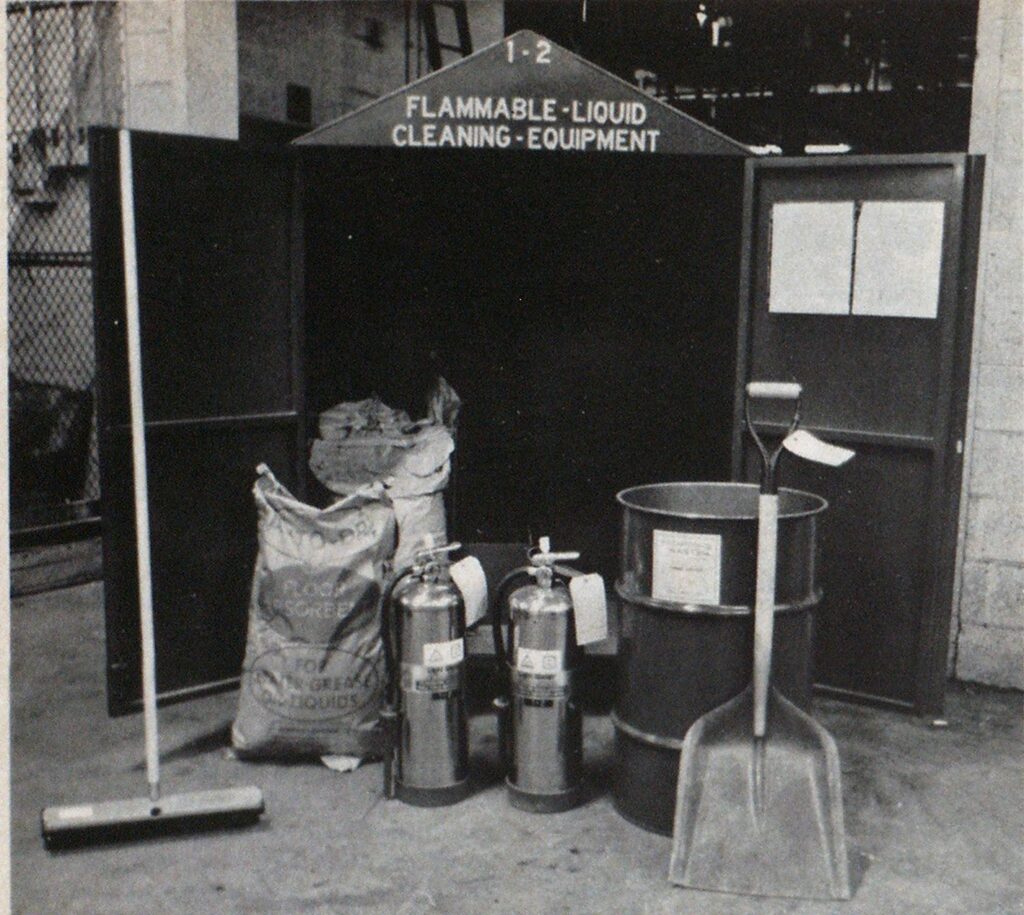
Industrial Flammable Liquid Spills Handled with Mobile Cleanup Kit
features


In most industrial settings where flammable liquids are used extensively, spills are a continual threat. In response to several large spill incidents, the fire protection and safety departments of Steelcase, Inc., of Grand Rapids, Mich., devised a spill cleanup kit which provides our employees with a safer method of controlling flammable liquid spills.
Preliminary research indicated the need for a portable self-contained unit which would be easy to use by any employee, readily accessible, mobile and easy to service.
Agents tested
A primary concern was that the selected agent suppress the flammable liquid vapors and allow safer handling of the liquid during cleanup. The agent was determined through preliminary testing of two solutions, the Light Water brand of aqueous film-forming foam (AFFF) and No Flash, a flammable liquid foam agent used bv a local fire department. The test involved flammable solvents such as naphtha and xylene. Each solvent was spilled in an isolated 100-square-foot area inside a manufacturing facility. Flammable vapors were measured using a MSA Model 2A Explosimeter. The Light Water AFFF was applied to the spilled solvent and flammable vapors were measured again. The same procedure was used to test the No Flash agent. Absorbent material was used to soak up the solvent-foam spill. Using a fiberglass shovel, it was placed in a 30-gallon barrel and transported outside. Then ignition of the soakup material was attempted using a road flare. Flammable liquid vapor measurements were taken prior to ignition.
The results of the test indicated that the flammable liquid vapors were suppressed to less than 25 percent of the lower explosive limit (LEL) for each solvent. These results were the same for each solvent and both types of foam agents. Ignition of the soaking materials was accomplished only after stirring the material to release sufficient vapors. Both agents worked equally well. However, the convenience, availability and the desired use in a portable extinguisher were the reasons why AFFF was selected for our purposes.
Cart designed
After the portable extinguisher unit was selected, the maintenance planning department designed a cart to contain the spill kit materials. The unit was fabricated on the complex and the materials were ordered through local suppliers. A total of fifteen units were built and distributed to our six manufacturing facilities’ paint mix, spray rooms and upholstery glue areas.
A copy of the operating and disposal procedure for flammable liquid spills is outlined and posted inside the cabinet on the door. The spill procedure consists of the following nine steps:
- Isolate the spill area by positioning personnel at entrances or traffic areas to prevent other personnel or equipment from entering the area with possible ignition sources.
- Position personnel with portable fire extinguishers in the vicinity of the spill.
- Determine the spill size relative to the capacity of the AFFF portable fire extinguisher. Generally one extinguisher will cover approximately 2 gallons of spilled solvent or 100 square feet.
- Form a dike around the spill using the clay soakup material. Personnel should not walk in the spilled flammable liquid while distributing the soakup material.
- Using the broom supplied in the spill kit, push the soakup material toward the center of the spill until it has been completely absorbed.
- Use the fiberglass shovel to put the contaminated material into the 30-gallon steel barrel lined with a plastic bag. The barrel should remain stationary unless it can be placed on a dolly for more mobility.
- Tie the bag closed with the tag provided. Indicate the originating department, department foreman’s name, type of material spilled and type of soakup material.
- Contact the maintenance department for disposal of the material.
- Contact the fire protection department so the spill kit can be serviced.
Turn page
Training
The fire protection department provided a training program for employees in areas where the kits were installed. Training sessions consisted of a stepby-step familiarization of the spill cleanup procedure posted on the inside of the cabinet door. Upon completion of the lecture, approximately 2 gallons of water was spilled to simulate a flammable liquid spill. The employees were instructed to clean it up according to the outlined procedure. The water spillage gave the employees a general relationship of how 2 gallons of flammable liquid would spread out on a floor area. A critique of improper actions was accomplished during the cleanup operation. The practice of cleaning up a spill gave the employees hands-on experience concerning the “do’s and don’ts” of the operation.
All employees were informed of the location of additional spill kit units. A list of the units in the plant is posted on the exterior of the door of the spill kit, in case another unit is required for a large spill.
Since the units were installed in late March 1981, many have been used for small flammable liquid spills. The employee response to the efforts to provide a safer method of handling flammable liquid spills has been outstanding. Hopefully, the training being provided will help to increase employee fire safety awareness and provide a safer working environment in all of our steelcase manufacturing facilities.