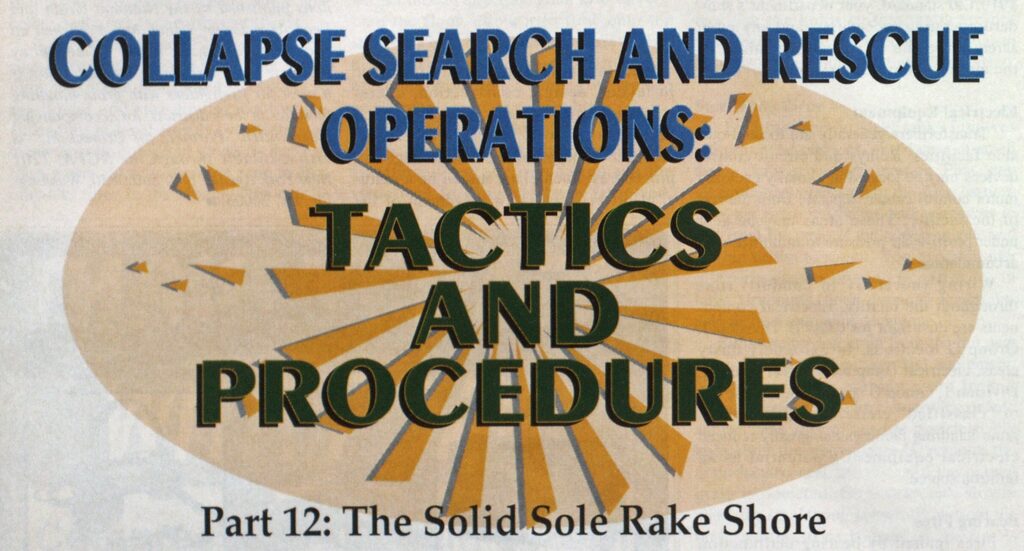
COLLAPSE SEARCH AND RESCUE OPERATIONS: TACTICS AND PROCEDURES

Part 12: The Sole Rake Shore
Once the officer in command has decided to erect rake shoring and has determined the size of the lumber to be used and a shoring size-up has been made, erection of the shores can begin.
STEP 1: ERECTING THE WALL PLATE
Erecting the wall plate is the first step in constructing a rake shore. The size of the lumber generally used is 4 x 4 or 4 x 6. The wall plate must be several feet higher than the projected point of the rake (see Part 11, Fire Engineering. July 1994); this ensures enough room for installing a two-foot minimum cleat or thrust block (as it is also called) above the rake. The two-foot length will ensure enough resistance to provide adequate holding power. After determining the proper length of the wall plate, the next step is to erect the plate; at this point, you also have the option of installing the top cleat (see step 4 below). The wall plate should be erected as “plumb” (vertically level) as possible in both directions; this helps ensure the angles of the rake will fit properly. Place the wall plate at the base of the structure, raise it up. and lay it against the building gently, keeping it plumb and shimming it if necessary. The points at which the wall plate may have to be shimmed are those at w hich the rake meets the building and at the base where it intersects the sole plate (the final adjustment will be made after the other elements of the shore have been erected). For the shore to be fully effective, these two points must have full bearing to the structure.
STEP 2: INSTALLING THE SOLE PLATE
First, make sure that the area surrounding the site at which the rake shore is to be installed is clear of debris. Clear the area on each side of the sole plate for several feet; this will keep debris out of your way while erecting the shore. Butt the sole plate into the base of the wall plate; bracing the wall plate tightly into the structure provides additional support to the structure. Lay the sole plate fiat on the surface in front of and in direct alignment with the wall plate. The sole plate must be as level as possible and at right angles to the wall plate so that the angle of the rake fits properly and has full bearing on the wall and sole plates—utilizing the rake shore’s maximum strength. Be sure there is no debris under the sole plate that could compromise the shore’s stability and integrity. If necessary, the sole plate can be shimmed to keep it level. It must be level especially at the point at which the rake’s bottom intersects the sole plate; full bearing from the base of the rake to the ground is essential for the shore to work properly. The length of the sole plate depends on the type of anchoring system used, which will be determined on site; each situation is different.
STEP 3: INSTALLING THE RAKER
Since the height of the wall and the angle of the rake shore already have been determined. the cutting team should have the raker precut to the exact length, with the proper angle cuts, and ready for installation. Then, by the time the wall plate and sole plate have been erected, the raker will be ready to be installed. The team can save quite a bit of time by predetermining— through a survey of the department’s response area and identification of the locations of potential hazards—the lengths and angles of the rakers appropriate for the situations the team is most likely to encounter.
Two members must control the raker. For ease of installation, measure back along the sole plate where the base of the raker is to intersect the plate. Place the bottom of the raker at this point, and gently lower it into the wall plate. At this time, the raker can be slid up or down slightly to get the best fit possible. Adjusting the raker up or down several inches, if necessary, ensures a proper fit and utilization of the rake shore to its fullest load-bearing potential. The raker then is toenailed into the wall plate and the sole plate; this will hold the raker temporarily in place while team members move on to the next step, installing the cleats.
STEP 4: INSTALLING THE TOP CLEAT OR THRUST BLOCK
If not installed during Step 1, install the top cleat or thrust block. The main purpose of these cleats is to stop the raker from moving upward or outward when pressure is applied to it: The shore is kept stable, enabling the raker to absorb the full load for which it was designed and transfer it directly to the ground most efficiently. The top cleat is the first cleat installed. Typically, two-inch dimensional lumber the same width as the wall plate is used; its minimum length, as mentioned above, must be at least two feel long to give it enough resistance to provide adequate holding power. Place the cleat directly on lop of the IH-inch return cut into the raker. Using the five-nail method, nail the cleat to the wall plate.
STEP 5: INSTALLING THE BOTTOM CLEAT
Place the bottom cleat on top of the sole plate just behind the base of the raker. To ensure uniformity and ease of nailing the gusset plates to the shore’s other structural elements, this cleat also should be constructed of two-inch dimensional lumber— the same width as the sole plate. The bottom cleat will be two feet or longer, depending on how you anchor the raker. Leave space for installing the wedges; this space should be approximately the width of one wedge (approximately 1½ to two inches). Nail this cleat down, again using the five-nail method.
SOLID SOLE RAKE SHORE

STEP 6: INSTALLING WEDGES
Wedges should be used whenever a shore is erected between two substantial points. The primary purposes of wedges are to prevent mistakes in measuring and cutting and to make it possible to “fine tune” the shore after it has been assembled.
The wedges also can be used as shims should the need arise, which may be often in many collapse rescue situations. Wedges can be adjusted easily; one set of wedges married together easily can fill a void of from one inch to more than three inches, if necessary. Wedges also come in handy when uneven spaces have to be supported or filled in.
STEP 7: INSTALLING GUSSET PLATES
Gusset plates lock all the rake shore connections together (the connections are the weakest part of the shore) and ensure maximum shore strength. By gusset plating both sides of the shore, the connections are locked tight, which will help stop the rake shore’s elements from moving should a secondary collapse occur. Penny (8d) nails are ideal for anchoring the plates. Larger nails are not needed; the shear strength of the nail, not its length, is being relied on. Twelve-inch by 12-inch pieces of ⅝or ¾inch plywood can be used for gusset plates regardless of whether the size of the rake shore is 4 x 4 or 6 x 6. The five-nail method is the most efficient for anchoring the plates to the shores; it ensures that the full benefits of the plates will be realized.
Top gusset plate. The top gusset plate should be installed several inches above the top of the rake itself. Doing this ties all three elements of the shore together: the wall plate, the top cleat or thrust block, and the raker. Nail the gusset plate into all three pieces, preferably on both sides of the shore, for the strongest joint possible.
Bottom gusset plate. The bottom gusset plate should be installed flush with the front edge of the wall plate and level with the bottom edge of the sole plate. This plate, too. should be nailed on both sides, using the five-nail method, for maximum effectiveness. After the plates have been erected on the shore, install the diagonal brace. Erect it on the outside of the gusset plate and nail it through the gusset plate directly into the wall plate and the sole plate. Use nails long enough to reach through the gusset plate and penetrate far enough into the wall plate and sole plate to hold properly.
Back gusset plate. The back gussets, which are the same size as the other plates, should be installed only after the set of wedges at the base of the raker has been fully tightened. These plates should be nailed into position only after you are satisfied that the raker is secured tightly enough and that the weight you are trying to support is properly transferred. Nail the plate flush with the bottom of the sole plate and slightly ahead of the wedges for maximum coverage of the area. Nail the plates into the sole plate and the rake using the fivenail method; doing this keeps the joint locked together and ensures the most efficient use of the rake shore.
STEP 8: INSTALLING THE CENTER BRACES
Installing one brace on each side in the center of the raker adds stability to the rake shore by helping to stop deflection in the raker when pressure is applied to the shore, enabling weight to be efficiently transferred directly to the ground while using the raker to its fullest capacity. As the raker comes under compression from the forces being applied to it, it acts as a column: should deflection occur in this column, its bearing capacity will be diminished. Center braces keep the rake shore’s effectiveness at its optimum. The braces are nailed over the bottom cleat and at the center of the raker using the five-nail method.
LUMBER SIZE
Determine the size of the lumber best suited for the particular situation. The size of the rake must be adequate for the load you are trying to stabilize and support. This decision can be made only at the scene with the help of a structural engineer, if possible, and by conducting a rake shore size-up, as every collapse situation is unique. The width of all of the rake shore elements should be the same. If the shore is constructed with different sizes of lumber, it w’ill not be possible to nail the gusset plates in properly, rendering the shore less effective.











WALL ANCHOR METHODS
Angle iron and pins are two of the common methods of anchoring the rake shore to the structure. When placing the rake shore against masonry, you must be careful when anchoring the shore to the building. When using pins, carefully predrill into the wall plate two holes, a few feet apart, if possible. After the wall plate has been erected, carefully drill two holes into the masonry wall and insert the pins through the plate and into the masonry, arresting any upward lift that may affect the shore. When using sections of angle iron, align them wherever you want, drill the holes into the wall, and then anchor into the wall plate. Several methods are used to anchor into masonry. Whichever method is used, anchoring should be done in two spots to achieve the best holding power.
DETERMINING RAKE ANGLES AND LENGTHS
Numerous methods for determining the angle best suited for a situation are available. The two options discussed here generally are considered the easiest:
- The 45° angle rake shore. This method is the simplest, since the top and bottom angles are the same and it provides a very efficient angle to absorb loads properly. The angle and length of the raker can be calculated in several ways. These methods are discussed in detail in Part 7 (Fire Engineering, November 1993).
- The 3, 4, 5 method. This option is especially useful if the rake shore has to be installed higher than usual and lumber size is limited. It is based on the long-standing mathematical theorem (the Pythagorean theorem) for determining the length of the hypotenuse of right triangles, which is equivalent to the length of the raker on the solid sole rake shore. The numbers “3, 4. 5″ are used for ease of measuring. For example: If you have a triangle with one leg that is three feet long and another leg four feet long, its hypotenuse would have to be five feet long to provide a 90° right triangle. The angles opposite the 90° angle would be roughly 54° and 36°. Either one can be used for a rake shore angle, if necessary.
Any multiple of the 3. 4. 5 will give you the length of the rake: 6, 8. 10 and 9, 12, 15 are two common examples. For instance: If your team had to assemble a rake shore nine feet high and had 16-foot material available, the 9. 12, 15-number sequence could be used. With the height of the rake against the wall at nine feet, the bottom of the rake would lie on the sole plate back 12 feet from the wall plate, giving you a raker length of 15 feet at an approximate angle of 36°. This shore would be quite substantial and able to support a heavy weight.
To shore an area 12 feet high using the same angles, place the raker against the wall plate 12 feet high. The base of the raker would be nine feet back from the wall plate, lying on top of the sole plate: the length of the raker would be 15 feet. The angle of this rake shore would be approximately 54° and able to support a lighter load than the 36° angle because of the higher slope of the shore. However, it may be necessary to use this system when longenough material is not available. In such a case, the rake shores can be placed closer together to support the additional weight.
The two angle cuts on this raker can be taken by measuring the square ends of the lumber or by using the steel square.