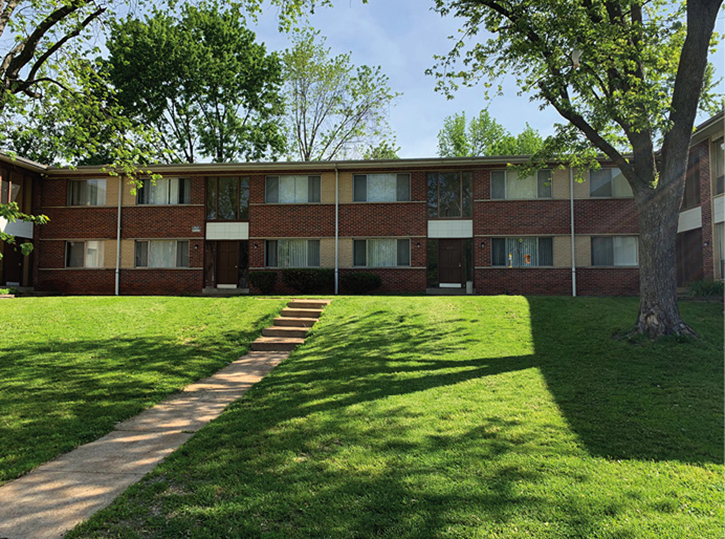
There is no shortage of articles, books, webinars, blog posts, and webcasts that provide direction for the first-due fire company at a working incident. Even with all the information available on first-due tactics, no one source covers every aspect of first-due assignments. You’ve seen and heard some of the information and ideas below before; take what you can use with the resources you have.
The focus is on tasks of which you need to be aware and for which you should be more prepared other than those of pulling lines, searching, or throwing ladders at a working fire. Although they are at the core of what a first-arriving company does, there are some areas that are just as important that will enhance your ability to do those core tasks right the first time.
As a company officer, I learned early that if we addressed the tasks perceived as “small,” my and my company’s job would be easier; and, if we did not, our job would be more difficult.
RELATED FIREFIGHTER TRAINING
First-Arriving Engine: A Progressive Fire Attack Plan
The 10 Commandments for the Company Officer: A Guide for Success Off the Fireground
We tend to take some of these steps for granted; they may seem easy and even insignificant to us. But they are some of the most important steps in the chain of events we move through when we arrive and start operating on the fireground. Intimate knowledge of all parts of the job, including those necessary actions that are less visible or noticed, is critical to the success of the first-arriving company whether you’re on a truck, an engine, or any other apparatus.
Prepare and Preplan
Preparing for the next call, whether it comes in a few hours, days, or months, must be a priority every time you cross the threshold into your engine house or volunteer hall. Preparation is not just training or drilling when it’s scheduled on the calendar; it encompasses many things. It’s an awareness and a meaningful attempt to be ready in action, skill, and knowledge so you can perform at the highest level possible without making mistakes when the margin for error is incredibly small. The frequency and intensity of your preparation could determine how successful you are when things get difficult.
The more information you have prior to arriving at a fire scene, the better the odds are of making the right decisions the first time. This is paramount and should be a regular part of the routine of every shift.
As an example, when running emergency medical services (EMS) calls, take the time to look around the house or unit and get a feel for the layout, heavy content conditions, occupant challenges, access, and so forth. If you were responding to the garden apartment complex shown in photo 1 on an EMS call, you would be able to gather information on the following: building access, the number of units, whether the building in which you are responding has challenges like disabled occupants, for example. You can note details about the construction type and the presence of open corridors, self-closing doors, and protection systems.
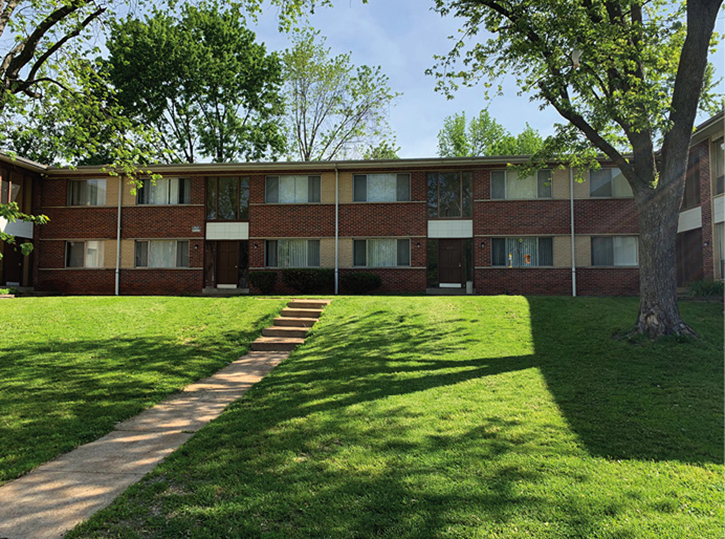
(1) Photos by author.
Ideally, you would go back to this complex and unit and start working on how long the hose stretch should be and whether a 200-foot preconnect would be sufficient or whether you will have to pull a static line. Say the building has a slope at the rear. Is it significant enough to necessitate a longer ground ladder than the one used at the front of the building? What is the quickest route to the basement? Will your aerial device reach the building with the farthest setback? Can you work around any obstructions?
From the photo, we can see that this building is the farthest from the parking lot and has two buildings on each side that form an upside down “U.” You won’t get most of these answers by just running the EMS calls; you will have to search out the answers.
Ask the owner/manager if your department can train on the premises. If you get permission, take your crews through the following evolutions:
- Stretch dry lines into the building (or use rope attached to the grab rail on the apparatus) to determine line length, challenges, and resources needed to make any unexpected adjustments.
- Place ladders of multiple lengths on the buildings, especially in places that may have significant grade changes close to the building. This will help to ensure that you grab the correct ladder the first time for rescues or firefighter egress.
- Set up and establish reach capabilities and limitations from multiple locations of the parking area. Allow space for areas where parked cars could hinder your access.
- Enter vacant units if possible. Look at the heating system, the air-conditioning units, the water heater, the electric panel, and any other utilities. Also, look for attic accesses and gas shutoff valves. I was the incident commander at a mutual-aid fire in an apartment building that started in the basement and was gas fed. This fire became more complicated than it should have been mostly because we could not find the exterior gas shutoffs and the meters were in the basement where the seat of the fire was. After the fire, we found that the gas valves on the outside of the building were blocked by some thick shrubbery. Had we found those valves early, we likely would not have had the problems we had and would have wrapped up much earlier, with less damage. The more familiar you are with a structure, the more effective you will be during an incident.
- If possible, with permission, get to the roof and check out the details. See what it feels like normally. Look for the locations of the dead loads. Will wires encumber or be a hazard to your operations? Is there a parapet? If so, how tall is it?
- Look at sublevel components, especially the floor system’s construction type. Are there exterior access and egress components? What are the window sizes and locations? Is the basement compartmentalized and cut up or is it one large open space? In single-family homes, these construction components may be common in many subdivisions but are not a given. However, the layouts and features may be the same as or similar in home communities built by one builder.
- Don’t overlook apparatus access. Is the entrance wide or narrow? What are the turning angles? Will it be difficult for additional apparatus to get into a strong, strategic position? For rural responses, will you need room for long hoselays for rural water supply options? Is there room and are conditions optimal for aerial apparatus?
These are just a few items to look for when investigating your initial response area. Your understanding of/ familiarity with the occupancy is the background knowledge that will assist you in making better and more accurate decisions. Of course, there are additional items that may not be listed above; gather as much data as possible on your response area. It’s all part of being well-armed when you arrive for the fight.
Check Your Equipment
Preparation includes checking your equipment frequently. I learned this lesson the hard way. In my experience, when this is a problem, its cause is complacency. Checking equipment is a critical part of your everyday routine, whether it’s on the truck, you carry it, or you wear it. Institute a solid and meaningful routine that requires a thorough check of things. The following rules helped us to ensure that our equipment was always ready for the next call.
- Check everything when you come on shift. Make sure that everything is in good working order and in its place. The oncoming and off-going officers must communicate! If something is missing, they must say so! There shouldn’t be any surprises.
- Check everything after switching into or out of an apparatus. If neglected, a driver may not notice that the booster tank was empty after the apparatus came back from repair work, the carbon monoxide (CO) monitor was left on the spare apparatus and was not available for a CO call, and a nozzle was missing on a crosslay after it was transferred to the spare unit. Since no one reported it missing, it wasn’t transferred back to the front line unit when it was placed back in service. Luckily, all these oversights and others were caught and rectified without incident. But all could have had some serious, even catastrophic, consequences for a first-due company—all because of complacency.
- Check everything after a significant incident where equipment was used. Once you leave the apparatus to perform required tasks, the driver/operator should keep track of the equipment on the apparatus. We know, though, that when things get busy and companies need equipment, they don’t always convey this to the driver/operator. On the call we should inventory what was used or was believed to have been used. At the house during cleanup, we give everything a once-over just to make sure.
- Fill the booster tank after any use before returning to the station. We added this rule later. It sounds simple, but I’ve seen it, done it, and heard stories of companies waiting until they got back in the house to refill and they got caught en route. It doesn’t matter whether it’s a grass fire, a trash fire, a mulch fire, or a car fire when you still might have most of the booster tank. The rule must be to always fill if you are in service. If you are returning out of service for cleanup but then have to jump to a fire, you have to have a full booster tank—no exceptions.
Training Practice vs. Incident Use
Something we learned from training was that we don’t always check our equipment in the same manner as we would use it at a fire or an incident. This became apparent during Mayday and survival training, and it is something I’ve validated in classes through demonstration. It was and still is common for firefighters and officers to check seat-mounted self-contained breathing apparatus (SCBA) units in a way that builds a habit that could cause problems on the fireground.
As the fire officer and jump seat behind the officer both approach the passenger side of the apparatus, we open the door and the SCBA will be to our left. The way I was initially taught to perform my daily check was to lay the unit down in the seat with the bottle facing up (photo 2). I would reach with my left hand to turn on the main valve while holding the mask and connect to the regulator in my right hand. Once the valve was turned on, I would hold the mask to my face and breathe off it and pick up the pressure gauge/personal alert safety system (PASS) device with my left hand. I would then reach back to the valve with my left hand and turn off the cylinder, breathing down the last bit of air on my mask, and allow the PASS to sound and then turn it off. I would then put the SCBA back in its bracket in the seat.
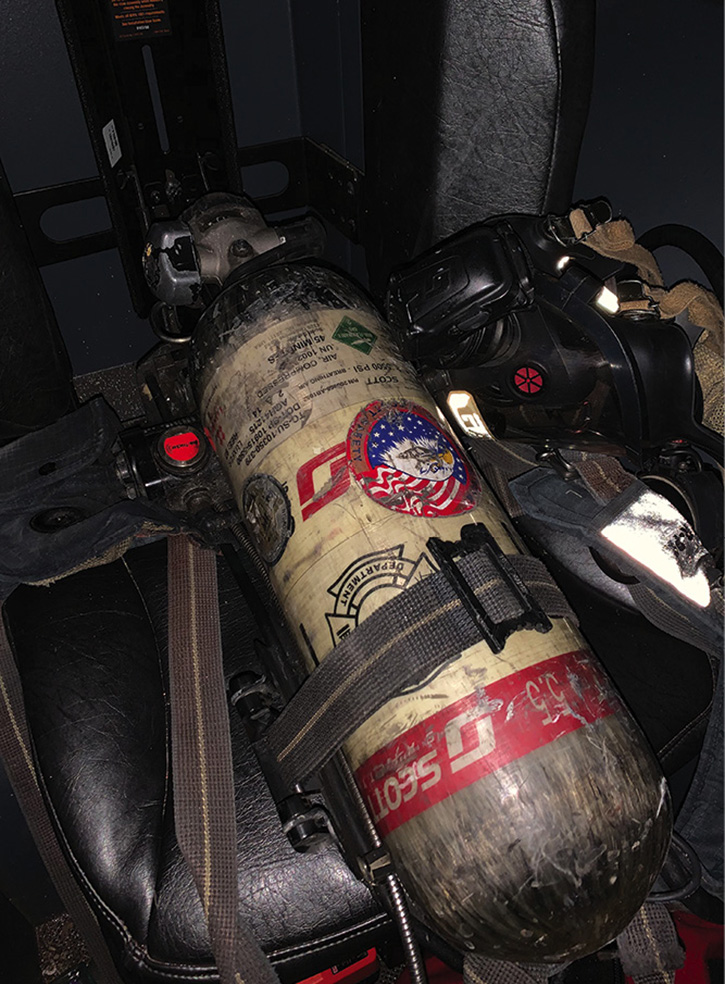
(2)
I’m not saying there is anything wrong with this, and there are some variations that may be unique to your specific SCBA brand that will not match what I just described. In my experience teaching and discussing this topic, I’ve found that the experience of a large majority matches what I just described. We realized that under pressure, as in Mayday and survival training, firefighters and officers revert to muscle memory.
Here is the issue: When we wear these packs on our backs, as we would at an incident, all the components we manipulated are positioned opposite of the way we checked the SCBA. On our back, we would reach behind us with our right hand and turn it on or check it—opposite from how we checked it. While wearing the pack on our back, the regulator is on our left chest strap and is manipulated mostly with our left hand; this is not so when we check it. Our regulator and, most importantly, our integrated PASS device are on our right shoulder; however, when we check it and look at it, we are commonly using our left hand. Reaching for the PASS device was what we noticed. We couldn’t understand why so many firefighters were reaching with their left hand to their left chest looking for that component. It was habit, and I demonstrated this in a classroom setting in several presentations.
The point is to check your equipment the way you use it. It’s not that difficult to sit in the seat and put the straps on your shoulders and then go through your SCBA check procedures. It creates muscle memory and habits, regardless of the positioning of your components, that are conducive to what you will need on the fireground.
When it comes to checking and preparing your equipment and apparatus, there some things you can do to make your deployment more effective and save time. Following are a few tips (not shortcuts) you can incorporate in preparing your apparatus and equipment. This list is not exclusive, and you may have your own tips. The key is to have a system that works and ensures that all your equipment is ready and fully operational.
Don’t Just Sit There; Do Something!
Our actions as the first due will largely depend on how we drill and train. How we spend our hours of downtime will determine how well we perform on the fireground.
Just as we’ll never get better only by running calls, we are unlikely to reach our potential and be as effective as we need to be if we train only when it’s on the calendar. We must supplement our training with realistic drills and preplanning our response area.
When responding to an alarm sounding in a closed occupancy, don’t just enter or wait for a key holder; use this time to develop and enhance your skills. Our department received an alarm at a medical building. It was nighttime, and the lock box key didn’t work. A key holder was 30 minutes away. In the past, we would have just sat on the front bumper and talked. This time, we practiced spotting the aerial device with a candidate driver, which also allowed us to check the roof and the heating, ventilation, and air-conditioning (HVAC) units (photo 3).
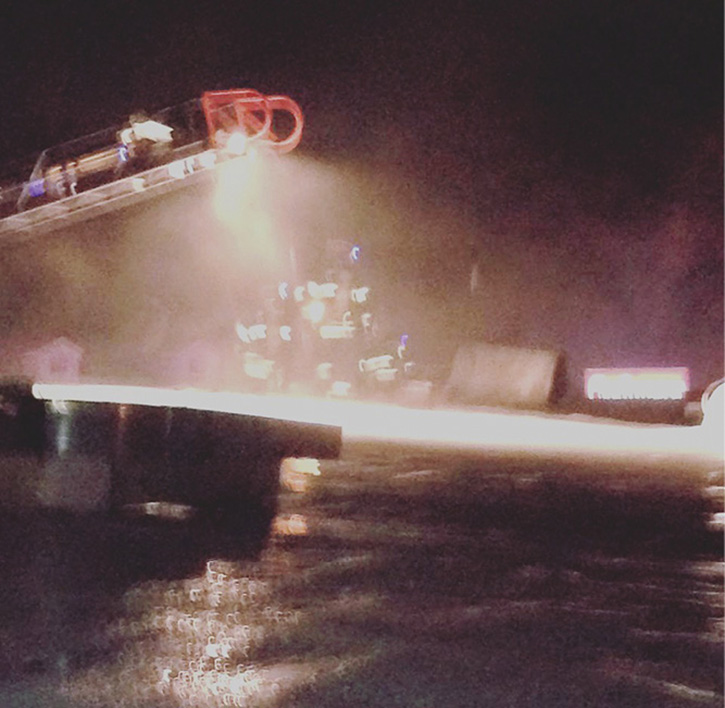
(3)
It’s too easy to do nothing and just wait for the key holder. These opportunities are readily available in various forms. Such incidents also allow us to use buildings in our response area instead of a drill ground with a tower.
In the medical building call above, we had to deal with a short parapet, darkness, using our lighting to spot the aerial, and evaluating the roof using hand lights. This was not earth shattering, but it certainly was different from the drill ground.
Drilling with purpose simply means that you are trying to accomplish specific intentions and outcomes. You might say that every drill has intention and purpose, but it is also quite possible to go through the motions or do the same drills over and over without learning the lessons from them and improving the drills for the next time.
Adapting Equipment to Needs
The quint on which I was the company officer operated as an engine and as a truck company. The standard operating guidelines (SOGs) dictated that our assignments depended on the order in which we arrived, not the apparatus type. It worked well. We knew we had some limitations and would routinely drill and train to overcome them or to find new challenges with our equipment and deployment packages.
With a 105-foot quint, we were challenged trying to use a ladder truck as an engine. We had limited ground ladders and water availability and shorter and fewer hosebed options because of the lack of compartment space. None of this was a deal breaker, but without going into things like limited hosebed configurations and booster tank size, we subjected ourselves to making an error.
Our hosebed configuration was a slide tray from the rear, along with our ground ladders, which resulted in a small booster tank capacity—less than 500 gallons vs. the 750 gallons we would have had in an engine (photo 4). In the hosebed, we had 800 feet of four-inch large-diameter hose (LDH) in one tray. In the other tray, we had 350 feet of three-inch hose with 100 feet of 1¾-inch hose for an extended attack line or a garden stretch. This was not a huge deal, but it limited our capabilities.
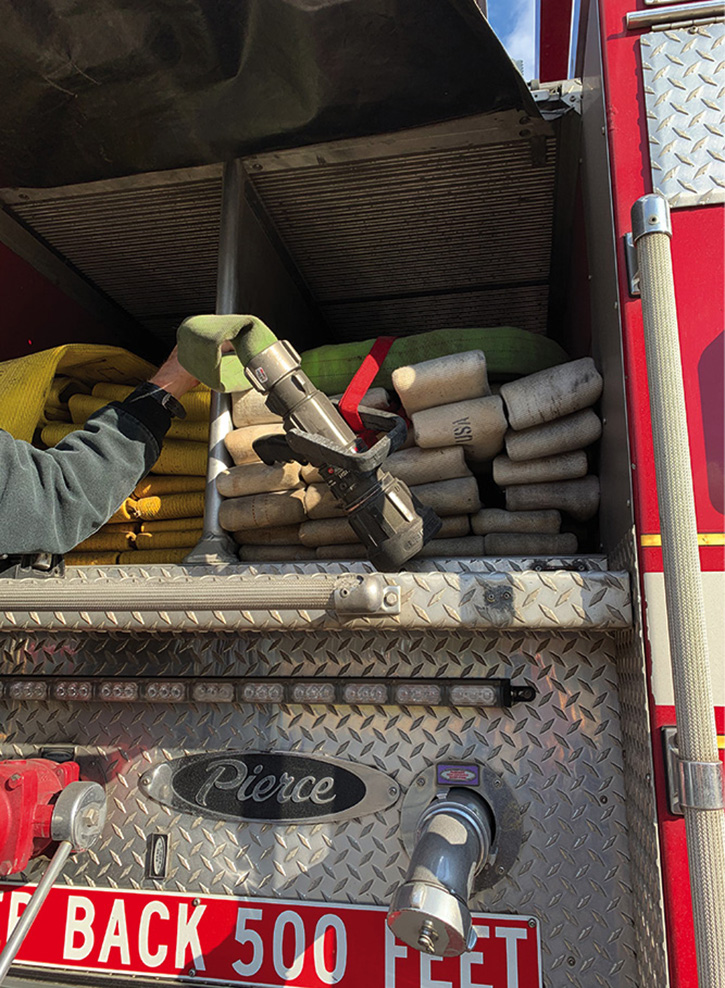
(4)
As a point of clarification, using the formula from the National Wildfire Coordinating Group in Table 1, 350 feet of three-inch hose connected to 100 feet of 1¾-inch hose filled with water would hold approximately 140 gallons of water, not including the 30 to 40 gallons you don’t get out of the pump. Table 1 shows the comparative capacities for various hose sizes.
Through drilling and flow testing, we also found that if we pulled that garden stretch and deployed it without a secure water supply, we cut our flow time in half. We discovered that only by looking at the apartment complexes mentioned earlier in the article and testing our flow rates. We ran the drills with and without a water source, looking at the different possibilities. With the decreased booster tank capacity, if we pulled the garden load, we would need to secure our own water supply to ensure we didn’t run out of water too quickly, resulting in an inadequate fire attack.
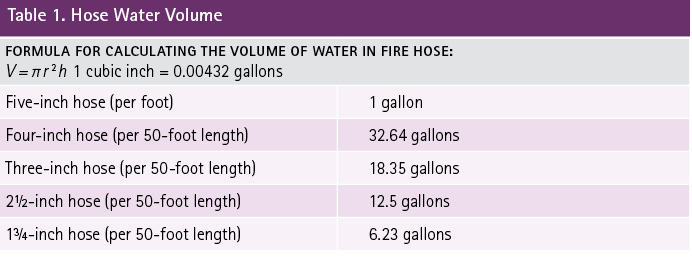
Deciding to pull the garden stretch is predicated on knowing the complex and the specific building to which you are responding. Knowing all that information, the company officer would know, based on the dispatch information, that with a working fire, we would not have enough length with a preconnected line. Using the garden stretch would require us to secure our own water supply and deployment will take a little longer than normal because of the distance from the parking lot. The gathering of that knowledge on which to base the decision started with the company’s visit to the apartment complex and response preparation days, weeks, or months earlier.
Knowing and Adapting SOGs
I can’t overstate the importance of having and operating with solid SOGs. A fire department must have a template for operations at incidents based on recognized standards and best practices. The template should consider the department’s resources and capabilities. Adopting a large urban department’s SOGs for a small or medium department could present severe challenges and failure. We must be realistic in what we can accomplish with what we have and not overreach.
A small department will find it difficult to complete all the assignments contained in the SOGs of a large department for making assignments for eight units. Creating realistic SOGs with clear tactical priorities is key for the first due and all other incoming units to operate effectively.
The SOGs should allow the officer license to adapt to the conditions within a set of parameters that might vary from the SOGs’ specifics. First-due officers must understand that, if conditions require it, they must call an audible to change the plan to improve effectiveness and achieve the desired outcome. On the fireground, I have witnessed officers sticking so precisely to the playbook that it caused problems or made their tactics less effective.
I am not endorsing freelancing or reckless behavior. Follow the SOG whenever possible; only in rare instances should you vary from it. But such exceptions do exist, and the first-due officer must set that tone early.
One exception occurred at a fire we responded to that included an exposure house on the D side. Our SOG says the first due is fire attack and/or rescue, and the second due will secure the water supply. The first due was our quint. Although it was not the old 105-foot aerial as when I was on the truck, it still has the limitations of a quint. As the company arrived, they could see the fire building and the exposure building. A hydrant was within 150 feet of the address. In the incident video, I could see the apparatus hesitate and then proceed to the scene without laying line for water supply.
The officer chose not to lay the line; he followed the SOG. The only issue was that his plan included pulling a 2½-inch line with a one-member monitor and a 1¾-inch handline to move toward the fire building. Additionally, the second due came from the opposite direction and did not connect to the hydrant. After I discussed this with the first-due officer, we agreed that his first instinct was correct and that the action would still meet the SOG’s intent and would have made his initial attack more effective. We won’t consider second due; they simply made a mistake and should have made the supply from their direction.
The point is, don’t box yourself in. The first unit’s not getting a water supply at this fire did not result in a bad outcome. The building was saved, no occupants were home, the exposure building was protected, and fire damage was limited to what the firefighters found when they started their attack. We want our officers, especially our first due, to make decisions based on the SOGs, but we also want them to use the information, education, knowledge, and experience to make a productive and an effective change when it’s needed.
If the first due does make a change, it must be communicated to the incoming units so that everyone understands what still needs to be done and takes assignments appropriately. We can’t leave those incoming units in the lurch and unaware of any changes that the first-due company had made.
It comes back to understanding your capabilities, resources, and recon information gained from getting out and training and drilling. Everything we do in preparation leading up to that fire should include what might cause us to override a portion of the SOG and do something just a little out of order or different based on what we know.
For the first-due officer to be able to call that audible, he must first intimately know the procedures and guidelines. Without that knowledge and background, whatever changes he may make or request would be freelancing. If he changes the order or makes a tactical decision that differs from the SOG, he must base it on conditions, training, and information. It’s not a free pass and is not something that should happen often.
The importance of gathering and obtaining as much information and experience as possible is critical for the first-due officer to make the best decisions on the fireground.
JASON HOEVELMANN is the chief of the Florissant Valley (MO) Fire Protection District. He has more than 30 years of combined fire service experience. Hoevelmann is the author of No Exceptions Leadership and The New Company Officer (Fire Engineering, 2018). He is an FDIC International advisory board member and presents at FDIC International and other conferences.