VOLUNTEERS CORNER | By BRIAN DABOUL
Across the United States today, the volunteer fire service has been a challenging environment to sustain. Countless hours of answering calls for service compounded by fundraising, community outreach events, fire prevention education, ongoing training requirements, equipment maintenance, and business meetings have caused the volunteer fire service to make large cuts in its staffing levels. As people struggle to provide for their families in this economy, working multiple jobs while taking on home improvement work and raising children, fewer people can find time to dedicate to volunteering. The combination of increasing requirements for volunteer fire departments and less free time for the common resident makes volunteer fire departments tighter on staffing than ever before.
The Need for Compliance
When staffing is lacking, firefighters and officers end up holding multiple positions, causing some responsibilities to fall by the wayside and receive little to no attention. One of these commonly forgotten items is occupational health and safety compliance. It is critical to assign someone to this role within each fire department as well as to understand this is not the same role as a typical “safety officer.” When we think of a safety officer in the fire service, it is commonly someone who monitors activities during training or on the fireground to prevent unsafe actions and harm to our firefighters. The role we are talking about here is much different and just as important.
Because of outrage over working conditions and on-the-job injury rates in the workplace, the Occupational Safety and Health Act of 1970 was drafted and signed into law on December 29, 1970, by President Richard Nixon. On April 28, 1971, the Occupational Safety and Health Administration (OSHA) was officially created to enforce the act by encouraging and mandating a safe work environment. Fast forward to 2022, and OSHA is actively enforcing the standards outlined in the Code of Federal Regulations, specifically, 29 CFR Part 1910, which is what fire departments must comply with for occupational health and safety standards.
Over the past 10 years, standards enforcement in the volunteer fire service has been on the rise, leaving many departments scrambling to understand what needs to be done to gain compliance. In 2020, there was a total of 21,710 inspections, with an increase to 24,333 in 2021 across all industries. Volunteer fire departments are now more commonly experiencing routine inspections of their organizations. Typically, these inspections are conducted by agencies other than OSHA in the volunteer fire service.
For example, in New Jersey, public sector local and state level organizations are inspected and handled by the New Jersey Public Employees Occupational Safety and Health agency. Safety hazard complaints are investigated by the New Jersey Department of Labor and Workforce Development, while workplace health hazards fall under the New Jersey Department of Health. These agencies, however, are enforcing the standards created by OSHA and outlined under 29 CFR 1910.
Assign the Role
Next, let’s discuss who is responsible for this within your organization and the most common items on which to focus. As discussed earlier, it is critical that you assign this role to someone. The person assigned to manage your occupational health and safety compliance should be well experienced in the fire service and able to understand how to incorporate compliance into everyday activities without overcomplicating your standard operating procedures (SOPs). This person also may be, but does not need to be, an officer. Ultimately, the chief or top leader of the department is responsible to ensure compliance is achieved and should designate a person or multiple people to carry out these tasks.
Many times, the township in which we operate bears the ultimate responsibility of compliance, as we are technically “employees” of the township even though we are not compensated. The township may be looking to the fire department to manage compliance, so it is critical to communicate and determine where there are gaps that need to be addressed.
Compliance Items
The list of standards in 29 CFR 1910 is extensive. Let’s look at some common items of focus for the volunteer fire service.
General duty clause. The OSH Act contains what is commonly referred to as a “general duty clause,” which is commonly used to cite hazards not outlined in a specific standard. For OSHA to cite under the general duty clause, four key elements must be proven.
- The employer must have failed to keep the workplace free of a hazard to which its employees were exposed.
- The hazard must have been recognized by the employer.
- The hazard must have caused or been likely to cause serious physical injury or death.
A feasible method to correct the hazard must have been available. An example of this would be a firefighter driving a piece of apparatus while talking on his cell phone. Although there is no specific standard prohibiting this, it meets the four criteria for a general duty clause citation. In 2010, the general duty clause was used around 1,600 times. In 2018, that number dropped to around 900 citations. In 2018, there was approximately 62,000 citations showing that the general duty clause accounted for around 1.5% of those citations.
Documentation. Although there is no specific standard outlining all documentation requirements in one place, documentation is arguably one of the most important aspects of surviving an OSHA audit. If something is not documented, then, according to the audit, it never happened.
One of the most important sets of documents is your OSHA 300, 300A, and 301 forms. You are required to keep these up to date for five years into the past. The 300 form is your log of workplace injuries or illnesses. The 300A form is a summary of your 300 log that must be posted in an area for all employees to see, from February 1 until April 30 each year, for the year immediately prior. The 301 form is an incident report form, but you may create your own form as long as it is comparable and contains the same minimum information. Determining what is a recordable injury or illness is a topic for another day, but it’s something you must understand to adequately maintain these documents. Recording injuries and illnesses can be found in 29 CFR 1904.
Other documents you must keep on hand and up to date include copies of your various safety programs discussed below; SOPs; apparatus maintenance logs; certification copies; employee onboarding paperwork; personnel files; and records of fit tests, training, equipment calibration, hose tests, pump tests, ladder tests, and self-contained breathing apparatus (SCBA) inspections, just to name a few. If you can produce accurate compliant records quickly during an audit, the audit will go much smoother, and you will likely get fewer questions. Remember, record-keeping requirements for equipment may come from other sources as well, such as the National Fire Protection Association (NFPA).
Walking working surfaces (1910 Subpart D). This standard includes many items such as staircases, floors, scaffolding, and ladders. The general takeaways from this standard are to make sure your walking working surfaces are free of defects or hazards. Railings and staircases must be in good condition; elevated working areas must have edge protection; and ladders must be in good, defect-free condition. It is also advisable to keep storage areas clean and organized. Many violations have been written for storage of flammables such as gasoline or lawn equipment stored under stairwells, combustibles stacked up too close to gas-powered heaters, and clutter-causing hazards in walkways.
Emergency planning (1910 Subpart E). This standard deals primarily with emergency exit routes, emergency action plans, and fire prevention plans. Although these items may seem unnecessary to some in a fire department, they are still required. Ensure your exit routes are clear (at least the width of the doorway), exits are clearly marked with illuminated battery backup emergency exit signage, and any exterior doors not operable or not intended for use are marked “Not an Exit.”
When it comes to an emergency action plan, the standard outlines exactly what must be included in your plan in 29 CFR 1910.38. All your firefighters must be trained on the components of the emergency action plan such as evacuation routes and methods of alarm. For your fire prevention plan, find the requirements in 29 CFR 1910.39. This document outlines how your organization plans to prevent fires from occurring in your facilities as well as identifying known fire hazards such as flammables, combustible dusts, or spark-producing tools and how you plan to control those hazards. Any employer with more than 10 employees must have both plans in writing.
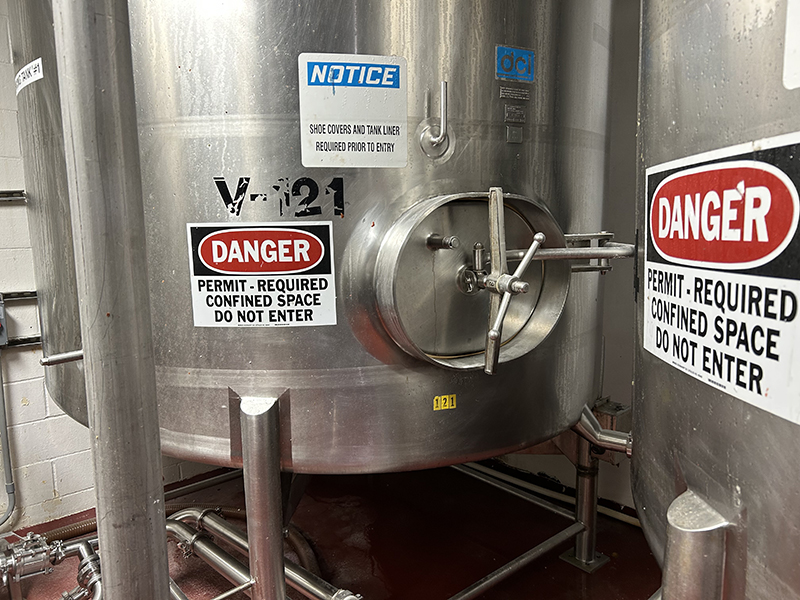
(1) A confined space entry point on a large metal storage tank. (Photos by author.)
Personal protective equipment (1910 Subpart I). This standard has sections for each type of personal protective equipment (PPE) such as hearing protection, head protection, and so on. When it comes to structural firefighting PPE, NFPA 1971, Standard on Protective Ensembles for Structural Fire Fighting and Proximity Fire Fighting, should also be reviewed alongside these standards, as it provides more specifics to the industry. Ensure your firefighters’ PPE is not outside its useful life, is inspected regularly, and is repaired or cleaned when needed. One of the most important sections of Subpart I for the fire service is 1910.134, covering respiratory protection. Your organization needs to have a written respiratory protection program that is carefully followed. Key elements include regular training, fit testing at appropriate intervals, medical clearance for respirator use, appropriate cleaning methods, storage of respirators, and methods of conducting a seal check. It is also important to establish a policy for interior firefighters that facial hair is never permitted that will interfere with the seal of a respirator; this happens time and time again where firefighters show up in pictures standing out front with an SCBA on their back and a full beard. When that picture is posted on social media the next morning, you just opened your agency up for an OSHA inspection.
General environmental controls (1910 Subpart J). This standard has multiple sections that are applicable to the volunteer fire service. Most important are the sections on permit-required confined space entries (1910.146) and the control of hazardous energy (1910.147).
Confined space entry (1910.146). Any fire department conducting confined space rescue needs to be aware of the requirements for air monitoring, ventilation, written programs, preentry requirements, sewer entry, and emergency rescue procedures outlined in 1910.146. Any good training program for awareness, operations, and technician level confined space rescue will cover these requirements, but it is always good to audit your procedures against this standard. Use the appendix documents to help ensure your program and procedures meet all requirements.
Control of hazardous energy (1910.147). Controlling hazardous energy is typically referred to as “Lockout/Tagout.” Your department must have a written program, initial/annual refresher training, and adequate lockout supplies. Typically, a fire department will use lockout/tagout for elevator rescue, confined space rescue, man in machine-related rescues, or shutdown and control of utilities. It is critical to understand how you will conduct these activities in an emergency response situation. Failure to properly control various forms of energy can result in severe injury or death to you, your fellow first responders, or the people you were called to help. It is a great idea to ask questions during activated alarms when you see heavy equipment you may be required to lock out. Ask the site supervisor to give you a quick tour before you clear that routine activated fire alarm and turn the call into a learning experience. Keep in mind that site maintenance or supervisory staff best knows the equipment and should be incorporated into any rescue situation where lockout is required. Lockout procedures are specific to each piece of machinery and can involve multiple forms of energy such as electrical, mechanical, pneumatic, hydraulic, gravitational, thermal, and even nuclear.
Electrical (1910 Subpart S). Electrical is another big item often cited during OSHA inspections. These items are low-hanging fruit and easy to spot such as exposed electrical conductors, frayed wiring, damaged cords with exposed conductors, broken plugs, missing electrical panel breaker fill plates, stray voltage from improper grounding, missing ground wires, and lack of ground fault circuit interrupter protection in wet areas. Permanent use of extension cords is another issue to look out for. Give your electrical components around the firehouse a good once over with an electrician to determine what needs to be fixed ahead of time to eliminate the hazard. I once had an inspector put a meter on a vending machine and claim there to be less than one volt detected to the frame. We were cited and decided to toss the old machine as it wasn’t being used to remediate the situation and the proposed penalty was eliminated.
Toxic and hazardous substances (1910 Subpart Z). This final section discusses the Bloodborne Pathogens standard (1910.1030) and the Hazard Communication standard (1910.1200):
Bloodborne pathogens (1910.1030). Many agencies understand this concept well and conduct annual refresher training, but it goes deeper than that. You must have a written exposure control plan. This plan outlines how to prevent and handle exposures and any documentation requirements. A big part of the plan is ensuring all your first responders have been offered the Hepatitis B vaccination. Your employees can either take the vaccination at no cost to them, decline the vaccination by signing the declination form in your exposure control plan, or provide proof of previous vaccination. Regardless of their option, that documentation must be in their medical file should an exposure or audit occur. Consult with your township first, as it may have an exposure control plan you can use.

(2) An electrical energy source locked out on a piece of machinery.
Hazard communication (1910.1200). This is another critical written program for your agency and covers how you will inform your employees of the hazardous chemicals in their workplace and how to safely use them. You must maintain safety data sheets (SDS) for every chemical on site for reference in an emergency. If you have few items, this can be easily maintained in a binder kept in a location accessible to all. If you have a lot of items or multiple facilities, subscribe to an electronic SDS management software.
It is critical to assign someone to oversee and implement your safety and health compliance proactively. With firefighting being an inherently dangerous task, safety should never become reactive. It may seem like a never-ending task, but take things one step at a time to move your department toward compliance and soon you will be looking back at the progress you and your team can be proud of.
References
Ferguson A. OSHA’s General Duty Clause. (2019). Safety and Health Magazine. Retrieved from www.safetyandhealthmagazine.com/articles/19258-oshas-general-duty-clause.
Fairfax R. Letter of Interpretation. (12/18/2003). Retrieved from www.osha.gov/laws-regs/standard interpretations/2003-12-18-1.
Rolfsen B. OSHA “Inspector Numbers Increase For First Time In Trump’s Term.” (2020). Bloomberg Law. Retrieved from www.news.bloomberglaw.com/safety/osha-inspector-numbers-increase-for-first-time-in-trumps-term.
OSHA. (2021). Enforcement Statistics. Retrieved from www.osha.gov/enforcement/ 2021-enforcement-summary.
OSHA. General Duty Clause. Retrieved from www.osha.gov/laws-regs/oshact/section5-duties.
OSHA. OSH Act. Retrieved from www.osha.gov/laws-regs/oshact/completeoshact.
OSHA. 29 CFR 1910. Retrieved from www.osha.gov/laws-regs/regulations/standardnumber/1910.
OSHA. 29 CFR 1904. Retrieved from www.osha.gov/laws-regs/regulations/standardnumber/1904.
OSHA. History. Retrieved from www.osha.gov/about-osha/30-years.
OSHA. Hazcom. Retrieved from www.osha.gov/Hazcom/global#.
BRIAN DABOUL is a 14-year veteran of the Mine Hill Township (NJ) Fire Department, spending the past five years as a chief officer and another three years as a line officer. He has also managed compliance for environmental health and safety at a senior management level in consumer goods—including in the pharmaceutical, nutraceutical, cosmetic, food, and manufacturing industries—for 13 years.