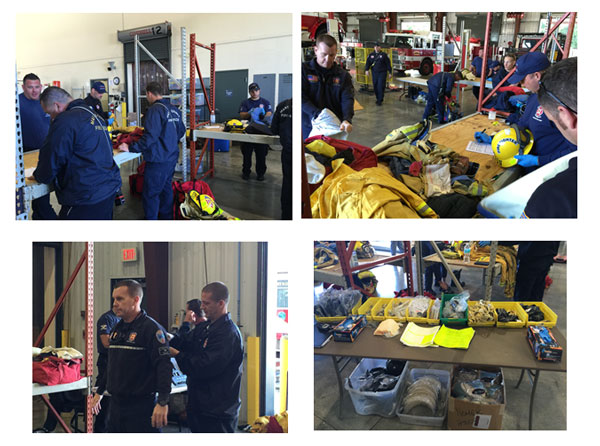
By Jeffrey L. Reed
In 2003, I was honored to write an article about the newly updated National Fire Protection Association (NFPA) Standard 1851, Standard on Selection, Care, and Maintenance of Protective Ensembles for Structural Fire Fighting and Proximity Fire Fighting. More than 12 years later, we are all still here. Everyone thought that complying with the then-new standard would be the end of us all. They were wrong. NFPA is a guideline, a place to start. As long as the fire department uses some form of guideline and has some sort of accountability for their personal protective equipment, it’s a step in the right direction.
Since the 2003 release, there have been some modifications to the standard. The core of the message remains: spec it right, keep it clean (keep it safe), and keep records of it. Seems pretty simple. Traveling around my part of the country I have seen various levels of compliance, and felt compelled to share with you all how one department has handled their compliance.
Martin County (FL) Fire Rescue is a county-run department consisting of about 400 firefighters, each assigned two sets of structural gear as well as a set of wildland firefighting gear. Every year, Martin County requires that all components be inspected. Not by the firefighter, who uses the gear on a daily basis, but by a group of selected personnel that have been trained by the manufacturer to perform the necessary inspections.
The Need
The county had a need to ensure some level of compliance for their 800+ sets of gear, as well as asset tracking of the costly equipment. They have a certified independent service provider (ISP) that they use during the year in addition to extractors spread across the county so that firefighters can keep their gear clean during the year. Additionally, the personnel trained in inspections are on shift around the county and available to answer questions for the rank and file, should the need arise.
The Cost
The county recognizes that the cost is high, but also values the safety aspect of the program. They can’t place value on the safety of their employees, who go out every day to perform tasks the general public all take for granted. There is always some question about where funds come from for capital purchases, but they manage to work it out and have kept their firefighters in safe, clean gear all manufactured less than 10 years ago.
The Method
On a sunny, chilly Florida morning in February, a manufacturer’s 1851 specialist, Brian Marenco, goes in to the department’s logistics facility to train selected personnel on bunker gear inspection. Brian gives a class to the firefighters on what to inspect and how to inspect it, and in the afternoon they perform some mock inspections and finish the day off with a question and answer session. This is usually done annually, the day before inspections begin.
For the next three days, every company is taken out of service to head to logistics. The companies come in one at a time and move through the system, set up by Matthew Resch, logistics coordinator for Martin County Fire Rescue. This is no simple task. Space is taken from the apparatus shop and shelving is set up. A set of gear is paced and taken apart on a cart for the incoming firefighters to see. A sign above reads: “Have your gear dissembled and look like this, Thank you.”
Photos 1 and 2. Signage for the gear inspection process, and disassembled gear.
As the firefighters come in, they have the room to take the gear out, take it apart, and move to an inspection table.
On day one, Brian Marenco remains to ensure the training has been beneficial, and is there to answer any questions the inspectors may have for the manufacturer.
The tables fill up quickly Three workstations are staffed by two firefighters each; these members have been trained to inspect the gear and go through all aspects of the inspection process.
Above: Firefighters go through the turnout gear inspection process.
The inspectors start by checking the date of the ensemble. Provided the date is serviceable under the 1851 guidelines, they go over the outer shell, checking for tears, wear, and any usual stains. They test the strength of the garments’ outer shell to ensure that there is no UV damage and they check all stitching and trim. Once the outer shell has been inspected, they look through the liner, The manufacturer they use has a port via which the liner can be inverted for inspection. Every liner is checked inside and out for burns, tears, and general signs of wear. All seam tape is looked over and, given that it’s in good condition and the serial number matches the outer shell, it is returned to the firefighter to be put back together and placed back in service.
Wildland gear is inspected, but since it’s not a part of the 1851 standard, they do a similar inspection of the outer shell and ensure it is safe to use. Hoods and helmets also get an inspection; inspectors ensure that all trim on the helmets is intact and all helmet parts are present and accounted for. Hoods are inspected and, if required, spare hoods and gloves are on hand for the inspection. Boots are checked to ensure they are free of debris and in good shape.
During the inspections, if a firefighter’s gear is close to being out of date or its condition is such that it either requires repair or replacement, personnel are on hand to size the firefighter for replacement sets of gear. Once the three days are over, a list of needs is compiled and given to purchasing to start the process of replacing the gear.
The end result is a fire department having a good picture of what they own and how well the firefighters who wear it are protected by the provided equipment. More importantly, the department has established a level to maintain the articles in concert with the guidelines set forth by the NFPA. This is just one very good example of how to spend three days a year to concentrate on the first line of defense worn by those who accept the challenge to do the job.
Jeffrey L. Reed is a 25-year member of the Hillcrest Fire Company #1 in Rockland County, New York, with 23 years of active service. He is a past assistant instructor of the Rockland County Fire Training Center in Pomona, New York.