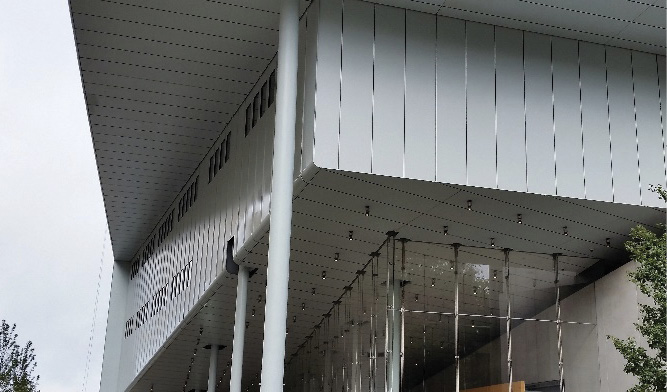
By Philip Paff
It has been a little more than 18 months since the tragedy of the Grenfell Tower fire of London in which 71 lives were lost. Much has happened in Great Britain since that event—an investigation, an inquiry, and the subsequent audit of other buildings throughout the country.
The fire that occurred on June 14, 2017, has origins in the failure of a number of construction practices and systems within the structure. One such component was the aluminum composite panel (ACP) used as cladding on the building’s façade, which, in conjunction with insulation materials, has been blamed for the rapid fire spread across the building’s external skin. The fire, in moving externally, circumvented many fire protection systems, resulting in fire damage throughout virtually all areas of the building.
But, let’s consider for a moment what would have happened if that fire had occurred in the United States in an equivalent building constructed to North American standards.
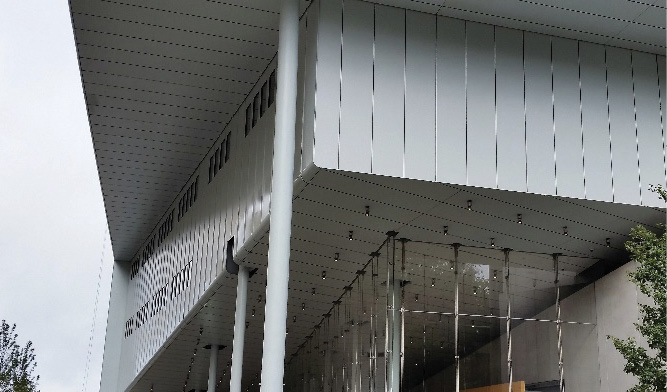
(1) An ACP-clad building in New York City. Once the panels are applied, it is difficult to identify the panel type. (Photos by author unless otherwise noted.)

(2) This auto mall is clad in ACP. (Photo by Greg Havel.)
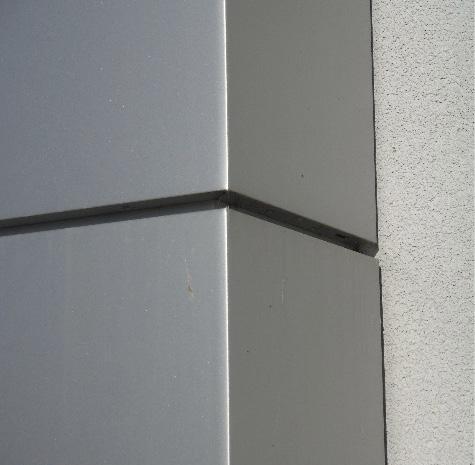
(3) A close-up of ACP on a building. (Photo by Greg Havel.)
Grenfell Tower
Drawing a comparison with the Grenfell Tower fire is difficult. The 43-year-old, 24-floor apartment block that was rehabbed in 2016 had but one evacuation stairwell, no sprinkler system, an alarm system that serviced common areas only, and highly combustible external cladding. Some may even say at the time of the Grenfell Tower fire that it would not be possible to find a structure of the same description in the United States. However, as time has passed, similar cladding has become part of buildings being constructed throughout the United States.
So, what might we expect during a fire in a structure built to an equivalent U.S. standard? A building that makes comprehensive use of fire protection systems such as multiple fire isolated evacuation routes; fire command centers; and fixed fire suppression systems such as sprinklers, hydrants, and a smoke-responsive heating-ventilation-air-conditioning (HVAC) system.
Strangely enough, to make this comparison, we have to look to a fire that occurred in Australia in 2014. Australia, although it has its own system of codes and fire protection methodologies, shares similarities on many fronts with those of the United States. This allows for a case study of sorts of a fire event involving ACP used as cladding.
Aluminum Composite Panels
As a brief refresher, ACP is approximately 3⁄16 inch thick and is comprised of two sheets of thin aluminum that sandwich a polymer core. Predominantly, the polymer core is polyethylene and the source of many fire-related problems globally. ACP can be applied flat, rolled, bent, or formed into many other profiles.
Let’s consider the fire potential of ACP to gauge the depth of the issue. The panel or, to be more precise, the polyethylene core material has an ignition temperature of approximately 660°F and in its form as cladding has an energy density similar to that of gasoline. This means that every 10 ft² of polyethylene-cored cladding is equivalent to a gallon of gas. When viewed from the perspective that an average 30-story building may require approximately 90,000 ft² of cladding, that’s around 9,000 gallons of gas hanging from the building’s exterior.
What’s in an Aluminum Composite Panel?
An aluminum composite panel (ACP) is found in two primary forms that may be further divided into subgroups.
1. ACP—Polymer core
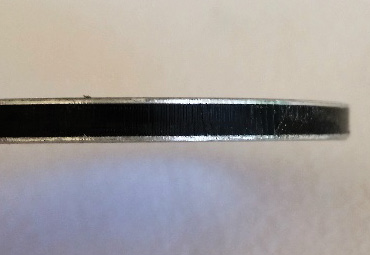
(1) It is highly flammable and contains no additives for fire resistance. (Photos by author.)

(2) It has mild resistance to fire and contains minerals or clay-based compounds, which increase fire resistance. The panel will self-extinguish in the absence of heat/ventilation; it will delaminate when exposed to heat.
2. ACP—Aluminum Core
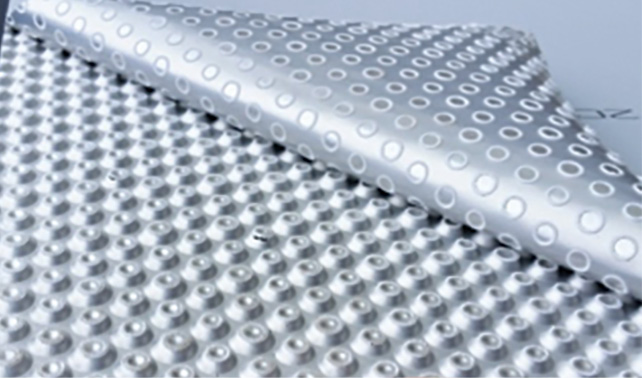
(3) The aluminum stamped core. Note the air gaps.
Case Study
Following is a case study of a fire that occurred on November 25, 2014, in a Lacrosse, Docklands (Melbourne, Australia) apartment building clad with flammable ACP.
Fire Building Construction
The building had a footprint of 39,000 ft² and a height of 193 feet. It consisted of 23 levels. Level 1 was a parking garage. Levels 2-3 were commercial occupancies, and Levels 4-22 were residential occupancies. Each floor had 15 apartments; each apartment had an area of 1,000 ft2. There were an estimated 400 occupants.
The structure was of Type 1 construction with a reinforced concrete moment resisting frame and walls of concrete, masonry, and gypsum board. The floors were concrete, and the roof was metal deck. There were three elevators in the central core and two evacuation stairs, fire isolated and pressurized, one one-third and the other two-thirds of the floor length.
Fire Protection Systems
The building, including the apartments, had a fire detection and alarm system as well as a wet pipe sprinkler system. Activation of sprinklers initiated signaling to the fire department through the fire indicator panel. It also had the following:
- Hardwired interconnected smoke alarms within the apartments; they did not have signaling to the fire department.
- An early warning and intercommunication system with speakers for use by the fire department only in both public and private areas.
- The stairwells used an air-pressurization system with variable speed discharge fans when in fire mode.
- There were internal fire hydrants (standpipe hose valves), an internal fire sprinkler/hydrant pump system, and an external fire department connection (FDC) boost point.
The Apartments
The affected apartments were aligned vertically. They were serviced by individual split-style air-conditioning units located on an external balcony. Because it was a residential complex, smoke alarms were required within the occupiable space of each apartment. It was not required that smoke alarms be linked back to the main fire alarm panel. A speaker system was fitted to the common areas and the individual apartments, providing automatic alerting of occupants. The system also functioned as a public address system in emergencies. All apartments were fitted with fire sprinklers, four to six sprinkler heads per apartment depending on size and layout. No sprinklers were fitted to balcony spaces because the balcony area was smaller than the size for which the code mandated sprinklers.
The Fire
A cigarette discarded improperly in a plastic container atop a timber table on the balcony of a residential apartment on level 8 (Apt. 805) started the fire. The plastic container and timber tabletop supplied enough fuel to set off a nearby split-system outdoor air-conditioner unit, waste cardboard, and ultimately the ACP on the building’s exterior. The ACP extended along the vertical faces of the building and was applied in such a way as to form a return wall running to the intersection of the balcony and a sliding glass door leading to internal living spaces of each apartment on every level.
Fire Service
Fire service communications received a phone call at 2:24 a.m. reporting a fire; secondary notification in the form of an automatic alarm notification was also sent to dispatch. The alarm was triggered by activation of a sprinkler flow switch.
Fire crews arrived within five minutes of the call and observed fire rapidly extending upward, externally involving approximately six floors. As the fire moved upward, it caught onto the balcony area of each level, involving external air-conditioner units, garden furniture, and clothes racks. Command immediately ordered a third alarm. At 2:35 a.m., command advised dispatch that the fire had reached level 21 (uppermost floor) and struck a fourth alarm.
Fire Operations
Fortunately, an elevated roadway was beside the building. Firefighters were able to position an aerial apparatus on the roadway, providing at least an additional three floors of reach with its stream.
Internally, the building’s sprinkler system was in operation over 16 floors, containing the fire to the rooms directly above the fire apartment of origin on each level. This gave firefighters the time to evacuate occupants and get attack teams in place; only crews on levels 10 and 19, respectively, required hoseline intervention. One hundred twenty-two firefighters staffing 29 varying apparatus combated and managed the incident.
The building’s internal hydrant and sprinkler system was designed to flow water to support four sprinkler heads and two fire hydrants simultaneously. This design load was made possible on upper floors by on-site internal pumps that could be supplemented by apparatus at the FDC if necessary.
During the incident, 26 sprinkler heads and two hydrants were in operation. The system obviously performed well beyond its design parameters in containing the fire. A number of the fire-affected apartments saw operation of more than one sprinkler head; activation locations were predominantly the kitchen area and bedroom 2 of each apartment. Fire crews used handlines in apartments 1005 and 1905; attack crews reported at the time that the sprinklers had contained the fire in each instance.
Externally, the fire ceased to progress as it had reached the uppermost level of the building. Design aspects of the building minimized fuel available horizontally, preventing lateral spread. Heat, smoke, and water damage were well contained to the “5-series vertical block” of apartments within the building.
Evacuation of the building’s occupants commenced prior to the arrival of the fire department. The building’s fire alarm system automatically initiated automatic evacuation. In Australia, it is common for high-rise buildings to have an automatic system that applies a cascading or segmented system of evacuation. On activation, occupants of the fire floor and one floor above and one floor below are notified. The system then radiates upward at a level per minute to the uppermost floor, after which alerting begins two levels below the fire and radiates downward to the first floor.
Despite an effective alerting system, common factors inherent to many multitenant occupancies such as ignorance, impairment, and access to private residences make identifying evacuation numbers and accountability difficult. This influenced tactics particularly with the external fire, causing multifloor involvement that prompted a need for greater resources extremely early in operations. The “reflex” time needed as adequate units respond, are assigned, and then go to work highlights the need for the right building intelligence at the right time—that is to say, that access to information for what’s important now. The building also requires simultaneous effective internal fire management strategies and systems such as the process of full evacuation and automatic suppression systems.
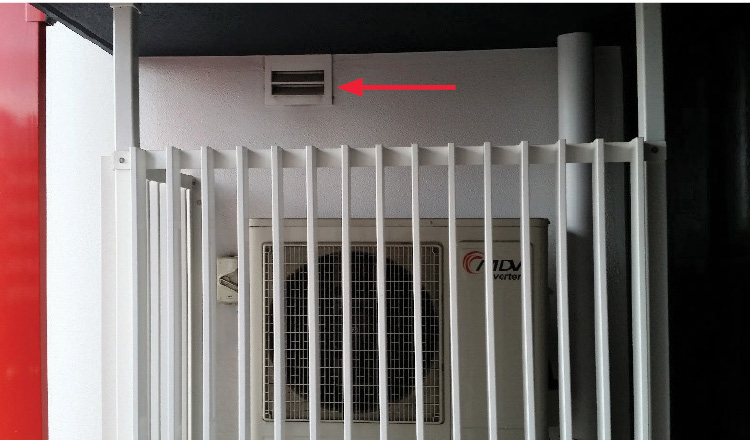
(5) The arrangement of the apartment exhaust discharge (arrow) onto the balcony area, a common design feature. Also note the location of the external air-conditioner.
Initially, the building’s internal alerting system operated well, but then it suffered a progressive failure because of what may be viewed as code and design shortfalls.
Each balcony contained an exhaust outlet that was supplied by flexible ducting fed from the kitchen and bathroom spaces within each apartment. During the event, fire entered the exhaust discharge of the external wall and destroyed the flexible ducting behind. Fire, then within the void space, compromised the wiring of the public address speaker system progressively throughout the building. This necessitated a resource-intensive complement of firefighters to rapidly investigate every apartment of every floor to clear occupants.
Firefighters aided in the removal and evacuation of more than 400 persons. Command instigated measures to temporarily rehouse occupants of smoke- and fire-affected apartments to a bus station nearby. Support agencies then assumed management of evacuees for the extended term. No firefighters or civilians were significantly injured during the event.
Frontline Code Enforcement in Australia: A Primer
Investigation
Postincident investigation identified issues that firefighters may commonly experience at larger-scale incidents, such as communications, building system failures, and a lack of high-quality intelligence in the form of occupant numbers and location. The following elements challenged or aided fire crews:
Figure 1. The Building Plan Indicating the Fire Apartment

Figure 2. Plan of Fire Apartment 805
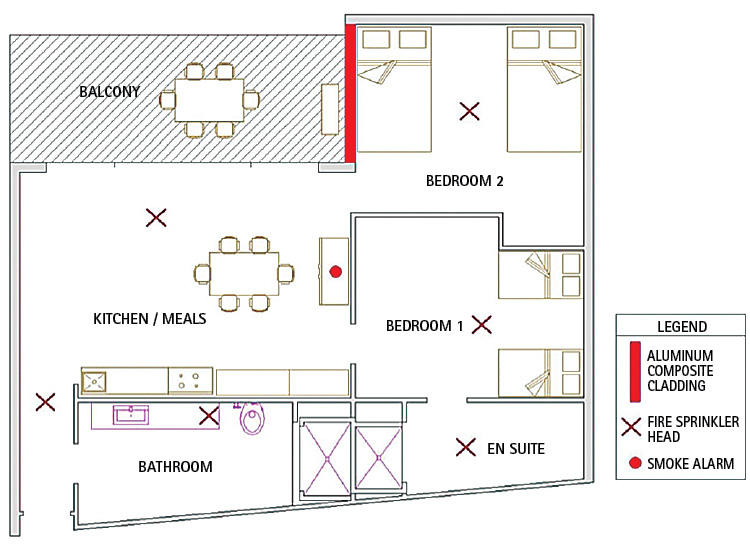
The floor plan of the fire apartment. The section in red denotes the area clad with ACP. Approximately 55 ft2 of 3⁄16-inch material at each floor may appear as a small fuel package at first glance. When exposed to fire conditions, however, the material was the equivalent of 5½ gallons of gasoline.
Occupants
- Varying degrees of overcrowding were evident; the permitted occupancy levels were exceeded. Each apartment contained two bedrooms; many apartments contained between six and eight beds.
- Higher occupancy contributes to a higher fuel load. Personal items; clothing; and, in some cases, temporary structures around beds within the living spaces contributed to a higher fuel load. This situation extended to balcony spaces also.
- A number of apartments displayed characteristics of hoarding.
- Tampering with smoke detection equipment to prevent false alarms was evident in many occupancies.
- In a residential or, more precisely, high-density “sole occupancy” building, building management and fire service personnel are restricted in inquiring about occupancy levels in an attempt to maintain safety; each apartment is a private residence—simply put, a person’s home really is his castle.
Fire Protection Systems
Fire involvement into the void space immediately behind an exhaust outlet on the balcony of Apt. 805 caused the building emergency public address system to short-circuit, rendering the system useless. Australian standards require that fire protection system wiring be fire resistive only from the annunciator panel to the area or zone covered (in this case, each floor).

(4) The apartments outlined in red were primarily affected by the fire.
The system rigged electrically at each floor in “series” configuration failed when fire impacted the cabling of one apartment’s wiring loop.
Other features installed to support occupant safety and evacuation—such as extinguishers, emergency egress lighting, fire doors, and hardware—were maintained and operated as intended.
An issue was the all-too-common occupants’ use of extinguisher recesses or cupboards as storage space.
Stairwell pressurization in each of the two evacuation stairwells operated as required; no smoke contamination was observed.
Note: It is required that smoke detection be installed on the supply air to HVAC and pressurization systems. Detection of smoke forces a system shutdown, minimizing smoke contamination of unaffected areas.
Building
Wind conditions on the evening of the fire event were from the west and were between 12 and 18 miles per hour. Orientation of the affected apartments was on the eastern side (leeward) of the building. The wind drew away smoke, heat, and flame, likely assisting in fire control. The outcome of an alternative wind situation on fire conditions has not been investigated.
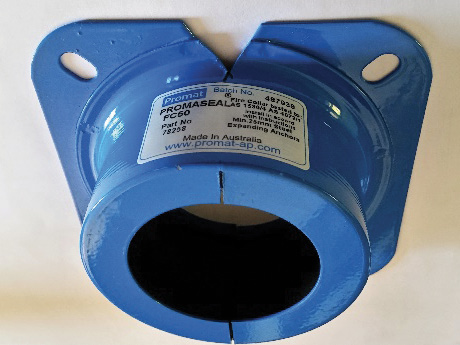
(6) An example of the intumescent fire collar. It is placed around utility pipe passing through a wall or floor. When exposed to fire, the lining of the collar swells, sealing the opening. The material will eventually char, forming a protective seal, limiting flame and fire gas travel.
An aspect of the building’s systems contributed to fire spread. Drainage to each balcony was by a drainpipe that was “T’d” into a vertical drainage pipe encapsulated by the aluminum cladding. The vertical drainage pipe, constructed of PVC, passed through the concrete deck of each balcony section. As required by code, the pipe work was sealed with an intumescent collar to prevent fire spread. When a pipe is impinged by fire, the collar swells inward and closes the plastic pipe, stopping fire. The collar has a two-hour fire rating. The issue is that the collar is designed for a single pipe to pass through. During construction, contractors used a T-junction piece to connect the balcony drain pipe to the vertical drainage. A junction piece is of heavier construction than straight pipe, and the joint produced is also heavier. This affected the operation of the collar under fire conditions and failed to limit fire spread.
At this fire, it was fortunate that the architectural features of the building minimized the application of the ACP cladding. This is not the case with many structures that apply thousands of square feet vertically and laterally without any fire engineered barriers such as fire breaks, separation, or fire stopping materials. This may also be the case of architectural barriers that may be coincidental to design such as the use of alternate materials for effect or breezeways intended for ventilation or wind loading.
The outcome of this fire, driven heavily by its use of ACP cladding, had a good ending. Yet, it illustrates the effect many groups have on building safety—from the engineering and design stage to physical construction and the actions of contractors and occupants.
Firefighters have a responsibility in this equation also: They should be familiar with the building and its occupancy and know those systems for which we have lobbied so hard and long, such as sprinklers, risk-suitable fire water, and evacuation and smoke-control systems.
Philip Paff, AFSM, MIFireE, CFO, is a captain in Queensland, Australia, with 23 years of experience as a rescue officer. He has a bachelor’s degree in emergency service operations and is a member of Australia Task Force 1 urban search and rescue. He is a recipient of the Australian Fire Service Medal for his contribution to rescue.