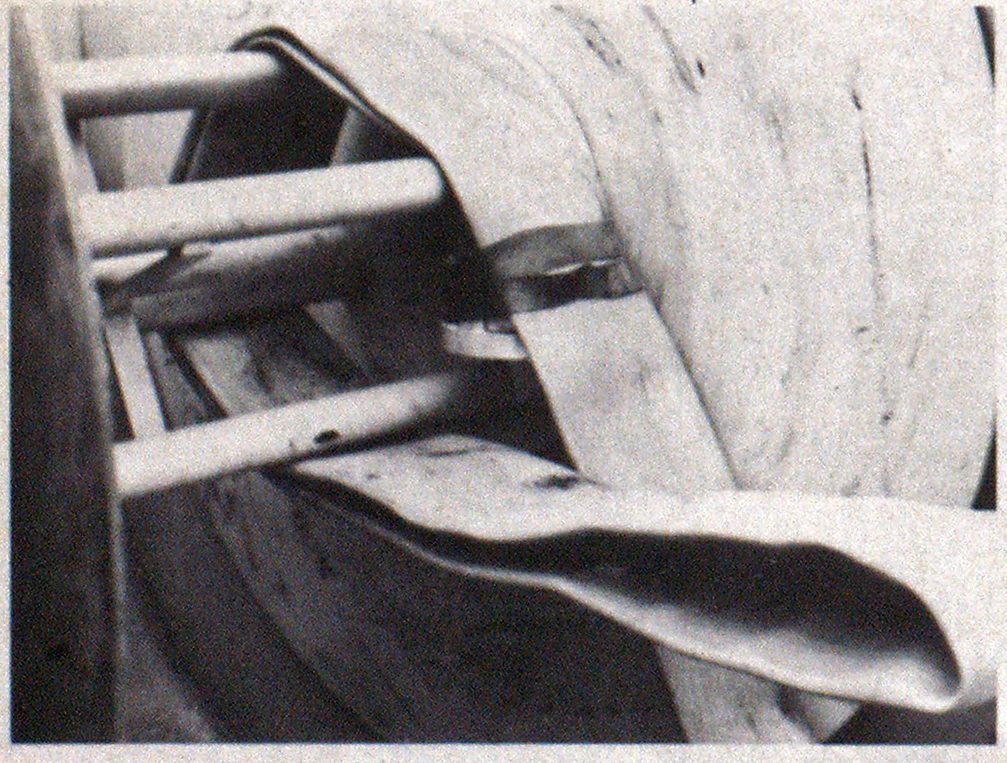
Hose Reel for Large-Diameter Hose Allows Fast Reloading in the Field
features
When the Laconia, N.H., Fire Department purchased its first 4-inch lightweight hose in 1969, we were not satisfied with the standard hose bed load. Each length of hose had to be broken, drained and rolled before picking up. It was then transported back to the station, put on a hose table and packed back aboard. We wanted to be able to do this in the field, but couldn’t because air and water entrapment prevented it.
We arranged a visit to a department using powered reels to store the hose. It didn’t take more than one look to convince us that the reel method was the answer. It allowed pickup in the field and squeezed the air and water out of the hose as it wound around the reel. The powering system used to turn the reel was a PTO drive with a slip disk clutch arrangement.
After returning home, the decision was made to draw up specifications for our own reel vehicle and have it built. The telephone company was using hydraulic power to turn the reels on their truck. After observing the variable speed that was possible with this system, we chose it over the PTO drive.
Learned a lot
When our reel vehicle was completed and delivered, we went to work on developing a SOP for its use. We probably made as many mistakes as was possible, but we learned a lot in the process.
Apparatus can be installed with a single reel or twin reels. The independently operated twin reels can be positioned side by side or with one forward of the other. In the latter case, the rear reel should be laid out first so that the hose on the forward reel can then pass freely over the empty drum of the rear reel. A solid drum is preferred on the rear reel in this type installation to prevent couplings catching on an open spool. The axle of the forward reel should be slightly higher than the rear one. In loading hose, the forward reel should be filled first.
Regardless of which installation is employed, the hose must always come off the top of the reel.
Operating systems
After using other powering systems, I have to recommend hydraulic systems above all others. Probably its greatest feature is the ability to vary the speed of the reel in loading. When starting, the hub is small and must turn at a faster speed than it does as it fills. It is easier and much safer to vary the reel speed than to speed up and slow down the backing vehicle. A three-position, four-way control valve with motoring spool and spring return to neutral is recommended. The valve must have good feathering action, and pressurecompensated flow control is desirable.
Some departments use a power takeoff drive with slip clutch and are quite satisfied with it. It employs a directdriven clutch on the side of the reel that is tightened to get the proper power.
This does not have the speed varying feature of the hydraulic. A foot-actuated brake is recommended to stop the reel if necessary.
The main advantage of an electric reel is lower price. Again you are restricted to one speed, and I would recommend a small reel, up to 500 feet of hose. A clutch is required and there are two types available.
A centrifugal clutch is automatic and allows the reel to be disengaged from the motor during layout. It prevents the rapidly turning reel from driving the motor faster than it was designed to spin. When loading the reel, the motor spins the clutch closed.
A manual clutch has a push-pull mechanical device that, when open, protects the motor during layout. When loading the reel, the clutch must be closed by hand. I recommend this type because sometimes you want to power hose off. This can’t be done with the centrifugal system.
Loading the reel
Before starting to load the reel with hose, fold back about 8 feet and slide a band of innertube over the hose to secure the coupling and hose. Wrap the flap section around the reel hub and lock the end under itself. During layout, this allows the coupling to be off the reel before the end comes lose. Then the weight of the coupling won’t slam into the body of the vehicle and fly into the air, damaging itself.
The loading operation is essentially the same for all types of reels. It is to your advantage to have a planned and practiced rewind procedure in order to assure maximum reel capacity, safety and ease of operation.




A tight rewind is important to reduce “sag” on the reel. A loosely wound hose will not support the weight of the couplings and may interfere with the operation or even prevent the reel from turning on layout.
Recommended method
Backing the truck for loading is the only method I recommend. It allows for proper tension and tight loads while removing all air and water.
Another method which has been used is driving over the hose—straddling it between the wheels. This is entirely unsatisfactory. In no way can you load your reel and keep the proper tension to squeeze the air and water out of the hose.
The reel control person is the loading team’s leader. He runs the reel control and his task is to watch the hose behind the reel as it comes off the road. In controlling the speed of the reel, he must keep the hose as tight as possible, but not so tight that the other man guiding the hose onto the reel can’t steer it. The hose should have a gentle slope from the reel hub back to where it leaves the road. Another thing he will have to do is to keep the operator of the vehicle aware of the speed of the truck in relationship to how the hose load is progressing. He must tell the other man who is guiding the hose onto the reel when a coupling is coming. A typical conversation would be: “You have a coupling coming about 30 feet back, 20,10,5, you got it.” The reason for this is that it allows the other man time to get that coupling into a depression in the load he has planned for. It also warns him that he has to move his elbow out of the way so that the coupling will not hit it.
The man guiding hose evenly onto the reel never looks back at the road. He doesn’t have to if the control person is talking to him as he should. The guide’s job is to load the hose in as even a way as he can. When a coupling comes aboard, he immediately steers away from covering it and builds up the load in other areas. If the tightness of the hose does not allow him to steer it properly, he tells the reel controller to slack off a bit. But care should be taken to keep the hose load as tight as possible. A loose load will sag overnight and drag on the bottom of the reel bed, causing problems when laying out the next time.
The best advice I can give is to practice, the more the better. A good working arrangement will develop from working together.
The driver of the vehicle must be able to properly back up using both rear view mirrors. Initial use and practice should be done during daylight because working with lights is much more difficult. He will have to learn to work as part of the loading team. He will start, stop, speed up, and slow down as directed by the reel control person.
One or two people walking behind the vehicle during loading helps to speed things up. Their job would be to break couplings and clean the hose if necessary. Sometimes they can straighten the hose or round out corners so that the water can drain properly.
Always load hose downhill so water will drain. When approaching a depression, have a hose handler break a coupling at the low point. If the lay was made down a long slope and up again, pick up to the low point and start again at the top on the other side.
Laying out
Reel control must be in free-wheel for laying out hose.
Use of so-called hydrant rope is recommended for securing the hose end. This rope should be attached so that about 10 feet of hose will be ahead of the hitch. Short make-up lengths should be carried in case an end does not reach the outlet or hydrant.
Rope must be looped around a stationary object (such as a tree, telephone pole, hydrant or another fire engine. Never try to hold hose manually, either by hand or by standing on it.
Truck layout speed should be governed by operating in first gear only (automatic or manual transmissions) and up to 20 mph, as traffic or conditions allow.
With practice and coordinated action, the driver will be able to unwind and lay the hose and couplings very gently onto the road surface, whether straight or around curves or corners. Curves and corners require slightly increased speed. The reel speed is built up and the resulting momentum lays the hose around the curve or corner. Allowing the reel to gain relative speed will prevent the hose being pulled around the corner. Care should also be taken to avoid stretching the hose around poles or trees (which would greatly restrict the water flow).
A gradual slowing of the vehicle when coming to a stop will prevent reel overriding. Time spent in practice and developing technique will result in faster, safer operation.
Safety
For safety purposes, an intercom is essential for any vehicle equipped with a reel system. For a side-by-side twin reel setup where more than one reel could be used simultaneously, there should be a speaker on both sides of the rear step.
For night operation, the rear of the vehicle should have two lights to illuminate the rear step area, one on each side, and four hose loading lights on top (six if two reels, one ahead of the other), the rearmost two lights to be directed on the road behind the vehicle.
A fold-down rear step will allow double the working space while loading and not increase the angle of departure.
Never allow anyone to ride anywhere on the rear of the vehicle when laying out hose.