
BY VYTO BABRAUSKAS
The United Kingdom (UK) government’s investigation of the Grenfell Tower disaster is treating it as a criminal matter. Thus, it may be years before the technical investigation’s findings are released. One can only hope that UK officials act more responsibly than those in the United States. The Bureau of Alcohol, Tobacco, Firearms and Explosives (ATF) report on the West, Texas, disaster of 2013 has not been released1 and likely never will be. Regarding the West incident, officials claimed incendiarism as the cause based on discredited negative corpus reasoning. The 2001 AZF fertilizer plant explosion in Toulouse, France, was followed by a wildly politicized, inaccurate investigation.2 Nonetheless, even early reports have revealed an astounding list of fire safety transgressions at Grenfell Tower. This article will focus on one—the façade’s fire spread performance. The fire safety faults of the façade most likely determined the fire’s tragic outcome.
High-Rise Façades Fire Performance
The potential for fire spread along building façades involves some unique problems, and they involve numerous, sometimes specialized and complex, technical issues. Although any building façade can propagate fire with unexpected rapidity if not built safely, high-rise buildings are a special problem.
- A fire spreading on the façade can rapidly overwhelm the fire service’s ability to intercede, or it may be physically impossible to attack. Façade fires can involve conditions where the fire spread rate is rapid initially and keeps accelerating as the upward spread progresses. Apparently, this is exactly what happened at Grenfell. Moreover, if the fire starts at or reaches a height beyond the reach of fire service water streams, then suppression cannot occur.
- Normal building fire protection features are designed only to address interior fires. Automatic fire sprinklers protect only internal spaces, not the exterior façade. Similarly, the compartmentation that fire-resistive floors provide will limit only internal fire spread but does nothing useful at the façade.
- Jurisdictions vary greatly regarding trying to mitigate façade fire problems. Furthermore, the regulations in many have changed progressively over the years. New test methods now used in the United States, Canada, and Europe were not used or were not mandatory some years earlier.
Façade fire spread is a broad concept. The two primary means of fire propagation are external and interstitial. The most significant fires have tended to involve fire propagating along the façade’s exterior. But a second mechanism must be understood. In some cases, a curtain wall is erected, spaced some inches away from the ends of the floor slabs. This gap between the edge of the floor slab and the curtain wall should be firestopped. The fire service learned a lot from the One New York Plaza fire of 1970.3 In that fire, flame spread occurred from floor to floor at the façade and also along its interior. The builder had used a piece of thin aluminum sheet metal as firestopping at the slab end. Although aluminum does not burn under normal building fire conditions, it melts readily and easily. As a result, a hole was created and fire moved up that way. The remaining discussion will focus solely on external fire spread, which is what occurred at Grenfell and at most disastrous high-rise façade fires.
Figure 1. The 1939 Schlyter Test Apparatus
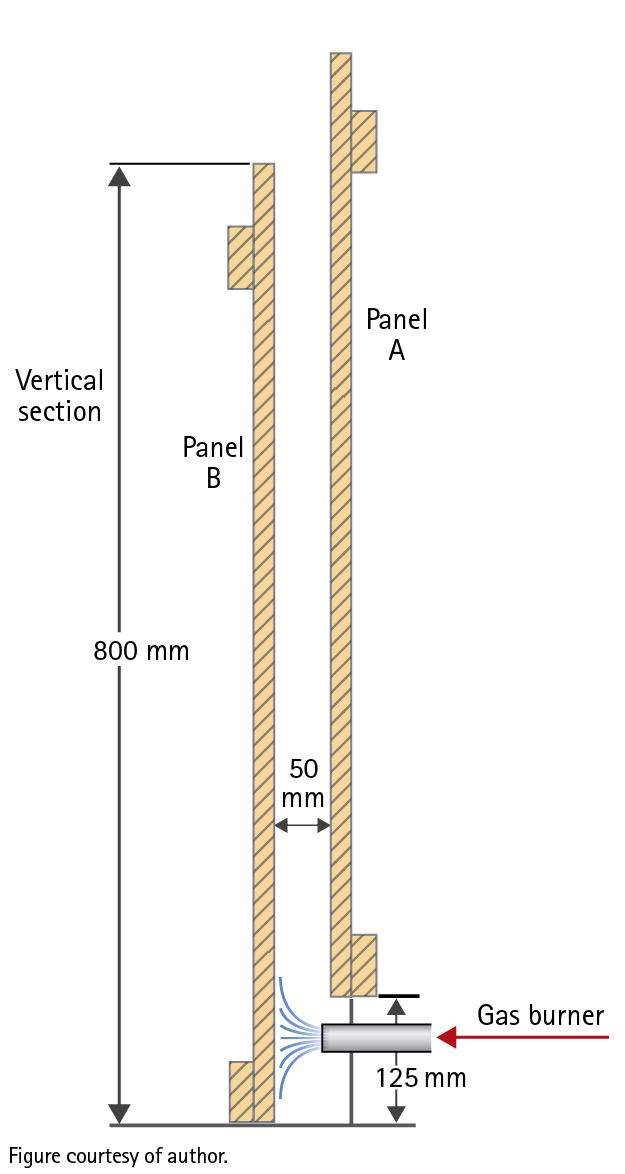
Combustible Cladding
Combustible cladding is generally accepted in all countries for the exterior walls of single-family houses. Although such façades can ignite and burn, this generally does not contribute to deaths or injuries of the occupants, who normally escape—or perish—well before fire progresses into the exterior. Different considerations, of course, may apply in the wildland urban interface,4 but that is a problem that will not be addressed here. When high-rise buildings started becoming popular in the late 19th century, it was inconceivable to build them from combustible materials. Thus, until the past three or four decades, a high-rise building was built of steel or concrete and clad with stone, concrete, brick, steel, glass, and similar noncombustible materials. But more recently, designers have gotten more “creative” and started using combustible claddings on high-rises. Among the most prominent is exterior insulation and finish systems (EIFS), although other combustible materials such as solid-plastic panels have also been used. EIFS is an aesthetically versatile material and can be made to look like plaster, noncombustible stucco, or other “faux” finishes. However, it generally consists of a plastic skin (often acrylonitrile) on top of a polystyrene foam insulation layer. Additional layers may include plastic mesh or an air gap. The net result, however, is a nearly all-plastic cladding. Although it is possible to use mineral wool instead of polystyrene foam, this costs more. It is of exceedingly grave concern that most countries have accepted the use of such combustible claddings for high-rise buildings at the behest of industry without adequately considering the fire safety implications.
Testing Façades
Generally, the authorities having jurisdiction (AHJs) take the position that combustible façades are acceptable because they have been qualified according to some particular fire test for this purpose. A typical high-rise building is a vastly larger structure than the size of a specimen that can be accommodated in the laboratory. But it is an elementary principle of fire dynamics5 that radiation from flames tends to increase with the size of the flame and the size of the flame, in turn, is likely to increase with an increase in the size of the burning object. This should raise a concern about the adequacy of laboratory testing, but it rarely has.
During the late 1990s to early 2000s, I served as the U.S. delegate to a group within the International Organization for Standardization (ISO) that was working to develop international standards for façade testing. Eventually, this work resulted in the ISO 13785-26, Reaction-to-fire tests for façades—Part 2: Large-scale test, along with a small-scale screening test.6 The group considered the U.S. proposal that the Southwest Research Institute offered, a massive two-story rig, but concluded that, despite the impressive amount of flaming created, the industry had so developed the criteria to allow plastic foams that might well support sustained flame spread in building fires. The U.S. response was not to make the test tougher but to replace it with a milder, smaller new version, National Fire Protection Association (NFPA) 285,7 Standard Fire Test Method for Evaluation of Fire Propagation Characteristics of Exterior Non-Load-Bearing Wall Assemblies Containing Combustible Components. What is remarkable is that, to the present time, tests have been studied and actual building fires have been studied, but not in conjunction with each other. The NFPA Research Foundation, for example, recently published an ambitious study8 that provides useful reference to a number of severe façade fire incidents and, in the same report, outlines many of the test methods. But no examination is made as to which tests, if any, would have prevented which fires! The broad perspective view must be that using significant amounts of combustibles, especially plastic foams, in façade construction is an unsound practice. Tests that appear to indicate the acceptability of such practices are likely to be poorly grounded in reality.
Figure 2. The Grenfell Tower Façade
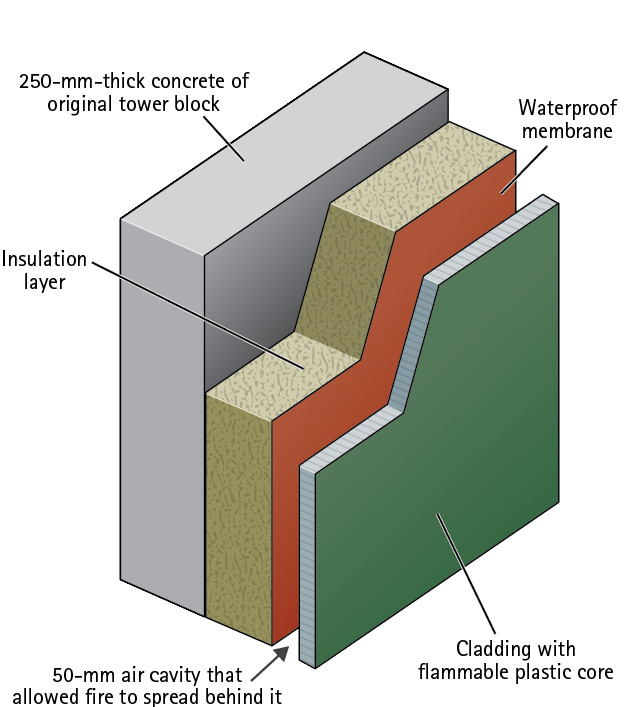
The Schlyter Effect
The Schlyter effect is the increase in the burning rate and the flame spread of a combustible panel that occurs when a second panel is placed in front of it, separated by a small gap through which air can flow due to buoyancy. Some materials may show limited burning and no significant flame spread when ignited as a single panel but yet show severe burning when a second panel is used. Ragnar Schlyter was the head researcher studying fire safety at the Swedish National Testing and Research Institute (SP); he first demonstrated the effect in 1939.
In the United States, at about the same time, Underwriters Laboratories’ (UL) Al Steiner developed the Steiner Tunnel,9,10 now generally known as ASTM E84,11 Standard Test Method for Surface Burning Characteristics of Building Materials. This apparatus requires a 24-foot-long test specimen, making it costly to construct and complex to operate. But, in contrast, Schlyter’s motivation in developing a flame spread test was to create conditions for fire spread that would be indicative of the fire behavior of large specimens or large buildings, yet to do so on a small scale. Small-size tests often produce mild exposure conditions, but Schlyter did not fall into that trap; his test12 was as simple and elegant: Two slabs of test material are oriented vertically with a small air gap in between. The bottom is open to allow air inflow, and a burner flame is applied to the bottom. In this test, only highly fire-safe materials do not show runaway combustion. Schlyter achieved such severe test conditions in a small footprint because of the parallel-slab geometry with an intervening air gap. Schlyter’s original test rig involved panels that were 800 millimeters (mm) (31.5 inches) high with a 50-mm (two-inch) gap in between. But the results are not very sensitive to these measurements unless the gap is made much smaller, which we shall consider below (Figure 1).
After Schlyter developed the test, the SP used it fairly regularly for assessing flame spread of materials, and eventually it was published as Standard NT FIRE 00213 by the Nordic test standards organization Nordtest.
The Schlyter effect is known to some fire scientists but is not generally well known in the fire safety area. For example, it is not mentioned in the Society of Fire Protection Engineers14 or NFPA15 handbooks, although the Forest Products Laboratory in Madison, Wisconsin, did some research with it in the 1950s and 1960s,16,17,18 as did the National Bureau of Standards, now the National Institute of Standards and Technology.19
The Schlyter test geometry was then rediscovered by researchers at Factory Mutual in the 1970s,20 in Canada’s National Research Council (NRC) in the 1980s,21 and at UL during the 1980s22 and later around 2010.23 Some additional studies can also be found in the mathematical combustion literature.24 Factory Mutual even published a standard test method based on a scaled-up (eight-foot-high) geometry of the Schlyter test.25 None of these later researchers, however, realized the origin of testing in this geometry was by Schlyter. The research at the NRC, even though without acknowledgment to Schlyter, has been exceedingly important for the fire safety profession. Choi and Taylor were concerned with fire potentially spreading up inside cavity walls because of faulty construction where floor-line firestopping was absent and also the insulation material failed to fill the full thickness of the wall cavity, leaving a vertical gap. (21) Thus, they studied various insulation materials, measured their flame spread ratings in the Steiner Tunnel, then tested them in a cavity wall with a variable gap spacing of the vertical channel. Their findings showed the following:
- The crucial factor was gap spacing. In their work, tests with gaps of less than one inch (25 mm) showed no sustained flame spread while those of greater than one inch showed continued upward flame spread.
- Remarkably, they found that “the flame spread rating of the materials used in the tests was not a significant factor.” In other words, even slightly combustible specimens were likely to show uncontrolled upward flame spread for a sufficiently large gap (over 25 mm) while even relatively highly combustible ones would not show such spread if the gap was made narrower than 25 mm.
The practical lessons from this research are as follows:
- Walls with vertical cavity spaces can present severe fire hazard issues unless knowledgeable and competent measures are taken to control the hazard. Thus, it is by far the best not to design systems that incorporate vertical cavities, channels, spaces, or flues.
- Flame spread ratings as measured by the Steiner Tunnel (ASTM E84) are not a credible measure of the propensity for fire to spread upward in cavity spaces.
- If a wall is designed with a vertical cavity, for uncontrolled flame spread to be precluded, it is necessary that either the surrounding materials be truly noncombustible or that it be very well sealed against the entry of air from the bottom (or the sides). With regard to the latter, however, the thermal effects of fire must also be considered. A means of closing off a cavity will be useless if heating from a fire melts out, burns through, or otherwise compromises the closing element.
Grenfell Tower Façade Fire Performance
The original 1970s construction of the Grenfell Tower contained a façade that was comprised of 250-mm-thick precast concrete panels.26 Thus, it had had no combustible materials and no vertical cavity. Exterior fire propagation along such a façade would be extremely unlikely. A renovation was completed in May 2016,27 only a year prior to the disaster of June 14, 2017. The existing façade was fitted with aluminum-faced exterior panels, behind which was a three-mm layer of polyethylene plastic and an air gap.28 Beyond the 50-mm air gap (more than twice the maximum safe gap dimension per the Canadian research results) was a 150-mm layer of polyisocyanurate (PIR) foam that was attached to the original precast concrete spandrel panels29 (Figure 2). The PIR foam was faced with aluminum foil on both sides, but the presence of an ostensibly noncombustible surface facing the cavity is not helpful when the material is a thin layer that will readily melt out and the opposing face is a highly flammable solid piece of plastic. The combustible materials in a vertical cavity do not have to be of notable thickness for a hazard to be created. But even a novice fire safety functionary should have questioned a 150-mm (six-inch) layer of plastic foam. The foam’s manufacturer explained30 that it carried the best flame spread rating in the UK testing methodology, Class 0. However, as in the United States,31 the UK system for flame spread classification does not do an acceptable job of classifying foam materials. Even if it did, the Canadian research results indicate that the most minimal levels of combustibility would suffice to create a disaster when a cavity is created in a wall, especially one twice the width of the maximum 25-mm gap found acceptable by the NRC researchers.
Lessons Learned
Understand the crucial faults in the Grenfell Tower that allowed the disaster to happen, but also realize that a building need not have the same faults to suffer a disastrous fire. The two major factors that allowed unrestricted flame spread to develop along the façade of Grenfell Tower were the combustible materials in the cladding and the air gap between the two layers of combustible materials. That combination ensured a disastrous outcome. In any combustible façade, a 25-mm or greater gap is likely to lead to catastrophic failure. But a combustible façade does not need a flame-spread-promoting gap to sustain a massive fire. A tall façade made of combustible materials is a grossly unsound idea. It is a design that trifles with the public safety.
High-rise buildings have been prominently constructed in many large cities ever since the late 1800s. Yet, serious fires involving high-rise buildings façades were exceedingly rare until the past few decades, and they are now common. The difference is the introduction of combustible materials into a building element formerly built of noncombustible materials. Interestingly, 50 or 100 years ago, building codes did not regulate façades to any significant extent; there was no need to. Developing a test to examine the flame spread possible along a granite slab or a stainless-steel panel was not worthwhile. The construction industry cleverly exploited this regulation gap by introducing combustibles into high-rise façades. In the United States, the industry ostensibly responded to this newly created hazard by developing a two-story façade test rig sponsored by The Society of the Plastics Industry.32 It does not take great analytical skills to figure out that such a test would be accepted by building code bodies; specifically, the then-existing International Conference of Building Officials accepted the work at face value, and it became the original U.S. national test for façade flammability, Uniform Building Code (UBC) 17-6,33 superseded by the less rigorous test, UBC 26-9/NFPA 285, which remains the standard in the United States today.
Except for a few tests for basic chemistry properties (such as heat of combustion), fire tests are empirical and do not possess intrinsic validity. They must have been validated for any particular scenario by comparing the output of the test against a full-scale or actual fire reality. Successful validation means that the comparison showed a close enough correspondence. None of the national tests for flame spread—ASTM E84 (U.S.), BS 476 Parts 6 and 7 (UK)—were even intended to characterize fire spread along a building’s façade. Consequently, it is an abuse to attempt to use them this way.
But even more problematically, none of the façade tests, even the better ones such as SP FIRE 10534, CAN/ULC-S13435, and ISO 13785-2, have ever been validated against façade performance in actual fire incidents. Yet, most users are unaware of this problem, which makes nonsense of claims (or implicit assumptions) that the tests can accurately quantify what they claim to be quantifying.
Few persons today understand what Schlyter learned some 79 years ago: A vertical gap between two facing surfaces that can sustain burning along them is a recipe for disaster unless air flow can truly be stopped. The best way to stop air flow is not have a gap in the first place. But if a gap has to exist for some moisture engineering purpose, then it is essential that it be less than 25 mm or one inch and be fully firestopped along the bottom and the sides by materials that cannot fail in the heat of the fire. If these precepts are not understood or are ignored, a bad situation can quickly be made much worse.
It is tragically ironic to note that the designers of the recladding of Grenfell Tower chose exactly the same air gap, 50 mm, which Schlyter had determined was the optimum spacing in his test to promote upward flame spread in a cavity.
Finally, I strongly emphasize that the building codes in the United States and other countries completely ignore these important fire safety problems and their solutions. The roles of air gaps and flame propagation mechanisms are not understood, and façade fire safety is regulated by tests that may be convenient for industry to comply with but have not been validated against performance in actual fire incidents. The fire service faces a long, steep, uphill road if it is to correct this state of affairs.
References
1. White, D. “Incendiary Findings.” Industrial Fire World. (31:3): 4, 29.
2. Guiochon, G. “On the Catastrophic Explosion of the AZF Plant in Toulouse.” September 21, 2001. In 8th Global Congress on Process Safety, Houston, TX: AIChE, 2012, 737-759.
3. Powers, WR. “One New York Plaza Fire, New York, N.Y., August 5, 1970.” The New York Board of Fire Underwriters, New York, 1970.
4. Slaughter, R, ed. California’s I-Zone. California State Fire Marshal, Sacramento, 1996.
5. Drysdale, DD. An Introduction to Fire Dynamics (third ed.). Wiley, Chichester, England: 2011.
6. “Reaction-to-Fire Tests for Façades.” Part 2. Large-scale Test (ISO 13785-2), Geneva, 2002.
7. National Fire Protection Association 285, Standard Fire Test Method for Evaluation of Fire Propagation Characteristics of Exterior Non-Load-Bearing Wall Assemblies Containing Combustible Components, 2012.
8. White, N and Delichatsios, M. “Fire Hazards of Exterior Wall Assemblies Containing Combustible Components.” Fire Protection Research Foundation, Quincy, MA, 2014.
9. Steiner, AJ. “Method of FireHazard Classification of Building Materials.” ASTM Bulletin, 1922, Mar. 1943.
10. Steiner, AJ. “Fire Hazard Classification of Building Materials.” Bull. of Research No. 32, Underwriters’ Laboratories, Inc., Chicago, 1944.
11. ASTM E84, Standard Test Method for Surface Burning Characteristics of Building Materials. ASTM International, 2016.
12. Schlyter, R. “Eldskyddspreparat för träkonstruktioner och textilier.” Meddelande 62. Statens Provningsanstalt, Stockholm, Sweden: 1939.
13. Nordtest Fire 002, Building Products: Ignitability (second ed.). Nordtest, Espoo, Finland: 1985.
14. Hurley, MJ. SFPE Handbook of Fire Protection Engineering (fifth ed.). Springer, New York: 2015.
15. Cote, AE, et al, eds. Fire Protection Handbook, 20th ed., NFPA, 2008.
16. “Fire-Test Methods Used in Research at the Forest Products Laboratory (No. 1443).” Forest Products Lab., Madison WI, 1959.
17. Bruce, HD. “Effects of Some Preservative Treatments on the Flammability of Wood.” Proc. Amer. Wood-Preservers Assn., 1956, 52, 11-23.
18. Schaffer, EL. “Effect of Panel Thickness and Noncombustible Inserts on Surface Flammability of Plywood (FPL-0152).” Forest Products Lab., Madison, WI, 1967.
19. Sandholzer, MW; Bender, EW; and Rhodes, C. “Evaluation of Four Test Methods for Fire Retardant Paints (Report 1555).” National Bureau of Standards, 1952.
20. Tamanini, F. “Calculations and Experiments on the Turbulent Burning of Vertical Walls in Single and Parallel Configurations (0A0E7.BU-2).” Factory Mutual Research. Norwood, MA, 1979.
21. Choi, KK and Taylor, W. “Combustibility of Insulation in Cavity Walls.” J. Fire Sciences, 1984, 2; 179-188.
22. Levins, A. “Development of Photovoltaic Array and Module Safety Requirements (DOE/JPL 955392-1).” Prepared for Jet Propulsion Laboratory, Underwriters Laboratories, 1982.
23. Backstrom, B and Tabaddor, M. “Effect of Rack Mounted Photovoltaic Modules on the Flammability of Roofing Assemblies (File No. 1N15911, R26475).” Underwriters Laboratories, Northbrook, IL, 2009; revised 2010.
24. Toong, T-Y. “A Theoretical Study of Interactions between Two Parallel Burning Fuel Plates.” Combustion & Flame; 1961, (5), 221-227.
25. American National Standard for Cleanroom Materials Flammability Test Protocol (ANSI/FM Approvals 4910). FM Global, 2004.
26. Lane, T. “Grenfell Tower: Should This Cladding Be Allowed?” bdonline.co.uk, 16 June 2017.
27. Maizland, L. “Grenfell Tower, Explained: How a Deadly Fire in London Became a Political Crisis.” vox.com, 20 June 2017.
28. Davies, R. “Grenfell Tower: Cladding Material Linked to Fire Pulled from Sale Worldwide.” The Guardian, 26 June 2017.
29. Spillett, R. “‘Killer’ Cladding was Toxic: Makers of Insulation Installed to ‘Pimp up’ Grenfell Tower Warned That It Emitted Noxious Gases When Burned.” DailyMail.com, 6 July 2017.
30. “Grenfell Tower Fire Released Hydrogen Cyanide.” Skynews.com.au (22 June 2017).
31. Babrauskas, V, Lucas, D, Eisenberg, D, Singla, V, Dedeo, M, and Blum, A. “Flame Retardants in Building Insulation: A Case for Re-evaluating Building Codes.” Building Research & Information; 2012, 40, 738-755.
32. Beitel, JJ and Evans, WR. “Multi-Story Fire Evaluation Program (SwRI Project No. 01-6112).” Southwest Research Institute, San Antonio, TX. Prepared for SPI Exterior Nonbearing Wall Task Group, The Society of the Plastics Industry, Inc., 1980.
33. “Method of Test for the Evaluation of Flammability Characteristics of Exterior, Nonload-Bearing Wall Panel Assemblies Using Foam Plastic Insulation (UBS Standard No. 17-6).” International Conference of Building Officials, Whittier, CA. Later renumbered as UBC Standard No. 26-4.
34. “External Wall Assemblies and Façade Claddings—Reaction to Fire (SP FIRE 105).” SP, Borås, Sweden, 1994.
35. “Standard Method of Fire Test of Exterior Wall Assemblies (CAN/ULC-S134-13).” Underwriters Laboratories of Canada, Scarborough, ON, 2013.
VYTO BABRAUSKAS, Ph.D., earned degrees in physics and structural engineering and a Ph.D. in fire safety. As a researcher at the National Institute of Science and Technology, he developed devices to measure the heat release rate of products and developed a computer program for modeling the development of room fires. He founded a consulting firm in 1993 and provides fire safety science expertise to fire investigation and litigation.
Related training:
The Grenfell Tower Fire: A Closer Look