Training Notebook ❘ By Adam Haywood
Rotary saws have earned their place on fire apparatus across the nation since having been adopted by the fire service more than 50 years ago, and rightfully so. Capable of cutting metal, wood, masonry, Lexan™, and countless other materials, rotary saws help firefighters gain access, ventilate, extricate, and more. In today’s modern fire service, there is a wide array of saws, manufacturers, and blades available to choose from. But what blade and saw combination is right for you and your mission? Let’s break down the current classes of blades available, their strengths and weaknesses, and then explore what powerhead is best suited to each blade type and why.
Considerations for New Battery-Powered Cutoff Saws
Blade Classes
Abrasive blades are arguably the most accessible class of blade. They are extremely affordable and readily available at any local hardware store. Today’s abrasive blade offerings are typically manufactured with a resin-bonded matrix of silicon-carbide or aluminum-oxide and come in two variants, one designed for cutting metal and the other for cutting masonry.
This class of blade is also the fastest metal-cutting blade offering on the market, which makes it a good choice for saws dedicated to forcible entry. However, the trademark speed of abrasive blades is hampered by several drawbacks. For one, abrasive blades are fragile and prone to catastrophic fragmentation if torsional stress is applied to them during a cut. The blade must remain as close to perpendicular to the material being cut as possible. This will alleviate any stress that’s applied to the blade.
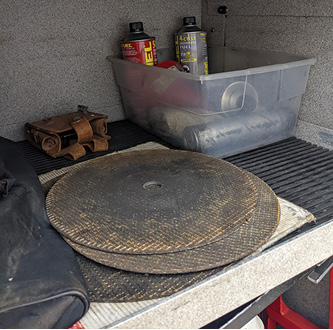
1. These abrasive blades are not stored properly. Note the wear caused by friction from unprotected, horizontal storage. Also, fuel containers are stored in the same compartment, which is not recommended. (Photos by author.)
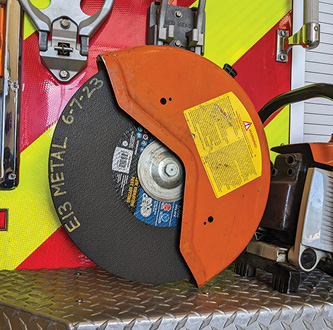
2. An abrasive blade, marked with a paint pen. The notes indicate unit designator, blade type, and in-service date.
Furthermore, abrasive blades are susceptible to degradation from both friction in storage and fuel vapors from nearby fuel containers. Whenever possible, store your extra abrasive blades vertically. This prevents friction from destroying the blades as the apparatus travels down the street. It’s also a good idea to avoid storing any fuel in the same compartment as the blades, as the off-gassing fuel vapors can degrade the adhesives in the blade (photo 1).
It’s important to keep in mind that abrasive blades are consumed very quickly in comparison to diamond and carbide blades. It isn’t uncommon to have to replace a blade after only a short period of use. One helpful tip: Mark your abrasive blades with a paint pen. Mark the blade in 1-inch-high letters to denote the blade type (metal or masonry), unit designator, and date of in-service (photo 2).
Marking your blades serves two purposes. First, it makes the blades easily identifiable so you can select the appropriate blade for the operation. Some departments will even paint the entire blade for ease of recognition. Second, it gives you a good reference point for when to replace the blade. Once the blade has lost approximately 2 inches of its diameter, the 1-inch letters will be completely gone, indicating that it’s time to replace the blade.
Considering the low cost of abrasive blades, fire departments should always strive to have extras on hand. This will enable them to change a blade out quickly, which may be needed while operations are still ongoing. And having a cache of extra blades allows you to put a new one on after a blade is used so your equipment is fully prepared for the next incident. Any used blade can now be utilized for training until its life span is completely depleted.
Abrasives, while affordable and fast-cutting, require extra attention by the saw operator, get consumed at a greater rate, are limited by their single purpose (metal or masonry), and have greater demands for proper transport and storage.
Diamond blades truly have become the industry standard in the past decade or two—and rightfully so. These blades are typically manufactured in one of two ways: They’re either made from a steel core with welded-on cutting segments or from one solid steel core with laser-cut segments, the latter being the preferred, more durable method of construction (photo 3).
Synthetic diamonds are then either sintered or brazed to these segments. Designed to cut metal, masonry, Lexan, wood, drywall, tile, and more, modern-day fire-service diamond blades are really a “one blade fits all” kind of solution. Despite the diamond blade’s claim to cutting such a range of materials, it can struggle with wood and roofing media because it performs its cuts by grinding through the material rather than chipping away at it like a carbide blade would.
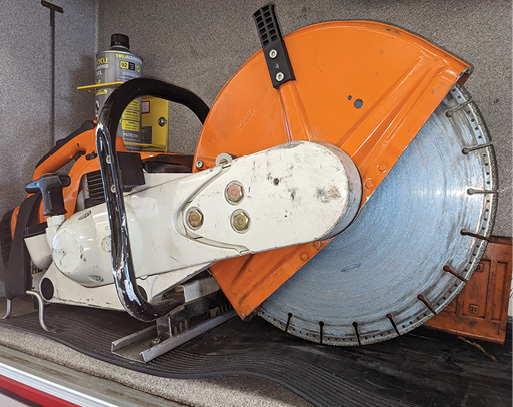
3. A diamond blade.
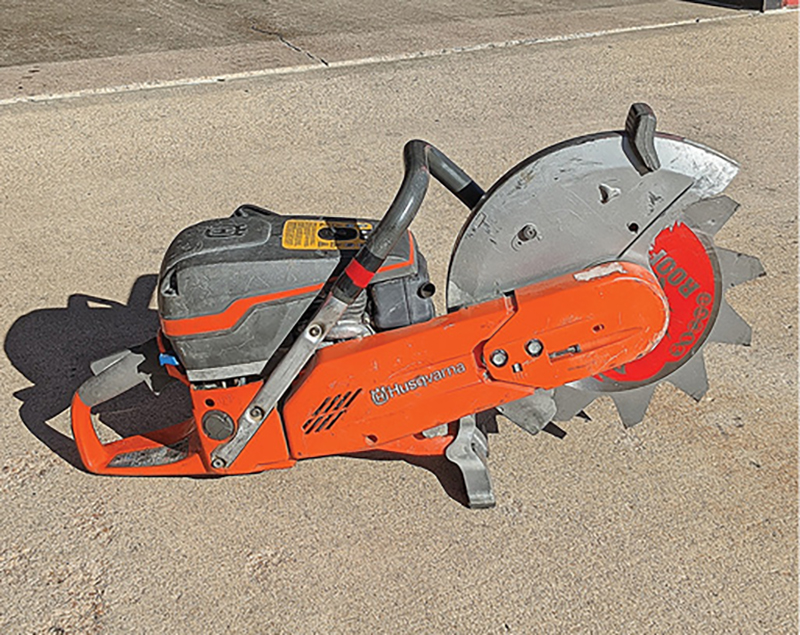
4. A carbide blade, designed for ventilation duties. Notice the unidirectional design.
While these blades are best suited for metals, Lexan, masonry, and other materials you may encounter when forcing entry into a structure, they may also take longer to cut obstacles like hockey puck locks in comparison to the abrasive blade. Today’s modern diamond blades are extremely resilient and durable. They don’t require the same level of delicate care and storage that abrasive blades need.
Diamond blades are, however, still consumable blades, and the exposed diamond is prone to wearing away after heavy, repeated use. If you find your diamond blade is not cutting well, or at all, inspect the segments for any glazing. If glazing is present on the segments, “redress” the blade by running it through an abrasive material such as asphalt or concrete to expose fresh diamonds for cutting. Having a concrete block or brick in quarters helps dress the blade as needed during daily saw inspections.
Diamond blades offer a good middle ground in terms of application. They can perform both forcible entry duty and some limited ventilation duty as well.
Carbide blades round out the field and are the most aggressive blade of the three. These blades are made from a steel core with carbide tips welded to the “teeth.” They are available in a variety of tooth-counts and have a unidirectional design, meaning they can only be operated in one direction (photo 4).
Most carbide blades are stamped with an arrow, which indicates the direction in which to install them. Carbide blades are made to cut wood, drywall, roofing materials, and fiberglass and—in a pinch—can cut thin sheet metal. These blades are best suited for a dedicated vent saw paired with another rotary saw, set up for dedicated forcible entry duty with either an abrasive or a diamond blade.
Note: Not all saw manufacturers approve the use of carbide blades on their rotary saws. Check with your saw manufacturer to see which blades are approved for use. Carbide blades, while immensely stout, still have weak points—most notably, the carbide segments can become dislodged during operation and become projectiles. And, while it’s a rare occurrence, errant carbide segments can come off a working blade and pierce through the bunker gear of nearby firefighters. To avoid being hit by debris or a dislodged tooth, firefighters operating behind the saw must remain vigilant and not stand directly behind the discharge port.
In addition to the traditional toothed design, you’ll find two other variants of carbide blades on the market: the “chunk” blade and the “bullet” blade. A “chunk” blade is a round steel core with “chunks” of carbide welded to it (photo 5) that act as the teeth. In contrast, a “bullet” blade is a round steel core wrapped instead with a length of carbide-tipped chainsaw chain.
Both variations can also cut thin sheet metal but should not cut any metal that’s thicker or more substantial. Hyperaggressive in design and nature, and purpose built to chew through common construction materials, a carbide blade is the definitive choice for a rotary saw dedicated to ventilation duties.
Choosing Your Saw
Once you decide which blade is best for how you intend to use the saw (forcible entry, all-around, or ventilation), you also need to consider which model of saw you’ll mate it to and in what configuration. We can think of the current offerings on the saw market as falling into one of three categories: lightweight, middleweight, and heavyweight.
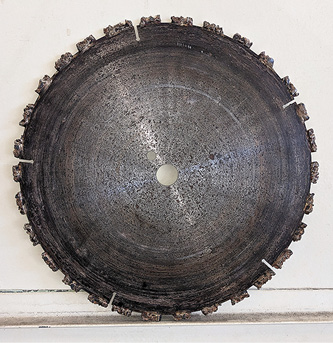
5. An example of a carbide “chunk” blade.
Lightweight saws have an engine size of 65cc to 75cc. Due to their smaller engine displacement, they work best with lighter blades, such as abrasives and diamonds. Consider saws in this class for dedicated forcible entry duty, as they are lighter and easy to use for tasks like cutting overhead doors but lack the power to run the appropriate blade for ventilation work.
Middleweight saws, which have engine sizes of 90cc to 100cc, are the most popular saw class and make an excellent choice for most blades and tasks. Capable of running abrasives, diamonds, and most carbides effectively, middleweight saws can handle forcible entry, ventilation, or a combination of the two.
Heavyweight saws include any saw with an engine larger than 115cc. They can do anything the other saws can do, but they excel in running carbide “chunk” blades and any carbide vent blades with exceptionally wide teeth. Their high-power output can spin the heavy “chunk” blades with ease and help wide-profile carbide blades cut through heavy built-up roofs.
Whichever blade you choose, always confirm that it is compatible with your saw’s rpm rating. One final note: Regardless of engine size, almost all saws on the market come equipped with water suppression systems for dust mitigation when cutting masonry with either an abrasive or a diamond blade. If you are unable to use the supplied suppression system, a pressurized water can that’s directed at the cut can reduce the dust produced and help the operator view the blade and cut.
Configuring the Saw
Another important consideration: How will you configure your saw? Should it be inboard or outboard mounted?
An inboard-mounted saw will have the blade mounted inboard of the cutting arm, more in line with the center of the saw. This is the standard factory setup for all rotary saws. Since the spinning blade is closer to the centerline of the saw, an inboard-mounted saw will be more gyroscopically stable than an outboard. Consider keeping your saw inboard if you plan on running a dedicated vent saw, as the saw will be easier to control on a roof and through a running cut.
Conversely, an outboard-mounted saw will have the blade mounted on the opposite side of the cutting arm. This outboard design offers a much greater angle of attack for flusher cuts because no part of the saw’s body meets the ground or cutting material. This is also the preferred choice for a saw dedicated to forcible entry. However, with the blade now spinning farther from the midline of the saw, an outboard-mounted saw will be less stable. As a result, it can be harder to control, making it a poor configuration for a dedicated vent saw fitted with a carbide blade. Virtually all saw manufacturers approve of converting their respective models to outboard. They outline how to do so with simple hand tools in their owner’s manuals (photo 6).
Blade Selection
It is important to consider how blade selection affects the new generation of battery-powered saws. While abrasive, diamond, and carbide blades will all maintain their same characteristics when mounted on these saws, there are some other factors to consider. The smaller 9-inch-battery saws run at a much higher blade speed, so confirm your blade of choice is rated appropriately for higher speeds. The larger 14-inch-battery saws run at the same speed as their gas-powered equivalents. And, keep in mind that no current battery saw models—9-inch or 14-inch models—are available to be outboard mounted.
Rotary saws remain a vital tool in the ever-expanding toolbox of the modern fire service. Ensure you are getting the most out of your saw. Be sure you select the correct blade for how you’re going to use the saw and match it appropriately with the proper powerhead.
ADAM HAYWOOD began his fire service career in 2010 and currently is on Engine 12 of Adams County Fire Rescue in the Denver-Metro (CO) area. He has served as both an instructor and subject matter expert in career and volunteer academies around Colorado, serves in his department’s training division, and has delivered various classes throughout the country as the owner of Independent Fire Training.