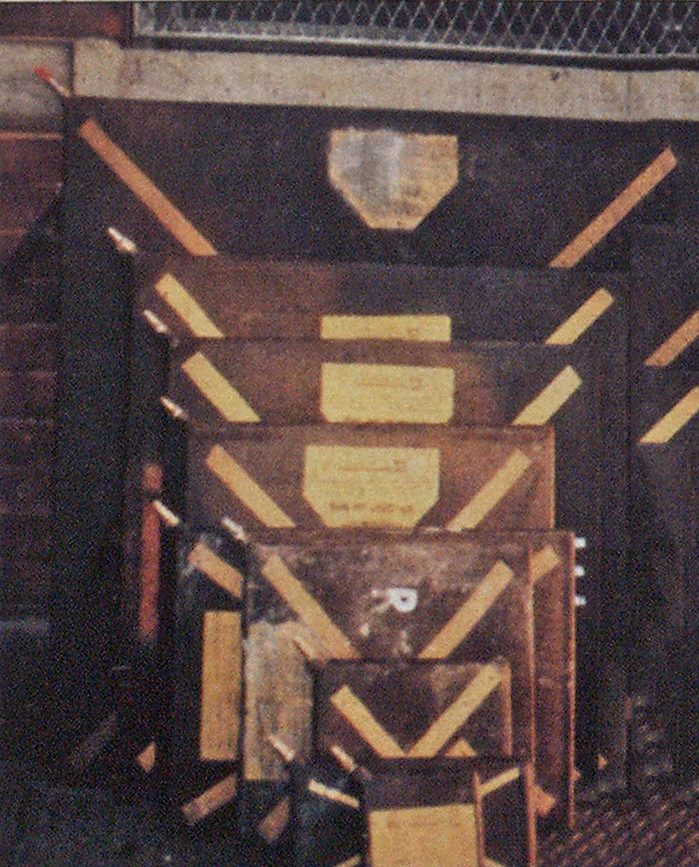
AIR BAGS PART I
THE RESCUE COMPANY
SINCE THEIR introduction to the fire service in the seventies, air bags have been used in many rescue operations. Because of their unique design, their adaptability for rescue incidents makes them a vital resource of any rescue unit.
Air bags have been used successfully in response to accidents involving automobiles, trucks, and other vehicles, rail or tank cars, elevators, and heavy equipment, and, very frequently, in building collapses. Major industries in such fields as mining, shipbuilding, pipeline construction. stone quarrying, rail car repair, refining, utility supply, and power supply, as well as the military, use them in their daily operations to lift, spread, shift, bend, force, or move.
Interestingly, when the air bag was first introduced to the fire service, its name led some to mistake it for a type of bag designed to catch airborn people who had jumped from upper floors of buildings during a fire or other emergency. When new equipment or tools are introduced to a department-particularly those specialized items carried only by selected units-a familiarization drill should be held to demonstrate capabilities and limitations in the event that literature is not immediately available to the whole department.
The air bag gets its name from its source of power-air. The air used to inflate the bags can come from compressed air cylinders (SCBA), compressors, apparatus air systems, or a hand pump. The SCBA cylinders are the most commonly used. Adaptors are available to convert alternative air supply (industrial compressors, for example) and make them compatible for use with the air bag systems.
There are high-, medium-, and lowpressure air bags. The lowand medium-pressure bags, operating at approximately 7 to 14 psi, are used to lift, support, or move heavy objects. Overturned vehicles, tankers, rail cars, and the like can be uprighted or stabilized during rescue operations. Design features allow them to be used on all types of surfaces, be it ice, snow, sand, soft marshy ground, or rubble. Because of the lower pressure they can be used against the thin skins of cars, buses, and airplanes without damaging them.
The cylindrical bags conform to all shapes that need to be lifted. Weighing as little as three pounds, they are capable of lifting 17 tons to a height of almost 70 inches. They are manufactured in both nylon and kevlar fabric; are highly resistant to oil and chemicals, tears, punctures, and heat; are very durable; and are available in special carrying cases that allow for transporting to remote areas. For safety purposes, it is advisable to use lowand mediumpressure bags in pairs.
High-pressure air bags are available in a variety of sizes, ranging from six inches wide and six inches long to thirty-six inches wide and thirty-six inches long. They are capable of lifting from one ton to 75 tons to heights between three inches and 20 inches using a single bag. (By stacking two bags, one on top of the other, the height reached can be over 40 inches.) The bags are constructed of neoprene and reinforced with either steel wire or kevlar aramid fiber. The kevlar-reinfbreed bags are approximately 40 percent lighter and are much more flexible than those of the steel-wire-reinforced variety, making them easier to use in hard-to-reach places.

Each air bag (low-, medium-, and high-pressure) is labeled with the capacities for lifting height, tonage, and air volume (in cubic feet), and with the operating pressure. Many rescue units, using highly visible paint, mark their bags with this information (in addition to the bag’s labels) to serve as a reminder of the bag’s limitations. The label’s listing also includes the safety guidelines to be followed during operations. A distinguishing mark indicates the center of the bag, which is used for proper placement during operations.
Like the low-pressure bags, the highpressure models are resistant to chemicals, gasoline, oil, punctures, scrapes, and cuts. Manufacturers offer complete systems, consisting of 10 bags of various sizes, or individual bags with necessary components. If your department’s budget prohibits the purchase of a complete set, start with one or two bags, with a goal of eventually completing an entire set. A complete system includes air supply, air hoses, controller, and air bags.
The compressed air cylinder (SCBA) is the most common means of supplying air. A high-pressure regulator reduces cylinder pressure down to the operating pressure. The regulator contains two gauges, for low and high pressure. The high-pressure gauge indicates the cylinder pressure; the low-pressure gauge is then set for the operating pressure (usually between 120 and 150 psi, depending on the manufacturer’s recommendations). A hose is connected to the air outlet connection, which is the supply line for the controller. This system-SCBA cylinder, regulator, and hoses-is portable, fast, and easy to operate, especially in confined spaces.
The air bag label lists the cubic-feet capacity of air volume for complete inflation; an important part of your operating plan must allow for having sufficient air on hand, depending on the number of bags, their capacities, and the number of lifts that may be required for a particular operation. A six-inch-by-sixinch bag requires .14 cubic feet of air, while a 36-inch-by-36-inch bag requires 47 cubic feet. Obviously, larger bags and multibag operations require more air. Drilling and training with bags of various sizes and in different combinations will develop confidence and assist members in getting to know the capabilities and limitations of the air bags and system.
Air hoses come in varying lengths and colors. It’s extremely important to use differently colored hoses in multibag operations. Often, the operator of the controller will not be able to see the air bag being used. Instructions to the operator from another member should be given by color code to prevent confusion. Picture two bags positioned to lift a heavy structural member off a trapped victim. They are supplied by one controller and are at opposite ends of the structural member, out of the sight of the operator. The member directing the operator relays, “Inflate the green hose,” “Take it up easy on the red hose,” and the like. Using colors to direct controller activity, particularly when the bags arc completely out of the operator’s line of sight, is simple and effective, and cuts down the margin for human error-and in air bag operations, inflating the wrong hose could spell disaster. The bursting pressure of these air hoses is approximately 1,000 psi, well above the operating pressure. The hose has a male connection at one end and a quick-connect, locking safety coupling on the other.


(Photos by author.)
AIR BAGS-PART I
The controller operates the air bag itself, and is designed for either single or dual capacity. A dual controller has a separate low-pressure gauge and safety relief valve for each air outlet. Built-in safety relief valves prevent overpressurization of the bags. Various manufacturers offer either simple one-quarter-turn valves or “deadman” control buttons or toggle switches.
The deadman control plays an important part in any rescue operation. It is activated when the operator applies pressure and stops when pressure is released. (If the operator were to die while operating the control, activation would stop upon his release of the button or switch-that’s how the term “deadman” came about.) At a recent building collapse, members were in the process of operating an air bag to free a trapped victim when a secondary collapse occurred, burying the rescuer operating the controller and causing him to release pressure on the deadman control. The rescuer and the trapped victim were removed successfully and the victim was spared any additional harm that could have occurred had not the deadman button been released.

The components of the controller are:
- air inlet valve: hose coming from the air supply;
- operating gauges (two on dual controller);
- control valve (either deadman button/switch or one-quarter-turn valve lever;
- safety relief valve with control knobs;
- air outlet connections (two on dual controller).
Air bags’ capabilities are directly related to their size. A six-inch by six-inch bag has a working surface area of 4.74 inches x 4.74 = 22.46 square inches. This multiplied by the input pressure, say, 118 psi, gives you the bag’s lifting capability, which in this case is 2,650 pounds-the bag has the capability to lift over a ton. A 36-inch-by-36-inch bag can lift approximately 73.4 tons. Lifting heights vary from as little as three inches to twenty inches, and stacking two bags of the same size will double the height that can be reached.
The different shapes, sizes, and capabilities of the bags allow rescuers to adapt to the most difficult situations. The overall thickness of only one inch provides rescuers with a most versatile tool that can be used in the narrowest of openings with the1 greatest of flexibility