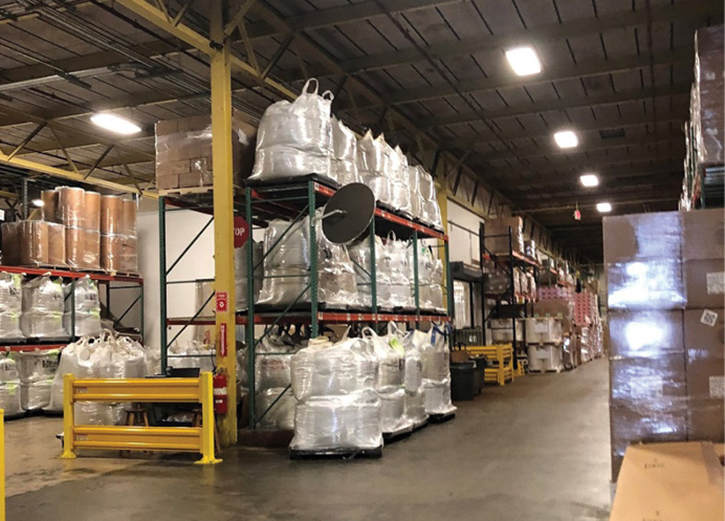
WHAT WE LEARNED ❘ By RUSSELL MAITLAND
On May 10, 2019, at 1030 hours, the Elmsford (NY) Fire Department (EFD) was dispatched to an automatic fire alarm activation at a 75,000-square-foot warehouse that stored and processed large quantities of roasted whole bean coffee into ground coffee for “K-Cup” packaging. The first-arriving assistant chief as well as an engine and a truck company determined that the initial alarm activation was caused by dust being agitated in the vicinity of a smoke alarm.
RELATED
Carbon Monoxide: A Silent Killer
Construction Concerns: Carbon Monoxide
THE DANGERS OF CARBON MONOXIDE AT THE “ROUTINE FIRE”
On entry into the office area of the warehouse, carbon monoxide (CO) levels were detected at 35 to 50 parts per million (ppm) on a single gas meter affixed to the chief’s radio strap. EFD members deployed multiple four-gas meters to monitor CO levels and determine their source location. CO levels were mostly similar throughout, with levels ranging from 35 to 50 ppm, with some areas in the 50- to 100-ppm range.
Members also identified a processing area within the building where oxygen (O2) levels dropped to 18.5 percent. This area processed whole-bean coffee into ground coffee, which was then packaged into K-Cups. With no building CO or O2 detection or any working mechanical ventilation in operation in the entire building, and with members unable to locate a CO source or reason for decreased O2 levels, the assistant chief contacted me as the Greenburgh, New York, fire inspector to address code deficiencies related to this facility. I then issued a “Cease Occupancy” order for the facility until the CO source was identified and the situation rectified.
The Findings
In the storage area, which contained more than 50,000 pounds of whole-bean coffee in 500-pound totes, CO detection readings increased to more than 150 ppm directly for each 500-pound tote. A quick Internet search yielded numerous technical bulletins that indicated CO as a known by-product of roasted coffee, with ground coffee producing significantly higher levels than whole-bean coffee; company management was not aware of this hazard.
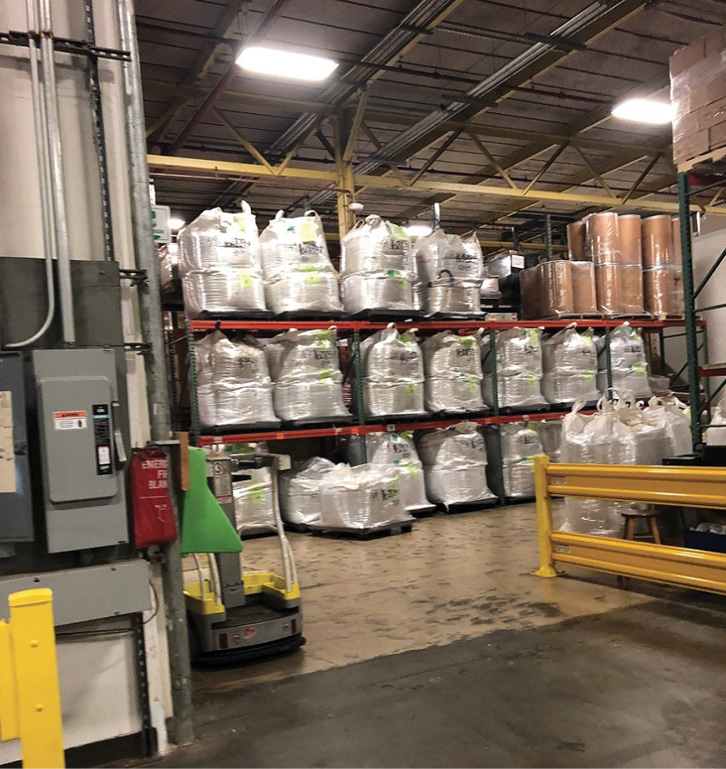
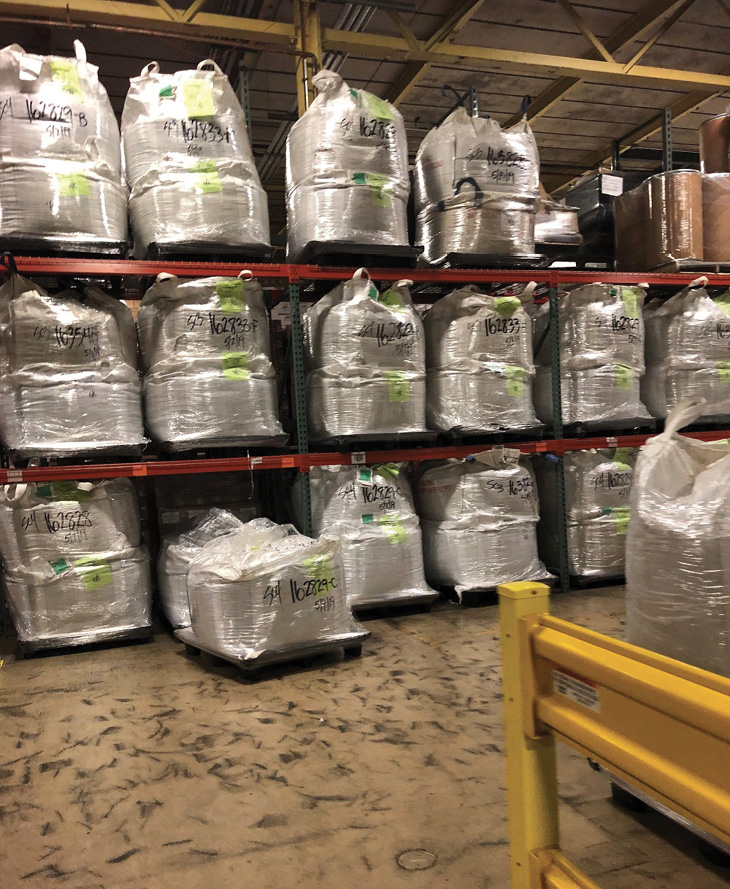
(1, 2) Five-hundred-pound totes of whole roasted coffee beans. (Photos by author.)
Interviews conducted with the operations supervisors provided information that was key in determining the cause of the O2-deficient work/processing area. Machinery used to package ground coffee into K-Cups introduced nitrogen as an inert gas to preserve the freshness of the coffee into the K-Cups. When the fire alarm sounded, all employees evacuated the building. However, all machinery used to package the K-Cups remained, with nitrogen flowing (although the production line had stopped). The nitrogen from the packaging process was found to have seeped from the machinery and into the processing area, displacing the O2 and causing the O2-deficient atmosphere.
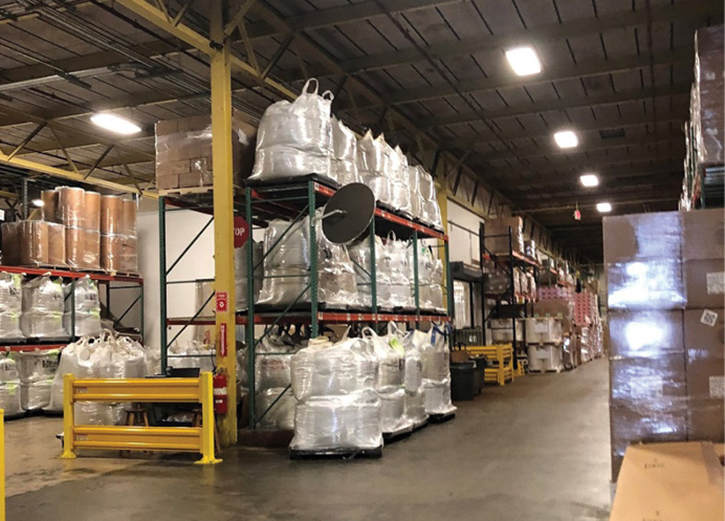
(3) Five-hundred-pound totes of whole roasted coffee beans (left) and packaged K-cups (right).
Key Points
Following are some key points to consider from this incident:
- It is critical to identify and understand that roasted coffee produces significant levels of CO and that ground-roasted coffee produces significantly higher levels of CO.
- The coffee company had no knowledge that its product produced CO.
- Regarding code enforcement, refer the incident to the proper agencies to incorporate safeguards into future codes and alert responding agencies to the potential hazard.
- Post appropriate signage to alert entrants to potential hazards.
- Fire departments must preplan and inspect facilities to understand hazards and identify systems in place or a lack thereof.
- Identify emergency shutoff to equipment (including all gases used during processing). This may require programming automated equipment.
- There is a need for professionally designed ventilation systems and backups to mitigate known hazards. (Note: The International Code Council’s 2015 International Fire Code Section 5307.5.1 addresses ventilation requirements for carbon dioxide use in beverage dispensing applications, where similar requirements may be beneficial and specific to coffee roasting and packaging facilities.)
- Conduct safety inspections (e.g., code enforcement and company staff) regularly to ensure ventilation systems are functional.
- CO and other air monitoring must be in place within the facility.
- Conduct air monitoring on all calls, regardless of dispatch information.
This incident reminds us that every day we face incidents where the hazards are not immediately evident and can have a significant impact on life safety. Training, education, and knowing your first-due area are key components to our safety and that of those we protect. In this instance, sharing information with fellow first responders may give us an edge against the unknown.
RUSSELL MAITLAND is the fire inspector for the town of Greenburgh, New York, and the assistant chief and 38-year member of the Chappaqua (NY) Fire Department. Maitland is a nationally certified fire instructor I, II, and III and is a state fire instructor for the New York State Office of Fire Prevention and Control.