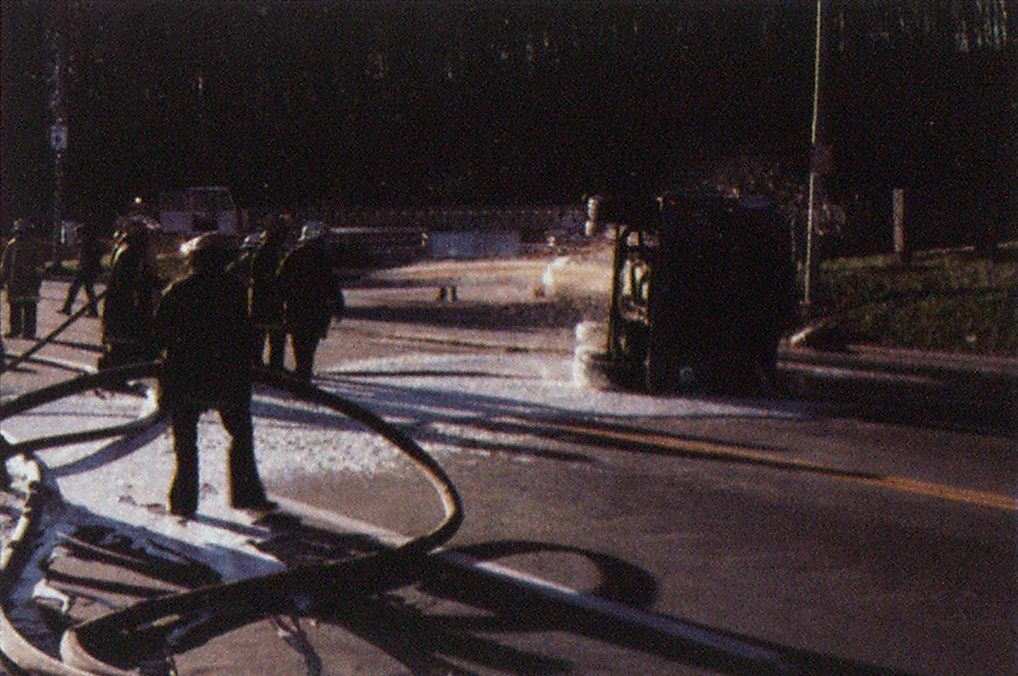
The Gasoline Tank Truck: Rollover Emergencies
HAZARDOUS MATERIALS

photo by Al Troo~
The second of two articles on the most common form of hazardous-materials transport.
Gasoline tank truck rollovers are one of the most challenging emergencies the fire service ever faces. They’re generally long-term (campaign) operations that are marked by the potential for fire and explosion. Frequently, the firefighting foam and the product transfer and uprighting equipment on hand are inadequate to handle the procedure. And although it’s usually the industry or contractor personnel who conduct the especially hazardous product transfer and uprighting operations, the fire service is still responsible for maintaining site safety throughout.
In most cases, an aluminumshell MC-306 tank truck involved in a rollover will be leaking. The size of the leak may vary from several gallons per minute to a complete failure of the tank. The incident is likely to present one of two situations: Product will be leaking from tank appliances and attachments, such as dome covers and piping; or the tank itself will have been breached and will be leaking. Depending on the severity of the rollover, this breach can range from splits and tears along weld seams to punctures and complete failure of the tank’s integrity.
The approach and placement of all emergency equipment is critical. Remember—most liquid hydrocarbon vapors are heavier than air. Firefighters must evaluate the terrain, wind, and environment in positioning personnel and equipment and in evacuating the public.
The incident commander must not only assess the current status of an incident, but also consider future contingencies. Anticipate rather than react. Primary response objectives should be directed toward isolating the area, controlling and confining the product, safely offloading the product, and finally, uprighting the overturned tanker. The incident shouldn’t be considered terminated until these steps have been accomplished, the truck has been removed from the scene, and all spill areas have been cleaned up.
The product removal and transfer operations can begin once the incident site is stabilized. With flammable liquids, stabilization means that all fires have been extinguished and ignition sources controlled, all spills have been contained, and the entire spill area has been foamed down and cleaned up as necessary.


The tank truck should first be surveyed to determine the safest method of offloading. Factors to evaluate include the pitch and position of the tanker, the product being transported, and resources and equipment available. The pitch and position of the tank truck—front to back and left to right—are particularly important. It’s possible that the overturned tank truck may move as product is pumped off and the product load shifts. If it appears unstable, the vehicle should be braced with timber, jacks, or air bags.
To control the generation and accumulation of static electrical charges, the tank truck must be grounded and bonded before product removal and transfer operations begin. Bonding is the process of connecting two or more conductive objects together by means of a conductor. Grounding is a specific form of bonding and is the process of connecting one or more conductive objects to the ground. The pump-off vehicle and all pump-off appliances—such as hose couplings, downspouts, and recovery pans and tubes—should all be bonded by connecting a bonding cable from the appliance to the overturned tank truck. Bonding cable clamps should be placed on a clean, grease-free surface.
The overturned tank truck must also be grounded. Grounding cables should initially be connected to the tank truck, then moved outward away from the vehicles. The final connection can be made to a guardrail post, telephone or electric pole support rod, or portable grounding rod, providing it’s deep enough to carry away the charge. Some industrial response teams will carry resistance meters to measure the effectiveness of grounding devices. Because soil conductivity conditions vary widely, response personnel should ascertain the local conditions during preplanning.
Six product removal methods are commonly used on MC-306 tank trucks:



(Photos by Gregg Noll)
- Removal via a drilled hole (Figure 1). This is the fastest and one of the safest methods of removing a flammable liquid, such as gasoline, from an aluminumshell MC-306 tank truck. Drilling should not be attempted on steel tank trucks. Advantages of drilling include its speed—each hole requires only one to two minutes to drill; its simplicity—it doesn’t require detailed knowledge of the tank truck valving systems; and the fact that there’s no additional product spilled.
- Removal via unloading lines (Figure 2). Product can be removed through the discharge lines if the tank is lying on its right side and the regular discharge lines are undamaged and facing downward. Remember, a bottom-loaded tanker will have product in the discharge lines which first must be drained into a grounded container before pump-off can be attempted.
- Removal via vapor recovery lines. If the rollover rail isn’t damaged and the vapor recovery system is accessible, product can be removed through the vapor recovery system. The pump-off hoses and equipment are connected to the vapor recovery outlet; when all connections are in place, the vapor vent is opened, allowing product to flow through the vapor recovery system. Product is then pumped off to the level of the vent. The remainder of the compartment can then be pumped out the vent opening, through the dome, or through the internal valve opening using a bonded downspout or suction hose.
- Removal via internal valve. If a tank truck is completely overturned, product can be recovered by removing the internal valve and pumping the gasoline out through the valve opening. On a bottom loaded tank, where the discharge lines and piping will be full of product, open up the internal safety valve to allow the product to drain back into the tank before you remove the coupler. Again, the vapor vent must be disconnected.
- Secure all nonessential personnel from the immediate hazard area. Ensure that all personnel wear full protective clothing, including self-contained breathing apparatus as needed.
- Position all vehicles in a safe location. No emergency vehicle should be less than 100 feet from the overturned tanker. If necessary, reposition vehicles. However, when vehicles are within the spill area and aren’t running, they shouldn’t be restarted for repositioning; leave them where they are.
- Continuously monitor the area with a combustible-gas indicator. Readings higher than 20% of the lower explosive limit indicate an immediate fire or explosion hazard, and operations should be suspended until readings are reduced below 20%. Monitor at the ground surface, in low areas, and downwind of the incident especially well.
- Control all ignition sources, including flares, smoking, and vehicles operating in the area.
- Apply foam to all spill areas and reapply the foam blanket as necessary.
- Determine if product containment and confinement operations are necessary. Use dome clamps to control dome cover leaks. Always plan for and evaluate the worst-case scenario.
- Ensure that backup crews and a minimum of 1 ½-inch foam handlines are in place to protect personnel engaged in offloading and uprighting operations.
- Always have an escape signal and path for personnel working in the immediate hazard area. All personnel should be instructed in the procedures for an organized and immediate escape.
- Ensure that all personnel remain alert. Firefighters and industry personnel sometimes become sloppy and less attentive as rollover emergencies extend over several hours, and they may attempt shortcuts.
- Removal via dome cover knockout plug (Figure 3, page 39). A knockout plug with a threaded connection approximately 1½ inches in diameter is installed as part of the dome cover assembly. When involved in a rollover, an offloading pipe and valve are attached to the threaded connection. By attaching an offloading hose to the valve, a compartment can be pumped off to the dome cover level.
- Removal via dome cover and a funnel (Figure 4, page 39). Entry into a tank compartment can be made through an aluminum or neoprene funnel placed over the dome cover. The funnel cover and assembly are placed over the dome cover hatch and clamped down. The pump-off hose is then attached to the funnel assembly, the dome cover is opened, and the product is pumped out. Once the product level falls below the dome cover, a bonded pump-out tube must be used to recover the rest of the product.
- If the tank truck was bottomloaded and isn’t yet unloaded, the discharge piping will contain up to 40 gallons of product.
- Don’t assume that a compartment is completely drained down when opening a dome cover. It’s possible that the compartment bulkheads have broken, allowing product to flow between compartments. When dealing with a rollover, always consider the tank as one single compartment.
- Remember that the vapor recovery vents on top of the tank truck will open when the internal safety valves are opened. Always “block off” or disconnect the vents before opening the internal safety valves, or product will escape from the vents or vapor recovery piping.
- Ensure that any product remaining in the transfer lines is collected. Once the product recovery and transfer operation is completed, a certain amount of product will remain in the transfer lines. This can be drained into a container and added to the previously transferred product, or collected into another container for separate handling. In no case should the material be drained onto the ground.
A hole is made in the aluminum shell with a three-inch hole saw using an air-powered or waterpowered drill. Extensive testing has shown that even under the worst conditions, with an extremely dull hole saw and no water application, aluminum-tank shell temperatures never approach the ignition temperature of gasoline. The application of water and a sharp hole saw will extend this safety margin.
Each compartment requires a separate hole. The hole should be drilled in line with a dome cover to avoid drilling into compartment baffles [see “The Gasoline Tank Truck: Design and Construction,” Fire Engineering, June 1987].
Once the holes are drilled, a bonded pump-off tube is inserted into the drilled hole. After the product is removed, a tapered, wooden plug is driven into the hole. The aluminum disk from the sawing operation is saved to be welded back onto the tank if the tank is to be put back into service.
A 90-degree quick coupler with a pump-off hose is attached to the discharge outlet. The tank’s internal safety valve must be opened to allow product to flow from the tank compartment. To prevent product from entering the vapor recovery system or spilling out the vent opening, the vapor vent must be blocked off or closed before flowing any product.
If the vapor recovery system or the rollover rail is damaged in any way, the vapor recovery system can’t be used. It can be checked for leaks by connecting a vacuum truck to the vapor recovery outlet. If the system holds 10 inches of vacuum for one minute, it’s intact and can be used for product recovery.
Site Safety Checklist
If a tank truck is lying on its side, product can still be removed via the internal safty valve, providing the product level has been pumped down to or below the level of the valve. The discharge lines, whether facing upward or downward, contain product and must first be drained. After product transfer, the internal safety valve must be reinstalled before the tank is uprighted.
Knockout plugs are a relatively new method of product removal, and actual experience with this method is limited. In addition, very few of the major petroleum companies have the knockout plug design installed as part of the dome cover assembly.
This is the least desirable method because of the difficulty in maintaining a tight seal around the dome cover. In addition, should the funnel assembly slip off the dome cover, there’s no way to stop the flow of product.
Depending on the position of the vehicle, these six methods can be used individually or in combination. But several safety concerns must always be stressed:
Product transfer
Once a product removal method has been selected, there are many ways to transfer the product. These include vacuum trucks, vehicles with power take-off pumps, and portable pumps driven by air or water. Gasoline, diesel, and explosion-proof electric pumps should be used only if others aren’t available and only with proper safety precautions. Although transfer equipment availability will be a contributing factor in the type of equipment used, safety must be the primary consideration.
Vacuum trucks are the most common medium of product transfer. They’re an economical, efficient, and expeditious tool for recovering flammable and combustible liquid spills. However, the vacuum truck isn’t inherently safe, because the vacuum pump exhaust can saturate the surrounding air with flammable vapors. To minimize the fire potential, take the following physical and mechanical precautions:

(Photos by Gregg Noll)

- Connect an exhaust hose to the exhaust of the vacuum pump so you can vent the vapors to another area, taking into consideration related factors such as wind direction and velocity, terrain, and adjacent buildings and exposures.
- Take continuous combustiblegas-indicator measurements in the area surrounding the transfer operation to ensure that mixtures of vapor and air are kept at a safe level (below 20% of the lower explosive limit).
- Don’t use a sewage vacuum truck to recover hazardous substances, particularly flammables.
- Cables and lifting straps. Cables will crush the tank shell and damage it further, so in many instances, nylon lifting straps will be used. Straps should be placed so that the weight of the tank will be evenly distributed. The strongest points will be at the fifth wheel and the trailer’s tandem wheels, as well as at the tank baffles and compartment bulkheads. If straps are positioned between compartment bulkheads, the tank shell may be easily crunched.
- Air cushions (Figures 5 and 6, page 44). Air cushions, or air bags, offer a gentle and controlled method of uprighting. When used as a system with cables and lifting straps, they can lift an 80,000pound tractor trailer while minimizing the potential for fire and explosion. Wreckers with lifting straps should be used to slip uninflated air bags under the vehicle, anchor the tank truck during lifting, assist in controlling the lift, and serve as a safety backup to the air bags.
Adequate venting must always be provided during transfer operations. When it’s not, a vacuum will be created and the tank may collapse. Likewise, when venting is initiated on a tight container, leaks may appear at previously “sealed” locations and increase the product flow.
Uprighting
Uprighting operations are generally the responsibility of the carrier. In most instances, the carrier will contract with a towing or wrecker service company that specializes in these operations. Again, to ensure site safety, the fire department must know the capabilities and limitations of the wrecker service.
Serious spill situations have been created by uprighting a loaded tank truck prematurely or attempting to tow a loaded tank truck with inadequate equipment. An aluminum-shell MC-306 tank truck should never be uprighted while loaded, because the container isn’t built to withstand that type of stress.
For uprighting emptied tank trucks, two methods exist. Both of these procedures accommodate for the fact that there’s no suitable place on the tank itself for the attachment of hooks, because the only lifting points are on the chassis.
Mobile cranes, tow trucks, or wreckers are required for uprighting operations. Mobile cranes are the best, but they’re often hard to obtain. In most cases, you’ll need two and sometimes three wreckers.
Tractor-trailer combinations should be uprighted as one unit; separating the tractor from the trailer could contribute to instability. If the tractor has become separated from the trailer during the rollover, it might be necessary to use a fifth-wheel dolly to support the trailer duiing uprighting. Recognize that the unit may slide during uprighting until the tires dig in and provide resistance.
Once the vehicle is uprighted, it must be removed from the scene. Often it can be towed away. But if it’s badly damaged, it can be placed on a flat-bed trailer, or “low boy,” and transported.
Gasoline is the most common hazardous material transported in the United States. Despite the petroleum industry’s excellent safety record, accidents do occur, so it’s essential that the fire service be well trained in handling gasoline tank truck emergencies.