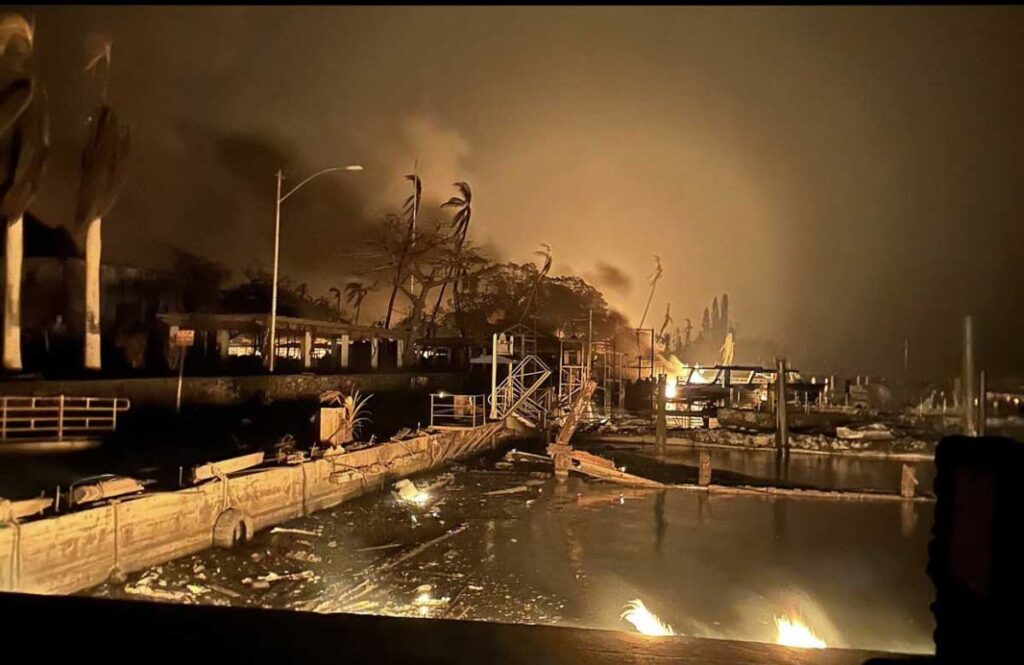
Energy Hazards | By Chris G. Greene and Greg E. Jenkins
A year has passed since the historic wildfires gripped Maui in 2023. For most, the loss and hardships may never be reconciled. For the response community, we are at a point of reflection, a tolling of decisions made and actions taken under duress. The passage of time may offer sobriety for our darkest and most desperate moments. Though much effort to support the residents of Maui and their families continues, the fire service has also begun to deliberate on lessons learned, and we have much to learn from this terrible fire.
The Maui wildfires are destined to become part of our educational apprenticeship. And we, the national response community, must ensure that our reflection is salient.
Unusually high winds coupled with tinder, dry nonnative overgrown vegetation, below-average precipitation, above-average temperatures, and a condition called flash drought all played major roles in this fire’s rapid proliferation. The transition from ground-vegetation-supported wildfire to an urban inferno took less than one hour. The outcome delivered the deadliest fire Maui has seen in more than 100 years (Figure 1). The fast-moving fires claimed 101 lives and devastated the landscape. For those who survived this tragedy, the physical and emotional scars will last a lifetime.
Figure 1. Reach of the Maui Wildfires
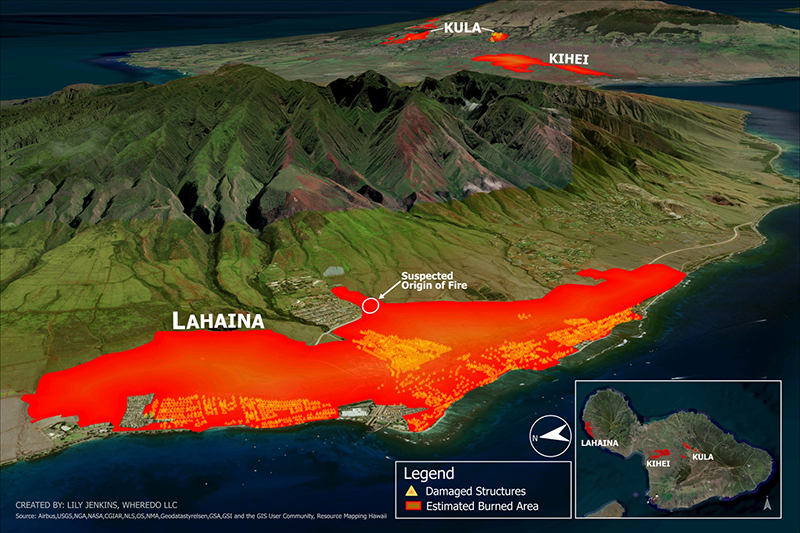
(Sources: Airbus, USGS, NGA, NASA, CGIAR, NLS, OS, NMA, Geodatastyrelsen, GSA, GSI, and the GIS user community, Resource Mapping Hawaii. (Figures courtesy of Lily Jenkins, WHEREDO LLC.)
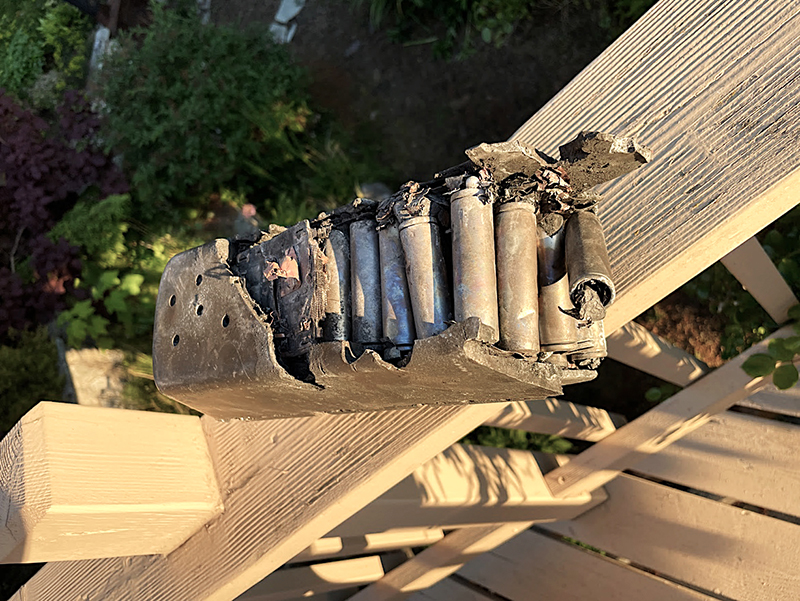
1. A thermally damaged battery casing reveals the multitude of 18650 lithium-ion cells inside. (Photo by Chris G. Greene.)
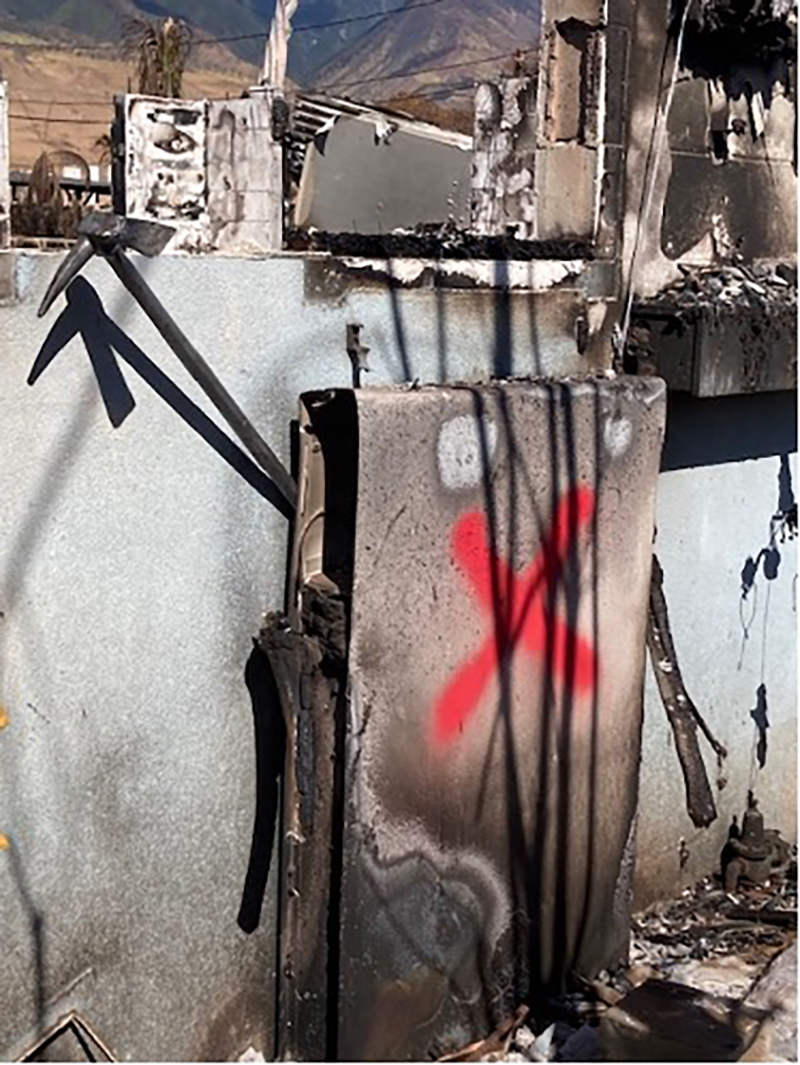
2. A lithium-ion power wall heavily damaged by fire. (Photos by Greg E. Jenkins unless otherwise noted.)
Hazard Stabilization
Processing damaged or potentially damaged lithium-ion cells involves accounting for each of the following energy hazards:
- Gas production.
- Electrical energy.
- Thermal hazards.
To neutralize the battery energy hazards, the EPA employed two complementary techniques:
- Immersion in a brine solution.
- Mechanical cell destruction.
Immersion in a Brine Solution
The brining process was generally the first step, as it was less invasive. This process, which involved submerging the cells in a mineral solution (aka brine), offered a way to draw down some of the energy. In effect, this took the edge off the energy component before initiating the more invasive stage of mechanical cell destruction. However, brine solution ingredients and methods are not equal, nor are they applicable to every situation.
Each requires independent modifications of brine solution. For example, specific consideration should be afforded to pouch cells due to the potential for the brine solution to corrode the electrode tabs, which may limit deenergizing and strand energy within the pouch cell.
Brine Solution Considerations
Energy that remains suspended in a damaged battery is considered stranded. This stranded energy results in gas, electrical, and thermal hazards for responders (Figure 2). The intent of brine cell submersion is to initiate and prompt the electrolysis process and thereby release the suspended energy. However, the composition of the solution is often the result of field experimentation (photos 3 and 4). For this situation, the team determined that a 50-50 combination solution of 6 percent sodium chloride (NaCl) and 6 percent sodium bicarbonate in water provided good reduction in voltage and state of charge.
EPA ESF #10’s Maui Wildfire Response by the Numbers
- 169: Number of parcels battery materials from energy storage systems were removed from.
- 30: Number of tons of former lithium-ion battery materials that were rendered safe and moved for recycling.
- 200: Number of tons of hazardous materials processed for disposal to the U.S. mainland by vessel and highway.
- 1,621: Number of parcels reconned for safety, energy systems, and hazardous materials.
- 94: Number of full electric and hybrid vehicles rendered safe.
First Steps
Processing an incident of this scale can be daunting. It requires collaboration from both local and federal resources. Recognizing and respecting the community loss are of the utmost importance.
The stabilization script for a fire event of this magnitude is well developed. It includes the following steps:
- Ensure full extinguishment.
- Account for losses.
- Safeguard the area so it is returned to the community as safely and expeditiously as possible.
However, the timeline for this process is under scrutiny. The Maui wildfires have exposed yet another layer of an already complicated process: the presence of high-energy battery storage and battery devices littering the fireground. The aftermath of a large urban fire landscape gives way to a massive energy field that must be accounted for. The cleanup is no longer static and predictable. Instead, it is dynamic and dangerous due to the capricious nature of lithium-ion battery energy sources.1
Accounting for the lithium-ion energy hazards was the responsibility of the United States Environmental Protection Agency’s Emergency Support Function 10 (EPA ESF #10).1 This article highlights the groundbreaking techniques developed by this team. It is understood that many of these operations were field deployed absent traditional academic supportive platforms. With that said, addressing energy hazard challenges for a scene such as this is often the forbearer for formal studies.
Investigators processed the energy hazards of this incident. They divided it into three segments:
- Identification and collection.
- Hazard stabilization.
- Transportation of processed material to the U.S. mainland.
The end goal was to return the landscape to the community free of all battery-related energy hazards.
Identification and Collection
Members tasked with this operation needed patience and temperance. Both were truly imperative for everyone’s safety. Accounting for these hazards equates to an energy-focused overhaul. It is a labor-intensive and time-consuming, block-by-block, house-by-house, vehicle-by-vehicle search for potential energy hazards.
Teams understood that they were not just looking for burned-up batteries. Most of today’s portable handheld tools use lithium-ion batteries as their energy source. However, unless the plastic casing for the tool is completely consumed, you are unlikely to see the batteries inside (photo 1). You must know the batteries are present.
Armed with an understanding of lithium-ion batteries, a well-trained crew can complete this task with confidence that they have not missed anything. Keep in mind that the incubation period between a cell being compromised and the onset of thermal runaway can be days or even weeks. And not all potential energy sources were investigated due to some material located subsurface and structural instability concerns. These conditions and structures were identified and transferred for Phase 2 of operations, led by the Army Corps of Engineers.
The EPA processed energy hazards for 1,621 properties in Kula and Lahaina. Removing the energy hazards from homes and buildings was not confined to just portable tools and e-mobility devices. Investigators also needed to consider residential and commercial energy storage systems. These often required invasive techniques and heavy equipment to be removed from a structure (photo 2).
Operating procedures developed by the EPA during the response mandated that battery material removed be secured in a way that did not allow for any product loss and would assist with containment of potential thermal events. The crew then transported this material to a predetermined staging site. Subsequently, after the accounting and collection of these batteries were complete, the team could begin the process of addressing the stored/stranded energy potential inherent in lithium-ion cells.
Figure 2. Gas, Electric, and Thermal Hazards
The gas, electrical, and thermal hazards are a result of stranded energy and/or chemistry within the battery cell or processed battery debris. Investigators must address each of these hazards for a cell to be considered processed and stable.
The solution offered the added benefit of containing the thermal hazards that often accompany the release of stranded energy. However, a perfect brine solution does not exist, and not all batteries respond well to brining. At times, the brine solution may react with a cell structure in a way that inhibits the electrolysis process necessary to draw down the energy in the cell. This anomaly was accounted for during the cell destruction portion of this process.
Throughout the response, the team maintained the brine solution for the least volume possible and never discharged it into the environment. Because Hawaii does not have the infrastructure to process many of these materials, the team had to carefully manage the collection and disposal of the brine solution. They sampled all brine solutions, remaining sludge, and surrounding soils in areas of proximity to the brining and battery destruction process. Then they tested those materials against original baseline soil results.
All brine solutions and sludge were then transferred into totes for shipment to the U.S. mainland. This amounted to a few hundred gallons of used brine solution. Pre- and post-soil test results matched, which confirmed that no cross-contamination occurred from battery processing operations to the staging area. Finally, all brine-related materials met the requirements for waste disposal and were moved under domestic regulations in approved performance packaging.
Mechanical Cell Destruction
The second stage of cell stabilization involved the physical destruction of each battery and cell. By destroying the battery cell, the energy hazards were further reduced and stabilized. Additionally, the resulting material would no longer meet the definition of a battery, per 49 CFR 171.8. (This is acutely significant when it comes time to transport this material.)

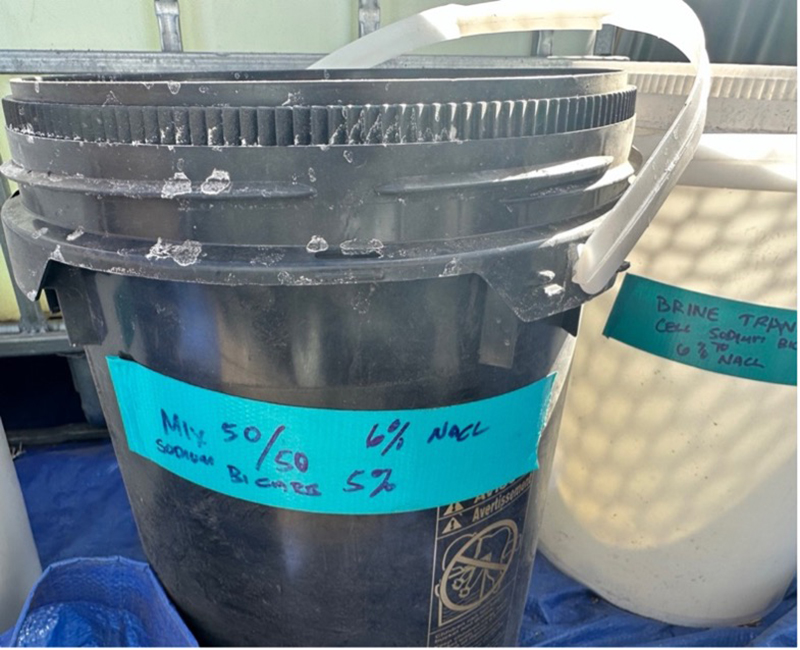
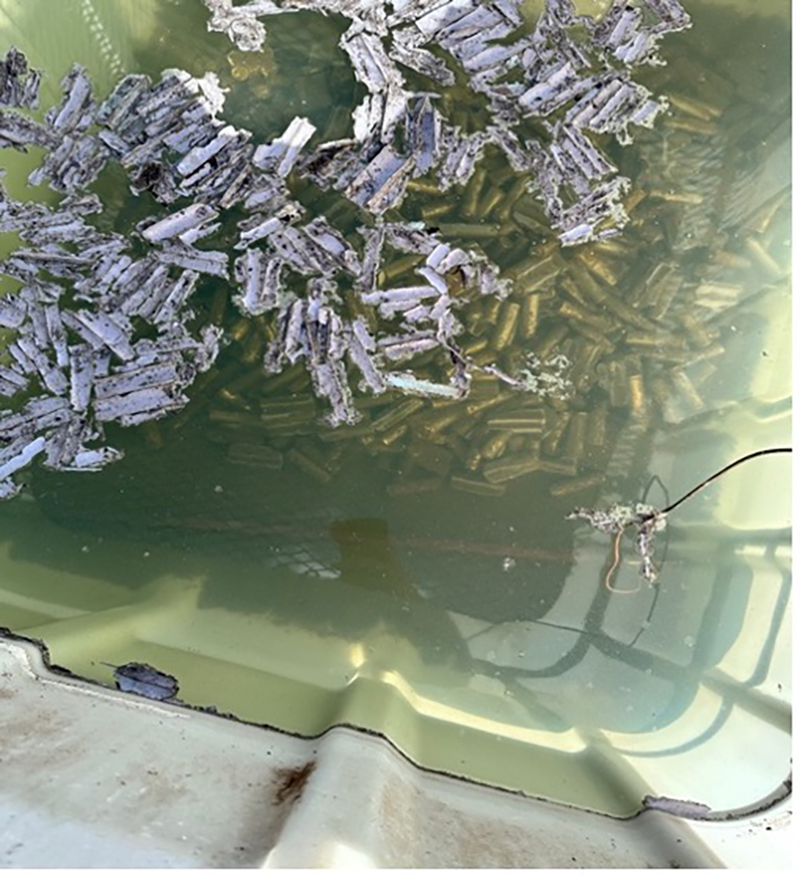
3. & 4. Bubbling and rust-colored discharge from the batteries were common reactions to the brining process. Batteries were immersed in brine until they stopped reacting with the solution. The immersion process generally lasted 72 hours; however, some cells required several weeks of brining.
Cylindrical batteries were crushed to fracture the cell, separate the current interruption device, and vent structure from the cell casing. When there was concern for stranded energy within a cylindrical cell, it was heavily brined to reduce the energy prior to the destruction process (photos 5-7).
Addressing the energy in pouch and prismatic cells proved more challenging than cylindrical cells. Processing these cells often required they be incised using an excavator shovel to destroy the cell. The EPA also considered employing aqueous grinding technology instead of common heavy equipment, but it was logistically and cost prohibitive.
Persistent Hydrogen Gas
When a lithium-ion cell fails, it releases a cocktail of gases. Some of the most concerning gases are elevated concentrations of carbon monoxide and hydrogen. Apart from vapor density, these two gases are strikingly similar. Both have large explosive ranges and low minimum ignition energy values. In short, these gases are extremely volatile and problematic when they’re confined. Accounting for this often means destroying the cells to ensure a controlled release of gases. However, the crew discovered that even after the battery was destroyed and reduced to crushed materials, the hydrogen gas persisted. It was at lower levels than before and did not bring the possibility of explosion, but the gas did remain. And this revealed yet another gap in the calculus of addressing these batteries: how to manage persistent hydrogen gas.
This begs the question: If a lithium-ion battery is reduced to metal and material debris, is this material now considered a reactive solid? And, if so, what do we do about it? In this case, the EPA had to remove the material from Maui and transport it to the U.S. mainland.
Once this material was confined into a container, detection, measurement, and management of the persistent hydrogen gas generated from thermally or physically destroyed lithium-ion battery material created the potential for a deflagration event. The hydrogen generated may have been from any combination of oxidation, electrolysis, hydrolysis, or decomposition of the former lithium-ion battery chemistries.
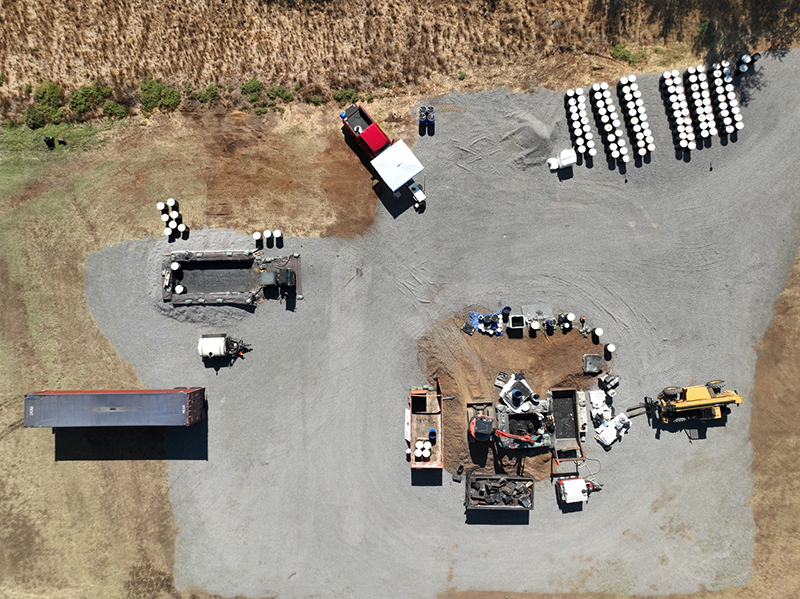
5. (A) Drum roller heavy processing area; (B) processed material containment vessels; (C) destructive processing area with brine bath containment; (D) nonbattery scrap metal; (E) trench box for emergency cooling/brining.
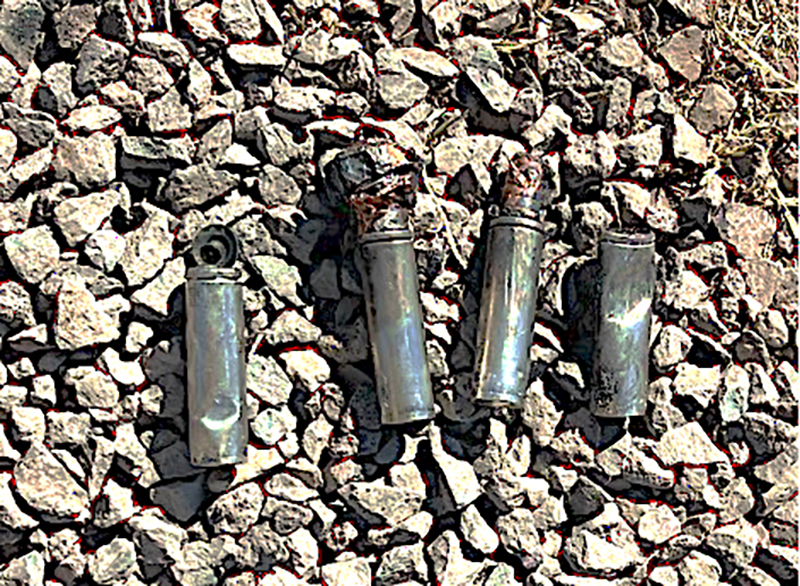
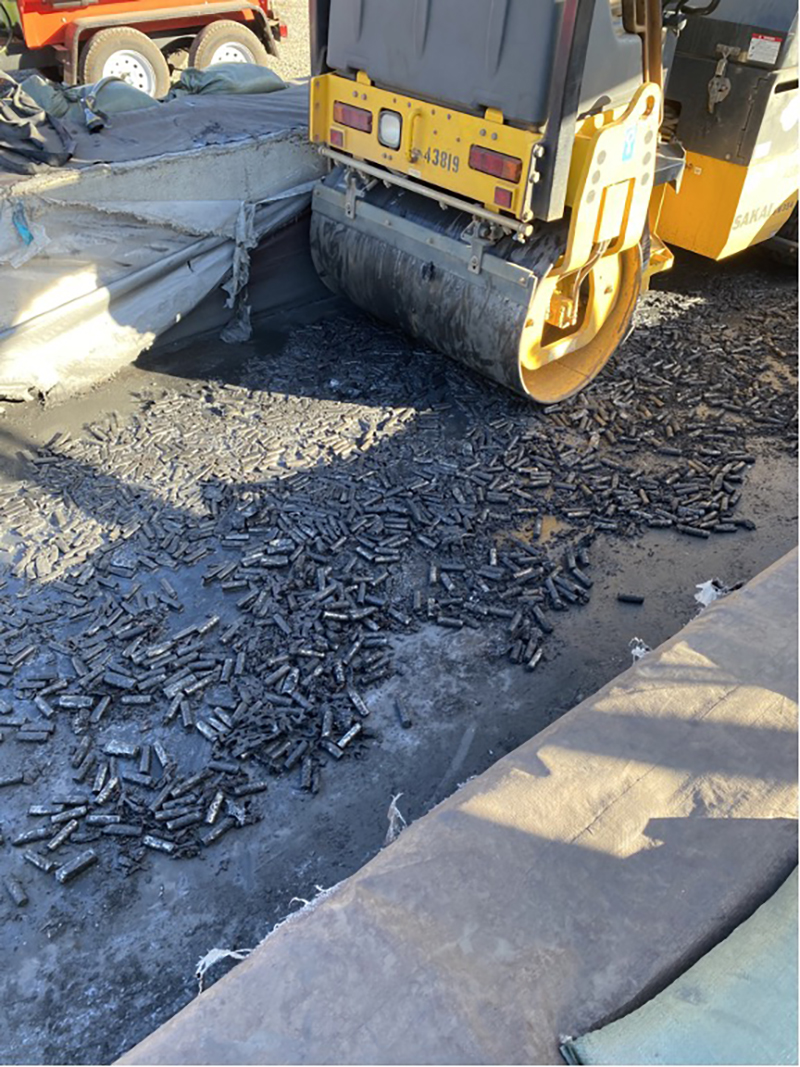
6. & 7. Heavy machinery ensured mechanical destruction of cells. Failing the current interrupt device (a safety feature of most lithium-ion-format cells, often called a CID) and housing for cylindrical cells often required a drum roller.
UN Test Method N.5 is used to determine reactivity of a solid to be considered a “dangerous when wet” substance when a specific mass of material comes into contact with water and produces a specific volume of flammable gases.2 Solid material is considered water reactive if it produces 1 liter of flammable gas per kilogram per hour.
Furthermore, using the characteristics of reactivity defined under 40 CFR 261.23, the EPA determined that the battery debris did not meet the definition of a material that is unstable, reacts violently with water, or forms potentially explosive mixtures with water.3 The combination of the material not being defined as a lithium-ion battery under 49 CFR 171.8, passing the U.N. N.5 Test, and not meeting the reactivity characteristics defined under 40 CFR 261.23 determined that the material was a nonregulated, nonhazardous waste that could be safely transported for recycling.4
However, under confinement in any airtight package such as metal drums, hydrogen could slowly build up and approach its lower explosive limit (LEL). The on-site team engineered the packaging to allow for passive ventilation of hydrogen gas. The intent of modifying the containers was to ensure that the gas remained below the 10 percent LEL for hydrogen gas (4,000 ppm). The team found that a level of 2.5 percent of the LEL was not exceeded in packages or open-top shipping containers after the material was loaded and stored for several days under targeted variable weather conditions (photos 8 and 9).
The EPA’s process of risk identification and mitigation, combined with regulatory permissibility, resulted in the maritime carrier’s acceptance of a first-of-its-kind move of such material by vessel to the U.S. mainland for recycling.
Hydrogen Gas Detection Equipment
While various toxic and explosive gases are released during a lithium-ion battery thermal event, it is the deflagration potential of hydrogen gas that has proven most disconcerting. Only a few portable detection devices are suitable for emergency response settings and have specific sensors that reliably detect hydrogen at low and high concentrations. Additionally, while some detectors may be cross-sensitive to hydrogen, they require the use of a correction factor, which results in an academic “best guess” as to the amount of hydrogen gas present.
While colorimetric tubes are available to measure specific concentrations of hydrogen and carbon monoxide, their accuracy is +/- 25 percent of the reading. Research conducted by the U.S. EPA related to the battery-stabilization stage of this incident confirmed the presence of hydrogen in thermally destroyed and former lithium-ion battery material placed in enclosed packages with direct-reading gas detection instruments outfitted with hydrogen sensors. Moving forward, in the interest of human and environmental health and safety, the U.S. EPA and its lithium-ion task force will place special emphasis on the direct detection and mitigation of hydrogen during incidents involving lithium-ion batteries.
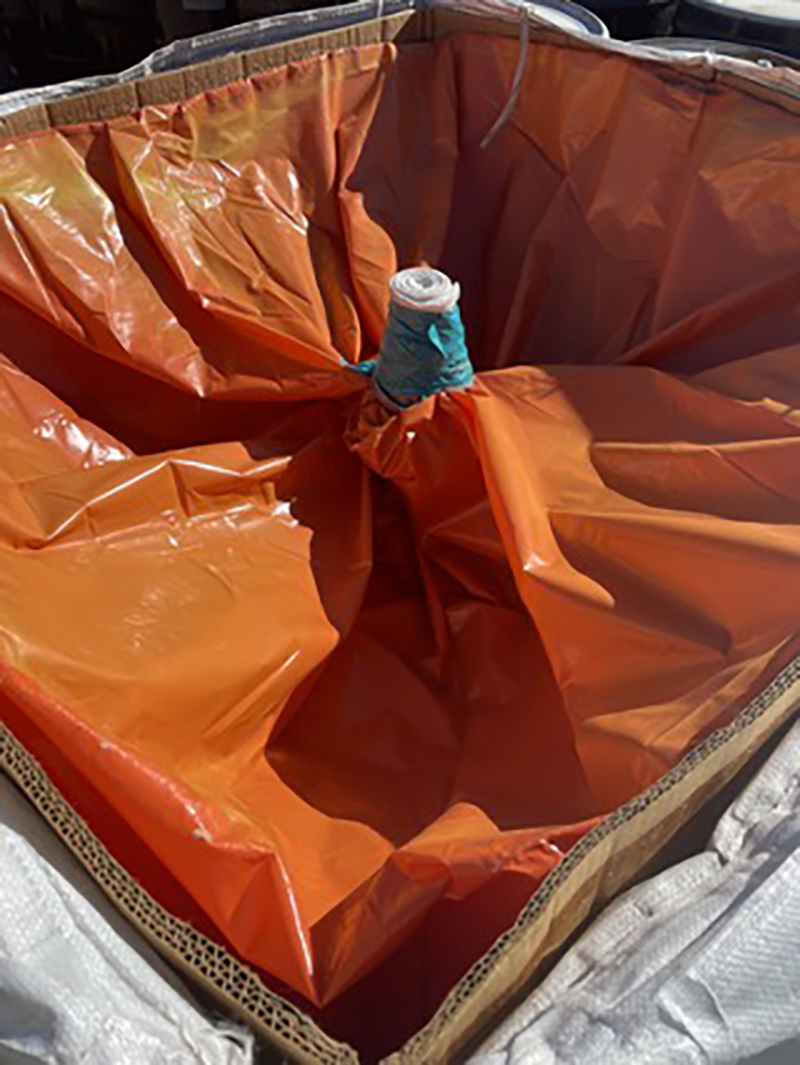
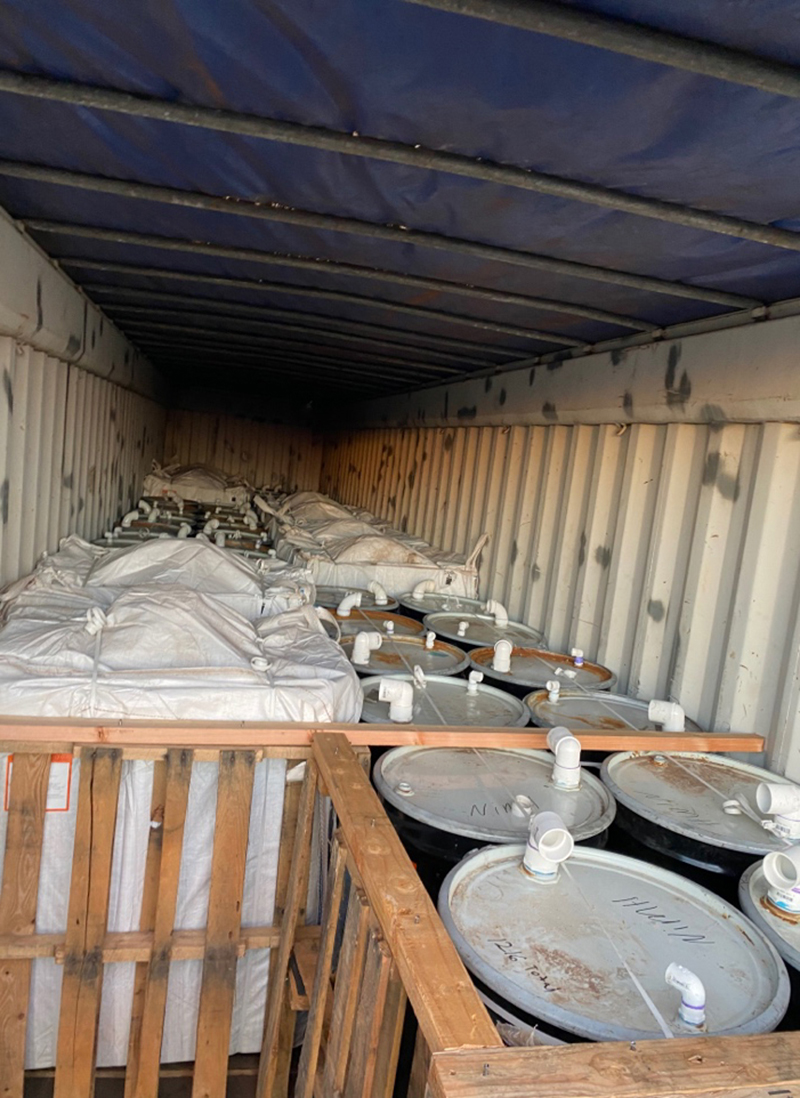
8. & 9. Processed lithium-ion cell material was contained in drums and cubic yard boxes for transport to the U.S. mainland. Drum lids were outfitted with plastic elbows (snorkels) to allow for gas ventilation while they prevented water from entering the container.
Transportation to U.S. Mainland
Another element worth discussing: maritime commercial acceptance procedures. Generally, commercial maritime carriers are risk averse on the topic of carrying damaged, defective, or recalled (DDR) lithium-ion cells or batteries. While we have regulations that allow for the movement of a DDR cell or battery in special packaging or under special permit, those regulations do not require a carrier to accept the goods for transport. According to the Code of Federal Regulations, 49 CFR 171.8 defines a lithium-ion cell or battery as a rechargeable electromechanical cell or battery.4 However, when the process reduced the cells to a condition that no longer met the definition of a battery as it applies to the transportation materials, the classification of the material to be transported changed. And by accounting for the persistent production of hydrogen gas created by the resulting materials returning to a safe level, the material was deemed safe for transport by the vessel carrier.
The initial energy-stabilization phase of this incident was concluded on November 28, 2023. The processes and procedures developed by the EPA’s ESF #10’s mission team are considered groundbreaking. Now, only time and thoughtful analysis will reveal the acuteness of their labors. However, the EPA’s steadfast commitment to ensuring the environmental health of this landscape can be captured in one word: exemplary.
Lithium-Ion Battery Toxins: Unanswered Questions
Health and safety concerns about the toxicity of gases and persistent metals released during lithium-ion battery thermal events remain a turbulent discussion. The EPA identified many gases during the battery stabilization and removal process the organization led. However, much of the focus was on hydrogen fluoride, carbon monoxide, and hydrogen, along with a standard metals analysis. Today several independent studies exist, and they’re aimed at better understanding these specific exposure concerns.
As we move forward, incidents involving battery energy sources are mounting. Absent federal funding for comprehensive, long-term studies, much of our knowledge about this hazard rests with our national responder community.
Acknowledgment: The EPA has committed efforts to ensure battery processing and stabilization techniques developed during the Maui wildfire tragedy remain open source and available for posterity.
To the local, national, and international responder communities who have provided their time and resources to support those affected by this tragedy, we say thank you.
ENDNOTES
1. Emergency Support Function #10-Oil and Hazardous Materials Response Annex. Environmental Protection Agency, 2008. bit.ly/4cCGGS7.
2. Committee of Experts on the Transport of Dangerous Goods and on the Globally Harmonized System of Classification and Labelling of Chemicals. N.5 Test for Water Reactive Materials that emit flammable or toxic gas-Status of the HM-14 Project “Test Procedures and Classification Criteria for Release of Toxic Gases from Water-Reactive Materials,” June 2013. bit.ly/4eTrQZF.
3. Title 40. Code of Federal Regulations, June 2024. bit.ly/3VJlrXW.
4. Title 49. Code of Federal Regulations, June 2024. bit.ly/4eDfWml.
CHRIS G. GREENE is a captain (ret.) with the Seattle (WA) Fire Department and the supervising officer for its Energy Response Team and Program.
GREG E. JENKINS is a Maui (HI) Fire Department hazmat captain (ret.) and a U.S. EPA contractor.