and their SERC.
Decentralize Your Incident
Make it a rule that, as your command officers arrive on scene, they are assigned to critical areas requiring supervision to ensure appropriate span of control. When creating a group or division, announce the radio designation based on its area of responsibility or geographic area. Announce the individual in charge and the companies reporting to the individual. Ensure they understand the tactical objective and how they fit into your IAP. Inform the companies reporting to this group supervisor and establish a good unity of command to enable better accountability, command, and control.
At a minimum, establish an operations section and a hazmat group. Based on the incident’s size and complexity, you may make other general staff (e.g., planning, logistics, and so on) and command staff assignments (e.g., safety officer, liaison officer, information officer). Within the hazmat group, assignments can include the research unit, decontamination unit, entry unit, and rapid intervention team (RIT) unit. You may also set up a medical group if the incident requires it.
An effective operation requires a lot of people. One important but often overlooked support role is a scribe who can track resources and document actions. If a command officer is looking up and entering data into a screen, a tablet, or a computer, he is working with his hands, not his mind; this is no different than if a chief were working with a tool. Although tactical worksheets are the chief’s best friend, only the scribe should be writing on one. Solid documentation and timelines tracked on incident command system forms increase the chance of incident cost reimbursement.
Site Safety/IAP
Site safety is every member’s responsibility. The site safety plan should be a verbal plan to start with, usually developed by the IC and, if appointed, the safety officer. As soon as a scribe is available, he can write down the verbal plan. In a fixed faculty, this plan can be a boilerplate document that contains the safety controls that you will most likely need to keep your members safe in the event of a release. You can expand this plan on based on the circumstances found on arrival. You can incorporate the site safety plan into the IAP as long as the information is delineated.
Public Information Officer (PIO)
This critical position keeps the media and public informed. The PIO should not just conduct a press conference; he must control the message and get the word out. The PIO should use all social media platforms to get the message out first and get it right. What are the facts? The media wants to know the following: the number of agencies, companies, and firefighters on scene; any injuries/fatalities; the risks to the community and the environment; the impact on traffic; what has happened, what is happening, and what is expected to happen; and the projected duration.
Planning Section
The research should be done on arrival; for the best response, it should already be complete in the preplan. The occupancy involved in the incident was a known chemical target hazard. For known hazards, ensure that the proper documents are maintained and updated at least yearly.
Based on the incident size and complexity, you can use the planning section to provide situation status, develop the IAP, and identify/develop plans for contingent events. This includes the actions needed if neighbors or sensitive occupancies (e.g., schools, nursing homes, and so on) must be evacuated or shelter-in-place, if traffic patterns must be diverted, or if responders must rapidly evacuate the incident scene. Incidents involving materials with low odor thresholds, including ammonia, chlorine, and methyl mercaptan, should also consider how responders will address secondary and tertiary odor calls remote from the facility. The situation status unit (Sit-Stat) will evaluate what has happened, what is happening, and what is expected to happen.
If a hazmat group is not in place, you can set up a research unit within the planning section to perform all the chemical research and coordinate with the Sit-Stat Unit and the operations section chief to develop the IAP.
Operations Section
For a hazmat incident, the operations section chief need not be a hazmat technician since one should be able to rely on his company officers as group supervisors (e.g., hazmat group supervisor) to feed the correct information. The most desirable skills needed for this position are a firm grasp of basic hazmat knowledge, good communication skills, and the ability to separate essential information from minutiae when briefing the IC.

Medical Group
Assigning a medical group early on for any hazmat incident is critical to ensuring that you are not playing catch up. The medical group supervisor should receive a verbal or written report on the chemical’s hazards. The medical group’s location and unity of command should be based on local SOPs. The National Incident Management System places the patient oversight under the operations section chief and the responder oversight under the logistics section chief. With a small incident that is not likely to last more than one operational period, it may be easiest to have the medical group report to the operations section chief and have responsibility for patients and for emergency responders.
Depending on local SOPs, the medical monitoring of responders varies. OSHA 29 CFR 1910.120(f) requires hazardous materials team members to receive a medical evaluation prior to assignment to the team and at least once every 12 months, unless the attending physician believes a longer interval (not greater than biennially) is appropriate. More specifically, hazmat team members who may have been injured, received a health impairment, developed signs or symptoms that may have resulted from exposure to hazardous substances resulting from an emergency incident, or exposed during an emergency incident to hazardous substances at concentrations above the permissible exposure limits or the published exposure levels without using the necessary personal protective equipment must be evaluated as soon as possible following the emergency incident or development of signs or symptoms and at additional times, if the examining physician determines that follow-up examinations or consultations are medically necessary.
Many departments place further incident demands with pre and post entry vitals. If a department choses to require pre-entry medical monitoring, we recommend obtaining the vitals at the start of the shift. Operating at a low-frequency, high-risk emergency is stressful; an elevated blood pressure or pulse rate is expected after a responder readies the entry equipment and then is dressed to the waist awaiting entry. Additionally, if there are emergent life safety needs present, we cannot wait for vitals to be obtained.
It is imperative to ensure a transportation corridor so that emergency medical services units can get in and out of the scene, even in situations where there are no victims. A trip and fall that results in a head injury to an entry team member requires a plan for rapid transport. Assign a member to the supervisor as a scribe for victim tracking if there are victims. Tracking should include approximate age, sex, injuries, and the hospitals to which the victims were transported.
When terminating the incident, the medical group supervisor or the safety officer should conduct an on-scene briefing of personnel for signs and symptoms of hazmat exposure. Convey this information before all personnel depart an incident. This has proven problematic on incidents with multiple operational periods or when personnel depart individually. The accountability officer can assist with this by directing personnel to the appropriate person during the demobilization process.
Decontamination Unit
A decontamination (decon) line must be commensurate with the hazard; keep it as simple as possible. Since ammonia is extremely water soluble, you will be exposed to it in vapor form rather than liquid. The decon line need only be a rinse station coupled with a suit pH check station prior to doffing equipment. Try to generate as little waste as possible. The most important issue in waste generation is the fate of the final waste product, which varies according to local and state laws.
In Connecticut, depending on the waste stream, the DEEP can issue an emergency discharge authorization. For the waste generated from an ammonia release decon line, if authorized by the authority having jurisdiction—i.e., DEEP—the waste solution could be directed to soil.
Also, depending on the volume and pH and with concurrence with the sanitation department, it may be directed to the sanitary sewer. If neither option seems acceptable, a licensed environmental contractor may be brought in for waste removal.
RIT Unit
Assign personnel to the RIT who will stand by and be equipped to render assistance or rescue. The RIT must be well informed of the IAP to ensure it is equipped with the necessary tools and retrieval device to remove a down entry team member. This is not a position for your weaker skill set personnel. RIT members must be prepared to provide rescue air, ventilate the building, force doors, breach walls, and set up a haul or lowering system for stairwells or catwalks and must have their own metering package.
Direct RIT and decon unit members not to go on air until operations has coordinated with the entry, RIT, and decon unit leaders. Once they have set up their equipment, depending on ambient temperatures, consider staging the groups in a suitable environment dressed to the waist without air until all teams are ready to implement the IAP.
Entry Unit
Entry unit personnel must have a clear mission from the IAP. If the mission is reconnaissance, then it should be just that. If it happens that taking a different action would prove positive, it must be conveyed to the entry team leader and approved by the operations section chief.
A three-team rotation has proven very effective in dealing with a potential long-term or multiple-entry operation involving an entry team, a RIT, and a stand-by team. The entry team goes in and performs a task while RIT is its backup. When the entry team has either timed out or determined that a second entry is needed, the RIT replaces the entry team and the stand-by team replaces the RIT. The initial entry team goes through the appropriate decon process and gets new cylinders. They then go to the back of the line as the stand-by team or are replaced with fresh technicians. This greatly limits downtime. There may be times when a face-to-face turnover is needed between entries; make sure there are good communications.
Facility Control Room
Process operations at fixed facilities may often be coordinated at a control room. Depending on the type of facility, a Systems Control and Data Acquisition computerized system may be used to control and monitor process operations, valve positions, and air monitoring data.
At this incident, air monitoring confirmed that the control room was a safe operating area and the room’s proper positive pressure was maintained. Never assume a control room is a safe place! We had a call a few months later in an occupancy that processes chlorine in which the control room was contaminated by vapors. You must evaluate the room’s location and access to its emergency egress in case positive pressure is lost or the area otherwise becomes contaminated. Consider the following:
- Is it accessible to the outside?
- If not, is there access to an area of refuge?
- Should ladders be placed to enable a hasty exit if needed?
At this alarm, we did not occupy the control room to aid in mitigation until after the king valve was already closed and interior metering was complete.
I (Ricci) was positioned in the control room as interior safety to work with the company technical specialist. Together, we maintained radio communications with the entry team. The entry team was monitored through the sealed window of the control room, thus allowing for a second set of eyes during this complicated mitigation technique. Crews performed admirably (photos 1-2).
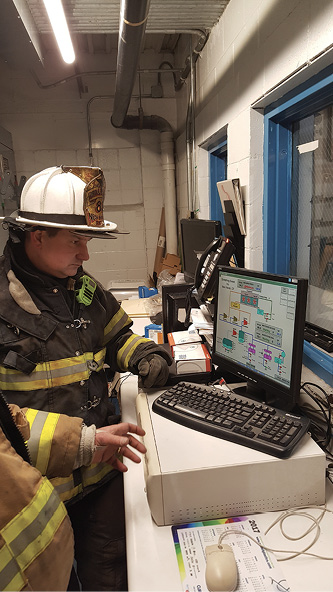
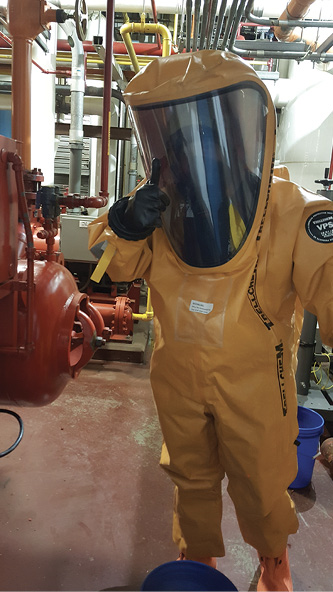
(1-2) Photos courtesy of New Haven Fire Fighters.
Blocking and Bleeding
After reviewing the process drawings, we determined to further limit the area of the piping in which the leak was found. The entry team had to work overhead in chemical vapor protective clothing from a stepladder to close two valves and tighten a packing (photo 3). We provided the team with a safety briefing prior to entry, advising them of a limited splash hazard possible from tightening or loosening a valve’s packing. We also went over the concern of overextending while on the ladder, thus creating a fall hazard.
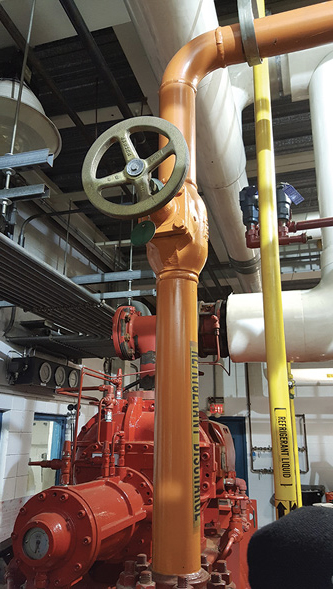
(3) Photo by Frank Ricci.
Our next entry took more planning. We determined that the best way to completely eliminate the hazard was to drain the remaining product. It was vapor in this part of the system in between the two closed valves. The cause of the incident was a packing gland around the valve stem. Tightening with nonsparking tools didn’t stop the release; our technicians had to drain the pressure so the maintenance technician could replace the packing.
The plan was to dissolve the vapors in a five-gallon bucket of water. The reaction of ammonia gas with water is exothermic; the by-product of the reaction is highly concentrated ammonium hydroxide, which is extremely caustic. The IAP as written would only allow the system pressure to drop 10 pounds per square inch per five-gallon bucket to ensure the water would not boil off. This was monitored and controlled from the control room. The valve would be reclosed and the bucket, now containing heated water, was dumped into an overpack drum.
This process took a prolonged amount of time and was directly coordinated through the control room. The ammonia vapors released from the ammonium hydroxide solution in the overpack are significant. Make sure the vapor release does not migrate outside of the hot zone and impact other locations (e.g., warm zone, cold zone).
Valve Shutoffs (King Valve)
At this incident, the anhydrous ammonia tank that held more than 1,200 pounds of product was on the roof. The king valve is the main valve in the main line from the tank leading to inside the building. It isolates the tank from the piping and reduces the amount of product that can be released from the leak point to just the amount of product that is in the piping.
We used the tower ladder to bring a technical specialist, escorted by a hazmat technician, to close the valve. We monitored the air to confirm that there was no hazard and that the valve was isolated. Using the tower ladder prevented members from having to travel through the building in a hazardous atmosphere. This action involved very little risk and reduced the hazard.
Is It an Emergency Shutoff or a Dump Valve?
During recon, we found a valve that was labeled “Emergency Shutoff,” which was just inside a locked door. Since no one was in the building, remotely shutting down the system seemed the best course. While formulating the IAP, an interview with the facility representative and the service technician revealed that the “emergency shutoff” was actually an “emergency dump valve” for an ammonia diffusion system; it would mix 1,200 pounds of product with water and dump the solution into the sanitary sewer system. What sounded like a great option could have led to a disaster.
Anhydrous ammonia systems may have an emergency dump valve/diffusion system. Although there is a mixing valve to put the gas into solution, which would make aqueous ammonium hydroxide, we were not sure what the effluent concentration would be. As is the case with any water-soluble gas in solution, the ammonia vapors will come out of solution. This would have put a lighter-than-air, toxic, flammable gas into a sanitary sewer system. In poorly ventilated areas, this off gas can reach unsafe levels, definitely above the permissible exposure limit, likely above IDLH and though less likely but possibly into its flammable range.
In older urban settings, like New Haven, these drain systems are often connected to the sanitary sewer. Even if legally tied in, dry traps can allow toxic gases to infiltrate private residences and expose the occupants. Also, if you choose to use the emergency dump valve, make sure you coordinate with the sanitation department. It could be catastrophic and place sewer workers at risk if they are working downstream from your emergency.
A large slug of a high pH solution traveling into the sewer plant could upset the system by killing the bacteria that is used to treat the wastewater. Although not as critical of an issue, these vapors could lead to numerous calls for ammonia odors, taxing resources. First responders should have a predetermined way to notify the sewer department of a significant amount of anhydrous ammonia entering the sewer system, and the fire department should establish the route that the product will take once it enters the sewer system.
Ventilation
Is the building equipped with a ventilation system? Using a facility’s ventilation system could be very helpful. If you use it, ensure that it was designed to ventilate an emergency release from the anhydrous ammonia system. Remember, ammonia is a flammable gas, and the most likely place to encounter it in its flammable range is in an enclosed space, such as the building that you want to ventilate. So, ensure the ventilation system is designed for this and is intrinsically safe.
Does the fire department or HMRT have the capability to initiate PPV? Most fire department ventilation fans (electric box and gasoline-powered fans) are not intrinsically safe, so positive pressure (not negative pressure, in which the gases are drawn across the ignition source of the fan motor or engine) coupled with a distinct remote building exhaust point are a must. However, there are some hydraulically driven large cubic-feet-per-minute-capacity fans available. If one is available, it should be on this run card.
Since this is a toxic gas too, ensure that the exhaust port is not going to impinge on the ICP, other areas of operation, or the public. Using intermittent ventilation could prove effective in ensuring responder and public safety. To ensure safety in sensitive areas, couple all ventilation efforts with metering. We used this method and found it also cut down on additional odor calls in the area.
Vapor dispersion using a fog stream of water is another tool if there is an immediate high risk of impact to the public. However, remember, ammonia is an extremely water-soluble gas, so you will not just be dispersing vapors; you are also generating a high-pH waste runoff. If using this tactic, consider that the runoff may impact surface water bodies and sanitary sewers. If there is a significant threat to human life, use this tactic; people win over fish.
Termination
On this alarm, despite previous training not to close their suits without being on SCBA, several members did so to keep warm. The safety officer and division supervisors had missed this. When terminating the incident, several members exhibited signs of carbon dioxide poisoning and were transported to the emergency room; OSHA had to be notified. The issue was corrected with remedial training. Training is not enough! We couldn’t believe that this could have happened; it confirms the need for continual drilling to reinforce training. Train in a realistic way that is fun and challenging.
At a hazmat incident, among the most important parts of the demobilization process is ensuring the responders know what the chemical is and its associated symptoms of exposure. A quick debrief prior to releasing companies can accomplish this task.
After-Action Review
The after-action review is an opportunity to improve your future responses and ensure your IAP is fully documented. Command level officers should state the actions taken and why, along with any missteps or alternate actions they would have taken in hindsight. This will demonstrate that command officers are part of the team, not above it; it allows others to share freely. The goal is not to please people or conceal deficiencies but to have an honest evaluation and address needed corrections. A bonus to performing this OSHA-required critique is that it counts toward required training.
If you haven’t made a mistake at a hazmat incident, it does not mean you’re that good. It means you haven’t been to enough or you’re not being honest. When making decisions based on imperfect information and extremely dynamic events, you will make mistakes. The key is always to strive to do better.
References:
CDC. NIOSH Pocket Guide to Chemical Hazards, “Ammonia.” https://bit.ly/339brfx.
EPA. (June 2015). Accident Prevention and Response Manual for Anhydrous Ammonia Refrigeration System Operators. https://bit.ly/3bkUkeq.
OSHA. OSHA 1910.120 – Hazardous waste operations and emergency response. https://bit.ly/2DiKzRc.
OSHA. Ammonia Refrigeration E-Tool. “Properties of Ammonia.” https://bit.ly/32IxcCI.
TRANSCAER. “Ammonia Training Student Handout.” https://bit.ly/3gNZ5OK.
Jeff Chandler joined the fire service in 1985 and is a supervisor with the Connecticut Department of Energy and Environmental Protection’s Hazardous Materials Emergency Response Unit, which he joined in 2001. He is assigned to the southern region, which includes the Interstate 95 corridor.
Frank Ricci (ret.) served as battalion chief and drill master assigned to Special Operations Command for the New Haven (CT) Fire Department. He is a contributing author to Fire Engineering’s Handbook for Firefighter I and II (Safety Chapter), the lead author on the Tactical Perspectives DVD series, and an advisory board member of FDIC International and Fire Engineering.