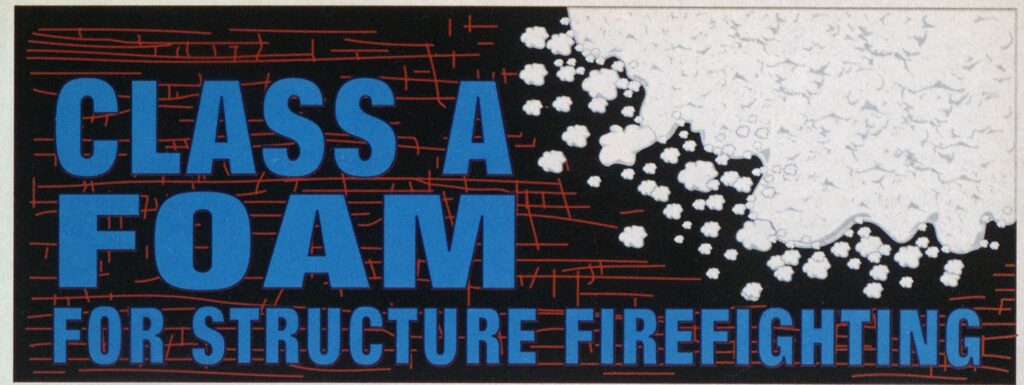
CLASS A FOAM FOR STUCTURE FIREFIGHTING

Class A foam development and application have received considerable attention in recent years. Some believe that Class A foam technology represents a new phase in the evolution of advancements in structure fire suppression.
The overall concept of Class A foam agents is simple: Add Class A foam concentrate to water, forming a foam solution that when applied to a surface will spread, wet, and penetrate, absorbing heat and cooling fuels in a shorter period of time than plain water, thereby increasing extinguishment capabilities.
THE PROPERTIES OF WATER
One gallon of water at 32°F heated to vaporization (212°F) will absorb 9,330 British thermal units (Btus) of heat. This same gallon of water on the foreground will absorb less heat because of a higher starting water temperature. If heat absorption and full evaporation actually occurred to each gallon of water applied to a structure fire, water damage claims on fire damage bills would be nonexistent. Walter Haessler’s research in 1974 found that a solid stream of water was only five to 10 percent effective at extinguishment (Haessler, Walter M. The Extinguishment of Eire. (NFPA, 1974) J. This means that only 933 Btus are absorbed for each gallon of water applied. The majority of water applied to structure fires through a conventional fire stream ends up on the floor and flows out of the structure or fire compartment. This is because of, first, gravity, and second, the high surface tension of water.
Surface tension affects the ability of liquid to spread across a given surface. The surface tension of plain water is high. This is what makes a drop of tap water tend to bead, not spread, when it is placed on a horizontal surface and to roll off vertical surfaces. Water’s high surface tension limits the surface area in contact with the fuel, as most of the water either beads or rolls off, accounting for its limited ability to absorb heat under actual fire conditions.
CLASS A FOAM AND WATER
Class A foam concentrate is a synthetic detergent hydrocarbon surfactant that enhances the fire-extinguishing properties of plain water. When mixed with water, it reduces the surface tension of the water molecules. For example, a solution of 99.7 parts water and 0.3 parts Class A foam concentrate will reduce surface tension by about two-thirds. The drop of foam solution will spread across the horizontal combustible solid surface and have a greater capacity to penetrate below the surface. The bulk of the droplet spreads out, allowing more of its surface area to contact the fuel, thus providing more rapid heat absorption.
In addition, since they are detergent hydrocarbon surfactants, Class A foams have an affinity for carbons and will form a cooling foam blanket that is oil-loving and water-shedding— meaning, in practical terms, that the foam concentrate/water mixture has a physical attraction to most Class A fuels, w hich allows w ater to first cling to and cool the surface, and then to drain out of the bubble blanket, thereby spreading, wetting, and penetrating the fuel.
Class A foam solution. A straight water-foam concentrate mix is called a foam solution. Class A foam solutions generally are 0.1 percent to 1.0 percent foam concentrate. They have excellent spreading and penetrating characteristics because of their lower surface tension. However, while foam solutions remove the problem of water’s naturally high surface tension, they do not resolve the issue of gravity. Thus, while foam solution has many tactical uses such as, for example, deep-seated peat bog or garbage dump fires, it is not yet in its optimum form for most structure fire attack situations: Too much of the foam solution applied to vertical fuels runs off onto the floor, absorbing only a limited amount of heat as it does so.

Class A finished-foam. To address this issue, air is introduced into the equation —the foam solution is “aspirated.” Taking the same amount of foam solution and, by some mechanical means of agitation, adding air will create a bubbly mass of finished-foam. The foam bubbles cling to vertical Class A fuels and allow the majority of the water (as foam solution, with its surface tension reduced) to absorb heat and evaporate. The adhering quality of the finished-foam keeps water on the three-dimensional structural fuel geometry. The finishedfoam has expanded volume and a greater surface area, allowing more water to contact more of the fuel. Increased surface area means negligible bulk and increased heat-absorbing efficiency.
In addition to their function as a “vehicle” for the cooling water, the finished-foam bubbles provide a “vapor seal” (for Class A fuels only) that assists in removing the oxygen and fuel sides from the fire tetrahedron. Foam bubbles create dead air spaces that “insulate” the fuel from heat and flames, thereby slowing down heat transfer to the fuel.
It is important to understand the underlying physical principles of Class A foam. Perhaps the most important fact to remember is that regardless of the type of foam-generating system used, the water extinguishes the fire. All the foam concentrate does is make the water work better. Do not expect the Class A foam solution to perform as a chemical fire retardant, which it is not. It is a fire suppressant, and once applied loses its suppressant action after the water evaporates. The ivater still extinguishes the fire.
Under ideal conditions, all of the finished-foam will evaporate (cooling) or penetrate (wetting) the fuel to which it’s applied. This would be considered a 100 percent or total fire suppression efficiency (no water runoff) if the exactly correct volume (critical application rate) were applied, causing rapid extinguishment. Accomplishing this with each gallon of water through application as finished-foam at the structure fire scene is practically impossible. Different methods of foam production, application methods, and application rates, as well as the fire situation itself, all factor in the suppression efficiency of the finished-foam.

(Photo by author.)
MIXING A FOAM SOLUTION
Tank mixing. One of the easiest ways to begin using Class A foam in fire operations is to mix the foam concentrate directly into the vehicle booster tank (also called “batch mixing”). Many departments trying Class A foam for the first time use this method; in the short term it is beneficial because all you need is a containcr of foam concentrate to begin using Class A foam in a training session. Pouring 2⅛ gallons of concentrate in a 500-gallon booster tank yields a 0.5 percent proportioning ratio.
When tank mixing for the first time, choose a newer pumper whose water tank and piping are relatively free of inside dirt and scale. Otherwise, the detergent action of Class A foam may loosen the debris and carry it to the nozzle screen, reducing or stopping water flow. The tank-mixing method has been a source of some controversy because of the cleansing action of the detergent within the tank and fire pump.
The tank-mixing method has some other disadvantages. The pumper will not be able to draft water from an untreated source such as a tanker or hydrant and directly pump foam solution onto the fire. Once tank-mixed, if the proportioning ratio is too high, it cannot be adjusted for changing fire conditions. When refilling the water tank, leftover foam solution can become agitated into expanded foam in the booster tank and overflow out of the tank vent; or if the water level in the tank becomes low enough, this expanded foam will be drafted into the fire pump, leading to priming difficulties.
Eduction. Eductors work on a venturi principle and utilize atmospheric pressure to force concentrate into the fire stream from a concentrate pail or tank. Most common eductors are in the 60to 95-gpm flow ranges and have one-, three-, and six-percent adjustment settings. In some applications, Class A foam concentrate is used at one percent, but in most applications the 0.5 percent proportioning rate is used. Some manufacturers offer a retrofit kit that converts the eductor to accept the 0.5-percent setting.
Be sure to match your nozzle to the eductor: If your eductor is 95 gpm, then match it with a 95-gpm nozzle. Follow manufacturers’ recommendations for pump pressure and maximum hose length. Keep the nozzle in the fully opened position during use, maintaining the rated gpm flow, or a loss of foam concentrate in the fire stream will result.
Direct-injection, discharge-side proportioning systems. This method eliminates many of the difficulties in accuracy and logistics associated with some of the other methods used to mix foam. These devices inject foam concentrate in the discharge side of the fire pump to make a foam solution. They also make foam solution production a very accurate, less-manpower-intensive job —a vital consideration at the fire scene. These devices give you the capability to adjust proportioning rates for changing fire conditions using only the amount of concentrate you need. Without a precise method of proportioning, concentrate is wasted and cost-effectiveness is defeated. (Class A foam concentrate proportioned at 0.5 percent should cost about 0.06 to 0.08 cents per treated gallon.) Advanceddesign discharge-side proportioning systems work over a wide variety of flows and pressures and keep foam concentrate out of the fire pump and water tank.
GLOSSARY
Foam concentrate: The fire chemical product —as received from the supplier—that, when diluted with water, becomes foam solution.
Foam solution: The dilute, working form of foam concentrate to which air is added to produce foam. Editor’s note. The author defines “foam solution” as the mixture of water and foam concentrate.
Foam: The aerated mixed solution, as produced by foam-generation devices. Foam is an aggregation of small bubbles produced by entraining air into a foam solution. Editor’s note. The author uses the term finished-foam ” as a more definitive way to describe ‘foam” that is in the correct bubble structure and ready to be applied to the fuel for the particular tactical use needed.
Drainage Time: The time (minutes) it takes for foam solution to drop out from the foam mass, or for a specified percent of the total solution contained in the foam to revert to liquid and drain out of the bubble solution.
Expansion: The ratio of the volume of the foam in its aerated state to the original volume of the nonaerated foam solution.
High-energy system: A foamgenerating device that adds the energy of the air source to the energy of the water pump —the compressed air foam system is high energy.
Low-energy system: A system that uses only the energy of the water pump to educt air into the foam solution — nozzle-aspirated foam systems are low energy.
Mixing chamber: A drilled tube, with deflectors or baffles, that produces bubbles in a short distance (one to two feet).
Scrubbing: The process of agitating foam solution and air within a confined space (usually a hose) that produces tiny, uniform bubbles—the length and ty pe of hose determine the amount of scrubbing and, therefore, foam quality.
Surface tension: The elastic-like force in the surface of a liquid, tending to minimize the surface area and causing drops to form.
Surfactant: A surface active agent; any wetting agent.
Wetting agent: A chemical that, when added to water, reduces the surface tension of the solution and causes it to spread and penetrate exposed objects more efficiently.
Source: Introduction to Class A Foams and Compressed Air Foam Systems for the Structural Fire Service. John Liebson (1SFSI. 1991)
GENERATING FOAM
After foam proportioning is accomplished, the foam solution is ready for application on the fuel through a discharge device. The level of aspiration and type of discharge device are contingent on the fire problem at hand. Your experience, training, and available resources come into play. Does the fire problem dictate a dense finished-foam? A quick-draining finished-foam? A very lightly aspirated foam solution? A deep-seated fire in a bale of paper, for example, may require using a foam solution in its raw form without aspiration. Protecting exposures will require an air-aspirating nozzle that forms a slower-draining finished-foam blanket that adheres to, insulates, and wets the exposure for a considerable length of time.
The ideal finished-foam type that gives the best knockdown and extinguishment characteristics for structure fire attack is a low-expansion, quick-draining foam blanket comprised of small, uniform bubbles. An expansion ratio of 7:1 of foam solution to finished-foam, producing a wet frothing foam, will increase the water’s surface area for efficient heat absorption, yet still hold a sufficient amount of water on the fuel to wet the surface and extinguish the fire.
Different low-expansion foam-gencrating devices—fog nozzle, low-energy air-aspirating nozzles, or highenergy compressed-air foam systems—produce different quality finished-foam bubble structures (different bubble sizes, bubble durability, and bubble drain times). These variables have a direct correlation to the efficiency and effectiveness of the foam for different tactical challenges.
Conventional methods. Foam solutions may be applied through conventional nozzles. Smooth-bore nozzles produce little or no bubbles and are excellent for deep-seated fires in compacted fuels. Fog nozzles and automatic nozzles, depending on design and stream pattern, produce from little or no bubbles to a 2:1 to 4:1 lowexpansion, quick-draining foam. (A 4:1 expansion ratio means that the foam solution is expanded with air to four times its original volume.) These nozzles are excellent for deep-seated fires in compacted fuels and for structural attack. Die only aspiration with these conventional devices is that which occurs through natural air entrainment created by the fire stream and through turbulence inside the nozzle itself. Applying foam solutions through smooth-bore or fog nozzles is an ideal way to begin a departmental Class A foam program, as flow and firefighting techniques remain basically the same.
Low-energy, foam-genera ting NTtem. In a low-energy system, air-aspirating nozzles use the energy of the fire stream to draw the air into the foam tube through a venturi effect, whereupon it mixes with foam solution to create the finished-foam as it leaves the nozzle. Low-energy system methods produce a low-expansion foam (expansion rate of up to 20:1) or a medium-expansion foam (expansion ratio of between 20:1 and 200:1).

(Photo by author.)

(Photo by author.)

Low-expansion finished-foams produced by air-aspirating nozzles, particularly on the lower end (below 10:1) of the low-expansion range, are excellent for direct structure fire attack; choose a nozzle with a high gpm flow to maximize volume and reach. Medium-expansion foam generally is not a suitable choice for direct fire attack, since medium-expansion, airaspirating nozzles use most of the fire stream energy to create the finishedfoam and leave little energy to propel the fire stream. Medium-expansion nozzles produce a drier finished-foam bubble that will fill structural wall cavities, fill inaccessible/poorly ventilated fire compartments such as basements. and envelope burning tire or rubbish piles, cutting oft oxygen while wetting and cooling fuels. Medium-expansion foams are also excellent for mop-up and overhaul.
Higb-energy, foam-generating sy>stern High-energy systems produce finished-foam by directly injecting compressed air into the fire stream. (The term “high energy” is used because the energy of the compressed air is added to the energy of the fire stream.) These are called compressed-air foam systems, or CAFS. CAFS technology represents a departure from traditional methods of foam generation but nevertheless has tactical advantages in structure fire suppression.
A typical CAFS configuration includes not only a fire pump and concentrate-proportioning system but also an air compressor. Compressed air is injected into the fire stream at the apparatus discharge, where it mixes with foam solution in a mixing chamber and the discharge hoseline. Unlike air-aspirating nozzles that mix air with foam solution in the foam tube to create finished-foam, CAFS use the scrubbing action of the turbulence of products in the mixing chamber and hoseline to create the finished-foam product. Foam bubbles produced in this way are very small and consistent through this highly efficient method of foam bubble production.

CLASS A FOAM-GENERATION SYSTEMS

In a CAFS, 90 percent of the foam solution used is converted into foam bubbles. All that is needed for a discharge device is a ball valve or smooth-bore nozzle: The finishedfoam is ready for application as it leaves the last section of hoseline. Adjusting the amounts of water, air, and foam concentrate entering the discharge will alter the CAFS finishedfoam product for different tactical uses. For example, a CAFS can be made to produce a dry, shaving cream-like discharge for some exposure protection applications.
Solution and air ratios for direct attack generally are one gallon of solution to one cubic foot of air. Volumetrically, that translates to a 7.5:1 ratio of air to foam solution in the hoseline. This makes for a much lighter and more maneuverable hoseline compared with those filled with water. Discharge distances are dramatically increased with the additional energy added to the fire stream via compressed air: Forty gpm of water produces four brake-horsepower; an additional 40 cfm of air adds 10 brakehorsepower and will propel the stream approximately three times farther. The most noticeable difference between CAFS and nozzle-aspirated foam-generation systems is on direct attack. CAFS dramatically reduce knockdown times, generate less smoke and steam, and leave little water damage.
CLASS A FOAM AND THE STRUCTURE FIRE ATTACK
What interior conditions can be expected when Class A foam is used in fire attack? Many firefighters who have used the technology correctly under actual conditions have experienced outstanding visibility within the structure after the foam application. The reasons for this are found in the finished-foam/flame interface. Under partial fog attack using plain water, a percentage of water vaporizes to steam as it travels through hot fire gases before contacting the fuel. Other than cooling the atmosphere around the fuel, the water lost to vaporization has no bearing on instantaneously cooling the fuel and “fogs out” the room. Other plain water droplets hit the fuel and vaporize as they roll off. By converting water into a good-quality finished-foam bubble structure, the resulting fire stream will he “insulated” from hot fire gases, losing only a small percentage of foam solution to steam as it penetrates the fire plume. This accounts for lower volumes of steam generated.



(Photos by author.)
As the finished-foam stream contacts the burning fuel, it immediately begins penetrating the material, slowing and then ceasing the combustion process. Since combustion is stopped more quickly than it is when using plain water, reduced amounts of toxic incomplete-combustion products enter the atmosphere. Water used as finished-foam absorbs heat more efficiently, causing temperatures to diminish more quickly, thus reducing the chances of rapid fire progression and flashover. The firefighter’s exposure to the high-heat environment is lessened. These factors translate to increased firefighter safety, increased operational efficiency, and increased chances for victim survivability.



(Photos courtesy of ISFSI.)
When correctly applied, Class A finished-foam keeps the water where it’s most wanted —on the involved surfaces/portions of the building. Since the penetrating ability of water is enhanced by the finished-foam, less water is required on the fire. This has some advantages: The possibility of structural collapse from additional water weight is decreased; damage from fire suppression activities is decreased; and water conservation, with its attendant benefits—such as positive environmental effects and less extensive water shuttling operations in rural areas —is increased.
How effective is the application of aspirated Class A foam solution on direct structural attack? The foam industry is saying it’s “three to five times more effective than plain water.” I have been involved extensively with Class A foam and CAFS in structure firefighting. In my experience with using CAFS and contrasting flows on structures with Iowa Water Supply methods, the general range has been a fivefold-plus increase in efficiency. These results, however, were not quantified through scientific testing in a controlled environment. The fire service needs full-scale comparative, scientific testing that will contrast Class A foam solution, applied through the different foam-generating systems, with plain water. Exact efficiency figures surely will steer future decisions relative to this technology. Still, a number of end-users have found, after proper education, training, and use in actual fireground conditions, that fire suppression capabilities can be substantially increased using this technology.
A WORD OF CAUTION ON APPLICATION RATES
The fire-killing ability1 of Class A finished-foam raises discussion about application rates for structure fire attack. Some firefighters immediately assume a much lower flow of foam solution will be needed to do the same job as plain water. In analyzing limited comparative testing and much anecdotal evidence, this may be true. However, quantitative comparative testing has yet to be performed that will verify what, if any, the reduction in specific water flows will be.
A fireload that requires a 250-gpm application rate of plain water will be knocked down in a fraction of the time when that flow rate is turned into a Class A finished-foam. A substantially lower flow rate of 75 gpm as finished-foam applied to this same fireload may extinguish the fire through the increased securing effects of its ability to wet fuels, thus reducing the total fuel load available to burn. However, it may take a much longer period of time to do so, increasing stress and reducing safety margins for the attack team. At a specific point, reducing the flow rate will prove inadequate and no longer will meet the application rate necessary for extinguishment, even though it is finished-foam.
In assessing Class A foam technology for structure firefighting, keep in mind that the water still extinguishes the fire, and approach it in the sense that it will improve your existing accurate flow rates to enhance suppression operations. This is accomplished easily by using the same flow rates on handlines with the same smooth-bore, fog, or automatic nozzle you are now using and adding to it Class A concentrate through a proportioning system. Preferably, use a nozzle that will create turbulence, adding a small amount of air, creating a lowexpansion, foam-bubble structure. While conventional application devices are not as efficient as using airaspirating nozzles or CAFS to produce the foam bubbles, at least a low percentage of the foam solution will turn into foam bubbles that will adhere to fuels, helping to do the job.

(Photo by FS6 Ind.)

(Photo by author.)
When planning to use CAFS for interior attack, pay special consideration to application rates. The physical dynamics of CAFS place less water flow per equal size hoseline than that of a plain water line. For example, 1 Viinch hoselines will flow 40to 50-gpm foam solution and 40to 50-cfm compressed air (one gpm to one cfm ratio) on direct attack. I have been involved in extinguishing numerous fully involved structure fires, including a barn fire, that demanded a 337.5gpm IOWA method flow rate with a 1 ½-inch CAFS line. However, while anecdotal evidence points to high increases in efficiency of water when using CAFS, scientific documentation—not hype or anecdotal evidence-should be used as a guide in choosing an interior CAFS flow. Common sense dictates using the same flows currently used with plain water. This could mean using a 2‘/2-inch CAFS line flowing 90 to 125 gpm/cfm for interior attack. Although the diameter of the 2½-inch hoseline is larger than that of the 1⅛ line, it will weigh approximately the same because it is filled with a 7.5:1 ratio of air to foam solution and should be as maneuverable as the l V4-inch hoseline with plain water.
SOME EQUIPMENT CONSIDERATIONS
Choose a Class A foam concentrate that is U.S. Forest Service-approved and meets NFPA 298, Standard on Foam Chemicals for Wildland Fire Control (1989). These foam concentrates have undergone testing with regard to biodegradable ability, corrosiveness, viscosity, and fire suppression performance. Be sure to ask the manufacturer for—and post—the material safety’ data sheet for the product. Class A foam in the concentrate form is a hazardous material and should be treated as such. Common sense handling means protecting personnel, equipment, and the environment. When mixed in the suggested ratios of 0.1 percent to 1.0 percent with water, it becomes a biodegradable fire suppressant. Even though it is generally regarded as safe, hill turnout gear and SCBA should be worn. All turnout gear should be cleaned after contact with the concentrate or solution. The corrosiveness of Class A foam concentrate is approximately that of a triple-strength dish soap.
A careful prepurchase evaluation process is essential to maximize the benefits of Class A foam technology Clearly identify what you hope to accomplish based on your specific needs. No single equipment item will do all things, and each piece will pose a different dollar value, tactical use, and training requirement. The ability or willingness to change your standard operating procedures should be taken into consideration, as certain equipment will mean more change than others. After careful evaluation, choose the equipment with the best benefit-to-cost ratio for your specific needs, and be sure you have enough education and training to feel comfortable about using it. When writing specs, positively match gpm flow ranges to the intended use. This is an important issue when designing municipal apparatus because much equipment is made for lower-flow forestry usage.
Utilizing CAFS on a municipal pumper requires a basic understanding of hydropneumatics and a good working knowledge of the CAF system. All units have one basic goal that must be met to produce CAFS discharge: the marriage of water, foam concentrate, and compressed air into the discharge. During a recent instructors’ seminar, an instructor emphasized the point of the possibility of operator and equipment error, leaving the nozzleman with little or no discharge from the nozzle. This could happen with CAFS for the same reason it has happened to many of us with plain water: equipment failure or operator error. Purchase CAFS equipment from a reputable manufacturer with a proven track record who will provide an equipment in-service program. And, of course, the importance of regular, thorough training cannot be overstated.
When looking to utilize Class A foam in suppression operations:
- Obtain all the education currently available through private and governmental agencies, trade publications, association literature, and so on.
- Ask present users how they like their equipment and what impact it has had on their fire operations.
- Have foam industry representatives explain the technical aspects of
- the equipment and demonstrate it.
- Schedule supervised live fire training sessions after receiving qualified instructions on the operation, application, tactics, and safety of Class A foam-generating equipment.
- Follow all guidelines of NFPA, OSHA, and other authorities having jurisdiction for live fire training.
Class A foam is not a panacea for the fire service. It is not a replacement for personnel, equipment, or water supplies. Class A foam concentrate enhances water’s effectiveness but will not replace water. The increase in firefighter safety margins possible with Class A foam are not a substitute for sound fireground command decisions, proper tactics and procedures, or general fireground safety practices. However, experience shows that Class A foam technology, when used correctly, presents a substantial gain in fireground operational effectiveness and, more important, in firefighter safety. It can be an important resource in the search to improve your fire suppression capabilities.