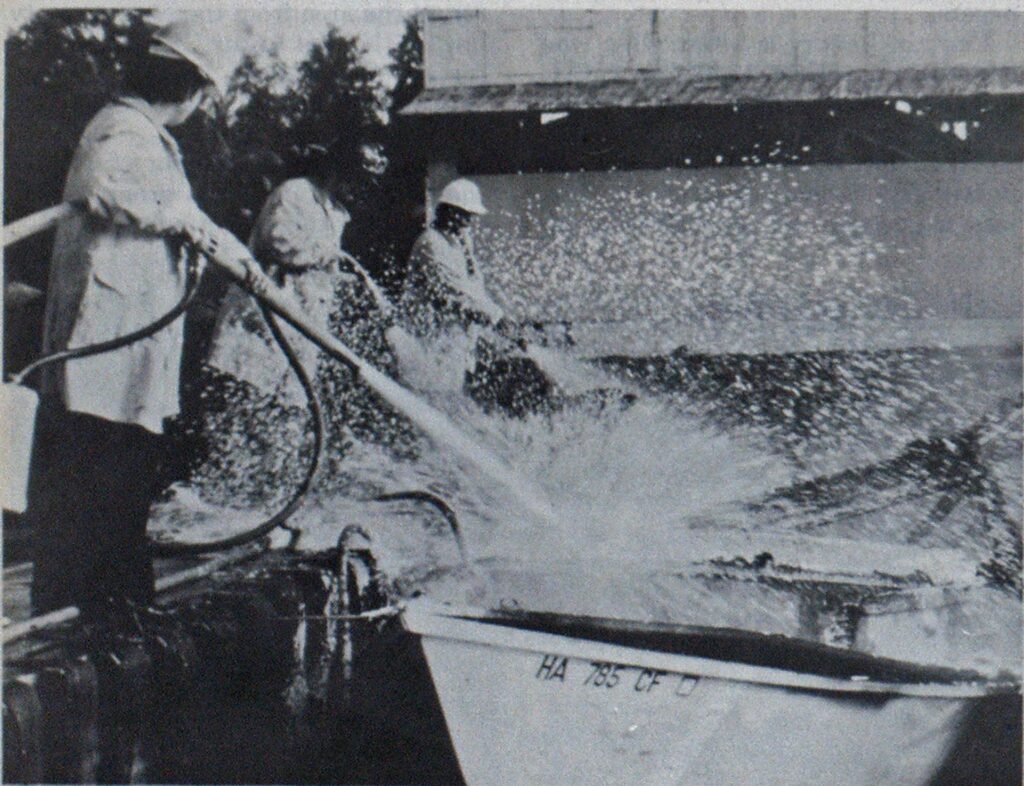
To Aspirate or Not to Aspirate AFFF? Tests, Advice Help Answer Question
features
Foams have been used in the United States for fighting flammable liquid fires for more than a half century, but it was just prior to the outbreak of World War II that mechanical foam was introduced. Rapid progress was made in foam technology in the succeeding years and finally, about a decade ago, aqueous film-forming foam (AFFF) became available to civilian fire fighters. AFFF had been developed by the United States Navy in the mid-1960s.
Despite great progress in understanding foams and developing new ones to handle modern products, there is still little agreement among fire fighters on the basic question of what type nozzle to use whether it should be air-aspirated or not. Everyone has an opinion on this question but all too often these opinions are based on incomplete information.
This dilemma indicates the need for further research to gain more knowledge and for better dissemination of currently available information. The purpose of this article is to bring together test data, fire department practices and manufacturers’ recommendations on how to apply AFFF. Then we will try to draw a meaningful conclusion.
Composition of AFFF
Basic to understanding the problems, though, is an understanding of just what AFFF really is. Regardless of which manufacturer’s product you use, each AFFF concentrate is a combination of a surfactant to lower the surface tension of water and a synthetic foaming agent. This combination of chemicals produces an aqueous film, a thin film of foam solution (water plus foam liquid) that rapidly spreads across the surface of a burning liquid. This action is based upon the ability of the surfactant to make water float on the surface of liquid fuels which are lighter, i.e., have a lower specific gravity, than water.

Photo by John E. Bowen
The aqueous film actually drains out of the foam, advancing across the fuel surface slightly ahead of the foam blanket. This film is a monolayer (just a molecule or two thick) and thus very fragile. It is easily disrupted by convective heat and turbulence in the fuel. The aqueous film, being so fragile, must be continuously replaced from the foam blanket. So, without a visible blanket, the self-healing property of the film is lost. When this self-healing characteristic is lost, the film is disrupted and burnback and flashback resistances are lost also.
AFFF actually extinguishes a flammable or combustible liquid fire in a combination of three ways. The film physically separates the flame and oxygen from the fuel surface. Secondly, the film acts as a vapor seal, suppressing vapor release from the fuel surface. Last, the film absorbs heat from both the fuel and exposed solid surfaces.
Definitions
Before continuing, however, let’s make certain that we are all talking about the same thing when we use these terms. By ‘flashback resistance,’ I mean the resistance of a flammable liquid to reignition caused by exposure of its vapors to an ignition source, such as a hot metal surface. ‘Burnback resistance’ refers to the ability of a foam blanket to resist direct flame impingement, such as in a partially extinguished flammable liquid fire.
The ‘expansion’ or ‘expansion ratio’ of a foam is the ratio of the volume of foam formed to volume of solution used. Expansion is somewhat influenced by temperature, being slightly less at lower temperatures. We won’t consider this important for our purposes, however.
The ‘drainage rate’ of a foam is the rate at which foam solution drains from the foam blanket to form the aqueous film. Drainage rate is frequently expressed as the ‘25 percent drainage time,’ i.e., the time in minutes for onefourth of the total liquid solution to drain from the foam blanket. ‘Quarter life’ is used synonymously with 25 percent drainage time. The quarter life of a foam also decreases as the temperature drops. A decrease in water pressure will shorten the 25 percent drainage time, too.
Lastly, a ‘skin fire’ is a flammable liquid fire in which fuel depth is 1 inch or less, such as a spill on a solid surface.
Essential properties
There are certain essential properties or characteristics that all AFFF blankets must have. These are universally agreed upon, so let’s look at them first.
No foam can be used successfully unless it is chemically resistant to attack by the fuel. This is why polar solvent liquid AFFFs had to be developed specifically for use on fires involving alcohols and other polar solvents. A useful foam must he capable of withstanding radiated heat and direct flame impingement. Also, a foam must not be too viscous, i.e., it must be sufficiently fluid to flow smoothly and quickly across the fuel surface. All AFFFs in use today meet these criteria. Otherwise, they would never have been adopted for fire fighting purposes.
However, all mechanical foams must be applied properly if the highest quality foam is to be obtained. In the case of AFFFs specifically, the method of application has an important bearing on the characteristics of the resulting foam. At the root of this problem is the question of whether AFFF should be applied with specially designed air-aspirated foam nozzles or with conventional water-fog nozzles that are not air-aspirated.
Before addressing this question directly, let’s try to put it into proper perspective. From the outset, you must understand that no single method of AFFF application will yield optimal results for all quality parameters. It is a matter of opt imizing one characteristic and sacrificing somewhat on another. The best foam will be a careful balance of all factors.
Two basic questions
We’ll consider two basic questions: (1) How fast does air-aspirated AFFF (AA-AFFF) and non-aspirated AFFF (NA-AFFF) extinguish a fire? (2) What is the burnback and flashback resistance of AA-AFFF vs NA-AFFF? You must clearly understand which question is being addressed when comparing question depends upon which of these two questions you’re considering, as we shall see.
The answer to the AA-AFFF vs NAAFFF question also depends upon the conditions under which you have conducted your tests. For example, some factors that can affect the outcome are the type and depth of fuel in the test fires, and preburn time during which light ends will burn off, giving an apparent but false increase in burnback and flashback resistances.
It is a difficult task to design and conduct an unbiased test. Instead, it is all too easy to consciously or subconsciously bias the results by neglecting a factor that can influence the data. For instance, use of a fuel with a high flash point can give false burnback and flashback resistances. A lengthy preburn coupled with shallow fuel can affect all parameters, making the fire easier to extinguish and also apparently making reignition difficult.
Keep these points in mind as we evaluate some test data that the United States military and foam manufacturers have collected.
Aspirating nozzles
First, though, we’ll discuss air-aspirating nozzles at length, so let’s make sure that we all know exactly what we mean. An air-aspirating (AA) nozzle is one that has been designed specifically for foam application. It incorporates a venturi tube whereby a jet of foam concentrate enters a long foam tube as water flows through the constriction. This action lowers the atmospheric pressure around the air inlet ports at the base of the air-foam mixing barrel so air enters the solution. The air and foam solutions are mixed by high turbulence in the tube. These types of nozzles, which may also have stream-shaping devices in the barrel for pattern variation, produce a relatively viscous foam. The expansion ratio for AFFF generated from an AA-nozzle is likely to be in the range of 6 to 15-fold.
Non-aspirating (NA) nozzles, on the other hand, are simply conventional, variable-pattern, water-fog nozzles. There is no attached mixing barrel. The venturi principle is not used for introducing air into the stream, so it is primarily a foam concentrate and water mixture that is discharged from the nozzle. Any air that is ultimately mixed into the solution is entrained while the solution is in flight. These NA-AFFFs are quite fluid, having low viscosities with expansion ratios on the order of 2 to 10.
The U.S. Navy has conducted much of the research on effectiveness of AAAFFF vs NA-AFFF. Let’s briefly review some of these tests and data. The first to attract the attention of the civilian fire service was conducted at the Jacksonville, Fla., Naval Air Station in 1968. Hand lines with AA and NA nozzles were used for attacking and extinguishing 3500-square-foot JP-5 (kerosine) spill fires. Fire control and extinguishing effectiveness of the NAAFFF was 20 to 100 percent greater than that of the air-aspirated AFFF.
The increased effectiveness of NAAFFF in fire extinguishment is not surprising because, as stated above, NA-AFTF is very fluid. It spreads across the surface of a burning fuel faster than the more highly expanded—and thus more viscous— AA-AFFF. Therefore, the former should extinguish the fire faster. Since NA-AFFF is more fluid, it will have a shorter 25 percent drainage time and the burnback resistance theoretically would be less. Unfortunately, this parameter was not considered in these tests, however, so the results seemed to “prove” that NA-AFFF was more effective than AA-AFFF.
Larger-scale test
By 1972, AFFF had replaced protein foam on all crash-fire-rescue vehicles at all military air activities. This heightened the demand for meaningful information on the use of AFFF, so further studies were undertaken at the China Lake, Calif., Naval Weapons Center. Test fires ranged from 4000 to 48,000 square feet in area, so turret nozzles were used rather than hand lines. Again, test results seemed to indicate that NA-AFFF was more effective than AA-AFFF. This was attributed to the greater range and trajectory of NAAFFF, factors that are both directly related to the lower viscosity of NA-AFFF. It was observed in these tests that burnback resistance was less when NA-AFFF was used, as compared to AA-AFFF, but once again no measurements were taken to document this effect. Therefore, the data were interpreted as supporting the earlier results from Jacksonville to the effect that NA-AFFF was superior to AA-AFFF for fire extinguishment.
In 1976 and 1977, E. J. Jablonski of the Naval Research Laboratory undertook the most extensive study yet of NA-AFFF vs AA-AFFF. Turret nozzles with rated capacities of 250 gpm and 750 to 800 gpm were used on Navy MB-1 and P4-A, and USAF P-4 crash trucks. The fuel was JP-4. Test fires had surface areas of 4000 and 8000 square feet for the 250-gpm and 750 to 800-gpm nozzles, respectively.
Two-phase study
These tests were conducted in two phases: phase I for the 250-gpm nozzles and phase II for the 750 to 800-gpm ones. Let’s look first at the phase I (250-gpm nozzle) tests. The AA nozzle was a Rockwood foam barrel turret. The NA nozzle was an Elkhart Model DSF. Military specification FC-206 AFFF was used. One thousand gallons of JP-4 were poured into a diked area, providing a calculated fuel depth of 0.4 inch. Thirty seconds of full-area preburn were permitted in each study.
Expansion ratios for the AA and NA foams from these 250-gpm nozzles were 5.2 and 2.5, respectively, 52 percent less for the NA-AFFF. The quarter life for NA-AFFF was 39 percent less than for the AA-AFFF (3.3 vs 5.5 minutes). To repeat once more, this is due to the greater fluidity of the NA foam. The reach of the NA stream was 57 percent greater than that of the AA stream, again a manifestation of the greater fluidity of the former.
The 90-percent extinguishment times for AA and NA foams were 29 and 21 seconds, respectively. This is readily explained by the fact that the lower viscosity of the NA-AFFF permits it to flow across the fuel surface faster.
Close accord with theory
These data are thus in close accord with the theoretical discussion above concerning foam properties and Characteristics. The AA foam has a two-fold greater expansion ratio although even its 5.2-fold expansion is somewhat low. Since NA-AFFF has a significantly shorter quarter life, we would expect it to have less burnback resistance also.
Burnback evaluation was begun seven to eight minutes after fire extinguishment. The time, in minutes, to achieve reburning over 25 percent of the total surface area was recorded. There was a small difference between the two foams, but it was not statistically significant, meaning that the two times can be considered equal. We would expect burnback resistance to be less for NAAFFF, however. Let’s look at the data for the 750 to 800-gpm nozzles and then we’ll come back to this question.
The nozzles used in the phase II (750 to 800-gpm) tests were a Feecon double barrel foam turret (AA) and an Elkhart/Feecon turret nozzle (NA). FC206 AFFF was used again. Two thousand gallons of JP-4 were poured over 8000 square feet, again providing a fuel depth of 0.4 inch.
Once again, AA-AFFF had the greater expansion ratio and 25 percent drainage time, whereas NA-AFFF had a 22 percent greater reach, all in accord with our theoretical expectations. The 90-percent extinguishment times were 33 percent shorter for NA-AFFF (24 seconds for NA-AFFF vs 36 seconds for AA foam). This, also, we would expect.
Little burnback difference
Since AA-AFFF has the greater expansion ratio and longer 25 percent drainage times, we would predict that AA-AFFF would also provide the better burnback protection. Such was not.the case under these test conditions, however. Burnback times for AA-AFFF and NA-AFFF were 15.9 and 16.2 minutes, respectively. This is not a statistically meaningful difference. Note, though, that emphasis should be placed on the phrase, “under these test conditions.” This is because test conditions can do so much to affect the resultant data. It becomes virtually impossible to extrapolate data from one situation to another.
Here are some factors that may have influenced the apparent similarity in burnback times in these China Lake tests. First, the fuel used was JP-4, a mixture of 25 to 35 percent kerosine and 65 to 75 percent gasoline. Gasoline has a much lower flash point (—40° to —50°) than does kerosine (100° minimum) and a much higher vapor pressure. Therefore, one would predict that gasoline would burn out of the mixture first, leaving a kerosine-enriched residue. Kerosine, then, with its inherent properties would be more difficult to reignite than either JP-4 or gasoline. This could account in part for the apparent equality of the AA-AFFF and NA-AFFF burnback resistances.
Secondly, fuel depth in these tests was only 0.4 inch. The test fires were thus skin fires rather than in-depth flammable liquid fires. It has been well documented that skin and in-depth fires respond differently to foam applications.
Third, burnback resistance measurements were begun seven to eight minutes after extinguishment. Quarter life times for both foams were less than six minutes in every instance, so much of the foam blanket had dissipated before burnback resistance was measured.
These comments are not meant to cast doubt on the validity of the China Lake tests but rather to emphasize the importance of considering all test conditions when interpreting data. Only when similar conditions exist can data be extrapolated from one situation to another.
What manufacturers say
Foam manufacturers are logical sources of information on how to use their products, so I posed this question to each of them: Do you recommend using air-aspirated or non-aspirated nozzles with your AFFF products?
Edward Norman of National Foam Systems, Inc., said, “Our position is that while AFFF is usable through non-aspirating nozzles, the foam produced by these nozzles is of poor quality and short life when compared to that produced by aspirating nozzles …. When AFFF is used through an aspirating nozzle, the foam blanket has a much longer life and therefore can act as a continuous source of fresh film.”
In its “Light Water AFFF Products and Systems Engineering Manual,” the 3M Company states that its AFFF can be applied through both foam (AA) and NA water-fog nozzles. It is acknowledged that foam nozzles are more effective, however. Company tests clearly demonstrate that AA-AFFF has much greater expansion and an almost threefold longer 25 percent drainage time than does NA-AFFF. Many fire service authorities consider 25 percent drainage times of less than two minutes to be unacceptable. With NA-AFFF in these tests, the time averaged 1.1 minute whereas it was 3.1 minutes for AAAFFF.
No information was available from other foam manufacturers.
Let’s turn now to other sources of information on this question of AA vs NA-AFFF. The NFPA “Fire Protec tion Handbook” (14th edition, 1976) states that NA water-fog nozzles can be used with AFFF solutions for attacking and extinguishing fuel spill fires in shallow depth, i.e., skin fires. Unless air is aspirated into the stream at the nozzle, though, it is cautioned that the resultant foam is generally fast-draining and has a low degree of burnback resistance. It is thus implied that the use of air-aspirated foam nozzles is preferred.
Standard 406M position
NFPA Standard 406M (Manual on Aircraft Rescue and Fire Fighting Equipment and Techniques for Fire Departments Using Structural Apparatus and Equipment, 1975) unequivocally states that AA foam hand line nozzles are preferred over NA water fog nozzles for AFFF application. The reason given is that AFFF generated through NA water-fog nozzles has a lower expansion ratio and therefore a higher application rate is generally required.
The recommendations of foam manufacturers and the NFPA overwhelmingly favor the use of air-aspirated, specially designed foam nozzles for AFFF application, although the U. S. Navy reports do not concur.
The recognition of the value of AFFF as a fire extinguishant has rapidly increased in the past decade and many fire departments are now replacing protein foam with AFFF on each engine company. Thus, in preparation of this article several departments throughout the United States and Canada were asked about their AFFF practices. In this quick and rather unscientific survey of 12 fire departments, none was found that routinely equips every engine with an AA foam nozzle. Each used NA water-fog nozzles for this purpose. Captain John Maleta of the Los Angeles County Fire Department indicated that that department does plan to provide each company with a foam nozzle very soon,though.
Many respondents stated that the advantages of AA nozzles notwithstanding, the monetary aspect of purchasing foam nozzles has forced them to make water-fog nozzles serve dual purposes.
Match nozzle, proportioner
Regardless of the type of nozzle used, AA or NA, there are certain considerations that must be taken into account before putting an AFFF system into operation. For both types of nozzles, the rated flow must be carefully matched to that of the proportioner. This is vitally important, so check it carefully. Most foam system failures are traceable directly to a mismatched nozzle and proportioner.
Remember that some variable-pattern water-fog nozzles have different flow rates at different pattern settings. Therefore, it may not be possible to use a particular nozzle at all pattern settings. In prefire planning and training sessions, determine the settings that are compatible with your proportioned flow rate. Mark these on the nozzle for rapid reference on the fireground.
Be certain that the metering valve on the proportioner is set at the proper percentage for the AFFF you are using.
The required flow rate will be achieved only when the proper nozzle and eductor inlet pressures are maintained. Read the manufacturer’s literature thoroughly to determine the optimum operating pressures for the equipment you are using. The requirement for accurate flow rate and eductor and nozzle pressures also places limits on the length of the hoseline that can be used because of friction pressure loss. These limitations are equally applicable to both AA foam nozzles and NA water-fog ones.
Keep nozzle fully open
When using an NA water-fog nozzle, make sure that the nozzle shutoff is fully open at all times. Don’t open and close it, as this will disrupt proper proportioning of the AFFF concentrate. Airaspirated foam nozzles commonly lack a shutoff valve to avoid this problem.
Don’t neglect to flush both nozzle and eductor thoroughly with water for a minimum of five minutes after each use.
The better quality AFFF is obtained from AA foam nozzles. Water-fog nozzles are in common use for AFFF generation, though. Regardless of the type of nozzle that you use, however, proper AFFF proportioning and application can be achieved only through practice. Experiment with various pressure combinations and How rates to prove to your own satisfaction just what works efficiently and what doesn’t work at all.
In closing, I would like to point out that while we’re agonizing over the problems of AA vs NA-AFFF, the manufacturers of foam products haven’t forgotten the fire fighters who face those flammable liquid fires. At least one company is already marketing a 3 percent AFFF that can be applied through standard NA water-fog nozzles to produce high quality foam with good extinguishing properties and reignition protection. It’s simply an AFFF agent which requires low energy input to convert the solution into good quality foam. Perhaps this new generation of AFFFs will replace those in use today even before we really learn how to use today’s AFFFs to their maximum advantage.