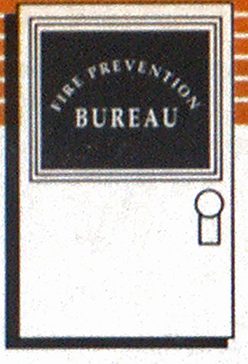
REFRIGERATED STORAGE FIRE PROTECTION
FIRE PREVENTION BUREAU

Refrigerated (cold) storage facilities follow many of the same fire code requirements as those of ordinary warehouses. The cold temperatures, however, necessitate some modifications in the way these facilities are protected.
Food products are the most common commodities stored in these buildings. Pharmaceuticals and antibiotics also are found in refrigerated storage buildings. Refrigerated storage keeps them from spoiling when stored for extended periods.
Products are stored in several different ways: solid piles, palletized storage, and rack storage. Solid piles of crates of vegetable and fruits are common. Rack storage of frozen foods also is common.
Very often the boxes, dunnage, wax paper, and pallets used to store the product determine the fire protection requirements. Many of the foodstuffs essentially would be considered noncombustible if it were not tor the combustible packaging and pallets.
In terms of “commodity classifications” (as referred to in NP’PA 231 and 231C), frozen foods, dairy products in nonwaxed containers, and fruits/vegetables in nonplastic containers on pallets are Class 1; foods in wood crates are Class II; and frozen meats in plastic trays and milk in plastic containers are Class III. A “special hazard” commodity classification is given to empty wax-coated containers, requiring a heavier sprinkler demand.
The various temperature “classes” of refrigerated storage are as follows:
- Cooler storage— 32°F to 65°F for storing such foods as eggs and apples.
- Chill rooms— 16°F to 35°F for curing meat.
- Freezer or holding rooms— — 10°F to 5°F for storing frozen foods including meats, poultry, and vegetables.
- Sharp freezer-35°F to 0°F for initial freezing and normal freezing.

(Photo by Marie Munoz.)
BUILDING CONSTRUCTION
For many years, the cold storage industry relied on the “massiveness” of building construction—the use of thick masonry walls made of brick or concrete to provide insulation—as part of the refrigerated storage process. In addition, cork or cellulosic materials very often were used for insulation on the interior of the building. Although cork rarely is used today, many older buildings still have it. A recent fire in San Antonio, Texas, points to the inherent fire problems of cork.
During the dismantling of an old meat-processing facility, individuals using cutting torches to remove old refrigerant lines in the building started a fire in the cork insulation. They had failed to place the noncombustible shields between the combustible cork and die refrigerant lines as the fire code required. The ensuing fire was contained. However, due to the nature of the cork, the remaining fire became deep-seated and continued to smolder.

(Photo by author.)

(Photo by author.)
Efforts to reach some of the smoldering cork at roof level proved to be extremely difficult. Firefighters attempting to open the multilayer roof encountered a thick top layer of gravel, six inches of sand, and finally a heavily reinforced concrete roof deck.
Today’s more modern refrigerated facilities often are of noncombustible steel frames, which can be considered fairly “lightweight” compared with yesterday’s buildings. Plastics, with their good insulating performance, have replaced cork in these facilities. Two types of plastics generally are used—polyurethane and polystyrene. For many years, “spray-on” polyurethane was applied to the interior surface of these buildings. This method of insulation has one major disadvantage: Fire will spread across its surface very readily.
Even with sprinkler protection, it is important to provide a thermal barrier to protect the plastic foam insulation from fire. In addition, be wary of missing thermal barrier tiles that have been removed during building use. They are weak links and will allow a significant fire to develop.
The prefabricated metal-encased polystyrene “sandwich” panel often is used today. In some cases, it is the actual exterior wall of a building.
From a building owner’s standpoint, openings in the walls of refrigerated storage buildings are to be avoided because they allow heat to enter the building and negate the refrigeration system. This desire to limit openings on the part of building owners becomes an issue when fire protection requirements call for firefighter access doors and smoke/heat vents as required under the Standard and Uniform fire codes.
Building access doors, essentially on 100-foot centers, are required for high-piled stock warehouses. This necessitates the use of heavily insulated doors.
Current smoke/heat vent designs make them unsuitable for use in refrigerated storage facilities because they have very little insulating value. (Some mechanical refrigeration systems can accomplish some smoke removal but not in great volumetric quantities, and they do not meet the fire-resistive requirements for fan units.)
REFRIGERANTS
The use of various types of refrigerants to establish and maintain cold temperatures is common to all of these facilities. There are three classes of refrigerants: Groups 1,2, and 3-
Group 1 refrigerants include halogenated hydrocarbons and carbon dioxide. Some of these materials are weakly flammable, while others are nonflammable; some are slightly toxic, others nontoxic.
Group 2 refrigerants are flammable, although they have a relatively narrow range of flammability. Ilie materials in this group also are toxic. Ammonia is an example of a Group 2 refrigerant.
Group 3 refrigerants are the most flammable of the refrigerants. Included in this group are such materials as propane and butane. Group 3 refrigerants are considered to be slightly toxic.
The Standard and Uniform fire codes regulate mechanical refrigeration systems. Essentially the requirements include the following:


(Photos by Mark Munoz.)
- refrigeration system installation in conformance with the mechanical code and American Society of Heating, Refrigerating, and Air Conditioning Engineers (ASHRAE) standards as appropriate.
- being readily accessible and free of combustibles.
- posted normal and emergency instructions with service and emergency phone numbers.
- appropriate labeling.
- ammonia safety features including ammonia diffusion systems.
Ammonia, at one time commonly used, is making a comeback. Due to concerns about the ozone-depleting aspects of some of the Group 1 refrigerants, some facilities have returned to using liquid anhydrous ammonia. Ammonia, although shipped as a “nonflammable” material, actually is flammable, with a flammable range of 16 to 25 percent. Several explosions and deaths have occurred in refrigerated facilities that use ammonia. In addition, individuals have been killed and injured due to ammonia’s toxic effects.

(Photo by Mark Munoz.)
Ammonia diffusion systems are needed to “dump” the ammonia from the refrigeration system in the event of an emergency, such as a fire threatening the refrigeration system or ammonia gas releasing from a break in the system and collecting in the building, creating an explosive situation or toxic atmosphere.
The diffusion system consists of piping on the highand low-pressure sides of the refrigeration system. These terminate in a specially designed and properly labeled fire department control box on the outside of the building. Labeled valves located inside the control box allow the ammonia to be released into the diffusion (mixing) chamber. Pressure gauges and equalization valves also are located in the box, as is an emergency switch to shut down all compressors.
A permanent water supply capable of providing at least two gallons of water for each pound of ammonia must be provided. In addition, a fire department connection allows the fire department to pump directly into the diffusion system.
The diffuser (or a water storage tank or water basin) is actually a mixing vessel. Initially water is introduced into the diffuser. Then the ammonia is discharged into the diffuser. Finally, the water and ammonia are mixed and then discharged into the sewer system for disposal.
SPRINKLER PROTECTION
Since a refrigerated warehouse often has automatic sprinklers, warehouse design must take into account the special conditions present. Walkin ty pe freezers/coolers very often can be protected with dry pendant sprinklers (yes, they must be sprinklered). Ensure that there is appropriate caulking with thermal mastic tape at the entry points to prevent the pipe from “sweating.”
Coolers and chill rooms often have dry or preaction-type sprinkler systems (which use detection devices for activation). Freezers, holding rooms, and sharp freezers often use doubleinterlocked preaction systems (systems in which both a detection device and a sprinkler head must operate before water enters the piping).
In freezers, holding rooms, and sharp freezers, water never should enter the system piping unless an actual fire is present. If water were to accidentally get into the piping, the pipe would have to be removed and thawed outside the building at great expense (not to mention the loss of a fire protection system for a considerable length of time).
When preaction-type systems are used, detection devices often are required in the racks themselves (especially when in-rack sprinklers are required). These detectors are commonly fixed-temperature and are of the pneumatic or electric type.
Other distinguishing characteristics of sprinkler systems in refrigerated storage facilities are the use of inspection fittings and moisture-free air. Inspection fittings are located at the following locations: where cross mains connect to risers or feed mains, where feed mains change direction, and where risers or feed mains pass from warm areas into cold rooms. These fittings allow you to examine the piping to determine if ice or frost has formed.
The air in sprinkler piping in refrigerated facilities must be free of moisture. This is accomplished with dehydrators or by taking the air directly from the coldest room being protected. As another alternative, nitrogen may be used in the piping.
Factory Mutual Data Sheet 8-29 has excellent information on the sprinkler protection (as well as other fire protection features) for these facilities. In addition, a Technical Advisory Bulletin issued with Data Sheet 8-29 includes good information on where in-rack detection may be eliminated under special conditions. In some cases, these documents are more restrictive than the NFPA standards.
When bringing the temperatures in a new refrigerated facility down for the first time, contractors will start the process very early and over a long period of time. Bringing a facility’s temperature down too quickly is said to bring about conditions of implosion due to the “tightness” of these facilities. This being the case, it is important that all inspections, including hydrostatic inspections, be performed as early as possible—before temperature reduction takes place. Once the temperatures have dropped too low, there is no opportunity to perform these inspections. Pressurized “air” tests instead of hydrostatictests are not acceptable.
OTHER CONCERNS
Fortunately, most refrigerated facilities are “clean” operations. This fact and the temperatures eliminate some typical ignition scenarios. Clean, washable interior surfaces are required by the USDA. As with other warehouses, cold storage facilities must comply with regular high-piled stock and other fire code requirements. In terms of building code requirements, specific considerations affecting these facilities often include exit travel distance requirements and interior finish requirements in the case of foam plastics.