
By Dennis L. Rubin
Shift change was over by just a few minutes, and the off-going Petersburg (VA) Fire Department members were driving back to their homes for a few days of well-deserved rest before doing it all over again in 48 hours. The morning briefing conference call with all on-duty companies and chiefs was scheduled to begin in about 30 minutes. The weather was about perfect for any outdoor activities. Little did we know that we would be forgetting all desk work on October 24 and be in the fresh air all day long.
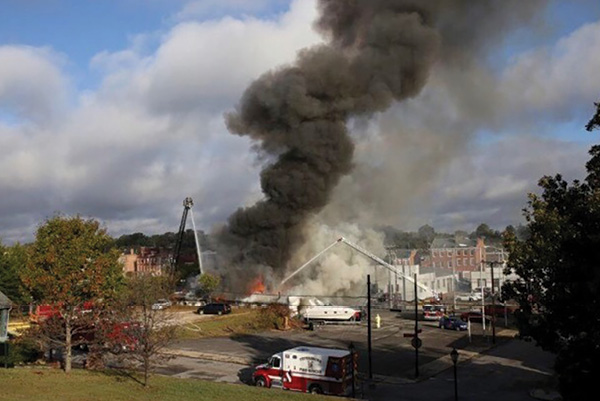
(1) Petersburg Fire Department and other Central Virginia fire departments are making an all-out attack on a very stubborn fire. It took three alarms of companies to bring this fire under control. (Photos by author.)
It was just about the time when we would be considering a second cup of coffee that the dispatch center intervened. After two alert tones, it was showtime: We were responding to a building reported to be on fire. This alarm turned out to be a major disaster for our community. Human error would raise its ugly head, and the incident would end in about a $1 million fire loss.
Petersburg Fire Department’s mission is to prevent harm to our community. We work hard to prevent fires and other emergencies from occurring in our city. However, if there is a fire, medical, rescue, or hazardous materials emergency, our firefighters are ready, willing, and able to face the challenge. We are good at what we do, and we enthusiastically face every challenge.
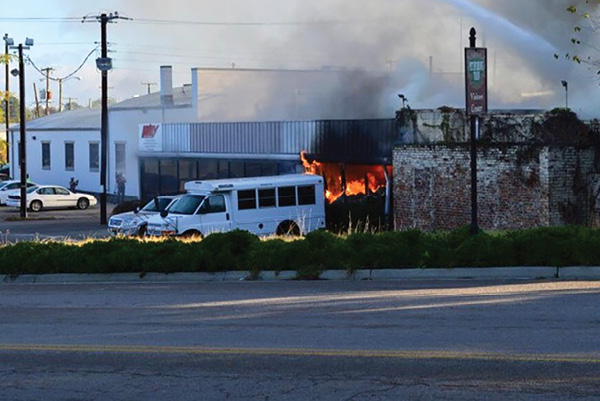

(2-3) Four elevated master streams were used to control and eventually extinguish this very stubborn fire.
Small Fires Spread Rapidly
Fire Marshal Chief Jim Reed later learned that the cause of this fire was predictable. A nearly full 55-gallon drum of a flammable product called “Tire Shine” was raised with a forklift to about the five-foot level. Once the drum was lifted into position for gravity to do its job, the employee filled one-gallon plastic containers for retail sale. As the product was being transferred from the large steel container into the plastic gallon jugs, the worker took a smoke break. As he lit his cigar, fire erupted and quickly spread in size and scope. The worker retrieved a fire extinguisher and attempted to quench the flames, to no avail. A second and then a third fire extinguisher were discharged on the now moderate-size fire. In all, seven or eight fire extinguishers were discharged in the vicinity of the burning chemicals; the fire was now impinging on the forklift’s liquefied petroleum gas (LPG) cylinder.
It was at least 10 to 15 minutes before the fire department was called. To make matters worse, the person who called the fire department told the dispatcher that “a vehicle was on fire.” Perhaps the “passerby” saw only the forklift burning. Engine 2 (from the Market Street Station) was dispatched as a single resource to handle what was initially described by the Good Samaritan as a car on fire without exposures. By now, the six or so plastic one-gallon containers were all burning along with the 55-gallon drum, which had fallen off the lift and was fully ablaze. The fire quickly extended inside the building and out into the front parking lot.

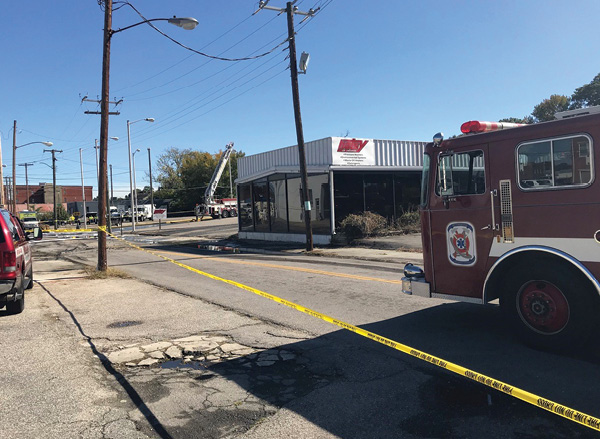
(4) Members of the Regional Hazardous Materials Response Team decontaminate a firefighter on site. (5) The aftermath of this chemical fire left the department with significant cleanup issues. Many city agencies had to coordinate their efforts to protect our citizens and the environment.
As Captain Chris Magann and Engine 2 made their way to the “car fire,” Captain Danny Partin, the on-duty acting battalion chief, heard the chatter on the police radio frequency and called to fill out the first-alarm assignment within the first few minutes.
Coincidentally, the Petersburg police station and emergency communications center were across the street and up the hill about 100 feet from the burning building. The police officers called into the Communications Center that fire was going through the roof of the structure and that quite a bit of smoke and fire were issuing from the building.
Engine 2 arrived within three minutes of the dispatch, followed by Battalion 1, who gave a brief initial report covering all six critical points.1 He cited the address, 120 E Bank Street, and reported a moderate size commercial building of Type 2 construction that was fully involved. He requested that a fourth-due engine company be added to the response. The initial incident action plan (IAP) was to start a defensive fire attack with members operating outside of the collapse zone and have Battalion 1 assume “Bank Street Command.”
The Operations
Engine 2 laid a five-inch supply line and advanced a 1¾-inch attack line to the address side of the building, side Alpha. The first-in engine company controlled the burning liquids and cooled the 20-lb. LPG cylinder. However, the fire took over the entire building and destroyed it. The strategic IAP was to establish (staff with firefighters and hoselines) four divisions to conduct an effective defensive attack. Two elevated master streams were added for cooling power. About five vehicles and a 30-foot boat were parked next to the fire building and had to be protected from the growing fire. Within the first five minutes, a second alarm was requested and staged in an area near the police station.
The staged companies (four engines, one ladder, and one battalion chief) were mutual-aid units and were on a different tactical radio channel until they were moved from staging. When they were assigned to the fire operations, each company was directed to switch to the appropriate tactical channel. The channel switch was made to limit the radio traffic and confusion that occurs at the beginning of a major incident.
Early in the operation, the material safety data sheet (MSDS) on each product was requested from the business operator, who advised that more than a dozen hazardous chemicals were inside the fire building. He said that the MSDS documents were in his office, which was now on fire. The plan was to obtain the needed human and environmental health and safety information from the vendors/suppliers. These documents were made available by the building operator six days later. The lack of this information was a problem.
The business operator’s statement about the presence of hazardous chemicals in the building and the fast flame spread prompted a request for the regional and state hazardous materials response teams. Since the chemicals were not identified, Hazmat Branch Manager Chief Wayne Hoover established a six-step filtration diking system. After the filtering steps, the runoff water (estimated at 4,000 to 4,500 gallons per minute for about two to three hours) was measured at 8.3 pH (highest reading) to 7.1 (lowest reading).
Based on this information, the city’s Water Department director and the city engineer decided to allow the runoff to be released (maintaining the filtering system) into the storm drain. Because of the volume of radio traffic generated by the Hazmat Branch, it was assigned to a separate tactical radio channel. All three channels were monitored at the command post; the incident commander managed and coordinated the flow of critical communications.
Soon, hoselines were operating in each division of the fire building. The elevated master streams were positioned in Division Bravo and Division Delta to support the handlines. After staffing each division and providing the “overhead team” positions, a third alarm was called and reported to the staging area.2 In all, a third alarm and a robust regional hazmat response were operating at the fire.
Petersburg, a small, urban city, handles about 8,000-plus calls for service each year. Two of our four fire stations were covered with two engines, one ladder truck, one battalion chief, and one medic ambulance to handle the balance of our workload. The firefight continued for several hours before the incident was declared under control. The emergency work was over, but the impact of this major fire was just being felt and its scope just being understood.
Recovery and Aftermath
When the MSDSs showed up six days later, the first-in engine company officer was closing out the fire incident report and preparing the firefighter exposure report. His plan was to incorporate the MSDS information into both reports. As he read the information on the materials involved, it became obvious that our members had been exposed to some toxic and harmful chemicals.
He passed the MSDS information up the chain of command. It was clear that more follow-up for our people and our equipment was necessary. Based on the chemical exposure at this fire, all members who were exposed received a thorough gross decontamination before leaving the fireground. Their personal protective equipment (PPE) and all tools and appliances used at this event were also decontaminated. The Hazmat Branch set up the decon corridor upstream of the makeshift straw water runoff filtering system.
On returning to quarters, members were directed to wash and dry their turnout gear using the department’s extraction washing machine with the detergent provided for that purpose and to shower as soon as possible and dress in a clean station uniform. The department believed that it had taken every necessary and known precaution to protect our people and decontaminate the equipment. With an abundance of caution, it was decided to follow up with evaluations of our members’ health risks. The equipment’s “cleanliness” was to be tested by an outside, independent, qualified consultant.
The department contracted an industrial hygiene firm in central Virginia, which was willing to look at the 14 MSDS profiles to determine if any additional steps were needed to ensure the health and safety of our members. The industrial hygienist determined that if the members used self-contained breathing apparatus (SCBA) in the hazard zone along with proper personal protective equipment, the long-term health risk was very low. The good news was that no medical follow-up or surveillance was necessary because of the required application of PPE and SCBA.
The department introduced National Fire Protection Association 1582, Standard on Comprehensive Occupational Medical Program for Fire Departments, physicals for our uniformed members in early 2018. This will serve as a final check to ensure that our employees’ health was not compromised at this fire.
However, the test results were not as positive for the turnout gear. First, we contacted the gear manufacturer of our nearly new PPE (placed in service less than two years before). The manufacturer requested that we send one set of the exposed gear for performance testing. That gear passed the flame spread test but failed the rip-strength standard. All exposed sets of turnout gear and the associated equipment (hood, gloves, and helmet liners) had to be replaced.
Lessons Learned and Reinforced
This type of fire is a low-frequency, high-risk event for our department. First, the fire was fully developed before our arrival. Our response time was less than four minutes from the time of dispatch. Next, the delay in calling the fire department was likely approaching 10 minutes. Finally, the number of chemicals and chemical blends burning was significant. A comprehensive after-action report was held. It revealed the following issues:
- Communications can always be improved, but assigning three tactical radio channels limited confusion.
- Calling for help early and often was critical in the successful handing of this alarm.
- Requesting the regional hazmat team was appropriate and determined to be necessary to protect the environment.
- Firefighter recycling/rehabilitation was important, considering that the entire Southside area had very little response capability left in reserve.
- The need for the MSDSs proved to be very important, but they were not immediately available. In this situation, the business was below the reporting requirements of SARA Title III. It’s important to identify locations such as the one involved in this incident and identify any hazmat issues during preplanning. MSDSs are useless if they’re being consumed in a fire.
- We identified the need to develop a policy relative to decontamination issues. This project is under development.
- The department hosted a Fire Fighter Cancer Awareness and Prevention program.
- Based on the size of the building and hazards involved in the fire, two incident safety officers were used to prevent unsafe acts, behaviors, and conditions.
- No firefighter or civilian injuries were reported.
Overall, this operation was very effective in extinguishing a difficult and unique fire. We learned much and gained experience in dealing with situations involving a “cocktail” of chemical hazards.
Endnotes
1. The following Virginia agencies responded to assist: Colonial Heights; Ft. Lee; Chesterfield County; Prince George’s County; Dinwiddie County; Hopewell; and Henrico Fire Departments.
2. The six points are as follows: Confirm Address. Incident Description. Incident Conditions. Request Assistance (if needed). Initial Action Plan. Assumption of Command.
Dennis L. Rubin, CEM, CFOD, CMO, is the principal partner in the fire protection consulting firm D.L. Rubin & Associates. He has served more than 35 years in the fire and rescue service. He is a field instructor with the University of Maryland Fire & Rescue Institute and an associate instructor with the Virginia Commonwealth University in Richmond and Rio Salado Community College in Mesa, Arizona. He has been an adjunct faculty member of the National Fire Academy since 1983. He is the author of Rube’s Rules for Leadership and D.C. Fire (Fire Engineering).