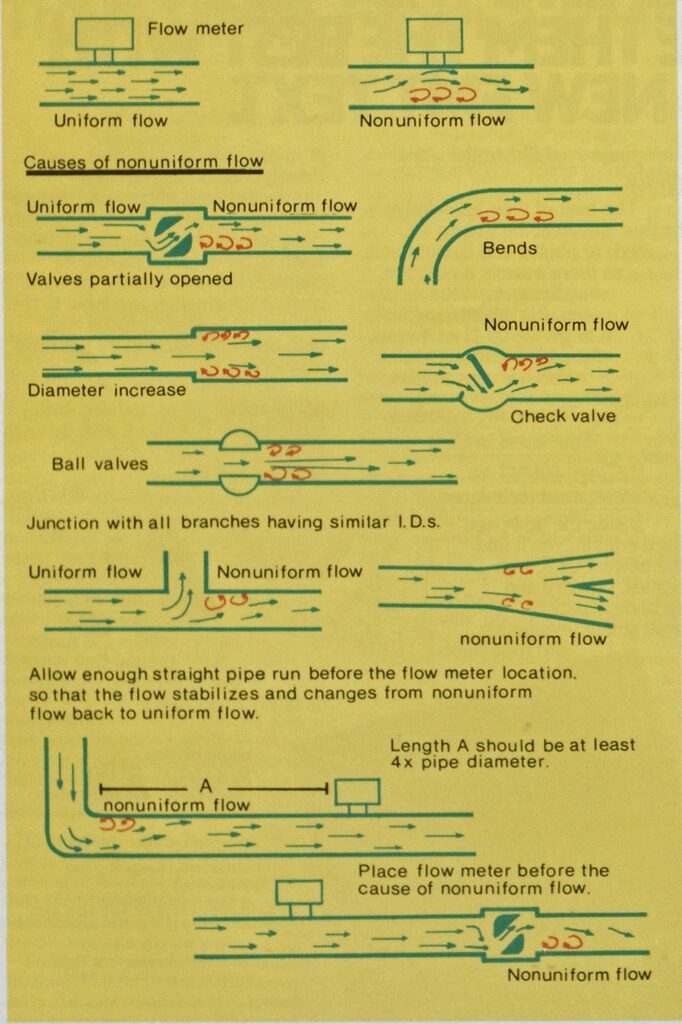
Flow Meter Readings More Useful Than Those From a Pressure Gage
features
If all hose lines delivering water for fire fighting were kept short, level, unbranched and within sight of the pump operator, flow meters might not have been adapted for the fire service. Instead, pressure gages would still be sufficient.
And if fireground hydraulics calculations weren’t so complicated, or if rule-of-thumb estimates were sufficient, then there would also be less need for flow meters.
But realistic fireground conditions have made flow meters especially important. Unlike pressure gages, flow meters measure actual flow of water in gallons per minute, which is the same at the pumper and at the nozzle (unless there is a break in the hose) no matter where the nozzle is taken.
Fire department personnel at both ends of a hose line have a stake in the actual flow, and thus in having it measured. It’s the pump operator’s job to deliver the necessary flow, not just to pump at a designated pressure. That leaves too much room for error. At the nozzle, any fire fighter who has held a limp hose before a raging fire or who has been thrown around by an overcharged line knows the value of proper flow.
Easiest way
The easiest way to deliver a proper flow is to watch a flow meter while increasing or decreasing the pump throttle. A pressure gage alone cannot clearly and instantly indicate that desired flow.
Today’s pumpers, however, feature a predominance of pressure gages, previously the best available way to determine an amount of flow. The problem is that a flow indicated only by a steady pump pressure is not always reliable. Gravity and friction can greatly affect how much water actually leaves the nozzle. The same pressure pumped on a long hose line or an elevated hose line delivers different amounts of water at the nozzle than on a short, level line. The nature of that difference is, of course, important in fighting fire.
Forget the formulas
Without flow meters, mathematical calculations, including friction loss formulas, must be used to adjust pressure readings to reflect flow. Whole books have been written on the details of fireground hydraulics. Pump operators mastered such hydraulic manipulation because they had to, just as fire fighters had to carry the extra weight of SCBA for safety reason. In both cases, it is best not to bother with extra work if there is a better way; that is, if lighter SCBA can be manufactured or actual flow can be determined.
Enter the earlier flow meters for fire apparatus, a number of years ago.
In addition to indicating the flow at the end of a complicated hose layout, the flow meter could save time when things went wrong. After a kink occurred out of sight of both the attacking crew and pump operator, for example, the officer would previously notice his poor stream and radio for more pressure. With only a pressure gage, the operator would assume his estimate of flow was off and take the time to increase pressure. Eventually, the officer would realize that flow was not increasing and would have to investigate his line. With a flow meter, when the flow rate did not increase with an increased pump pressure, the operator would see and stop increasing pressure immediately and notify the officer of a kink.
In a burst-hose situation without flow meters, the officer would radio for more water and the operator would again increase pressure as a first response. But if a flow meter showed good flow, the officer would get that information quickly and know his line had burst, since the flow was going somewhere.
In a similar way, flow meters would keep the pump operator better informed when pumping into a sprinkler or standpipe system. He would immediately be aware of a sprinkler system problem if no flow was registering but it was known that heads had opened.
“When supplying a sprinkler system,” WNYF magazine has reported, “a rough estimate of the number of heads that are open can be rapidly determined by dividing the total water flow by 20 gpm.”
The list of flow meter advantages is long.
Source of frustration
Then it was discovered that not all the early flow meters performed equally well in all environments. This fact caused much frustration in the fire service and some resistance even today to the idea of flow meters.
Like so much of the equipment used in the fire service, the original flow meters were adapted from industrial uses, such as measuring the precise flow of chemicals in manufacturing processes. Flowing water would seem to be as easy to measure as flowing alcohol, for example, but not necessarily. The alcohol and other chemicals used in manufacturing are typically pure or filtered and stored in stainless steel tanks. In fire service use, water from an old main may contain sediment or debris such as rust scale, especially at a rapid flow. Also, industrial flow meters were kept in one location, not carried over rough roads on a vehicle.
The result: Some of those earlier flow meters became clogged.
This condition seems less a problem today due to significant design changes. The New York Fire Department has almost 200 flow meters in service with a new design and has not found reason to complain about the devices.
N.Y. tests
“We had heard reports of flow meter unreliability,” said Chief Anthony J. Romagnoli, head of the FDNY repairs and transportation unit, “but we also knew flow meters were a good idea. So we tested three different types in a pilot program for over a year in each of the five boroughs. The captains at the selected stations also went in for specialized training. The result, as far as my involvement is concerned, has been very little problem with maintenance on the type of sensor that was selected for continued use. Some recalibration, some broken faces on the dials. But not clogging.”
Deputy Chief Bob Peterson of the Union Fire Company in Carlisle, Pa., was especially concerned about clogging. “Our water has a high calcium content because of extensive limestone deposits in the area. We were afraid of buildup, but there hasn’t been any on our flow meters.”
Peterson doesn’t believe that reliability is the main factor in the stilllimited use of flow meters. Instead, he sees two reasons why flow meters haven’t become standard equipment. It’s because of “tradition, mostly—the traditional reliance on pressure gages combined with lack of knowledge about flow meters. The other reason might be initial cost, although they are only in the $300 range.”
Installation Considerations
The flow must be fairly uniform at the point where the flow meter is installed. Otherwise an incorrect reading will result.

Resistance to flow meters comes not only from within some fire departments, but also from some in manufacturing, it seems.
“We included flow meters in our specifications for a new pumper,” explained Chief Doug Forsman of the Champaign, Ill., Fire Department. “Eight bids were received for the apparatus but all eight bidders excluded the flow meters. I got the idea there had been some maintenance problems and the bidders wanted to avoid a potential problem. But I believe in flow meters.”
Bob Barraclough wonders if some of those bidders were in fact not well informed about flow meters and used the unspecified “problems” as an excuse. As vice president of marketing at Hale Pump, Barraclough knows something about pumping water—and about flow meters.
“I think flow meters are very important to the fire service,” he said. “It’s the only logical way a pump operator can tell how much water is flowing with different hose and automatic nozzles.”
With automatic nozzles
Those automatic nozzles already are an asset to fire fighters, Barraclough explained. However, only when used in conjunction with flow meters do automatic nozzles maintain the highest efficiency.
Fort Worth Fire Chief C. H. McMillen has written similar comments, calling the advantage of using automatic nozzles with flow meters “particularly great.”
“You don’t even have to teach friction loss,” McMillan said. “It is significantly easier to dial a specific gpm for each line than to figure out which line works at what pressure and correlate that to gpm…Hopefully, manufacturers will continue to improve flow meters until they are satisfactory for our service demands.”
Three main types
Three main types of flow meters may be found on fire apparatus: including those with differential, turbine and paddlewheel sensors.
The differential type consists of two tubes with small holes placed in line in the flow. One tube faces into the flow, another away from it. Each measures pressure, but the differential in the two pressures recognizes a flow which can be translated into actual gpm. But it’s the small holes, according to some users, that are subject to clogging in fire service use.
Dieterich Standard, manufacturer of Eagle Eye flow meters, has improved its design of differential sensors, according to a spokesman, but no longer markets them for mobile fire apparatus. The spokesman added that his company had no plans to reenter this market.
Turbine sensors are used successfully in the hard-use farm industry, but the fire service demands for high-volume streams apparently limit their use.
The turbine propeller axis is in the middle of the flow, where it’s good for accuracy but causes a pressure drop. Clogging is a possibility, as is greater damage if a larger piece of debris hits the turbine. This type is necessarily a bulky unit, usually with a mechanical transmission making it more difficult to separate the metering point from the gage. No manufacturer is known to be advertising this type nationally for the fire service.
In a paddlewheel flow meter, most recently adapted to fire apparatus and the type used by New York, the axis is horizontal and completely out of the flow. Only a small portion of the paddles extends into the flow. Given the dynamics of flowing water, this is enough to measure flow without interfering with it. The paddles are not as subject to damage or clogging.

This arrangement easily connects to electronic metering to eliminate extra moving parts and allow a gage to be remotely located. Revolutions are converted to electrical signals, which can operate a regular needle gage or a lighted digital readout. Add an epoxy or other waterproof coating to the electronic circuitry and reliability is said to be improved.
Then if everything indeed works correctly, the officer of an engine company can take a line to wherever the fire is found, judge the conditions and, considering his nozzle, call for a particular flow.
Placement
If a flow meter is therefore found desirable on a pumper, the next decision is where to place the paddlewheel sensor. The location is critical.
One manufacturer of flow meters, Fire Research Corp., makes the matter seem simple: “Place it correctly—no problems. Put it in the wrong location, and it will never work satisfactorily.”
After clogging, installation errors can next be blamed for many of the problems of early flow meters—and some today. Enough is known now, however, to avoid misplacement if instructions are followed closely. This responsibility falls most heavily on the manufacturer of the fire apparatus during installation of options. Nevertheless, it is in the best interest of a fire department to understand the requirements for proper placement and inspect the equipment before acceptance.
The main installation error to avoid is placing the sensor too close after a sharp bend in a pipe. A bend causes turbulence, an unevenness of flow that can fool the sensor. Established minimum distances from other pipe arrangements that cause a flow disturbance must always be observed.
Another position consideration is the angle of the sensor in relation to the ground. If the sensor is placed downward, dirt might eventually accumulate in it. Any position above the pipe or parallel to the ground is allowed.
Strictly following all installation placement requirements for a paddlewheel sensor is said to give an accuracy of within 3 percent, or 3 gallons for each 100 gallons flowing.
As a fire fighter, Bob Barraclough thinks the fire service is ready for flow meters even at considerably less accuracy. To go along with that attitude, he prefers a new name for the device.
“I would use the term flow indicator” to lessen the precision implication of the word meter, he said. “Yes, I would want an easy way to know what I am flowing but, realistically, an accuracy within 15 percent is acceptable.” More important features to Barraclough are low cost and reliability.
Whether called flow meters or flow indicators, almost everyone who has studied the matter agrees they are a good idea. But what of the thousands of pumpers already in service without flow meters, especially those newly built for use into the next century?
Although it is clear that installation is easier when the apparatus is under construction, retrofitting is possible. Current users of flow meters say that the extra trouble of a retrofit is still better than having no flow meter at all.