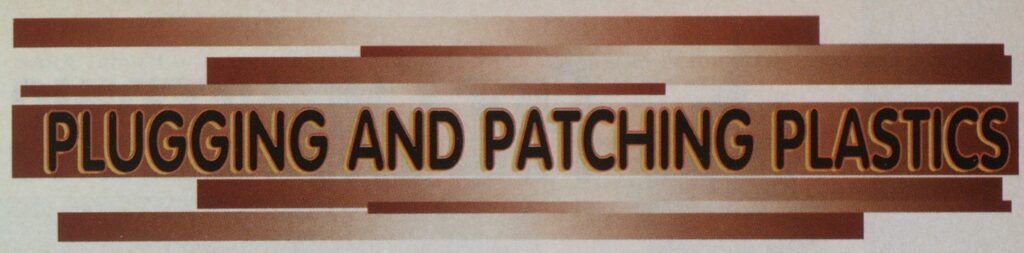
PLUGGING AND PATCHING PLASTICS

Plastics, once considered cheap substitutes for natural materials, today are regarded as designer materials that can do many jobs better than natural materials. Plastics have found their way into many areas, providing a host of opportunities for the designer and potential challenges for the firefighter or hazardous-materials team.
Firefighters are likely to encounter plastics in piping, fuel tanks, vessels, pumps, and a variety of containers such as jars, bottles, 30-gallon carboys, 55-gallon drums, 70-gallon overpacks, and large Department of Transportation-approved shipping containers.
Some types of plastics typically used in containers include polyethylene, polypropylene, polyvinyl chloride (PVC), and polystyrene. Acrylonitrile-butadiene-stvrene (ABS) and PVC commonly are found in piping systems. Nylon and Teflon® are other plastics in common use. These polymers may differ in chain lengths, may be mixed with other polymers, or may be reinforced with other materials and further modified with oils, extenders, and colorants. All of these variables make it possible to produce plastics with properties that will meet diverse particular needs.
TYPES OF PLASTICS
For the purpose of this article, however, plastics will be classified simply as rigid, thin-walled flexible, and thick-walled flexible.
Rigid. These plastics are nonflexible and usually hard. An example of rigid plastics is that used in piping.
Thin-walled flexible. This type of plastic is used for squeeze bottles.
Thick-walled flexible. These flexible, rubbery materials are used for containers that require strength, such as 55-gallon plastic drums.
METAL VS. PLASTIC
Most firefighters and haz-mat teams have had some practice plugging and patching metal drums and piping, but they have not had any experience repairing plastic containers. This could be a problem, since plastics and metals behave differently when they are torn. Consequently, the methods for repairing these classes of material must vary as well.
Following are some general techniques for plugging and patching plastics that Monsanto’s Indian Orchard Haz-Mat Team has tested on 55-gallon drums, 30-gallon carboys, and pound and gallon chemical containers. We filled the containers with water and created different types of holes and methods for repairing them.
How do the three classes of plasticcompare with metal when subjected to mechanical damage? Striking a metal drum with the point of a pickhead axe will create a square hole, and the torn metal will project into the drum. The drum itself will have a dent around the hole.
If you were to subject rigid plastic to the same treatment, it might become scratched, but no significant damage would occur. If a press were used to try to force a hole, the entire piece probably would fracture or crack.



(Photos by author.)
Striking a thin-walled flexible material with the axe would create a hole and tearing and would cause some of the plastic to project into the container. Some dimpling of the plastic also would occur, but there would be very little, if any, sign of failure (in the form of a hole). With enough impacts, a hole, without any dimpling around it, could be created, and the plastic around the hole would line the hole in a tapered shape and project into the container.
The differences in the ways the materials failed, the degrees of the failures, and the shapes of the holes can be attributed to the mechanical, physical, and structural differences of the materials. In general, metal and rigid plastic are strong, while flexible plastics are tough. Rigid plastics and metals can take a lot of force before they fail, but failure may be catastrophic. Flexible plastics will fail with less force, but they will absorb some of the force so that the thickwalled containers will have a smaller hole when they do fail.
PLUGGING
The methods for plugging (filling a hole with a substance to stop a leak) most commonly used by haz-mat teams include the following:
Wood wedges. The wedges are common, easy to make, and easy to use on metal (with a bit of practice). The wedges will tear thin-walled plastics when driven into place, and they work poorly with rigid plastics, as they seal by forcing the wedge against the tear wall. Since rigid plastic doesn’t give, wedges don’t work well unless they are close to an exact fit. This rules out using wood wedges for irregular tears in rigid plastics, but they can work for circular holes. We found that placing duct tape on the hole edges and then driving a wedge into the hole to take up the slack worked effectively. Duct tape worked better than felt, cloth, oakum, or metal wools, but duct tape also is attacked by many organic solvents.
Wood wedges work better with thick-walled flexible plastics but not as well as on metals. Rectangular wedges don’t work well because of fitting and tearing problems. Combinations of wedges don’t work for the same reason. Conical wedges, which are slender, seem to work best, since they seat against the material forced inside the container when the hole occurred. The golf “T” shape works well with small holes. A wood wedge on the market made with external threads works very well, as the threads hold throughout the tear surface and the plastic tends to seal back into the wood threads, sealing the hole.
Metal wedges. This category includes boiler plugs and self-tapping sheet metal screws. (Caution: Don’t use with materials that will react rapidly with the metals being used. This includes many acids, oxidizers, and other reactive materials. Check the material safety data sheets or check with CHEMTREC.) They don’t work for rigid or thin-walled flexible plastics, but they work very well for circular holes in thick-walled flexible plastics. As the metal threads cut into the plastic, the plastic seals or expands into the grooves between the threads. (Hint: It may be easier to take a halligan bar and drive the spike portion into an out-of-round hole to make it round.)
Heat welding. Because of the low melting point of many plastics, welding them with heat is more of a flowing together than the traditional metal welding. It also involves very different equipment than traditional metal welding and requires the services of an expert. The plastic edges should be very close and heat-soaked for about 30 seconds. The plastic then is brought up to 500°F. (Caution: This process should not be considered unless the materials in question are know n to be stable at these temperatures and don’t produce vapors that would endanger the lives of repair personnel.)
Gasket sealers. Materials used to form gaskets work well as plugs for small holes in all types of plastics. The type we used is found in most auto supply stores.
PATCHING
The following techniques for patching (the placing of something over or on top of the hole to seal it) were tested:
Toggle bolt compression patches. This group of patches involves fitting a toggle bolt’s wings through the hole and using compression material on the outside of the hole. Tightening the bolt against the wings forces the compression material against the hole and expands some of the materials in the hole. Compression materials can include corks with washers, rubber balls with washers, and a compression plate with gasket backing. The compression plate should have a curvature similar to that of the surface to which it is applied. This method works on thick-walled flexible plastics and can work on rigid plastics if the hole is large enough for the bolt wings to enter the hole.
Gasket patches. These are soft flexible materials that must be compatible with the contents of the drum or piping. They should be thick enough to be partially forced into the hole, and a back plate should be used for even compression. Force can be applied with banding, hose clamps, air bags and straps, inner tubes, or some types of tape. This method works best for rigid and thick-walled flexible plastics. Thin-walled plastics have too little strength for this technique.
Glued patches. The patch also can be glued, but the adhesive must be compatible and must make an airtight joint with the two separate materials. Because of the diversity of plastic types, every adhesive will not work with all plastics. Generally, a commercially available solvent (plastic cement) created for the specific ty pe of plastic involved makes a good glue. It is available where plastic fabrication products are sold. Building supply stores have the type for use with ABS and PVC pipe. Epoxy adhesives work well in many cases. Rubber glues, urethane glues, contact cement, and white glue all work in some applications. While this technique can be used for all plastics, the responder might not have the right adhesive available. When there is any doubt about whether an adhesive will work with a specific type of plastic, a sample of the glue should be tested on another section of the plastic container so that the hole does not become gooey, which could happen if the wrong adhesive is used.


Epoxy putties. These putty sticks contain two chemicals, each a different color, that react together to form the epoxy cement. A lump of putty is removed from the stick and worked until the color is uniform, an indication that it is properly mixed. We have found that it is best to wait until the epoxy lump starts to stiffen before jamming it into the crack, which should be as dry as possible. This approach works well for most types of plastic, provided there is no pressure in back of the repair. If there is pressure, the epoxy patch should be backed up with a compression plate held against the break by banding or a tire tube.
Fiberglass. We really arc talking about a fiberglass patch impregnated with polymerizing resin, such as the materials commonly used on a car body. Very strong and appropriate for use on most plastics, these materials can be built up in layers to form a new surface. They should be used to support patching materials on large holes There is even a fiberglass-resin package that need only be immersed in water to activate the resin.
SAFETY CONSIDERATIONS
When plugging or patching plastic containers, the standard techniques for initially stopping or reducing the leak should be used—if possible and if safe. They include shutting the valves in pipelines to seal the leaking sections and reorienting leaking containers so that the crack or tear is on the top.
Personnel must wear proper protective clothing, including gloves and eye protection, to protect themselves from the leaking material. Some of the plugging and patching materials (such as epoxies and glues) mentioned generate toxic or flammable vapors and are somewhat irritating as well. You must make sure, therefore, that ventilation is adequate and that open flames in the area are extinguished. In addition, you should read and follow manufacturers’ directions.
The tactics described in this article are offensive in nature, and only specific members of haz-mat teams and fire departments are trained to use the offensive methods outlined here safely and effectively. These techniques should be worked into department SOPs.