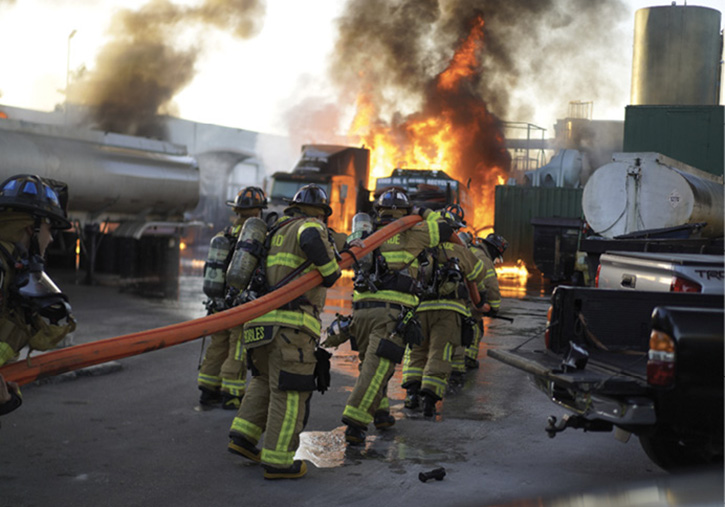
Waste oil facilities are businesses that store, process, and transfer large amounts of used and contaminated automotive lubricants, fuels, and coolants for recycling into useful products. The products they process will have multiple uses that range from heavy oils used to lubricate engines and machinery to lighter fuels like alcohols used for fragrances and sterilization purposes.
The facilities that store these products are in towns and cities across the United States. Many are in rural areas in plain sight of the public; others are hidden in more densely populated areas. Facilities such as fuel transferring stations, used oil recycling plants, and many other commercial businesses all hide the potential hazards of these materials.
Although the overall safety record of these businesses is remarkable, accidents do happen, and when they do, you must prepare for a long, drawn-out fight that could easily overwhelm your capabilities.
Response
Miami-Dade (FL) Fire Rescue (MDFR) units recently responded to a fire at such a facility—an oil recycling plant that converts used oil to biodiesel. The facility has been around since the early 1980s and, according to those who worked there, had an impeccable safety record that was something to be proud of.
The cause of the fire is still under investigation, but one possibility is that it may have started during a transferring operation of contaminated water and fuel to one of the vertical holding tanks. As the tank was filled with contaminated water, the layer of gasoline, being the lighter of the two, rose to the top, allowing vapors to exit through the vent pipes at the top of the tank. Gasoline vapors, being heavier than air, sunk to the ground and found a potential ignition source. The more likely cause is that an engine fire could have started the chain reaction that led to the ignition of surrounding fuels in the yard or may have played a role in the ignition source for the fire. This, however, has not been confirmed.

(1) Anywhere, USA, commercial fuel distributing depot. (Photos courtesy of author unless otherwise noted.)

(2) Facility diagram with fire and surrounding attack lanes. North/A side: Offices/parking. East/B side: Wall to adjacent property, two-foot gap between buildings. South/C side: Wall to adjacent property 15 feet high. West/D side: Adjacent warehouse building. Center: Fuel tanker parking lot/transfer station with fuel storage area. North side/center and directly behind offices: Parking spaces for fuel tankers. East side/center against wall: Batch containers consisting of 50- to 55-gallon drums and 5- to 330-gallon totes (containers constructed of a high-density polyethylene tank enclosed by a metal cage). South side/center: Vertical storage tanks 10,000 gallons each (6). West side/center: Horizontal storage tank 7,000-gallon transfer station.
As workers tried to extinguish the rapidly developing fire, the call to the 911 dispatch center was significantly delayed. Two MDFR hazmat staff units (H04, H05) that initially identified the dark column of smoke above several warehouses were the first to arrive and assume command, making the initial contact with dispatch. The fire was a fully engulfed tractor truck located in the rear of the property that was still attached to its trailer tank and was sitting adjacent to two other fully loaded tankers.
At the front of the property, the only structure contained the offices, which included a small kitchen and a breakroom area. To the west of the offices was a short road that led to the fuel yard where the fire had started.
RELATED FIREFIGHTER TRAINING
Developing Preplanning Standard Operating Procedures
Preventing Foam Operation Failures, Part 1 | Part 2
BLEVE: Facts, Risk Factors, and Fallacies
As units arrived and began staging, command was transferred to Battalion Chief 11 (B11), who had the first-due engine company connect to the hydrant conveniently located in front of the property. From there, crews quickly deployed 150 feet of three-inch supply line attached to a portable master stream device on the A side and began extinguishment of the tractor/cabin compartment. Ten minutes into the operations, the tank trailer ruptured, losing all its contents: 9,000 gallons of used oil quickly ignited, spreading fire throughout the yard and exposing more containers on the east and south sides of the property. Soon after, a second tanker located to the left of the ignition source also ruptured, creating an immediate inferno on the B/C corner. Within a few minutes of this occurring, several 55-gallon drums on the east side began to BLEVE.
With this new development, crews were ordered to back out and await the arrival of an airport foam apparatus. Twenty minutes after the first tanker failed, the third tanker truck ruptured, sending flames 30 feet into the air. This effect caused a major concern with the vertical tanks located in the C/D corner. Two aerial pieces already positioned at the C side began protecting exposures by directing their streams on these vertical tanks.
On arrival of the foam apparatus, the initial attack line was repositioned to the neighboring property on the west side, from where it assisted in cooling the horizontal tank. A second line was positioned to the B side in between the offices and the neighboring building to cool the remaining 55-gallon drums and keep them from exploding. Once all units were in position and the property was completely surrounded, foam operations began.
Positions and Tasks
A side: MDFR foam apparatus (Foam 4) positioned to attack the main body of fire.
B side: MDFR Engine Company 17 (E17) positioned a 2½-inch attack line to protect the B exposures by cooling the 55-gallon drums and to maintain safe conditions for the Foam 4 crew.
C side: MDFR Ladder Companies 29 and 26 (L29, L26) positioned to protect the C exposures and cool the six vertical tanks.
D side: MDFR Engine Company 48 (E48) deployed a three-inch exposure line to protect the D exposures and assist with cooling the horizontal tank.

(3) On arrival, Foam 4 was directed to lay foam on the main body of fire. (Photo by Ricardo Stephens.)
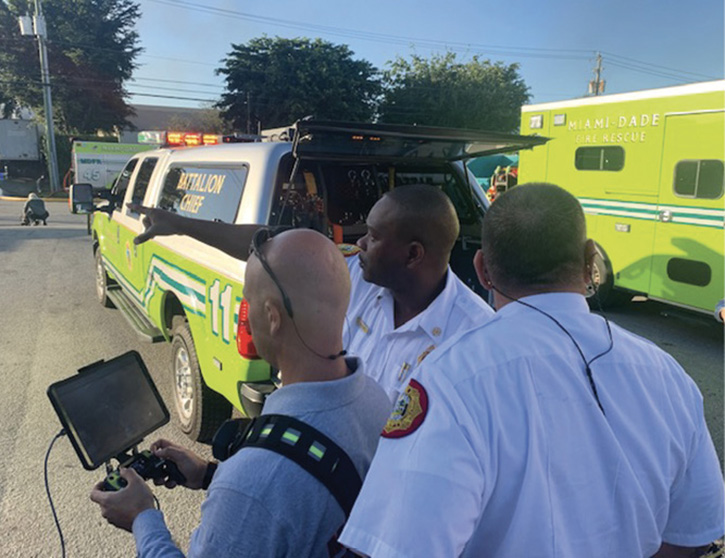
(4) Conducting drone operations to provide the IC with up-to-date information on fire conditions.

(5) MC 406 tanker truck #1.
Resources
Fires are rapidly developing events that can progress to an uncontrollable situation if fire dynamics and potential consequences are not understood at an early stage. Understanding what resources will be needed before they are needed is an attribute of an experienced and a proactive incident commander (IC). Keeping a few steps ahead of the fire and knowing what resources to use to match possible consequences are key components of fireground management and play a huge role in devising strategy. Resources—both personnel and equipment—are required to bring the response to a final positive outcome and are based on information gathered throughout the event.
Hazmat group. Establishing a hazmat group can assist in determining the amount, type, and location of the products involved by looking at preincident plans, Department of Transportation and National Fire Protection Association placards, material safety data sheets, and TIER 2 (hazardous material inventory) reports. A hazmat group was integrated into the response early to determine the types of fuels threatened and involved and their location to better assist the IC in directing fire streams to the areas most needed. The team also used meters to monitor lower explosive limits (LELs) after foam application was completed to determine vapor suppression and foam effectiveness.
Foam apparatus. Foam apparatus are one of the greatest resources you have when dealing with a spill of a large amount of hydrocarbons. The amount of foam on wheels available at a moment’s notice is unequivocal. Before the first tanker’s catastrophic failure occurred, the IC requested two foam apparatus from Miami International Airport (MIA). The first-arriving foam apparatus with a smaller foam tank capacity (200 gallons) and water (1,500 gallons) was put to work immediately on the A side. To conserve foam while awaiting the arrival of a larger apparatus, the driver reduced the percentage of foam concentrate from 6% to 3% and used the roll-on method to cover the fuel.
Drone unit. The implementation of drones as an observation platform during emergencies is a rather new concept. Advances in technology have reduced drone size and increased capabilities, making drones an invaluable resource. Before the arrival of drones in the fire service, an IC had to rely on information reported by companies from their limited perspective, depending on where they were operating on the fireground. This forces the IC to make decisions and direct actions based on incomplete information. Reports from companies, as we know, can be sporadic and difficult to read because the person providing the information is occupied with fire extinguishment.
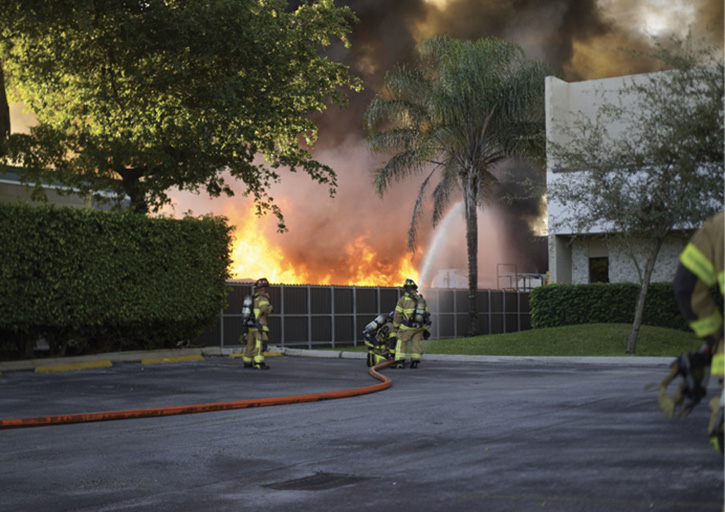
(6) E48 repositioned a three-inch exposure line directed on the horizontal tank. (Photo by Ricardo Stephens.)
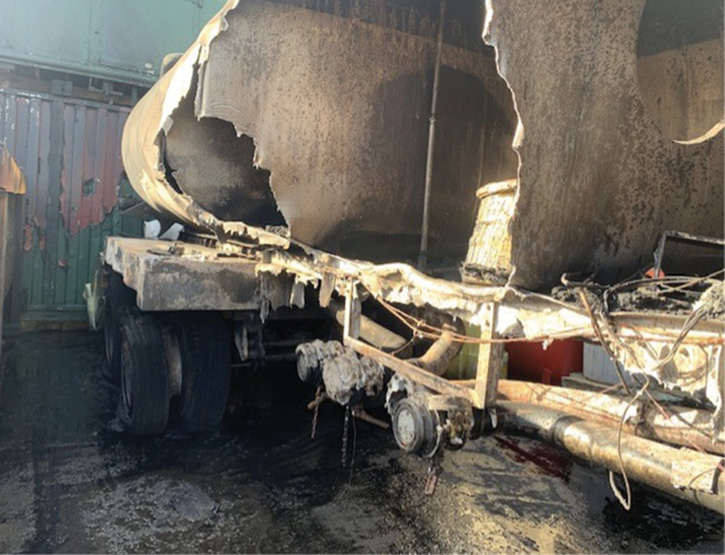
(7) MC 406 tanker truck #2. (Photo by Ricardo Stephens.)
With the arrival of drones on the scene, the IC can now observe actions taking place on the fireground as they occur and better direct his crews as they engage in tactical assignments. For this response, the drone unit provided thermal and high-resolution images directly to the IC so that he could position crews, direct water streams, and observe task outcomes.
Challenges/Lessons Learned
A four-sided attack completely surrounding the fire using five fire companies at various locations requires precise coordination and good resource management. Because it would have been very difficult to provide all five companies with an extensive amount of foam, it was decided that the attack line positioned on the A side would engage the main body of fire using foam. All other surrounding companies would provide exposure protection. As with any large firefight, this incident provided some challenges and lessons learned.
The urge to fight hydrocarbon fires without sufficient foam. In our profession, we are taught to move with a sense of urgency, to solve problems as quickly as possible so that they keep from escalating into bigger problems. For the most part, this is a good practice to follow but can lead to habitual performance in the wrong settings. This is the case when fighting fuel fires that require large amounts of foam. Foam concentrate must be on or very close to the scene before extinguishment efforts begin. Applying a foam without sufficient concentrate readily available can result in wasting concentrate if the spill fire reignites and burns off the foam blanket. The initial attack line put in place was used to combat the tractor/cabin fire using a portable master stream. When the tank ruptured, spilling its contents, the operation had to transition to a foam evolution. Rigging an inline foam eductor and gathering buckets of foam concentrate took several minutes, allowing the fire to spread before extinguishment could resume.
The amount of foam concentrate available to each fire company is typically three- to five-gallon buckets of alcohol-resistant aqueous film forming foam (AR-AFFF), proportioned at 3% for hydrocarbons and 6% foam for polar solvents such as ethanol. Here, 150 gallons of foam were marshaled to initiate extinguishment while awaiting the arrival of the airport foam apparatus.
Breaking down the foam blanket when protecting exposures. Exposure protection breaks the chain of potential fuel available to the fire. Applying water to exposures that are adjacent to the main body of hydrocarbon-fed fires can, however, dilute the foam blanket and increase the amount of foam required to control a fire and maintain a vapor-suppressing blanket. Disciplined crews understand the effects of their water streams on a recently placed layer of foam and resist the urge to apply water to exposures indiscriminantly. Once exposed metal surfaces no longer develop steam when water is applied, they are most likely sufficiently cooled, and cooling streams should be redirected or shut down.
Foam application. Calculate the amount of foam concentrate on scene taking into account the amount of potential fuel available for combustion, the surface area of the spill, the flow rate in gallons per minute (gpm), the percentage of foam concentrate (ratio of concentrate and water) to be used to suppress vapors, and a 15-minute cool-down period once fire knockdown has been achieved. In this case, three tankers filled with contaminated oil provided for approximately 27,000 gallons of fuel in an area of roughly 480 square feet (ft²). The application ratio provided by the first attack line was 3% at 0.10 gpm/ft².
Runaway/runoff. One important consideration when fighting three-dimensional fires is that for the foam to have an effect on the fuel, the fuel has to be somewhat stagnant. Moving fuel can easily run away from the foam blanket meant to smother it, allowing fumes to once again escape and reignite. Block fuel advancement by placing barriers (diking) in areas free of other fuels. Charged five-inch supply lines can assist in this matter.
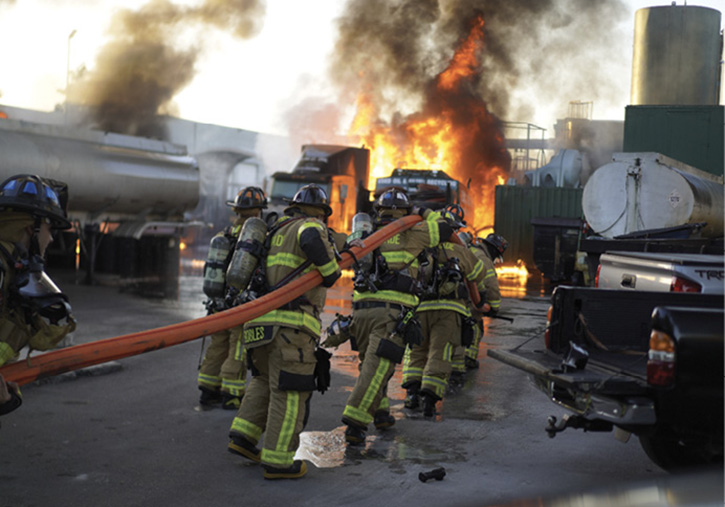
(8) Advancing the recently charged three-inch foam line into the attack position.
Crews were not immediately aware that a storm drain located in the yard was affecting the foam lay. Once identified, it was covered so it would keep from taking in more fuel and robbing valuable foam already laid. A hazmat crew under the guidance of the hazmat branch covered the drain and metered all drains in the area for combustible vapors.
Preplanning essential. Waste oil facilities are a necessity for all communities that depend on hydrocarbons to conduct their daily business for transportation, industrial, or energy needs. It is paramount to understand their potential hazards and know how these hazards may affect the surrounding areas. Territory familiarization and prefire planning of these facilities will assist you in developing incident action plans that you can put into place when needed.
Labor-intensive. The response described above took three alarms and close to four hours to extinguish using the following assets: six engines, one ladder, three platforms (tower ladders), six advanced life support medic rescues, five battalion chiefs, one division chief, two airport foam units, three hazmat units, and many others in support. From the time the first company arrived until the time the fire was completely extinguished, four operational divisions were created to manage each side of the yard. Given all the challenges that arise with this type of incident, fire crews performed as a well-organized team through proper communication and coordination. When not engaging, the fire companies were rotated through a rehab station for required work/rest cycles.
Alvaro Toñanez is a lieutenant and a 24-year veteran of Miami-Dade (FL) Fire Rescue, where he is the training officer for the hazardous materials team. He provides monthly training for more than 300 hazmat technicians and also assists in the development of hazmat/CBRNE procedures for Miami Dade County.