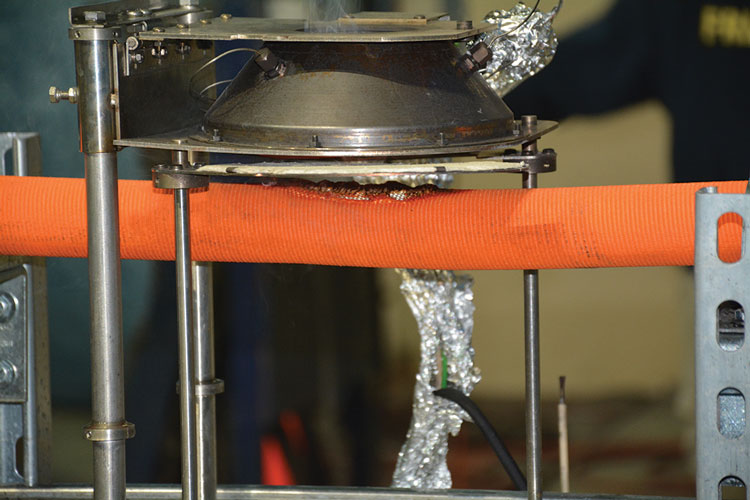
BY LISA A. HERB AND ADAM ST. JOHN
![]() |
(1) The front exterior of townhouses used in full-scale scoping tests. (Photos by ATF Fire Research Laboratory.) |
Interior attack hoselines have been failing more frequently from exposure to heat during fire suppression. The National Institute for Occupational Safety and Health (NIOSH) Fire Fighter Fatality Investigation and Prevention Program (FFFIPP) has observed this alarming trend.
The tragic Boston Back Bay fire on March 26, 2014, brought thermal hoseline failure to the forefront. Lieutenant Edward J. Walsh and Firefighter Michael Kennedy of the Boston (MA) Fire Department lost their lives as they advanced their hoseline down the stairs into the burning basement of a Boston brownstone. An open rear basement door caused a rapid increase in temperature in the basement, in the stairwell, and on the first floor. Strong winds exacerbated this ventilation flow path. Two hoselines inside the structure – a charged 1¾-inch hoseline and a dry 2½-inch hoseline – were burned through, preventing water flow at the nozzle. A trapped firefighter transmitted several Mayday messages over the radio following the hoseline rupture.
![]() |
(2) A townhouse during a full-scale scoping test. |
Like firefighter turnout gear, a hoseline provides critical thermal protection for interior crews; however, hoselines may thermally fail at a point remote from the nozzle, thus removing this protection and potentially trapping the crew. Research has shown that structure fires involving modern fuels develop significantly faster than those of several decades ago. Although firefighter protective clothing (turnout gear) and respiratory protection (self-contained breathing apparatus) have improved, the thermal standards to which fire hose is evaluated have remained unchanged. Firefighting gear is designed to provide a limited degree of thermal protection during unavoidable emergency conditions. However, for fire hose, comparable thermal performance data are currently unavailable.
In May 2014, the NIOSH FFFIPP contacted the Bureau of Alcohol, Tobacco, Firearms and Explosives (ATF) Fire Research Laboratory (FRL), requesting thermal analysis of several popular models of attack hoselines. The ATF has the federal nexus for investigating fires, frequently providing expert resources to state/local fire investigators to determine origin and cause. Both the ATF and NIOSH have documented multiple incidents of attack hoseline thermal failure (rupture) during firefighting operations. Many of these fires resulted in injuries/fatalities to residents and firefighters. Worcester Polytechnic Institute recently developed a database to track hoseline burn-through incidents. As of October 2015, according to the database, there have been more than 172 reported hoseline burn-through incidents.1
![]() |
(3) The labeled hoselines went through the front door and up the interior stairs. |
The ATF conducted research in two phases: full-scale scoping fire testing and bench-scale laboratory testing. The bench-scale laboratory testing was intended to establish a repeatable, small-scale testing protocol to evaluate hoseline samples. Several full-scale scoping tests were also conducted in acquired structures to validate and expand on the bench-scale data. In both tests, the elapsed time to hoseline failure was recorded. Failure was defined as a significant loss of operating pressure, usually associated with rupture of the interior lining of the fire hose. The tests’ purpose was to provide general data regarding the thermal performance of attack fire hose to the FFFIPP, the National Fire Protection Association (NFPA), the fire service, and the fire investigation community.
Full-Scale Scoping Testing
Full-scale scoping tests in acquired townhome structures were conducted to record the approximate heat flux level (radiant exposure) and the temperature at the time of rupture (photos 1-2). Three 1¾-inch hoselines were routed in parallel throughout the acquired structure’s first and second stories. One hoseline was dry and unpressurized, one was pressurized with water (static), and the third was pressurized with water flowing through the nozzle (photo 3).
![]() |
(4) The prefire interior stairway. |
The hoselines failed when the measured radiation (heat flux) levels at the floor ranged from 14 to 35 kW/m.2 These heat flux values were typically measured as flames extended along the ceiling (rollover) above the hoseline just prior to the flashover transition. The hoselines in all four full-scale scoping tests failed when the heat flux exceeded 40 kW/m2 (photos 4-5, Figures 1-2). Accordingly, it was decided for bench-scale laboratory testing to maintain constant heat flux levels at 30 and 40 kW/m2 and compare the relative times to failure for the various models of hoseline tested (Table 1).2
Bench-Scale Laboratory Testing
At the ATF FRL, 78 bench-scale laboratory tests were conducted using an electric resistance coil heater affixed to a metal platform (photos 6-7). The testing was intended to simulate the same heat flux exposure seen in the full-scale scoping tests at the time of hoseline failure in a repeatable environment. Each test was conducted with the hoseline pressurized with air or water to a typical operating pressure of 120 pounds per square inch (psi).
![]() |
(5) The postfire interior stairway in full-scale scoping tests. |
All hoselines evaluated during the bench-scale laboratory tests were new except for Mercedes Textiles Aquaflow Plus, of which both new and used samples were employed. NIOSH selected and provided the hoseline models to the ATF to evaluate a range of popular models and construction techniques.
During hoseline testing with pressurized water, the hoselines failed dynamically and sometimes violently (photo 8). Accordingly, each hoseline was first tested with charged air; then, the results were verified with a limited number of pressurized water tests (photos 9-10). Hoseline data from the 78 bench-scale laboratory tests are listed in Table 2.
Discussion
![]() |
Heat flux values (y-axis) vs. time (x-axis) for full-scale scoping test, burn 1. |
Heat flux values recorded at the floor of a compartment fire will vary significantly as a fire develops. It is difficult to quantify a “typical” firefighting operating environment since incident heat flux values fluctuate significantly as a fire develops. The elapsed time for firefighting equipment to reach thermal failure depends on time and on relative heat flux values. Failure of personal protective equipment (PPE) can occur at relatively low heat flux levels (less than 10 kW/m2) for long durations or high levels (80 kW/m2) for short durations.
NFPA 1961, Standard of Fire Hose (2013 edition),3 does not currently include a radiant heat exposure test. Both NFPA 1971, Standard on Protective Ensembles for Structural Fire Fighting and Proximity Fire Fighting,4 and NFPA 1981, Standard on Open-Circuit Self-Contained Breathing Apparatus (SCBA) for Emergency Services,5 contain specific radiative and convective heat exposure testing criteria. NFPA 1971 follows a protocol for establishing a thermal protective performance (TPP) rating for turnout gear. NFPA 1971 establishes a TPP test method where turnout gear is evaluated at a constant heat flux of about 84 kW/m2 and the elapsed time for skin burns to develop is recorded. This analysis method allows for a relative comparison between firefighter turnout gear designs.
![]() |
Heat flux values (y-axis) vs. time (x-axis) for full-scale scoping test, burn 4. |
NFPA 1961 currently includes a single test that addresses thermal failure of an attack hoseline. The existing standard addresses heat transfer to the hoseline via conduction through a steel block heated to 500°F (260°C), which is placed on a nonpressurized hoseline for 60 seconds. After the block is removed, the hoseline is then hydrostatically pressurized to three times the service test pressure.6
According to the hose manufacturers, all hoselines tested (excluding the prototype models) met or exceeded the performance requirements of NFPA 1961; however, a substantial variation was observed. The 1¾-inch hoselines charged with water to 120 psi demonstrated failure times that ranged from 33 seconds to 106 seconds at the lower heat flux of 30 kW/m2. At 40 kW/m2, the failure times for water-charged hoselines varied from 22 seconds to 70 seconds. These thermal performance data are not available to the fire service, and the end-user firefighter has no relative data indicating how thermally robust the hoseline is.
![]() |
(6) The electric coil heater and platform used to stabilize hoseline in bench-scale laboratory testing. |
The relative “heat sink” effect of water in the hoseline also had varied results. In the bench-scale laboratory testing, it appeared that radiant heat degraded the exterior hoseline materials, causing rupture of the pressurized hoseline before the water inside the hoseline could absorb significant heat energy. Some hoselines experienced significantly greater times to failure (~50 seconds longer) in the bench-scale laboratory tests when charged with water, whereas others showed little, if any, greater thermal endurance.
In the first full-scale scoping test, the flowing water hoseline failed prior to the hoseline charged with water (static). In the fourth full-scale scoping test, the hoseline charged with water (static) failed prior to the flowing water hoseline. The limited “heat sink” effect of water inside the hoseline is consistent with the “Full-Scale Exposure Testing of Hoselines” performed by the National Institute of Standards and Technology (NIST).7 In the NIST testing, all three hoselines – charged with water (static), charged with air, and charged and flowing water – failed within several seconds of each other. More testing is required to understand the variables affecting these results.
![]() |
(7) Close-up of the resistance coil heater with hoseline placed horizontally one inch (25.4 mm) below. |
Despite each hoseline’s meeting the testing criteria outlined in NFPA 1961, the significant variation among the hoseline models tested support the need for a standardized radiant heat test to provide thermal performance data to the fire service. Similar to a TPP rating for turnout gear, these data would allow the end-user firefighter to better understand the limitations of the equipment and compare relative hoseline designs. A standardized radiant heat test could also be advantageous for hoseline manufacturers attempting to develop and compare more thermally robust hoseline designs.
In May 2016, a report containing the ATF testing protocol and data was presented to the NFPA 1961 technical committee. As a result, the technical committee voted to include new thermal performance test standards, including radiative and conductive testing, in future versions of NFPA 1961.
![]() |
(8) Bench-scale testing of pressurized hose (water) just after thermal failure. |
References
1. Notarianni, K & Ranellone, R. (2015). “Next Generation Fire Attack Hose.” (WPI Presentation to NFPA 1961 Technical Committee). Worcester, MA: Worcester Polytechnic Institute (WPI). Retrieved October 18, 2015 from http://www.nfpa.org/Assets/files/AboutTheCodes/1961/1961_A2017_FHS_AAA_FDmi nutes_10_15.pdf.
2. National Fire Protection Association (NFPA). NFPA 921, Guide for Fire and Explosion Investigations (2014 ed.).
3. National Fire Protection Association (NFPA). NFPA 1961, Standard on Fire Hose (2013 ed.).
4. National Fire Protection Association (NFPA). NFPA 1971, Standard on Protective Ensembles for Structural Fire Fighting and Proximity Fire Fighting (2013 ed.).
5. National Fire Protection Association (NFPA). NFPA 1981, Standard on Open-Circuit Self-Contained Breathing Apparatus (SCBA) for Emergency Services (2013 ed.).
6. FM Approvals LLC. Approval Standard for Fire Hose Assemblies and Fire Hose Couplings. Class Number 2111, 2131. October 2014, 14.
7. Madrzykowski, D. (2015). Full-scale Exposure Testing of Hoselines (NIST Presentation to NFPA 1961 Technical Committee). Gaithersburg, MD: National Institute of Standards and Technology. Retrieved on October 18, 2015 from http://www.nfpa.org/Assets/files/AboutTheCodes/1961/1961_A2017_FHS_AAA_FDmi nutes_10_15.pdf.
![]() |
(9) Hoselines were charged to a 120-psi (827 kPa) operating pressure for laboratory testing (both with air and water). |
LISA A. HERB is a special agent and certified fire investigator with the Bureau of Alcohol, Tobacco, Firearms and Explosives.
ADAM ST. JOHN, P.E., is a fire protection engineer with the Bureau of Alcohol, Tobacco, Firearms and Explosives.
![]() |
(10) Visible damage to hoseline after exposure to 40 kW/m2. This hoseline failed in 51 seconds. It performed the best out of the commercially available hoseline tested, demonstrated by the longest recorded elapsed times to failure when exposed to 40 kW/m2. |
FDNY Firefighter James Lee Jr. Recipient of the 2017 Ray Downey Courage and Valor Award
Manhattan Man Reunited with FDNY Firefighter in Rope Rescue
Fire Engineering Archives