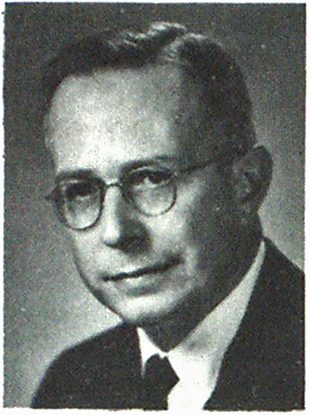
Check Pump, Accessories For Operating Condition
departments
The Volunteers Corner

Inspection of equipment is as important as fighting fires because unless your equipment is in prime condition, you won’t be able to fight fires as well as you should.
Equipment inspections should be made on a regular schedule—each shift, daily, weekly, monthly and yearly, depending on the specific items to be checked. For example, breathing apparatus should be inspected when each platoon comes on duty in a paid department. In both paid and volunteer departments, SCBAs also should be checked after each use of them. Volunteers also should look over their SCBAs at least once a week.
In addition to the usual daily, weekly and monthly inspections of apparatus, every pump should undergo an annual service test. This test also should be conducted after every major repair.
Service test procedure: Except for the length of time for each segment of the test, the service test procedures are the same as those for a three-hour delivery test. In the service test, the pump is operated at its capacity rating for a minimum of 20 minutes at 150 psi. Then the pump is operated at 70 percent of capacity at 200 psi for 10 minutes and at 50 percent of capacity at 250 psi, also for 10 minutes. Finally, conduct a spurt test for rated capacity at 165 psi for about five minutes. These times are minimums and the pump can be operated longer at any of the specified pressures.
During a service test, I like to take engine and nozzle pressure and tachometer readings every five minutes. The more readings you take, the more representative of conditions your averages for each stage of the test will be.
At the completion of the pump test, check the operation of the pump’s pressure control device—the pressure governor or pressure relief valve. Set the pressure control at 10 psi above any operating pressure over 75 psi while the pump is discharging water through one or more lines. Then close the outlet valves slowly. The pump pressure should not rise more than 30 psi if it is working properly.
Finally, conduct a vacuum test by connecting two lengths of capped hard suction to the pump and drawing 22 inches of vacuum on the compound intake—or suction—gage. All hose outlets are capped. After drawing the 22 inches of vacuum, shut off the priming pump and disengage the main pump. The pump should not lose more than 10 inches of vacuum in 10 minutes.
Check pump packing: If the pump loses more than 10 inches of vacuum in 10 minutes, the problem is frequently the pump shaft packing. While the pump is operating, it is a simple job to tighten the packing by putting a wrench to the adjustment bolts. It is important to remember that there must be a leakage of at least 10 drops per minute (I like to see somewhat more) through the packing to the ground. The passage of this small amount of water lubricates the pump shaft and keeps it from being scored.
If a pump does not put out water adequately, back-flush the pump by connecting a 2 1/8-inch line from a hydrant to one of the hose gates and then opening the hydrant. Control the hose inlet valve so that the incoming pressure is kept below 100 psi. Open each suction connection on the opposite side of the apparatus in succession and let water flow through. Continue doing this until not only all suction connections, but all hose outlet valves, have been flushed. Pump drains should similarly be flushed. Sometimes this cleaning out of accumulated sand, gravel, rust and other debris from water mains and other sources of water is all that is needed to restore a pump to good operating condition. Also check the suction strainers.
Other checks to make: All the nozzles on the pumper also should be inspected frequently. Fog nozzles may become clogged with sand and even pebbles that have passed through the pump. Some fog nozzles have a flush setting. Using this will clear the nozzle most times, but if it doesn’t, you may have to disassemble the nozzle to remove the foreign matter. A pebble lodged in the baffling of a fog nozzle can be spotted visually by the imperfect shape of the fog cone.
Also test the nozzle for smooth operation of the fog pattern adjustment and, if the nozzle has it, the gpm selector. Don’t wait for your next fire to discover problems with nozzles.
Straight tips should be inspected for burrs that will disrupt the shape of the solid stream. Sometimes it is necessary to use a fine, round file and then emery and crocus cloth to restore smoothness to the tip.
Also check your booster hose. Because it may seldom be stretched to its full length, there may be loosened couplings or damage to the exterior of the hose that may remain undiscovered until a critical time. Prevent this from occurring by pulling it all the way off the reel and then pressurize the hose to check for leaks at the reel and at the couplings. Gaskets may have to be replaced that went into service with the pumper too many years ago.
By regular inspections of your pumper and its equipment, you will ensure its reliability on the fireground.