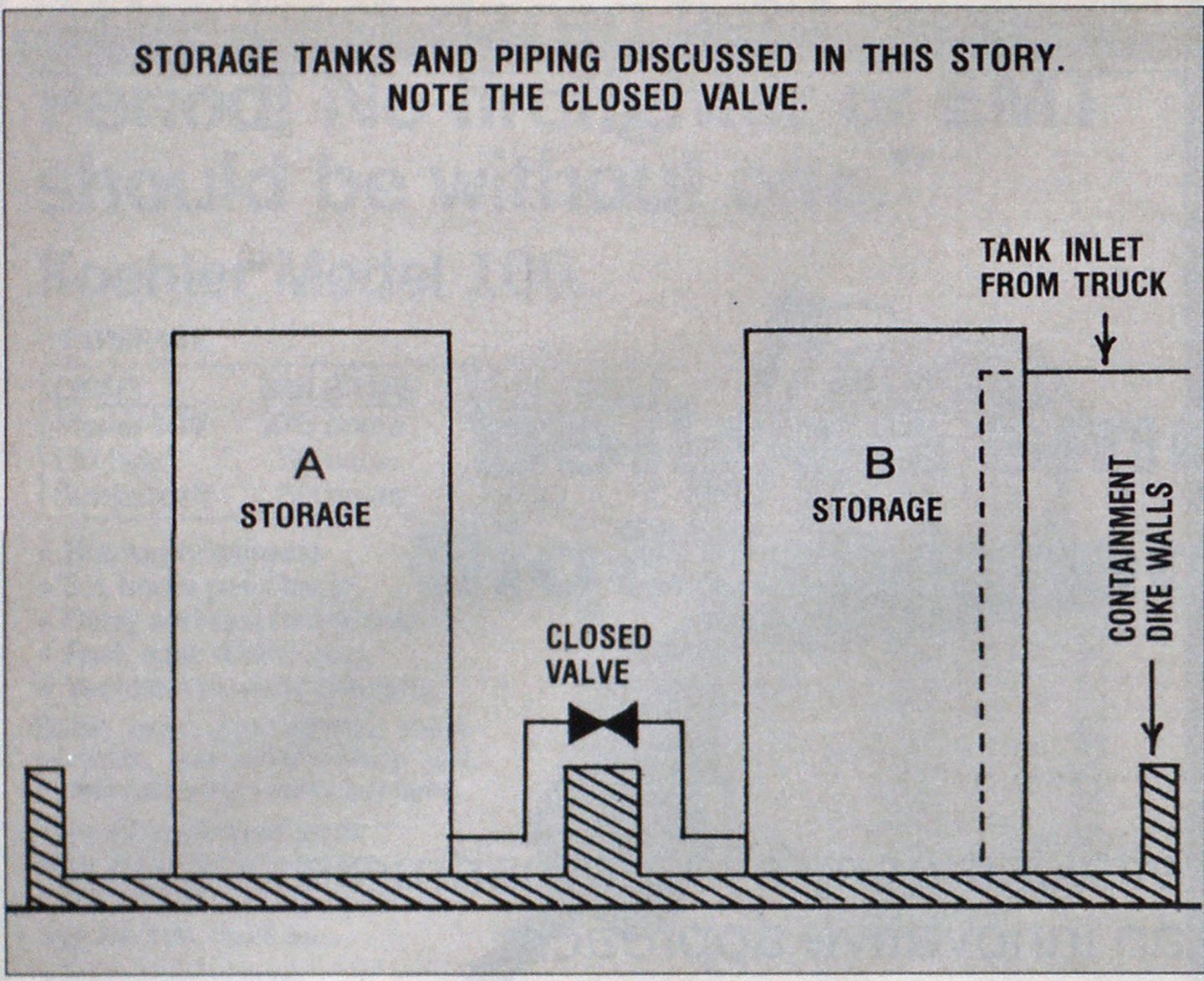
Foams Applied in Chemical Spill
FIREFIGHTING TECHNIQUES
A Massachusetts company’s fire department takes an innovative approach to the application of high-expansion foam.
On July 20, 1987, at about 9:45 a.m., the driver of a methanol tank truck began to offload to a methanol bulk storage tank at Monsanto Chemical Company’s facility in Indian Orchard, Massachusetts. The driver checked the tank’s level and started pumping from his truck to the tank. After about an hour, a maintenance man in the area noticed methanol leaking from the storage tank’s overhead piping. The driver shut down the filling operation and notified the manufacturing department’s supervisors of the methanol spill. The plant’s fire department and hazardous-materials team responded.
Methanol (also called wood alcohol, Columbian spirits, carbinol or methyl alcohol) is a hazardous material due to its toxicity and flammability. It is a colorless liquid with a characteristic pungent odor. The chemical formula for methanol is CH^OH. Short-term overexposure (due to swallowing or inhaling very high concentrations) may produce headache, weakness, drowsiness, nausea, vomiting, blurred vision, and death. The Occupational Health and Safety Administration and the National Institute for Occupational Safety and Health have established exposure limits of 200 parts per million for workers. 25,000 ppm is considered IDLH (immediately dangerous to life and health). Methanol is a highly volatile chemical, producing vapor with a density of 1.1 with respect to air (heavy enough to concentrate in the tank’s dike) and has a flash point of 52°F. (Air temperature at the time of spill was 95°F.) It also has a wide explosive range (6.7-36 percent), assuring that if an alcohol cloud were allowed to form and find an ignition source, there would be potential for explosion and fire.
Upon reaching the scene, the fire department immediately began to evacuate all nonemergency personnel to a predesignated area and reroute traffic away from the area. Initial size-up of the area showed that there were two storage tanks piped together and typically operated as one unit. On the day in question, maintenance work was being done on “A” storage tank, and it was isolated from “B” tank. Due to a breakdown in communication, the driver of the truck was not made aware that the tanks were individually isolated and that the audible warning devices were no longer part of the storage system. During the truck unloading, “B” tank filled up twice as quickly as it should have, not being able to equilibrate with “A” tank (see piping sketch, next page). This resulted in the overfilling of the tank, causing methanol to leak from piping gaskets and the conservation vent. Both tanks A and B had individual dikes (capable of holding more than the storage tank volumes) so that runoff and containment were not immediate problems.

With nonemergency personnel removed from the scene, the strategy for a successful resolution of the hazardous situation was initially split into two parts: first, suppress vapor formation in the dike, and secondly, simultaneously stop the methanol leak by reducing the amount of alcohol in B tank. The second task was delegated to the maintenance supervision. They worked with the manufacturing department’s foremen to determine the best pump-route and with the department’s operators to effect the pump-off.
The plant’s fire engine was located about 250 feet upwind from the storage tank, at a hydrant. We (the Monsanto company’s fire department) decided to reserve the engine for use in a flash fire and pull lines from it. This reduced the potential of bringing an ignition source to the vapor cloud, and it minimized the number of personnel exposed to the methanol.
Our preplan indicated that the best method of minimizing methanol vapors as well as the spill volume was to use foam. We kept quite a bit of 3%/6% alcohol-stabilized aqueous film-forming foam on hand, as well as some 1% alcohol-stabilized AFFF and high-expansion foam.
The 3%/6% alcohol-stabilized AFFF was indicated because:
- Polar solvents such as methanol effect a physical reduction in the surface tension of standard (that is, non-alcohol-stabilized) AFFF.
- Non-polar hydrocarbons (hexane, toluene, etc.) were present on the site; alcohol-stabilized foam can be used at 3% concentration on non-polar liquids.
- Polar flammables (alcohol, acetone, etc.) were also present on the site; alcohol-stabilized foam can be used at 6% concentration on polar liquids, methanol being just such a liquid.
A l 3/4-inch line with an aspirating nozzle and a matching eductor 100 feet in back of the nozzle was pulled from the engine. A second line was pulled as backup for the foam team. This allowed the deck gun on the truck to be used to cover both teams on the handlines, since the truck was not pumping foam. (Using the handline and eductor reserved the 400 gallons of foam concentrate the truck carried in its foam tank for firefighting.) A foam blanket about 3-5 inches deep—about 30-40 gallons of foam concentrate —was put into the dike. Vapor measurements of the foam in the dike, taken with detection tubes (using a long probe) indicated very low methanol vapor levels (less than 50 ppm).
After about 10 minutes, we noted that the foam had broken down to one-inch thickness in spots. We pumped some additional foam into the dike and checked the rate to ensure that we were at 6%. This was done by switching to the booster tank and running out a known amount of water with a known amount of foam.
The check confirmed that we were at the correct foam concentration—so why the reduction in the foam blanket? We believed that the hot, dry air was evaporating enough water to cause the foam to break. We started to pump out the alcohol storage tank, but estimated that it would require about 35 minutes more to drop the level sufficiently. We could continue to pump foam every ten minutes, but this could easily contribute 15002000 gallons of water and foam to the cleanup.
We decided instead to try to protect the AFFF foam blanket with a covering of a high-expansion foam. In this application, the dike walls would contain the high-expansion foam. If we were correct in our belief that hot, dry air was the problem, then the high-expansion foam would slowly break down by drying out, thereby protecting the AFFF by not letting it dry out. If we were incorrect, then once the AFFF foam blanket broke down, the high-expansion foam would quickly follow, since it is not alcohol-resistant.
Following the renewal of the AFFF foam blanket (5 pails of concentrate at 6%), we reset the eductor to 1% and switched to a highexpansion nozzle. The fire department was able to fill the dike to a level of four feet using about three gallons of high-expansion concentrate. Being much less dense than the AFFF foam, the high-expansion foam floated above the AFFF foam without crushing it.
About an hour later, enough methanol had been pumped out of the alcohol tank to stop all flows due to overfilling. The total foam depth at this time was 2 ½ to 3 feet. No fresh foam had been added during this period. This marked the end of the hazard incident period and the beginning of the cleanup/decontamination period.
We were unsure if the doublefoam use would complicate the cleanup. Forty bags (20 pounds each) of absorbent were used for the cleanup (the absorbent agent used was a finely crushed organic material). The bags were brought up to the dike, opened and poured over the edge of the dike. Testing of the dike’s vapor space indicated low vapor levels throughout the pickup period. The pickup was completed and all units were back in service by 1:00 p.m.
During both the foam blanket application and cleanup operations, positive-pressure self-contained breathing apparatus were worn by hose teams and cleanup teams. For chemicals such as methanol (which aren’t absorbed onto charcoal filter), wearing SCBA is the only recognized method of respiratory protection. Fire department members wore full turnouts. Individuals participating in the cleanup wore full-length turnout boots with polyvinyl chloride rain pants and jacket, and neoprene gloves in addition to the SCBA (level B protective equipment).
The techniques and strategy used here were standard, except for an important, new application: the combined use of two firefighting foams. Our role as firefighters is continually being broadened by emergency medical service and haz-mat incident response. We must become even more self-reliant and innovative to solve new problems with current equipment and new tactics. Hopefully, the action taken at Indian Orchard will encourage such positive growth.