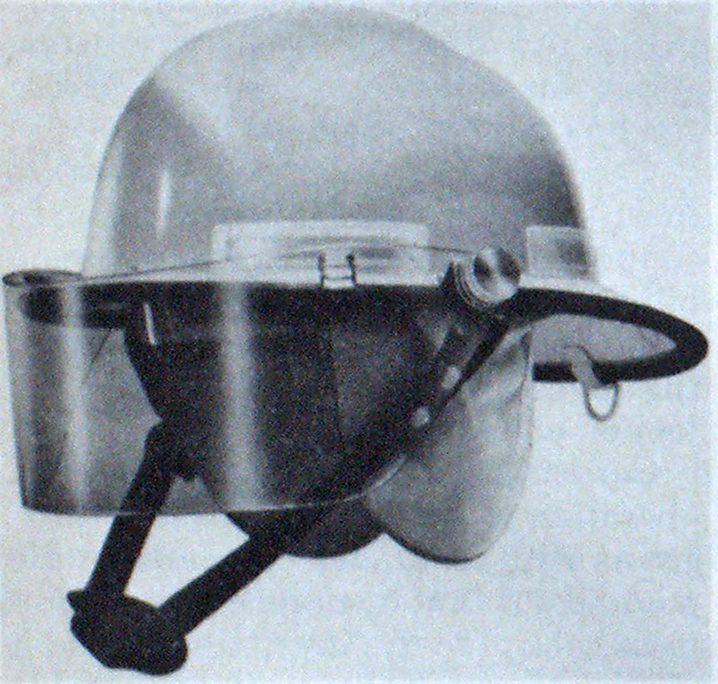
Designing Improved Helmet Starts With Performance Criteria, Testing
features
As the members of the research and development department of Cairns & Brother, Inc., began design designing an improved municipal fire service helmet, two federal specifications were developed that influenced their work.
The R&D people had as their goal a helmet that would exceed current OSHA standards and reach new levels of protection, reliability and comfort. They had made some progress on the Phoenix, the working name for the new helmet, when the United States Department of Defense asked Cairns to design a military fire department helmet to meet the toughest specifications ever established.

About the same time, the National Bureau of Standards published its “Model Helmet Performance Criteria for Structural Firefighters.” This pamphlet contained recommendations for establishing minimum criteria for helmet performance that were developed for the then National Fire Prevention and Control Administration, now the United States Fire Administration.
Test standards set
The NBS criteria set testing standards for impact attenuation, penetration, heat resistance and electrical insulation. Performance standards were specified for design features such as earlaps, chin straps and face shields. Labeling requirements also were instituted. The model performance criteria represented the first attempt by any national agency to establish specification for municipal fire fighters’ helmets.
Using the data we had already compiled on the Phoenix, and with the military and model helmet specifications as guides, we began developing what was to become the Phoenix 660.
Since the primary component of any helmet is the shell, the Phoenix 660 shell had to be strong enough to withstand penetration, impact, and heat load tests, yet resilient enough to accommodate an effective suspension system. We carefully tested materials for impact, penetration, heat and flammability. Finally, we chose a high-grade polycarbonate shell with the desired wall thickness, added suspension systems, and methodically constructed the helmet. The prototype helmet then underwent a series of tests patterened after the military and model specifications.
Two specs similar
Although written independently, the military and model helmet specifications were strikingly similar. The most significant new feature of each specification was a side-blow attenuation provision that required protection from blows to the side of the head. Prior to this, impact tests were made only in the apex area.
The provision for side-blow attenuation spurred the development of a suspension system designed to increase the helmet’s spectrum of protection. At the time, two types of suspension systems were in wide use. Web strap, fixed crown suspension provided excellent protection from impact and penetrating objects at the top of the helmet. The full foam suspension provided adequate protection from top impacts, but was more effectively used to cushion blows to the side of the head. By integrating these two suspension systems, we developed what is now known as the Phoenix Impact Cap. Our next step was to put the helmet prototype with the newly designed Impact Cap suspension system through a series of exhaustive tests.
As part of Cairn’s research and development process, each production helmet undergoes a series of major inhouse tests, including tests for impact, convection heat, radiant heat, penetration and weight.
Apex impact test
The Phoenix 660 prototype was tested for impact resistance at the apex and, in conformance with the new specification, on the sides. The test for apex attenuation measures the helmet’s ability to absorb force. The helmet, strapped to a 7 1/4 standard test head form, is positioned at the base of the testing apparatus. A steel ball is then dropped via a monorail device on the top, or apex, of the helmet. A force transducer measures the compression of the head form which remains after the helmet has absorbed the impact.
To illustrate this process, we will use the example of a hammer hitting a finger encased in a foam rubber pad. As the hammer strikes the pad, the pad compresses, absorbing the energy of the blow. The finger begins to sense pressure as the hammer continues its downward movement. The pressure increases, causing the sensory devices in the finger to alert the brain.



In the actual test, the electronic force transducer is the sensory nerve and an electronic test console acts as the brain, computing both the time it takes for the head form to absorb the compression from the blow and the total compression delivered to the head form. This information, combined with a measure of the highest level of force attained, is then displayed as a digital reading of the time/force profile. The time/force profile then was compared with the requirements in the test specification.
In testing the Phoenix 660, our goal was to meet the test specification requirements of ANSI Z89.1 (currently recognized by OSHA), which establishes 850 pounds as the maximum level of impact force a head can withstand without injury.



In the test for side-blow attenuation, the helmet is again strapped to a 7 1/4 test head form. This time, however, the steel ball or infinite mass, is positioned at the base of the testing apparatus and the helmet/head form is dropped on the ball. Now, instead of measuring the force delivered to the object, we measure how well the helmet slows down the impact of the head form.
To explain this process, we use the executive novelty toy, which is made up of suspended steel balls. One end of the rack of balls is placed against a solid brick wall, which serves as our infinite mass. We swing back the first ball on the free side and drop it into the rack. The ball strikes the balls in the rack, but because they have nowhere to go, they return all of the energy to the striking ball, causing it to rebound.
Now let’s place a walnut shell on the striking ball and swing it against the stack again. When the ball and shell make contact with the rack, the walnut shell crushes slightly, absorbing some of the energy. The striking ball continues to move forward, slowed somewhat by the force absorbed by the walnut shell and delivering the remaining energy to the balls in the rack.
Conduct of test
In the actual test, the helmet/head form is dropped on the steel ball. The acceleration transducer and its monitoring equipment measure the slowing rate of fall and the time it takes for the helmet/head form to stop. The combined measurement of the deceleration and time is then converted to an electrical signal or digital readout. The information contained in the readout is compared with the minimum requirements outlined in the model helmet and military specifications.
The criterion of 400 G’s of deceleration has been established by the model helmet and military specifications as the maximum level of side-blow impact a head can withstand without injury. This is the measurement we used as a guide in testing the prototype helmet.
The model helmet performance criteria also introduced two new testing procedures for heat resistance. The thermal soak, or convection heat, test requires that the helmet be placed in a forced hot-air oven for three minutes at 485°F. In the radiant heat test, the helmet is exposed to a radiant heat source of 6/10 watt and then measured for impact resistance. The prototype helmet underwent both tests and the degree of distortion and impact resistance was computed.
Next, the prototype helmet was measured for penetration resistance. Using the same monorail system as the impact test, the helmet, strapped to the test head form, was positioned at the base of the apparatus. A projectile was then shot down the monorail and the penetration depth measured.
The final stage in the prototype testing ran the gamut from dielectric testing (electric shock resistance) to weighing the helmet. We tested the prototype helmet to the most rigorous performance levels of each of the specifications to ensure that the finished product would not fall short in any category.
Our goal was to accomplish all this in a lightweight helmet. The military specification required an overall helmet weight of 30 ounces, while the model helmet specification had no weight requirement. The Phoenix 660 was, therefore, designed to meet the military requirement of 30 ounces. The addition of earlaps, edge beading, adjustable chin strap with cup, and face shield increased the municipal fire fighter’s helmet weight to 42 ounces.
After exceeding the standards in our prototype testing and making a few minor revisions, we were now ready to begin production. The model for the helmet shell was cast into a mold for thermoforming the production shells. These were then fitted with accessories, such as face shields and suspension systems. The first few production helmets were sent into the field for weartesting.
Helmets field-tested
Typically, a helmet is designed with the needs of a major fire department in mind. The helmets are evaluated by the people who rely on them to perform to the standards in the specifications. We, in turn, rely on the fire fighters who wear-test our helmets to tell us if the helmets meet their requirements for comfort and reliability.
The last step in the production of any helmet is quality control. Production, quality control, and management personnel who had participated in developing the Phoenix 660 teamed up to formulate a checklist of critical design features of the new helmet. Based on past helmet manufacturing experience and field-use data, this team established exhaustive quality control inspection and test criteria. These included, for example, measuring overhead suspension straps for elasticity as well as weighing each rigid foam cap for the proper density. In addition, every helmet is visually inspected for workmanship and proper assembly, including functional checks on such features as face shield and chin strap adjustments.
Quality control is our assurance that helmets leaving our shop have each component in perfect working order. We emphasize quality control for one reason alone—the personal safety of fire fighters wearing our helmets.