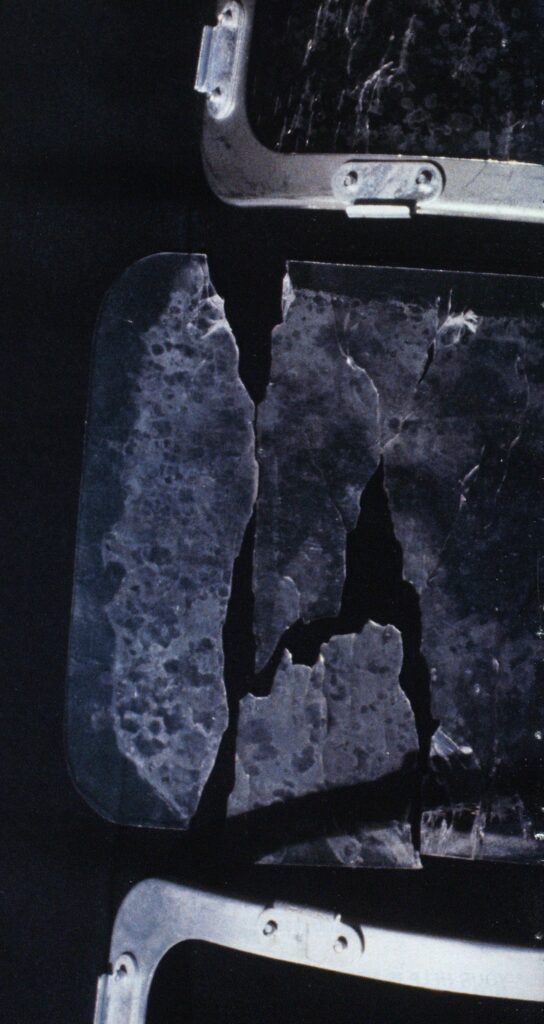


Making Sure Protective Clothing Protects
FEATURES
PROTECTIVE CLOTHING
That’s the task standards-writing bodies have undertaken for chemical protective suits.
Four years ago, firefighters approached a railroad tank car in Benicia, Calif., wearing chemical protective suits to shield them from leaking dimethylamine vapors. They came away with suits that bore cracked or shattered facepieces and failed seams, wearing fire boots on which the heels had become unglued from the soles.
In the course of investigating that incident, the National Transportation Safety Board found such problems with chemical protective suits were common, and it encouraged the National Fire Protection Association to develop standards in cooperation with ASTM (formerly the American Society for Testing and Materials). At the board’s urging, several federal entities—including the U.S. Coast Guard—also became involved in working with both of the private, voluntary organizations.
Right now, no comprehensive standards specifying garment and material performance requirements exist. It’s difficult to compare products because manufacturers report test data and suit features differently—even though the information may be obtained through the same standard test method. Once comprehensive standards are developed, users will be able to examine a garment for compliance labels to find out whether it meets minimum ASTM or NFPA requirements.
The two standards-writing bodies are taking distinctly different, yet compatible, approaches. Each is pursuing a different one of three categories of standards. (Neither is looking toward design standards, which specify to manufacturers the exact way in which a product must be constructed. Design standards are generally avoided because they don’t allow manufacturers latitude for innovative designs.)
ASTM’s approach has been to use documentation standards, which direct manufacturers and testing laboratories to perform specific tests and to report certain data from those tests to users. Documentation standards may also require manufacturers to provide product information such as a complete description of the materials used in fabricating a garment.
Several ASTM standards specifying methods for measuring the properties of materials or the performance of complete suits already exist or are near completion. Moreover, standards from other ASTM panels, such as the Dll Committee on Rubber, can be applied to protective clothing materials. Thus ASTM’s present direction is one of providing measurement techniques that will standardize product testing and documentation.
In contrast, the NFPA is working mostly on performance standards, which provide a minimum performance level against which to compare an actual property or characteristic of a product. For example, the garment material in a chemical protective suit might have to possess a tear resistance of at least a certain value. The Subcommittee on Hazardous Chemical Protective Clothing under the NFPA’s Technical Committee on Protective Equipment for Firefighters is developing standards of this type. The recommendations in this article reflect the subcommittee’s current direction, unless otherwise attributed to ASTM or some other source.

(Photo by Gerald L. Grey)
Developing realistic standards of either the documentation or performance type entails making choices about what characteristics to test, how to test, and how extensively to test. These considerations are apparent in the chemical protective suit standards ASTM and the NFPA are coming up with, which fall into four general areas: chemical resistance, physical properties, component functioning, and overall suit quality.
Chemical resistance
Because of the diversity of chemicals in use, chemical resistance has been one of the most difficult areas in which to write standards. But the ASTM F23 Committee on Protective Clothing has made significant advances in establishing standard methods for measuring the permeation (ASTM Standard F739), penetration (ASTM Standard F903), and degradation (Draft ASTM Standard F23.30.03) resistances of chemical protective clothing. These phenomena relate to the different types of chemical interactions with the protective material.
Test types. Although there are three chemical interactions to test, one of them—degradation—can be observed during the other two, permeation and penetration resistance. Degradation refers simply to visible changes, such as discoloration, that the material undergoes when it comes in contact with a chemical.
Permeation resistance testing is the most complex of the three ASTM chemical resistance methods. Because this criterion is more rigorous than judging penetration, it’s a likely requirement for vaporprotective clothing, which should prevent any intrusion by the hazardous chemical—whether liquid or gas. This method, described in ASTM Standard F739, makes use of a device that places the chemical on one side of a sample of the material and a sophisticated detector on the other.
The parameters measured in permeation resistance testing— breakthrough time and permeation rate—are subject to variations produced by the environment, equipment, material, and testing chemical. As a consequence, results from the test aren’t always easily compared between labs and can be difficult to relate to field conditions to which the entire suit is exposed.

(Photo by Hank A. Howard)
To eliminate some of these discrepancies, the NFPA might specify key test parameters and procedures and the configuration of test apparatus.
One important example is the minimum detection limit, or sensitivity, of the analytical device used to detect breakthrough time. On a new material, one device reported that the breakthrough time for carbon disulfide was eight hours, while a more sensitive detector yielded a breakthrough time of just 30 minutes. Testing labs can’t be expected to choose the same piece of equipment for each chemical. But if a sensitivity miminum were set for all permeation resistance testing, many of the disparities might be avoided.
ASTM Method F903 specifies the procedures for penetration resistance testing, measuring the resistance of suit materials to chemicals in liquid form. It’s important to distinguish this from permeation testing, because the qualifying test for liquid-protective clothing permits vapor permeation, and users should choose such clothing only if they’ve decided exposure to the chemical’s vapors poses no health hazard.
In the penetration test apparatus, the clothing material acts as a partition separating the hazardous liquid from the viewing side of the test cell. The test subjects the material to the liquid at a specified pressure of 2 psi; so the tester notes how long it takes for the liquid to visibly penetrate the material.
Selecting what to test. To fully evaluate a chemical protective suit’s chemical resistance, it would be necessary to test all suit materials against all the chemicals a response organization could possibly encounter. For the Coast Guard, this would amount to more than 1,100 priority chemicals listed in its Chemical Hazard Response Information System.
Some of these chemicals can be eliminated by taking into account their chemical state and toxicity. Still, it’s nearly impossible to test all material-and-chemical combinations. For a standard to be useful, some means of selecting priority chemicals must be adopted.

(Photo by Gerald L. Grey)
Both ASTM and the NFPA are devising standard chemical batteries for testing the chemical resistance of protective clothing materials. ASTM Standard F1001 specifies a standard list of 15 chemicals (see Table 1 on page 32) which represent a wide range of chemical classes and hazards. The NFPA is considering using the ASTM list, with the addition of ammonia and chlorine (as gases).
Specifying permeation or penetration tests on a minimum number of chemicals would allow comparison of different products’ general chemical resistance performance. However, each response organization must still determine how well its suits perform when they come in contact with the priority chemicals for its area.

(Photo by Hank A. Howard)
While it’s realistic to narrow the number of chemicals tested, realism in testing materials can be achieved only by examining them all. In the past, the practice has generally been to test a suit’s primary or garment material exclusively. But visors, gloves, boots, and garment seams are also likely to be contaminated during a hazardous-materials incident, as the dimethylamine spill in Benicia illustrates.
Thus recommendations for using chemical protective suits must be based on the chemical resistance of all major materials, with the weakest material being the limiting factor in suit-use recommendations. If a self-contained breathing apparatus is worn outside the suit or if air line hoses are employed, the external materials of these items should be subjected to the same type of tests as the suit materials.
The NFPA proposes to define the primary protective suit materials needing testing as the materials of the garment, visor, gloves, and boots. If the suit is constructed for wearing SCBA on the outside and the SCBA thus forms part of the seal, then the materials in the breathing apparatus protecting the critical air path must also be tested for chemical resistance.
Another selection—of the condition in which to test the material— is necessary to make chemical resistance tests reflect real-world conditions. To this point, all recommended testing has been proposed only for virgin materials. But users need to know how chemical resistance changes with wear.
One way to find out is to test the materials after some form of physical abuse. Early proposals recommended creasing materials, then subjecting the creased materials to the permeation or penetration tests. More recent ideas include the use of standard material-flexing devices that perform reproducible mechanical actions. A radical decrease in performance after flexing would indicate a high probability of material failure in the field.
Crude testing of this nature has already been performed for a number of materials brought into contact with methyl isocyanate. In one case, a sample of material demonstrated permeation resistance of eight hours when it was uncreased—but a mere 10 minutes after it was creased.
And finally, it’s necessary to select a test period that relates to field conditions. Without standards, each testing lab makes that decision, but usually the test time is related to how long the protective clothing is likely to be in use at one time.
For chemical protective suits, testing periods range from one to eight hours. However, many manufacturers base their recommendations for suit use on the criterion that the chemical in question won’t break through in one hour, reasoning that time limitations from SCBA and severe physiological demands keep use down to one hour. In fact, some researchers believe the one-hour limit includes a large safety factor because testing involves constant chemical contact for the full hour, which isn’t the case in the field.
Both ASTM and the NFPA are considering a minimum test period of three hours for documentation purposes, and the NFPA is proposing a performance requirement of one hour.
Proposed requirements. For chemical resistance documentation, manufacturers should perform either permeation or penetration testing, as appropriate for the type of suit, against a limited number of representative chemicals.
Standards must go on to specify how the tests are conducted. For example, the NFPA proposes to use ASTM F739 for measuring permeation resistance, with the added qualifications of a minimum detectable permeation rate of 0.1 microgram per square centimeter per hour and a three-hour test period for each material-and-chemical combination tested. These tests should be performed for the primary protective suit materials, including at least the garment, visor, glove, and boot materials.
Table 1.
Standard Chemicals for Evaluating Protective Clothing Material
(Recommended in ASTM F1001, “Standard Guide for Test Chemicals to Evaluate Protective Clothing Materials.”)
Table 2.
Battery of Physical Property Tests for Chemical Protective Suit Materials
(Recommended by A.D. Schwope, et al., in Guidelines for the Selection of Chemical Protective Clothing, 3rd ed., National Technical Information Service, U.S. Department of Commerce [Vol. 1, order #ADA179516, Vol. 2, order #ADA179164]—as modified in NFPA proposals)


The main purpose of such a documentation requirement is to allow users to compare products with the same information. This would also let users infer a chemical protective suit’s ability to resist mixtures and unidentified materials.
Chemical resistance performance requirements should be chemical-specific, but the standards won’t say which chemicals suits should be tested against. If standards are to support the quality of products used in hazardousmaterials spill response, responding organizations will have to decide which chemicals they’re most likely to come in contact with and communicate those needs to the manufacturers.

What the NFPA committee wants the standards to provide is a performance requirement—such as no permeation breakthrough (for vapor-protective suits) or detectable penetration (for liquidprotective suits) in one hour— that’s generic to any type of chemical for which a manufacturer might decide to certify a suit. Like the documentation standard, the performance requirement must define the test method and parameters (such as the minimum detectable permeation rate). The end result will be a list of chemicals associated with each suit and based on standardized testing.
Physical properties
ASTM, NFPA, and federal standards are available for measuring physical properties of materials, but they’re not easy to relate to field hazards such as tears, cuts, punctures, and abrasion. Different materials are worked into the design of a suit because they have certain properties, such as light transmission characteristics chosen for suit visors. But most of the existing test standards involve testing particular material types (textiles, elastomers, plastics, and coated fabrics) rather than testing materials for specific applications. Thus tensile strength (resistance to breaking) is measured by noting the force required to pull the material apart, although this action may or may not have an equivalent phenomenon in the field.
So new standards must describe physical property tests that simulate actual wearing conditons. Both ASTM and the NFPA are working on this.
Test types. Both organizations have classified physical properties in two main categories of material strength and durability. One recommended battery of tests for these properties is provided in Table 2, which appears on page 32.

(Photo by Hank A. Howard)
Material strength may be examined by testing materials for bursting strength and for hydrostatic resistance. These same integrity tests should be applied to suit seams and closures, which should demonstrate at least the same performance as the garment material.
Material durability might be evaluated by measuring resistance to ultraviolet light, ozone, and heat degradation.
Other properties, such as stiffness, can be measured under varying temperatures to determine lowand high-temperature performance. Flame resistance is another property of concern to users.
Selecting a lest method. ASTM and the NFPA are trying to pick a single test for each physical property that will be valid for all the different materials used in chemical protective suits. This would encourage testing standardization and allow users to compare characteristics of similar products.
But it’s not an easy assignment. The methods chosen will have to not only allow testing of different material types (such as plastic films and coated fabrics), but also differentiate the qualities of each material.
For example, some protective clothing materials are known to become stiff and brittle in cold temperatures. Yet the application of a cold-temperature bend test (ASTM Standard D2136) shows these materials passing at —13° F. In this case, the method doesn’t support the observed phenomena and isn’t sensitive to deterioration in cold weather performance. However, two other methods (ASTM Standard D1043 and FED STD 191A, Method 5202) show significant cold-temperature differences and can be related to field experience. The NFPA will probably adopt one of these more sensitive methods as a reference.
Component function
As mentioned already, a suit is only as good as its weakest material—which may be some component other than the actual garment material. The other components— closures, fittings, accessories, exhaust valves, and gaskets—must be tested both for chemical resistance and their own functioning.
Suit seams can be tested for both permeation and penetration using the standard methods. However, special gaskets must be used with the permeation test cell to prevent leakage along the nonuniform profile of the suit seam. And suitably sized specimens and test cells must be fabricated to perform penetration testing on the suit closure. This testing should be repeated after the closure has been operated several times, because wear can change the closure’s performance characteristics.
Suit gasket materials may be tested as sheet materials, and should be tested at least for degradation resistance and preferably for permeation resistance.
The NFPA is considering requiring documentation of these components against representative chemicals. A possible performance requirement is that suit seams should possess chemical resistance at least equal to that of the primary garment material.
The exhaust valves used in most vapor-protective suits to allow venting of exhaust air from SCBA worn inside the suit are usually made of materials with relatively poor chemical resistance. In addition, the valves’ performance characteristics are uncertain, because little testing has been done in that area.
On totally encapsulating suits, manufacturers employ valves with cracking pressures—pressures at which the valves begin to open— ranging from 0.1 to 3 inches water gauge pressure to maintain a small positive pressure inside the suit. This is meant to prevent the diffusion of hazardous vapors into the suit through poor seams and closures or through worn material. But in the absence of testing, we don’t know whether different types of valves are truly one-way, preventing negative pressures in the suits and the backflow of chemical through the valves, nor do we know how different operating pressures may affect this performance.
Many manufacturers add splash covers for both exhaust valves and closures. These are either flaps of material or inverted pockects which protect sensitive suit components from direct impingement of liquid splashes. This is one area where design requirements may be justified, because splash covers are difficult to test by traditional means.
Overall suit quality
Only a few types of tests exist for evaluating the complete protective garment, and some variations of the tests are more quantitative than others. One type—the garment pressure test—is a recently adopted ASTM procedure (ASTM Standard F1052). Methods for other forms of garment testing, such as for leaks and for manned functionality, are under development.
The methods described here apply only to vapor-protective clothing. There are no standard tests yet for evaluating the integrity of complete liquid-protective suits. Possible tests for liquid-protective clothing include using chambers outfitted with nozzles to spray liquid (water) against a suit ensemble dressed on a mannequin. Penetration for such clothing might be measured by using moisture sensors in the mannequin itself or by adding a dye to the liquid to stain special garments placed on the mannequin underneath the suit.
In garment pressure testing, the most widely used method, the tester inflates the suit (see figure on page 34) to measure the gas-tightness of it and the visor material, suit seams, and suit closure. Either the pressure drop is measured over time or a soap solution is applied to the outside of the suit so any leaks will create soap bubbles. The suit exhaust valves must be closed or plugged to perform the test, and a provision must be made for attaching a pressure gauge.
Some manufacturers specify the pressure to which the suit should be inflated, while ASTM Standard FI 052 specifies a maximum inflation pressure (3 inches water gauge pressure), a test pressure (2 inches water), and an allowable pressure drop (20 percent) over 3 minutes. It also requires using the soap solution to locate leaks if the suit doesn’t meet these pass/fail criteria.
Results regarding a garment’s design, comfort, and fit are generally subjective. They can be made more objective by measuring the wearer’s core temperature, skin temperature, heart rate, and blood pressure.
The ASTM method seems to be sensitive to even small leaks, catching suits that might pass the following leak test.
Leak testing measures the suit’s integrity against a gaseous or aerosal challenge agent in a manner simulating actual use. A test subject wears the suit and an SCBA in a closed chamber so the gas concentration can be measured in the chamber and inside the suit. Those concentrations can be ratioed to calculate an “intrusion coefficient”; large coefficients indicate high integrity. This is similar to the widely used practice for assessing breathing devices during fit tests.
During these tests, suit pressure can also be monitored to determine if relative pressures become negative and allow penetration of the challenge agent.
Manned functionality testing is often performed to determine the range of activities a user can do while wearing the chemical protective suit and an SCBA. These may include different exercises or tasks that simulate the end application of the suit.
Results regarding the garment’s design, comfort, and fit are generally subjective. They can be made more objective by measuring and comparing the wearer’s physiological condition (such as core temperature, skin temperature, heart rate, and blood pressure) before and during the test.
However, because the tests are essentially subjective and not reproducible, they’re not appropriate for manufacturing performance standards. They’re ideal, though, for user acceptance testing and for evaluations comparing products.
In fact, the purpose of all the standards is to aid the user in choosing products that will provide the greatest safety in handling haz-mat incidents. The ASTM documentation standard will allow a user to compare the same information from product to product. The NFPA performance standards will provide users with some confidence that a product “passes” specific tests to provide a minimum level of performance.
Collectively, the standards should provide incentives to manufacturers to improve their products and allow a framework within the marketplace to encourage competition.