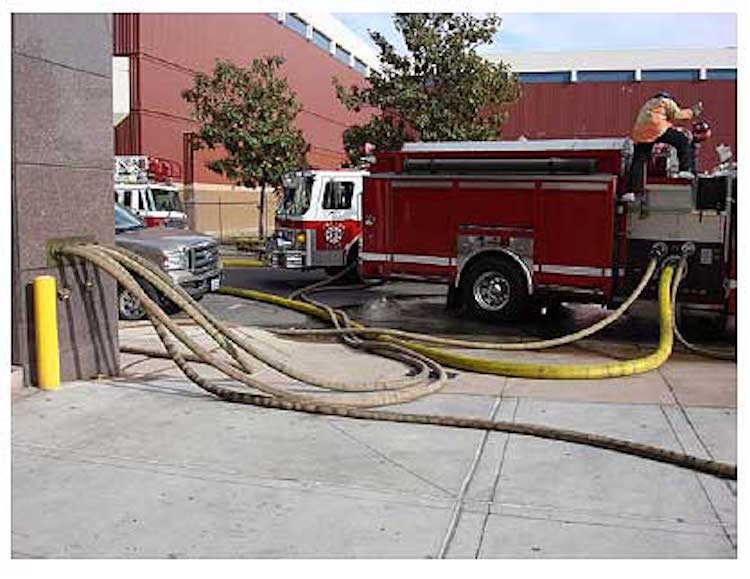
By Paul Shapiro
(1)
Developing the required flow through the stream-producing nozzle is crucial to the overall success of any fire attack. Producing a fire stream requires a positive pressure to deliver the water, which is the reason we have pumps in our engine companies. The pump has to be able to develop enough pressure to overcome pressure losses in the hose evolution being used. For the most part, this is not a problem. The only pressure limitations in an operation are the maximum allowed pressures of the hose and water-delivery equipment, which is set by the manufacturers themselves.
RELATED FIREFIGHTER TRAINING
FDC Tandem Pumping: High-Rise Building Fire Pumping Operations
Improper Staging Can Set a High-Rise Operation Up for Failure
High-Rise Firefighting Lessons Learned
Standpipe Systems: Stretching from the Street
What about developing flows inside a structure using its building fire protection system for a part of the water-delivery evolution? (Photo 1) It should be noted that from the beginning, the pressure rating of fire protection systems was based on the given that the handline being used from the standpipe would be 100 feet of 2½-inch hose using a 1 1/8-inch smooth bore nozzle at 50 pounds per square in (psi) nozzle pressure. This equates to a 265 gallons-per-minute (gpm) flow, thus the 65-psi standpipe residual pressure. In 1993, the National Fire Protection Association (NFPA) code changed requiring the standpipe residual pressure to be 100 psi. I am not sure if this number reflects a certain size handline, but the bottom line is that 35 psi more is now available to deliver more water. It’s important to know that this new code is not retroactive, so the 65-psi systems are still out there.
A high-rise water delivery operation, because of the restrictions in the building system itself, can significantly increase the required pressures needed just to get to the handline evolution to create a sufficient fire stream. Besides the low-system pressure potential, other restrictions can include elevation loss, plumbing friction loss, pressure-regulating devices, pressure-reducing valves, and pressure-restricting devices. These problems can be there whether the system is supplied directly from a municipal or a property water system or indirectly from city water to an in-house pump and then through the standpipe system.
Because of these restriction issues, the trend is to use one type of handline, the 2½-inch with a 1 1/8inch smooth bore tip. This option, because of its low operating pressure characteristics, ensures that the handline will handle any and all fire and system situations to the fullest potential.
There are other factors besides the plumbed fire protection system to consider for the flow requirements needed from the handline. The time needed to actually get water on the fire is delayed because of the logistics of getting people to the fire floor. This coupled with the fact that large open floor plans together with the modern more combustible fuels used in today’s products and the possibility of wind-driven fires all contribute to a big fire potential requiring big gpm flows to extinguish.
Two things can be done to offset low-system pressures with fire department pumping apparatus. Fire departments must be able to take over a system with pumping apparatus when applicable and supply the system by matching the system pressure. It’s important to remember that when a flow starts from a system supplied from the building pump, the residual pressure starts dropping. If additional flow is added, the residual pressure will continue to drop. This will lead to inadequate streams. When the fire department pumping apparatus take over the system, they continue pumping the system at the system pressure; however, unlike the building pump, the fire department units have the ability to maintain the pressure with throttle control whereas the building pumps do not.
Also, if you need pressure higher than the system can provide and the higher pressure can make the difference between the failure of the suppression operation and the possible successful extinguishment, a preplan of the building should indicate what the maximum pressure can be. If that is not known, the following rules shall apply:
All systems need to have a hydrostatic test done for the system to be certified. The code states that a minimum hydrostatic pressure test of 200 psi must be obtained for systems with system pressures up to 150 psi. For systems higher than 150 psi, the system shall be hydrostatically tested to 50 psi above system pressure.
Example: The Fitzgerald hotel in Las Vegas is a 36-story building and has a system pressure of 250 psi based on NFPA codes. This is a pre-93 building with a 65 psi standpipe residual pressure. The system was hydrostatically certified at 300 psi, again per NFPA. This pressure range allows us to add 50 psi to the system pressure to possibly assist in increasing the standpipe residual pressure.
Note: Even though all building systems are hydrostatically tested, older building systems could have a potential for leakage, or worse, under higher pressures or, for that matter, any pressure. Over-pumping is a last resort. Know your buildings.
Another interesting fact about system pressure requirements comes from the Underwriter’s Laboratories codes. They require a 5 to 1 pressure safety margin in all material used in the construction of the plumbed system itself.
There is something else that can be done to offset low system pressures, modify the design of the high-rise handline. The high-rise handline needs to be as easy as possible to deploy and flow adequate water in a usable stream.
(2) Fire department pumping apparatus can increase the pressure in the systems, sometimes significantly.
The key to moving adequate water in a high-rise/low-pressure system is to have a handline that offers the required water in an effective firefighting stream with the least amount of pressure loss–in other words, low-pressure nozzles and hose with low friction-loss characteristics. Secondary to this, the hose should be able to be deployed and used as efficiently as possible.
The low-pressure nozzles can be smooth bore or combination. An optimal nozzle pressure of 50 psi works well; a slightly lower or slightly higher nozzle pressure produced from a system pressure may also work. Just remember that the lower pressure equates to a lower flow and reach.
The truth of the matter is that a 2½-inch handline will work best in delivering the most water in any high-rise scenario with low- or high-pressure systems and with big or small fires. You can’t go wrong with this choice. The trade-off is difficult hose handling.
Many fire departments use only the 2½-inch handline; some use smaller lines as well. The Los Angeles (CA) Fire Department (a highly respected department that has had its share of high-rise fires) uses a high-rise attack line made up of lightweight 2-inch hose with a fixed-gallonage combination nozzle, and has been very successful with that combination. Of course, it also has the option of bringing up 2½-inch if needed.
The following information shows the capabilities of the 2½-inch handline as well as other hose diameter options that may be usable under specific conditions. It is up to each department to decide what to use.
RELATED FIREFIGHTER TRAINING
Q & A: Bill Gustin on Standpipe Operations
Training Minutes: Four Critical Points for Standpipe Operations
Engine Company Operations: Words of Wisdom on Moving the Big Water
Smooth Bore vs. Combination…and the Beat Goes On
A series of flow tests were conducted to analyze several types of high-rise hose pack combinations. The tests involved 1¾-inch (actually 1.88-inch), 2-inch, and 2½-inch lines–all 150 feet long. Smooth bore nozzles, sizes 15/16-, 1-, 1 1/8-, 1 ¼-, 1 3/8-, and 1½-inch were used as well as a specialty type large bore tip nozzle. These nozzles were chosen because of their low-pressure operation characteristics and the ability to flush debris.
There are those who think that combination nozzles are not good for high-rise applications because of the potential for debris from the standpipe system to clog the nozzle. Some departments, however, have successfully fought high-rise fires with combination nozzles; therefore, this test will include one. It is a fixed-gallonage, 150-gpm at 50-psi combination nozzle used with a break-apart nozzle valve in conjunction with a 15/16-inch tip. Remember, the purpose of this article is to show several choices.
(3)
The first set of tests were done ranging from a worst-case scenario situation (a low system pressure to a fairly high pressure simulating a newer system with a higher system pressure or a building system taken over by fire department apparatus). The standpipe pressures used in the tests ranged from 30 psi to 150 psi.
To ensure the accuracy of these tests, calibrated inline and pitot pressure gauges were used to measure the standpipe, nozzle base pressure, and exit or nozzle pressures. A calibrated flow meter was used to measure the flow of the combination and large-bore tip nozzles, since they can’t be pitoted for flow readings.
(4-5) An assortment of gauges as well as a flow meter assured test accuracy.
The hose used for the tests represented the best suited for high-rise firefighting because of its pressure-reducing characteristics. The following is a list of hose used in the tests with their corresponding weight per 50 feet of coupled hose:
- 1¾-inch (1.88), 20 pounds
- 2 inch, high-rise, 19 pounds
- 2½-inch, 23 pounds
You will note that the 1¾-inch hose is actually a little larger, measuring out at 1.88 inches (roughly 1 7/8 inches). For some reason, the fire hose industry has been allowed some leniency as it relates to the actual inside diameter of 1 3¾-inch hose. Some manufacturers have increased the size while still calling it “1 ¾-inch hose. This is not necessarily a bad thing. This larger than 1¾-inch hose has allowed for more flow because of less friction loss, and it virtually weighs the same or less than standard 1¾-inch hose uncharged. It is for this reason that this specific type of 1 ¾-inch hose, which is actually 1.88 inches) was evaluated for high-rise use.
Finally, to ensure complete accuracy of the tests, all hose was measured to see if the hose was actually the correct measurement. A common problem with fire hose is that it is not always the true measurement that is in the specs. In our case, the hose was supposed to be in 50-foot sections. The 2½-inch hose was indeed in 50-foot sections. All others were various lengths. The good news is that the shortest section was measured out at 48 feet so that the tests were not affected.
Nozzle Pressures.
The flow tests revealed that most streams had at least a minimum interior attack flow for a room or small square footage-type fire (note that I said “minimum”); however, almost half lacked sufficient reach and velocity to be very effective. A 30-psi nozzle pressure was considered to be the minimum to create a minimum workable stream. The cutoff point for the 30 psi nozzle pressure averaged around the 60- to 70-psi standpipe pressure. Keep in mind that pressures under 30 psi are not recommended but could possibly work if needed as a last resort. Just remember, safety comes first.
A common denominator in all of these tests was the fact that most of the tips that allowed higher flows also took higher standpipe pressures to create the minimum 30-psi nozzle pressures. The one exception to this rule was the large bore tip nozzle used with the 2½-inch line. Its 30-psi nozzle pressure started at 40-psi standpipe pressure.
1.88-inch and 2-inch Hose. The tests showed that the 2-inch hose was slightly higher in flow than the 1.88-inch hose. Again, the minimum 30-psi nozzle and base pressures seem to kick in around the 60 to 70 psi standpipe pressure range, and the flows at that range started at about 150 gpm, maxing out at 300 gpm at the top standpipe pressure of 150 psi.
2½-Inch Hose. In the event of a low system pressure or large-volume fire scenario that would require large flows to extinguish, there needs to be a hose evolution to deliver the required stream. The flow tests showed the capabilities of a 2½-inch handline using 800 hose 150-foot-long hose in the low pressure range, 30 to 100 psi, as well as the higher 100 to 150 range that you expect to see in newer systems and systems properly pumped by fire department apparatus. The following nozzle combinations were used:
- 2½-inch nozzle with a 1 3/8-inch waterway in conjunction with 1 1/8-inch and 1¼-inch smooth bore tips and the large bore tip nozzle
- 2½-inch nozzle with a 2-inch waterway used in conjunction with 1 3/8-inch and 1½-inch smooth bore tips
You should not be surprised to see the flows increase significantly with the 2½-inch for obvious reasons. This is the reason it is a very popular size for high-rise application. Again, because of the size of the hose, the higher nozzle pressures developed on average of around 20 psi sooner than the smaller-diameter hose. But remember, the trade-off is heavier hose.
The first flow tests used the discharge of an engine to simulate a standpipe outlet and have been done in many of the classes that teach high-rise handlines. These tests are as close to realistic as it gets when demonstrating what a specific standpipe pressure can deliver without actually using a high-rise system itself. However, one key point to remember is that in the above tests, we cannot measure the actual residual pressure left over in the building system after flowing the tested flow from a handline. The 65 psi used in the engine test is basically a given pressure. It’s not an example of residual system pressure.
Example: Let’s use the pre-1993/65-psi residual pressure for this example. Remember, the 65-psi number is based on a 500-gpm flow. In the flow tests conducted from an engine discharge, you can measure the flow at the 65-psi pressure and come up with an accurate reading, such as the 2½-inch flowing 265 fpm. Take the same 2½-inch handline and connect it to a standpipe on a 65-psi residual pressure system, and you will find that you can get more water/pressure. The reason, again, is that the system is designed for 65 psi at 500 gpm. The pump has one only speed or power potential, which is set for the 500 gpm/65 psi flow. Therefore, if you flow less than 500 gpm, which you would have with the 2½-inch handline, the residual pressure will be higher because the pump will not adjust to the lower flow. This increase can possibly go up by 30 psi or more. This is reality.
The following flow tests show what the adjusted standpipe residual pressures and corresponding flows can be if the maximum 500-gpm flow is not being delivered. These tests were also done using an engine, the three sizes of hose used in the previous tests, and smooth bore tips. All streams had adequate performance capable of suppressing fire. Using an engine company instead of a building system was considered to be accurate enough to prove the theory.
(6) An engine company simulating a standpipe system.
The worst-case scenario was the 65 psi/500 gpm system using the 1.88-inch hose. The numbers speak for themselves. A 183-gpm flow with a 92-psi residual pressure was enough to develop a workable fire suppressing stream with plenty left over. Now, look at the 100 psi/500 gpm stats. The 218-gpm flow from the 1.88-inch hose was almost up to the expected minimum 2½-inch flow of 265 gpm, which is what standpipe specifications were originally designed for way back when. The stats on the 125-psi/500-gpm chart are based on Clark County, Nevada, (Las Vegas) fire protection system codes. Clark County is the authority having jurisdiction (AHJ) and understands the need to provide firefighters with the ammunition they need to get the job done. Remember, the AHJ can be you!
To verify these engine company flow tests, the same tests were done on a 65 psi/500 gpm building system.
Although not right on the money, the engine company tests were close enough to illustrate the residual pressure potential that a high-rise system has to flow water. In fact ,even though the flows with the engine test were adequate, the actual flows from the building system tests were better in that more water and pressure were actually available.
Final Thoughts and Recommendations
An important point to remember is that many building fire protection systems have the ability to allow fire department pumping apparatus to increase the system pressures and flows, sometimes significantly. What does this mean? Yes, the low-end pressure range flows in the tests were marginal at best, but a properly run fire department pump operation into a building system can, in a lot of situations, bring the bottom end numbers up to the 100-psi range, if not more. The best-suited hose and nozzle combination for the highrise pack is also equally important. To neglect either one of these components could reduce the efficiency of the operation significantly. They both work together. I say bring both up and decide. If nothing else, the small-diameter hose pack can be used for overhaul.
When deciding which handline to use in a high-rise fire, consider the following:
If the fire is that of a large magnitude and/or the building system is either known to have low pressures or found to have low pressures on fire department evaluation (or if it was unable to be determined), the 2 1/2-inch handline should be deployed. I think it’s important to bring up small and large hose packs and make the decision based on the situation at hand. If the system pressures and the fire problem will allow, make it easy on the troops by using the small handline. If instead the system pressures are too low, the fire problem is big, or if you are just not sure of either, use the 2 1/2-inch line.
To help determine the correct hose size to be used, a pressure/flow test can be done at the standpipe outlet using an inline gauge at the point of the hose connection and the line of choice. Next, simply open the standpipe valve and take a pressure reading. This should give a ballpark indication on the standpipe residual pressure of the building system and the pressure requirements of the handline itself. This in turn can help determine the size of the attack line.
I encourage fire departments to do similar tests. Our tests were done with specific makes of hose and nozzles. Your tests should involve any equipment that you feel should be evaluated. A good resource for all fire departments to use is the local fire protection system contractor. They have a good understanding of the systems and codes. Often times they can clear up misunderstandings that we may have that could affect the performance of our operations.
Paul Shapiro is director of Fire Flow Technology. He is a nationally recognized instructor on large-flow water delivery. He is also a retired engineer from the City of Las Vegas (NV) Fire Department. He has authored numerous articles for fire trade magazines. He has been in the fire service since 1981 and is author of Layin‘ the Big Lines and produced the first in a series of videos on large-flow water delivery. He is available to answer questions; he can be reached at (702) 293-5150 or Layinline @aol.com.