On many fire departments, the first-arriving company officer (CO) is also the incident commander (IC) in those first few crucial minutes before the chief arrives and the CO’s company is operating alone. Those first minutes are very stressful for a CO in that position; he must make critical decisions and direct responding companies that can impact the overall outcome of the incident. When a first-arriving CO assumes command, he does so at a huge disadvantage. First, he will likely be forced to make decisions based on incomplete and what may be inaccurate information. Second, as IC, the CO has the same responsibilities as the highest-ranking chief on the department, but he seldom has the luxury of physically detaching himself from performing tactical operations with his company. A CO in this position can take some pressure off himself by staging companies as he conducts an initial size-up. The CO should not be pressured into prematurely committing his apparatus and other arriving companies before he gathers critical information such as a building location or lot number and how to reach it, especially if a complex has more than one entrance.
When arriving companies ask for an assignment, the CO should not be afraid to say, “I don’t know yet.” When arriving at an apartment complex, an industrial park, or a mobile home park, the first-arriving CO should order all arriving companies to stand by at entrances or a block away in the direction of travel. Do not allow police officers or civilians to conduct the size-up and be careful when they attempt to direct apparatus into the scene. The CO may need to order his company to stand by at an entrance while he proceeds on foot to determine where to position apparatus and other companies. This is critical when the first-arriving company is an engine that forward lays a supply line from a hydrant to the fire.
If apparatus are committed prematurely, they will have to back up to relocate and redeploy supply lines laid to the wrong location. Today’s fires, involving synthetic petrochemical-based materials and lightweight wood engineered structural members, intensify rapidly. Time is of the essence; first-arriving companies must get water on the fire as soon as possible if lives and property are to be saved; they cannot wait for a chief to arrive before taking action. Getting first water on a fire can, however, be delayed without a proper size-up.
Occupancy Is a Critical Factor
Professional engine companies, whether career or volunteer, do not operate the same at fires in commercial occupancies as they would at residences. A fast attack with a 1¾-inch hoseline supplied by a booster tank can be entirely appropriate and effective at fires in one- and two-family dwellings and at some apartments, hotels, and rooming houses. That same fast attack can be dangerously ineffective at a fire in a discount auto parts or a dollar store, especially after business hours. At commercial fires, such as big box stores and warehouses, firefighters are more likely to be at greater risk than occupants, who most likely have fled. Not that there is never any civilian life hazard in nonresidential occupancies, but search and rescue operations are conducted differently than for residential fires. The difference is that, unlike residential occupancies, occupants trapped in a commercial occupancy such as a restaurant or nightclub are awake and aware that there is a fire and are most likely unable to escape because exits are locked or blocked or crushed by panicky occupants against doors that open against the flow of exit travel. Search and rescue operations at nonresidential occupancies should focus on assigning firefighters equipped with rotary saws to force open steel side and rear doors.
Fires in closed commercial occupancies are likely to become fuel rich/ventilation limited and will most likely intensify when firefighters force entry, allowing air to flow into the building. Firefighters, however, can use a vent-limited fire to their advantage to buy them time to establish an adequate and redundant water supply and position 2½-inch hoselines and master stream devices.
Firefighters may delay a direct interior attack when a closed commercial building is protected by a sprinkler system, especially when there are indications that the sprinklers are having an effect on the fire—e.g., water running out from under overhead doors and white, steamy smoke. In this case, the most effective action to take is to ensure that the control valves accessible from the exterior, such as post indicator valves, are open and that the sprinklers are adequately supplied by pumping fire department connections (FDCs).
Do not assume that all sprinklered buildings have fire pumps or that there will never be a serious fire in a sprinklered building. Firefighters, in essence, bring a fire pump to the scene when they connect their apparatus to FDCs and pressurize the sprinkler system at 100 to 150 pounds per square inch (psi). Every year, fire destroys fully sprinklered buildings because sprinkler systems are impaired or inadequately supplied with water. A change in contents or storage rack configuration can result in fires that the sprinkler system was not designed to control. Additionally, a sprinklered building can become a total loss when firefighters neglect to adequately supply FDCs and then make matters worse by dropping pressure in the system when they flow hoselines to directly attack a fire.
In recent months, fire has destroyed a number of big-box retail and fulfillment center buildings, although they were believed to be “fully sprinklered.” One of these buildings had all or a portion of the sprinkler system out of service for a maintenance issue.
At another building, well-intentioned firefighters closed sprinkler system control valves to improve visibility. Clearly, sprinklers cool smoke, making it less buoyant; consequently, firefighters meet a dense cloud of white, steamy smoke that is being pushed to the floor and will not readily rise though vertical ventilation openings. Firefighters who close sprinkler control valves to improve visibility may not realize that sprinklers are often the determining factor of the outcome of the fire, whether the building and employees’ jobs are saved or the local economy suffers the loss of a vital business and jobs.
Water Supply Options and Considerations
Many departments that use large-diameter hose (LDH) rely entirely on hydrant residual pressure to supply pumping apparatus operating at the fire scene. Consequently, a combination of high-flow demand, which lowers residual pressure in water mains, and the friction loss in long hoselays can result in inadequate flow (photo 1). At extra-alarm fires, where

(1) A supply hose collapses at the pump intake because of low hydrant residual pressure. (Photos by Eric Goodman unless otherwise noted.)
Hydrants are designed to flow their maximum capacity with all their outlets flowing. Accordingly, engine companies should “double tap” or “triple tap” hydrants by connecting hydrant gate valves to 2½-inch outlets. This facilitates the subsequent connection of a second short supply soft suction hose without shutting down the hydrant (photo 2). If first-arriving engine companies choose to forward lay (from the hydrant to the fire) and rely on hydrant pressure, they should consider the use of a four-way hydrant valve, which will allow a later-arriving engine to position at the hydrant, take suction from the four-way valve, and boost the pressure in the supply hoseline without interrupting the flow of water (photo 3).
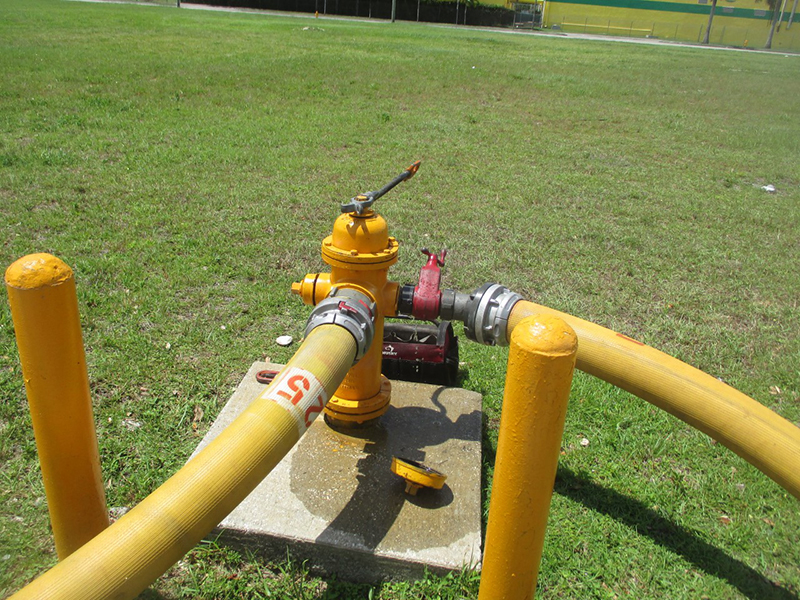
(2) A gate valve and 2½-inch female to five-inch Storz increaser are used to “double tap” a hydrant by connecting a second supply hose to the right-side steamer intake of the apparatus.
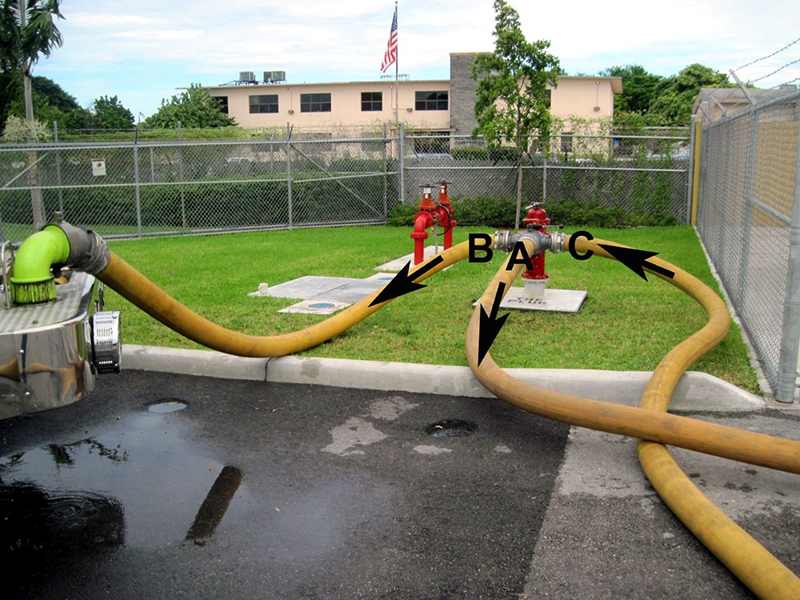
(3) The pressure in a supply line (A) is boosted by taking suction (B) and pumping into a four-way valve (C).
LDH has been touted as an “aboveground water main” that brings a hydrant to the fire scene, but it has its limitations. First, most LDH is relatively fragile as compared to conventional, smaller diameter hose. Consequently, if there are not enough police officers to keep civilian traffic from driving over LDH supply lines, engine companies should make every effort to avoid laying it across roadways (photo 4). A second limitation of LDH is that it can block roadways for subsequent-arriving companies. When LDH is laid on narrow roadways, engine companies should consider having members walk behind the apparatus to pull hose to the curb. Although a single LDH supply line may meet or exceed water flow demands, don’t rely on it as the only source of water, especially at nonresidential occupancy fires. Lay a second supply line in case one of them should fail.
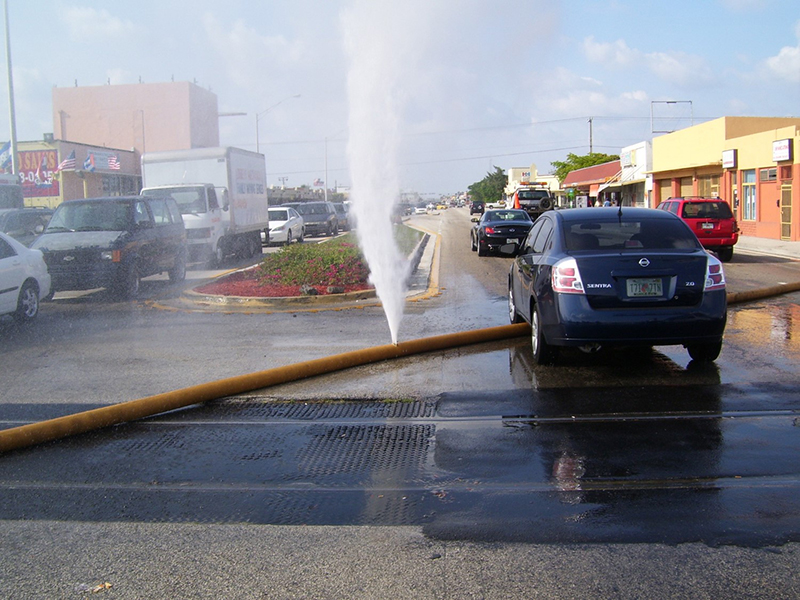
(4) A five-inch supply line fails because of traffic damage.
Ideally, fire departments should know the size of water mains and the hydrants are color-coded to indicate their gallons-per-minute (gpm) capacity. What if the hydrant capacities and water main diameters are unknown? This is when it is crucial to calculate the water available by comparing static and residual pressures. See the David Gates article “Calculating Available Water from a Hydrant”1 on calculating available water.
One department learned a hard lesson about a weak water supply at a working high-rise fire: The engine pressurizing the standpipe system FDC connected to the closest hydrant and read a 60-psi static on the pump’s master intake gauge. It wasn’t until companies were flowing water on the fire floor that the engine’s residual pressure dropped dangerously low. What happened? The standpipe systems for a complex of four 25-story waterfront high-rise residential buildings were supplied by a single six-inch-diameter “dead-end” main—that is, fed from just one direction. After what could have been a near miss for companies deprived of water, the department took decisive action: First, it conducted flow tests at high-rise condominium complexes to identify those that will require a two-engine relay from larger, higher capacity water mains. Second, driver engineers will no longer wait for companies to get up into the building and flow water to determine their residual pressure. Now, as soon as a hydrant connection is completed, the driver engineer will connect a 13⁄8-inch nozzle tip to a 21⁄2-inch discharge and charge it at 80 psi, flowing 500 gpm. If the pump operator notices a precipitous drop from static to residual pressure, command will be notified immediately.
Engine companies should evaluate the flow capabilities and limitations of pump intakes, especially front and 2½-inch auxiliary suctions. The capacity of front suctions depends largely on the diameter, length, and configuration of piping from the front bumper to the intake of the pump. Similarly, the capacity of 21⁄2-inch auxiliary intakes depends on the configuration of the pump. Modern, high-capacity midship pumps may have 21⁄2-inch auxiliary suctions with very little restriction. If 21⁄2-inch auxiliary suctions are found to restrict flow, consider connecting directly into the pump’s steamer connection (photo 5). Another water supply consideration is the diameter of the waterway in external ball-and-piston intake valves; some have relatively small-diameter waterways, which could reduce flow into the pump.
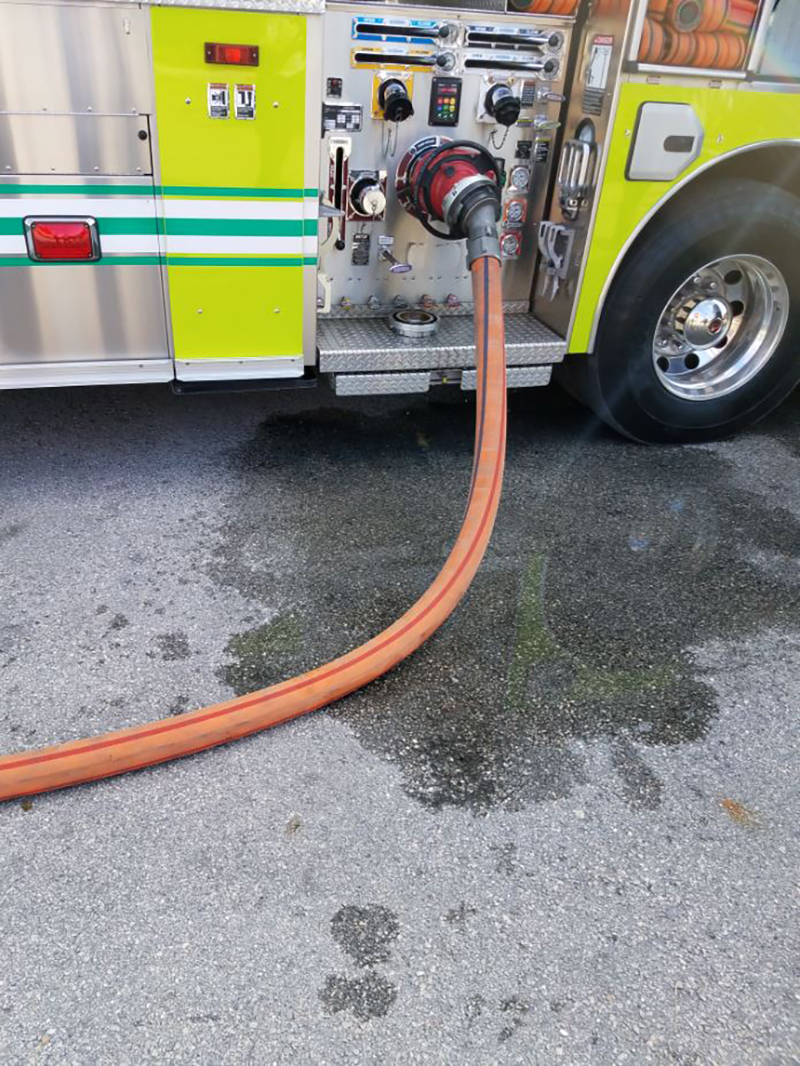
(5) A three-inch hose is connected to a steamer intake with the use of a 2½- to five-inch Storz increaser.
Fire Suppression vs. Conserving Tank Water
At very few residential fires is it justified to delay fire attack while establishing a continuous water supply. In rural areas, engines with 750- and 1,000-gallon booster tanks are the norm; in urban and suburban areas, engines tend to have 500-gallon booster tanks. Water from a 500-gallon booster tank can suppress a lot of fire, especially in residential buildings. Remember, the objective is to rapidly take energy from a fire, not to save water in the booster tank.
Every fire has a critical rate of flow required to absorb heat faster than it is generated. Apply water below the critical rate of flow and it will vaporize and be carried away in the thermal column until the fire has consumed sufficient fuel to reduce its size to within the hoseline’s suppression capability. This is what can happen when an engine company with a 1,000-gallon booster tank is more concerned with not running out of water than suppressing the fire.
For example, they limit their application rate to 160 gpm on a well-involved single-family home, a flow well below the needed fire flow. The result? The structure is destroyed, but firefighters can take comfort in knowing that they did not run out of tank water.
What if that same company was to apply their 1,000 gallons at a rate of 250 gpm for four minutes or 500 gpm for two minutes and overwhelm the fire? Might they empty their booster tank before the fire is under control and a continuous water supply is established? The answer is, “Yes, but running out of tank water is not the end of the world!” Fighting a structure fire is not like fighting a flammable liquid fire with foam. A structure fire is a Class A ordinary combustible fire. Unlike a Class B fire, it is not going to flash back to its original intensity if suppression is interrupted.
A large fire department in the Midwest has an evolution for discharging an engine’s 500-gallon booster tank through its deck gun before securing a source of water. Rapid application of a master stream, also known as a blitz attack, is very effective on well-involved 2½-story frame dwellings with highly combustible asphalt or vinyl siding. It is unlikely that a blitz attack will completely extinguish a fire, but it usually takes a lot of the energy out of it and slows its progression.
Preplanning Rural Water Supply
Orchestrating tanker shuttles is beyond the scope of this article; the focus here is limited to resources/methods for establishing a water supply in unhydranted areas (photo 6). A common rural water supply problem is when apparatus cannot get close enough to a static water source to draft. Some areas solve this problem by installing dry hydrants to facilitate drafting. Another solution is deploying a portable pump or a water jet eductor to take suction from swimming pools. A jet eductor does not actually displace atmospheric pressure the way a true drafting operation does; rather, it uses a venturi effect. In photo 7, the strainer screen has been removed to reveal how water, at approximately 200 gpm, pumped into the 2½-inch inlet changes direction; flows through a smaller orifice to increase its velocity; and discharges into the inlet, thus creating a venturi, which entrains as much as 670 gpm back to the suction of the engine (photos 8-10).
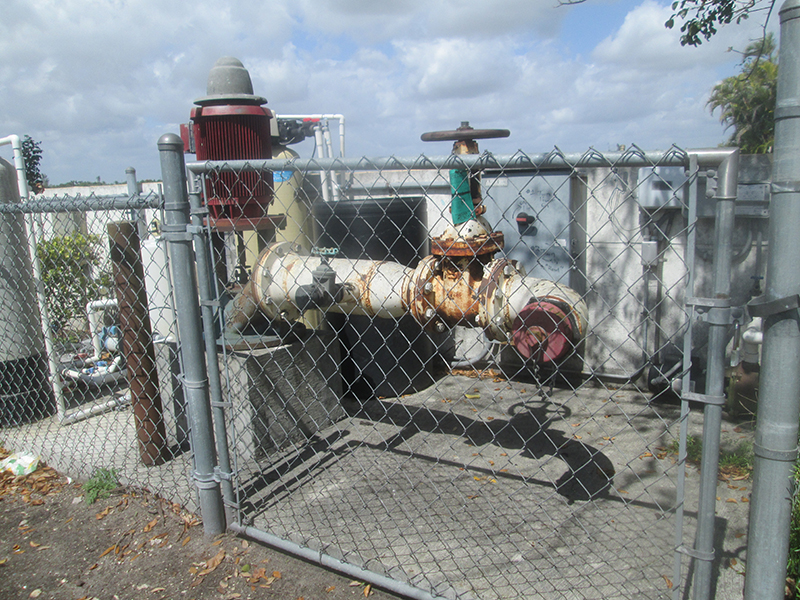
(6) A vertical turbine fire pump in poor condition, driven by an electric motor, supplies well water at a rural vegetable packing house. If electrical power is lost, an engine can connect hard suction hose to the pump’s discharge and draft through the pump from the well. (Photos 6-10 by Corey Logan.)

(7) The strainer screen of a jet eductor has been removed to reveal how water, at approximately 200 gpm, when pumped into the 2½-inch inlet changes direction; flows through a smaller orifice to increase its velocity; and discharges into the inlet, thus creating a venturi, which entrains as much as 670 gpm back to the suction of the engine.

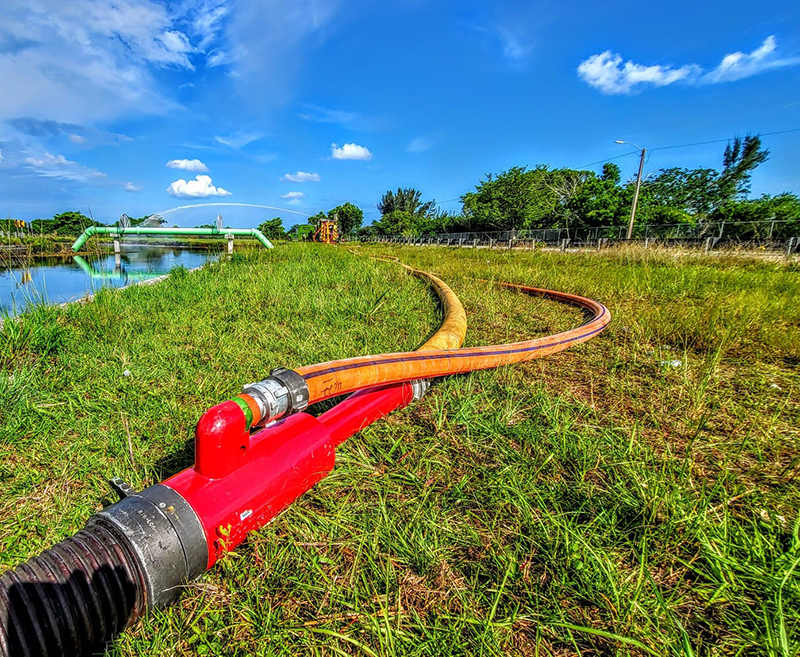

(8-10) An engine takes suction from a canal by pumping three-inch hose into a jet siphon that is connected to draft hose secured to the canal bank by a roof ladder.
Flow Testing to Determine Pump Discharge Pressures
The most accurate way for a fire department to determine pump discharge pressures (PDPs) is to conduct flow testing. This is a fairly easy process for departments that operate with smooth bore nozzles and “low-pressure” fog nozzles of equal gpm and nozzle pressure (NP). If this is the case, all that is needed is an accurate pitot gauge and in-line gauge if the apparatus discharge gauges are suspected of being inaccurate. Here is how the test would proceed: Say the objective of the flow test is to determine the proper PDP for 200-foot, 1¾-inch preconnect hoselines equipped with 15⁄16-inch smooth bore nozzles and the target flow is 185 gpm. Gradually increase the PDP of the preconnect until the pitot gauge registers a 50-psi nozzle pressure (photo 11). Now, note the PDP displayed on the pump discharge or in-line gauge; that will be the pressure for that particular length of preconnect. Additionally, that will be the same PDP if the nozzle has a spin-off smooth bore that can be replaced with a fog tip rated at 185 gpm at 50-psi nozzle pressure.

(11) A 50-psi pitot gauge pressure reading indicates the 15⁄16-inch nozzle is flowing 185 gpm.
For departments that operate exclusively with fog nozzles, a pitot gauge cannot measure their flow; they need a flowmeter, which is not cheap. Small departments with limited budgets may be able to borrow one from their state bureau of fire standards and training, a community college fire academy, or a neighboring department. To simplify testing using a flowmeter, connect it to a hoseline connected to a hydrant and an auxiliary intake (photo 12). If the apparatus pump and plumbing do not leak and the instrument is properly calibrated with a pitot gauge and a smooth bore nozzle, then flows can be read from any discharge; whatever flow is leaving the pump’s discharge side is the same flow registered as it enters the intake side. Again, if you doubt the apparatus discharge gauges’ accuracy, connect in-line gauges to discharges. Do not obsess about achieving exact and consistent flow test results. Test results will not be consistently exact unless you use the exact same hose, nozzle, pitot tube, and flowmeter every time. Additionally, a perfectly calibrated flowmeter could have a margin of error of five to 10 percent. Accordingly, hose manufacturers base their flow and friction loss numbers as an average of hundreds of flow tests. Once you obtain flow test results, display the PDPs for preconnects and friction loss numbers on a laminated chart. Similarly, some departments apply labels to their pump panels or use automotive pin stripe tape on preconnect discharge gauges to indicate their PDP.
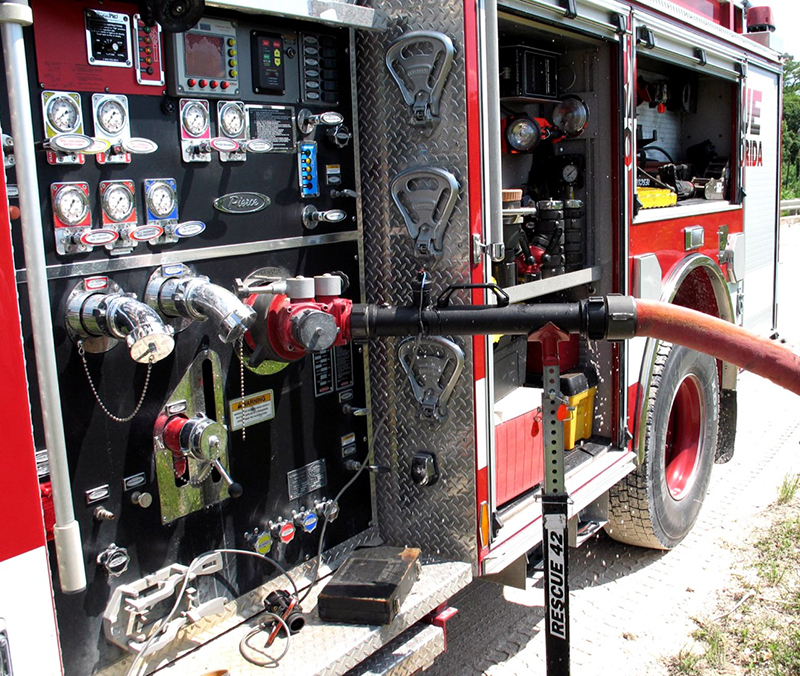
(12) A flowmeter is connected to the pump intake.
Team Up Engine Companies
Getting the first hoseline into operation should be a concerted effort of engine companies working together; not competing with each other. The Fire Department of New York will not hesitate to team up three engine companies to get that critical hoseline in operation. One of the biggest mistakes an engine company officer can make is to underestimate the number of personnel necessary to advance a charged hoseline around corners and where it changes directions at stair landings. Consider the consequences when an officer attempts a hose advance in a multiple dwelling with insufficient personnel: His crew advances the hoseline onto the fire floor from an enclosed stairwell, which now fills with smoke, and they struggle to get the nozzle just inside the door of the fire apartment when they run out of air and are forced to follow the hoseline back to the stairwell. With no one to relieve them, this engine company made conditions worse by abandoning their hoseline, which is now blocking open the door to the stairwell and the fire apartment (photos 13-16).
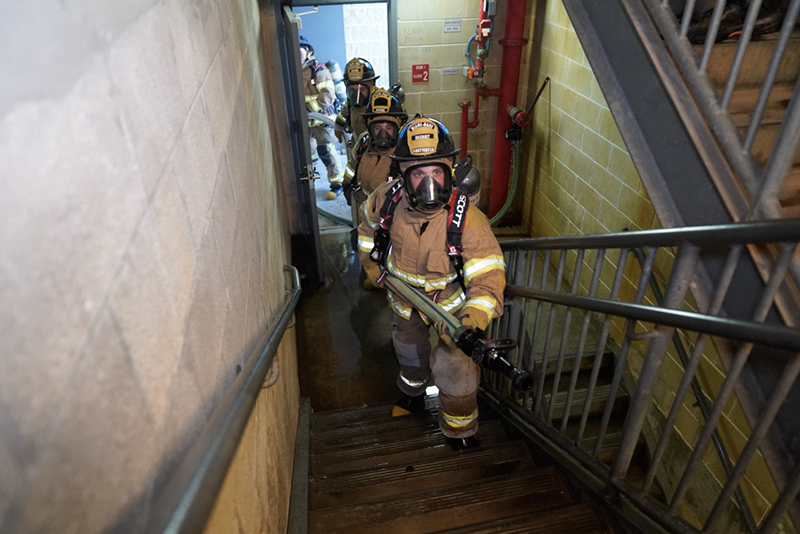
(13) Engine companies team up to advance a charged two-inch hoseline connected to a standpipe outlet in a stairwell below the fire floor. (Photos 13-16 by Rick Stephens, courtesy of Miami-Dade Fire Rescue.)
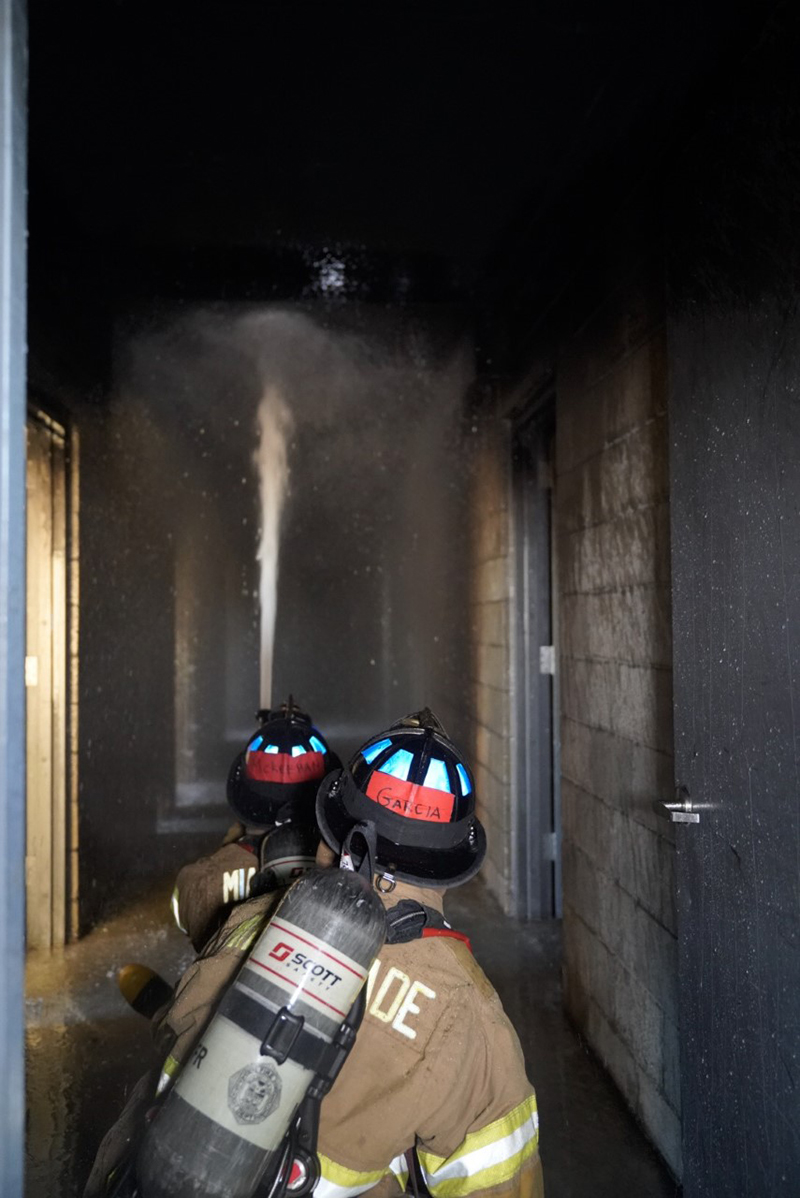
(14) The nozzle firefighter and officer advance down the hallway to the fire compartment but not without assistance from a firefighter feeding them hose from the fire floor stairwell landing.

(15) A firefighter operating at the fire floor stairwell landing receives hose from a firefighter operating at the mid-landing and feeds it to the nozzle team advancing down the hallway.
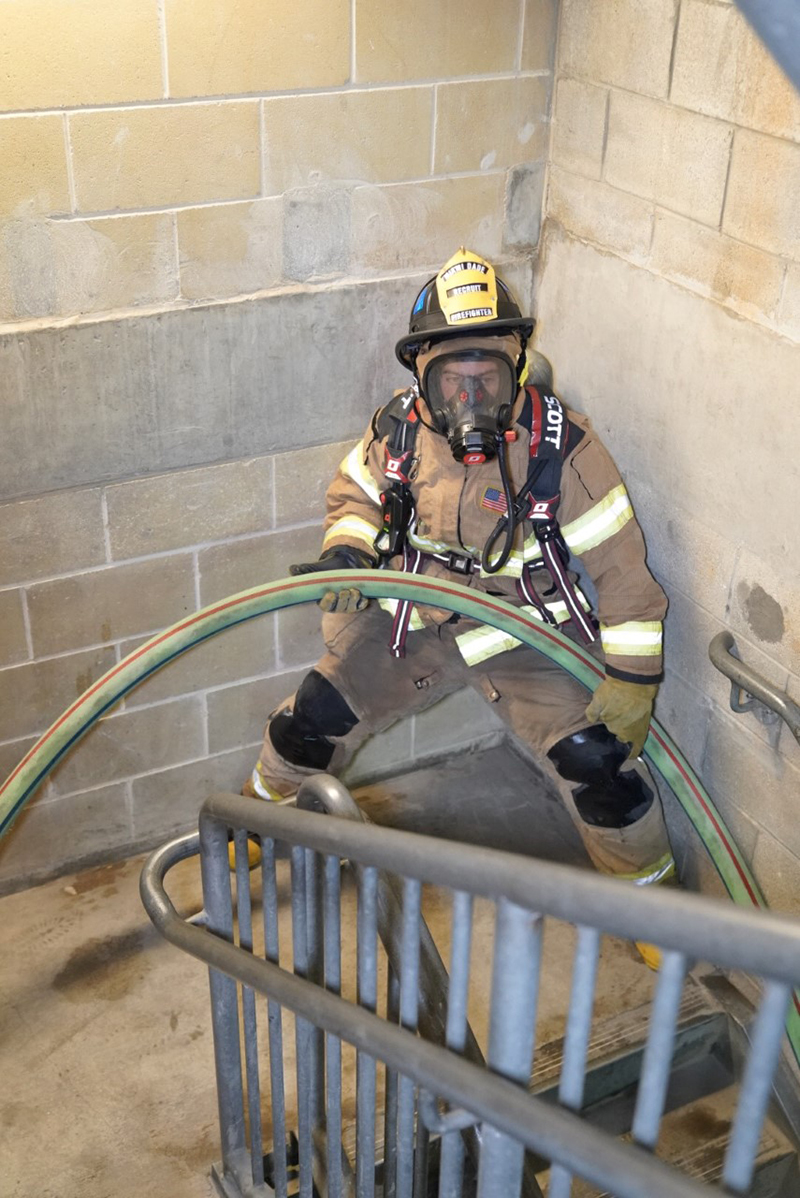
(16) A firefighter operating at mid-landing is receiving hose from firefighters operating on the floor below the fire and feeding it to the firefighter operating at the fire floor stairwell landing.
Charge the Line, Now!
For driver-engineers and engine company officers, at some point in their careers the apparatus pump will fail to pump water. Often, this is the result of the engineer missing a step when engaging the pump. Maybe the engineer failed to put the transmission in drive after engaging the pump, or perhaps the parking brake was applied when the apparatus was still in drive, binding gears in the transfer case. Whatever the cause, yelling at the engineer to charge a hoseline will certainly not make him get water any faster. At that point, no one feels worse about not getting water than the engineer. The appropriate response is for the engine officer to calmly tell the engineer to get back in the cab and repeat all the steps for engaging the pump; this usually solves the problem. If it doesn’t, then the engineer must engage the emergency pump shift mechanism.
ENDNOTE
1. Gates, David. (February 2021). “Calculating Available Water from a Hydrant,” Fire Engineering Water on the Fire Supplement,18-19. https://emberly.fireengineering.com/firefighting/the-february-2021-water-on-the-fire-supplement/.
BILL GUSTIN is a 49-year veteran of the fire service and a captain with Miami-Dade (FL) Fire Rescue. He began his fire service career in the Chicago area and is a lead instructor in his department’s Officer Development Program. He teaches tactics and company officer training programs throughout North America. He is a technical editor and an advisory board member of Fire Engineering and FDIC International.