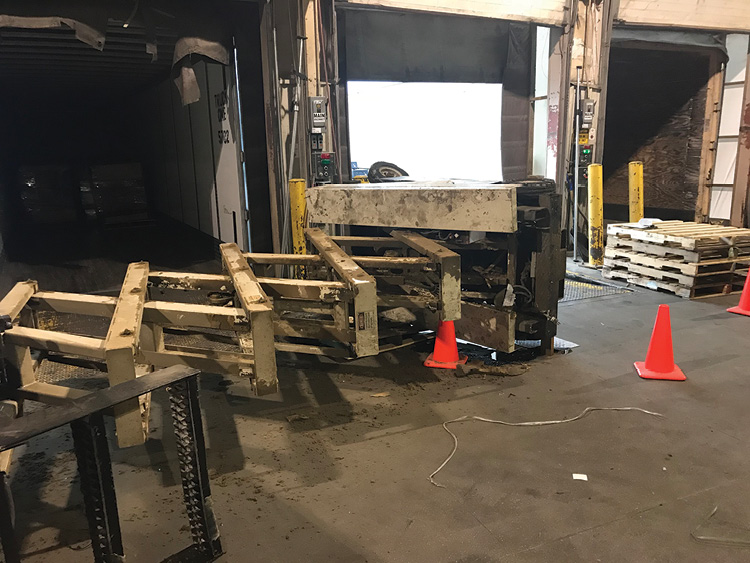
BY DENNIS RUBIN
Late one recent afternoon, Petersburg (VA) Fire Department (PFD) Engine 3, Fire Medic 3 (a transport ambulance), and Battalion 1 were “knocked out” for an interesting rescue call. The initial dispatch informed us of two employees trapped underneath a scissor lift that had fallen over. The description piqued my interest, and since I was the shift’s duty chief officer, I joined this rescue response. The incident facility was a large paper mill; the call for help was reported to be coming from the truck loading dock area. Within a few minutes, Engine 3 had arrived, was starting the size-up, and assumed “Wells Road Command.”

(1) Photo by the Petersburg (VA) Fire Department.
The engine company officer reported that two victims had fallen between 15 and 20 feet when their fully extended scissor lift device tipped over on its side. Medic 1 was assigned patient care, with support from Engine 3. Both patients had moderate injuries and would be treated as level 1 trauma cases, based on the mechanism of injury. At this point, the initial incident commander (IC) requested a second medic unit response. Southside Medic 1 (another transport ambulance) was soon underway and would be assigned to transport the least injured person. There were enough medically trained members on location to start patient care on both of the injured workers without delay.
MORE DENNIS RUBIN
Chemical Fires: The Hazards Follow You
What Is the Best Promotional System?
Caught on Film: the St. Norbert Fire
On arrival, the acting battalion chief (BC) requested an updated Conditions, Actions, Needs (CAN) radio report. After the initial command officer updated the BC, command was transferred; Battalion 1 was now Wells Road Command. On my arrival, I checked in with command and was assigned as safety officer. Since this incident was a rescue operation, I donned my turnout gear and headed into the operations area; a 360° view of the building was not needed. The impacted area was the fallen scissor lift and the floor space around the toppled machine. A few issues caught my incident safety officer’s eye (photo 1). Making sure that we had removed the victims to a safe location and that they were receiving high-quality emergency medical care was our first incident priority (life safety, incident stabilization, and property conservation, in that order).
The Incident
Fortunately, the plant’s safety manager was on location and provided some of the details that led up to this event. The injured plant crew was busy making repairs to a broken overhead door. Earlier in the day, the large overhead door had failed to operate properly and a few adjustments were needed to be able to receive the next shipment of goods. The workers diligently went about their efforts to fix the broken door, but they took a serious shortcut to save a little time. That shortcut, saving a few minutes, would almost take two lives that evening, cause two significant injuries, damage an expensive piece of equipment, and disrupt business for hours.
The two rear wheels of the scissor lift were placed atop an adjustable steel loading dock platform. This six- × eight-foot, ¾-inch-thick steel plate adjusts to match the dock height to the floor of the trailer being loaded or unloaded. The electrical power to the leveling plate was not locked out. When the steel leveling platform plate elevated (the plant safety officer was not sure why it moved), the scissor lift flipped over like a child’s toy (photos 2-3). That had to be one wild ride when the device crashed to the ground. Fortunately, the workers’ injuries were minor—a few bumps, bruises, and broken bones.
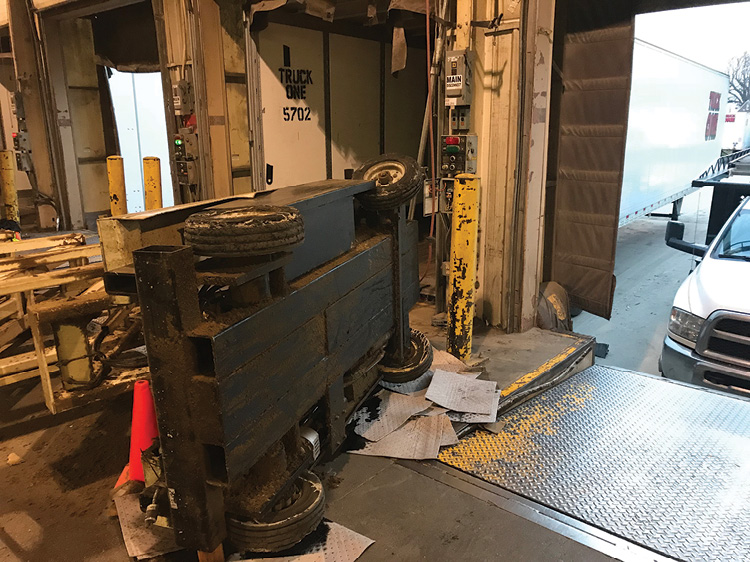

(2-3) Photos by author.
The Scissor Lift
A hydraulic lift system extends and retracts the 4,024-pound (two-ton) scissor lift to its maximum height of 20 feet; the human load in the work basket is not to exceed that of two people. The hydraulic oil reservoir tank holds 3.75 gallons of hydraulic fluid. An electric motor powered by four six-volt batteries propels this machine. The batteries are stored in the base of the device, where most of its weight is concentrated. Because of the concentration of weight, the scissor lift has no outriggers to stabilize it when the basket is extended.
The Operation
Once both patients were receiving proper medical care and the correct level of resources (a second medic unit) was ordered and en route, incident stabilization was the next priority. The fallen device needed to be rendered safe. The electric system that raised and lowered the device and moved the lift into location was disconnected by turning off the ignition and removing the operating key. Disconnecting the lead acid battery system was discussed; however, the access compartment door to the batteries on the side of the lift that was lying on the plant’s floor was inaccessible. This action would be impossible with the resources on location. The risk of disconnecting the batteries far outweighed the benefit.
The hydraulic oil posed a triple threat. The reddish fluid is potentially combustible, a corrosive, and a significant slipping hazard. Although the hydraulic oil reservoir contained less than four gallons, it seemed like much more spread out over the loading dock area. We used a five-gallon pail of absorbent to contain the spilled liquid. The captured hydraulic oil was left for the plant personnel to dispose of properly.
We could not determine whether the scissor lift operating system was still under pressure and we could not bleed off trapped oil pressure. Based on the inability to determine this, we kept a distance from all hydraulic oil system hoses and valves.
With both patients properly treated, packaged, and underway to the hospital for definitive medical care, command declared this incident under control. We moved into demobilization. Since two employees had received injuries, the Virginia Occupational Safety and Health Office in Richmond was notified; that office said it would take responsibility for formally investigating what happened and how to prevent similar accidents in the future.
Finally, we had to take up all of the used emergency medical materials and terminate command. This operation was a success since the patients were effectively cared for and we reached all benchmarks in a timely fashion. No members were injured and the plant would work with the Virginia Occupational Safety and Health Office to prevent future similar incidents.
Lock Out/Tag Out Standard
Lessons Learned and Reinforced
Size-up. The initial incident commander completed a quick and effective size-up at this incident. Typically, this includes a 360° view of the incident. Once the initial size-up is completed and the need for additional assistance is determined, request the correct level of resources. This incident required a second medic unit because two people were injured and the mechanism of their injuries. Call additional resources early and often if needed.
Lock out/tag out. Always “lock out and tag out” when an incident involves devices that contain stored energy such as high-voltage power sources or that perform hazardous operations (air pressure) to protect the operating firefighters and the victims. These devices uncontrolled can injure firefighters and victims quickly and without warning. All firefighters should read, understand, and heed the lessons of this case study. Had plant personnel locked out and tagged out the loading dock leveling device, the incident would not have happened. See the sidebar “Lock Out/Tag Out Standard.”
The big picture. Consider the big picture at every alarm. It would have been easy to disregard many of the hazards associated with the scissor lift. Once the patients were safely removed and receiving emergency medical treatment, the focus was incident stabilization. For example, the dripping hydraulic oil and battery acid containment are important, but they could easily have been overlooked.
Clean up operation area. One of the last steps of properly managing an incident is to clean up the entire operational area before terminating it and turning the property back over to the building occupants. This includes checking all of your tools and appliances and gathering any medical waste. If you provide great patient care but leave bloody gauze behind, all your department’s good work will be negated. A Washington, DC, junior news reporter tried to make a living off reporting that medical gloves were left behind at emergency medical calls. Don’t give the media any reason to discredit your operations or embarrass the department.
Overhaul. Ensure that overhaul is completed at all events. Overhaul means ensuring that the fire is completely out and the building/facility is stable—the roof or chimney will not fall down and injure someone once the department has turned the building back to the occupants. In this case study, there was no fire. However, a compromised, complicated machine had capsized. We secured it before our departure by bleeding off the trapped hydraulic pressure and disconnecting the battery.
Notify necessary agencies before terminating. Finally, ensure that you make all necessary notifications before terminating the incident. Some agencies (e.g., Virginia Occupational Safety and Health) require specific incident details that you can easily provide while at the scene but that are more difficult to provide once the fire department has cleared the scene.
DENNIS RUBIN, a 35-plus-year veteran of the fire service, is a principal partner in the fire protection consulting firm D. L. Rubin & Associates, which provides training, course development, and independent review of policy and procedures for all types of fire-rescue agencies.