BY BILL CORRIGAN AND MAT CHIBBARO
A five-alarm fire devastated a seven-story building under construction in College Park, Maryland, in 2017. The incident, again, demonstrated the inherent risks that building codes allow in large, tall combustible structures under construction. However, unlike the many fires that have occurred in the United States in such buildings while under construction, a sustained interior attack eventually stopped the fire before it ran the full length of the building. This occurred despite the challenges firefighters encountered with regard to construction and fire protection systems. The fire suppression forces and code enforcement officials learned many lessons related to these large combustible buildings in their vulnerable, incomplete stage.
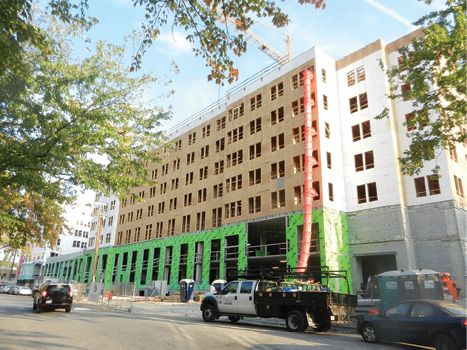
(1) The building several months before the fire. This side of the building, more than 500 feet long, was the only one accessible to fire apparatus. (Photo by Mat Chibbaro.)
The Building
The unfortunately named Fuse 47 building was a mixed-construction structure, sometimes referred to as “podium construction” (photo 1). Floors 1 and 2 were of fire-resistant Type I construction intended to contain parking, office, and amenity spaces. Floors 3-7 were combustible Type III ordinary construction containing apartment units. (Although the structure above the podium appears to be Type V wood frame construction, it is actually Type III construction; recent changes to the International Building Code now allow fire retardant-treated wood within a fire-rated exterior wall assembly). In April 2016, the complex was a few months away from occupancy.
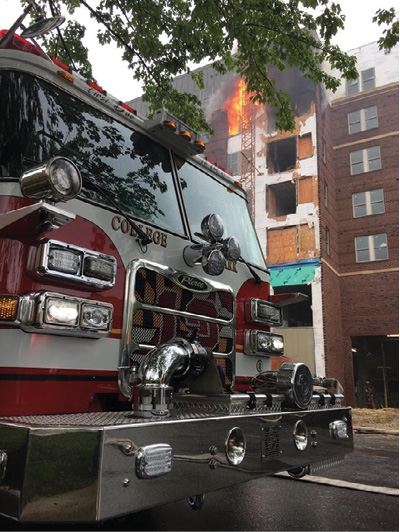
(2) Fire in the sixth-floor apartment of origin. Note the exposed exterior sheathing, the fire directly impinging on the construction lift, and the floor-to-ceiling appliance loading openings. (Photo by Ron Humberson.)
Fire Origin
The fire originated in the sixth-floor, one-bedroom apartment where the trash chute had been located when photo 1 was taken. The fire was later determined to be accidental. Electrical, hot work, and heating were ruled out as causes.
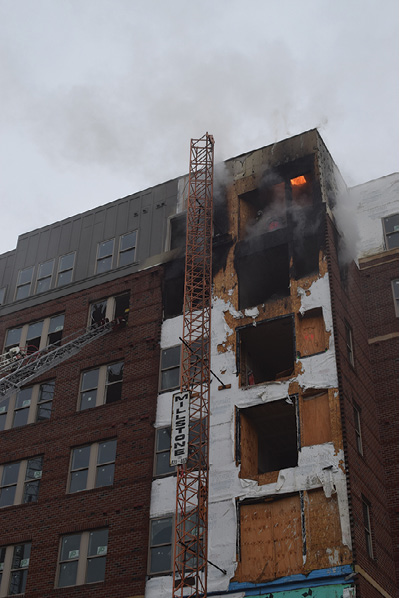
(3) Fire was visible in the attic space above the seventh floor after the fire in the sixth-floor apartment was knocked down. Fire extension was rapid in the concealed fire-rated roof/ceiling assembly. (Photo by Mark Brady.)
The apartment of origin contained a significant fire load of appliance-packaging materials. This apartment and the others in this stack were appliance staging areas served by an outside construction lift. To avoid damage, they were the last remaining apartments without drywall installed on all walls and ceilings.
The fire began on a Monday morning when construction workers occupied the building. The presence of spent fire extinguishers at the scene indicated that attempts to extinguish the fire had been made before the fire department’s arrival.
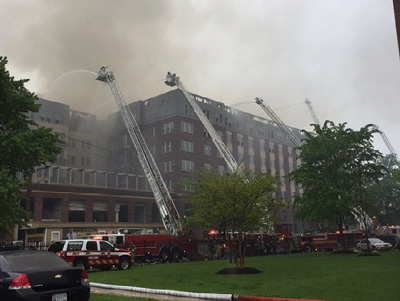
(4) Aerial master streams operating at side A. The trench cut was made at the fire wall close to the left side of this photo. (Photo by Mark Brady.)
Initial Attack
At 0935 hours on April 24, 2017, Prince George’s County (MD) Fire Department (PGFD) dispatched a box alarm for a fire in a building under construction at 4700 Berwyn House Road. The standard box alarm included four engine companies, three ladder companies, one ambulance, and two command officers. PGFD is the largest combination (volunteer and career) department in the country and borders on Washington, DC.
The first-due company, the College Park (MD) Volunteer Fire Department (CPVFD), is housed in PGFD Station 12, two blocks from the fire scene. On arrival, CPVFD Chief Bill Corrigan assumed command and reported fire showing from a sixth-floor apartment. He immediately requested a second alarm because of the building’s size and construction and because the area of the fire apartment was unfinished.
Fortunately, fire was showing from the building’s south side (side A), the only side that permitted fire apparatus access (photo 2). The rear of the building has a steep hill; both short sides of the building had no fire apparatus access lanes or roads. The fire was also very close to the only stairway (equipped with a standpipe) in the building’s east section near the A-D corner.
Engine 812 (E812) arrived next, intending to forward lay a supply line from a hydrant near the center of side A toward the fire. Since that hydrant was blocked by construction equipment, the driver proceeded to a hydrant near the A-D corner, leaving access for the ladder truck directly in front of the fire apartment.
As first-alarm crews proceeded into the building to the sixth and seventh floors, in accord with PGFD general orders, E812 made an exterior attack using the deluge gun, which darkened the fire down considerably. Another engine company on the box alarm supplied the combined sprinkler/standpipe fire department connection (FDC). Truck companies began a search for workers, which turned up negative. When the E812 crew reported good pressure on the standpipe in the nearby stairwell, command ordered the transition to an interior attack.
Several Challenges Arise
As interior crews set up to initiate an attack from the standpipe, the first of many challenges arose. The standpipe pressure dropped suddenly and significantly after the hose valve was opened. The crew reported this to command and quickly moved to control the fire apartment door. To do so, they had to move a stack of drywall holding the door open in heavy-smoke and high-heat conditions without hoseline protection.
Since the FDC was being supplied, the reason for the loss in standpipe pressure was unknown; the standpipe itself appeared to be intact. E812 Driver/Operator Lieutenant Dan Broskey led an operation to stretch a supply line to the bottom of the stairway to backfeed the standpipe through a hose outlet. As this effort was in progress, the fire again took hold of the apartment. Command was about to order interior crews back to the stairway to resume the exterior attack when the standpipe backfeed operation was completed. The sixth-floor crews then quickly moved into the fire apartment and knocked down the fire. E812 officer Lieutenant Jerry Fokas was careful to keep crews safely away from the floor-to-ceiling appliance-loading opening in the exterior living room wall.
Crews on the seventh floor found light smoke conditions and no fire, but they quickly discovered fire in the attic above the apartment directly above the apartment of origin. Worse, the truck company’s typical six-foot hooks were inadequate to pull the 11-foot ceilings. Moreover, the ceilings had two layers of drywall as part of a fire-rated assembly designed to keep fire out, but this exacerbated the challenge of gaining access to the attic from below.
Once the fire took hold in the continuous attic space formed by the wood trusses (photo 3), it spread rapidly and unimpeded in two directions above a circular corridor that was flanked by apartments. Crews attempted at several locations to gain access and get ahead of the fire from below. However, the speed of the fire and the aforementioned challenges made that impossible.
Defensive Operation
After about 35 minutes of a tough interior fire attack, crews were ordered out in a controlled fashion as aerial operations were set up. Eventually, six aerial streams flowed water into the attic. One limitation was that only side A allowed apparatus access (photo 4). Most of this side also had overhead power lines, necessitating shutting off power in the nearby area.
The building’s size and construction also presented challenges. Because of the structure’s height, the aerial streams barely made it over the roof edge, limiting their reach and penetration. The fire-rated roof/ceiling assembly also limited the aerial stream’s penetration—the fire appeared to break through the roof covering, mostly where air-conditioning units fell through fire-weakened trusses.
At the peak of the defensive operation, approximately 15,000 gallons per minute (gpm) were flowing into the building. Water supply was not an issue; a very large main was one block away on U.S. Route 1.
Trench Cut
As the defensive operation was underway, the third-alarm assignment made a stand at a fire wall that separated the wood-framed floors 3-7 into east and west sections. In heavy-smoke conditions, crews on the roof cut a four-foot-wide trench across the building on the fire side of the fire wall (photos 5-7). The topmost white layer of the roofing material resisted heat. As air-conditioning units began to sag into the structure, this layer just stretched and tore; it would hardly burn. It gummed up a lot of saw blades (photo 8). Crews on the seventh floor opened ceilings near the fire wall to prepare to stop extension. To obtain adequate water to defend the trench cut with portable master stream devices and handlines, a four-inch supply line was hoisted to the roof to supplement the standpipe in the one stairway in the building’s west section.
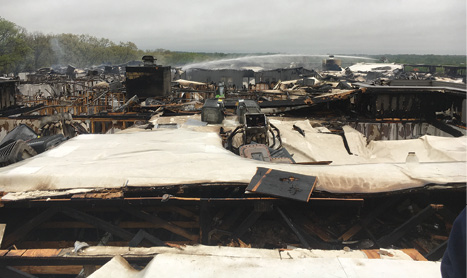
(5) A view from the west portion of the roof a day into the incident, showing the trench cut (foreground) and the limited penetration of the aerial stream (background). (Photo by Ron Humberson.)
Replenishing air tanks, saw blades, fuel, and other supplies was challenging. Officers on the roof ensured that crews stayed away from the edges of the roof, which had no guards or parapets. Eventually this stand succeeded and the fire was stopped before it could extend into the building’s west side.
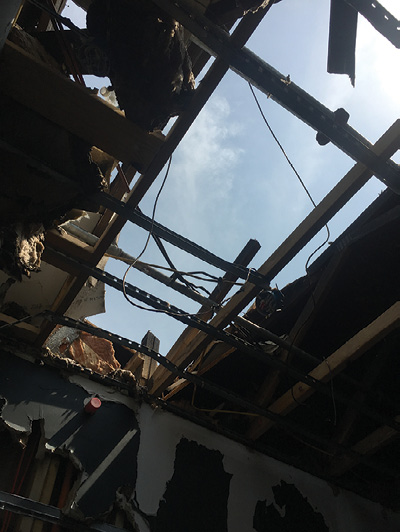
(6) The trench cut seen from the interior. (Photo by Jerry Fokas.)
Extended Operations
The incident’s effects extended well beyond the fire building. Directly across the street, a seven-story high-rise apartment building occupied by senior residents was completely evacuated because of smoke infiltration. The overcast weather conditions that day held the smoke close to ground level, prompting closure of the main University of Maryland campus at 1230 hours. A tower crane operator on an adjacent construction site was trapped overnight when the area power was shut off before his shutdown procedures were completed.
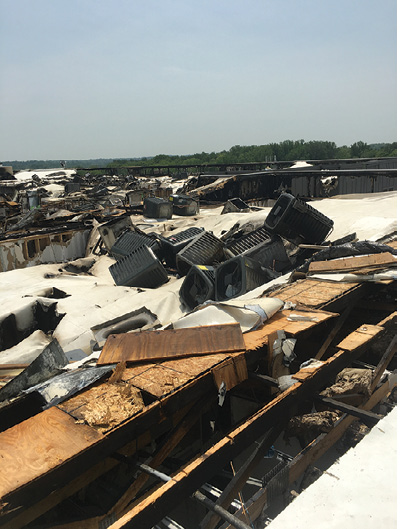
(7) An exterior view of the trench cut. Note the air-conditioning units. (Photo by Jerry Fokas.)
Companies from three surrounding counties and Washington, DC, operated on the firegound. Transfer companies came from up to 65 miles away near the Maryland/Pennsylvania state line.
Units maintained a constant presence on the scene for five days. Spot checks at three-hour intervals found hot spots until seven days after the fire began. Firefighters sustained only two minor injuries.

(8) The composition of the roofing material was unknown; responders had no access to approved building plans. When roofing was cut, it tended to resist heat and gum up saw blades. (Photo by Jerry Fokas.)
Aftermath
The direct property loss is estimated to be $51 million. According to PGFD Public Information Officer Mark Brady, this was the largest suppression effort in county history. Of course, as in most large incidents, indirect property losses such as demolition, rebuilding, lost rent, and so forth exceeded the direct loss.
National Institute of Standards and Technology (NIST) fire protection engineers investigated the vertical fire spread and determined that fire and heat had lapped though a seventh-floor window directly into the attic. A portion of the apartment ceiling where the top of the exterior trash chute had been previously secured (see photo 1) had not yet been drywalled. NIST currently theorizes that this provided a small but sufficient avenue through which fire could extend into the attic (see photo 3).

(9) The west showing the side A access. (Photo by Mark Brady.)
Building Construction
Type III construction structures were formerly known as “ordinary construction” or “brick-and-joist” construction. Legacy construction was constrained by materials available: Limited lengths of solid wood joists were framed into masonry or brick exterior or party walls. In the past few decades, lightweight engineered wood construction and sprinkler systems have allowed these structures to be built larger and taller. Additionally, a horizontal building separation allowance inserted into building codes permits a wood-framed building to be built on top of a separate fire-resistant building, referred to as “podium construction.” Furthermore, fire-rated wood and drywall bearing assemblies have replaced exterior masonry or brick walls.
All these changes yield a building that code development organizations deem acceptable for a finished structure. In fact, the allowable height and number of stories for sprinklered residential buildings is the same for Type II (noncombustible) buildings. However, during construction, when fire protection systems and features are not installed or not in service, the stage is set for a significant, fast-moving fire that can be beyond the capabilities of fire departments to stop, even in resource-heavy metropolitan areas such as where this fire occurred. This is where codes that address the construction phase come into play, primarily National Fire Protection Association (NFPA) 241, Standard for Safeguarding Construction, Alteration, and Demolition Operations, which is a mandatory reference in NFPA 1, Fire Code. The International Building Code contains similar provisions.

(10) The steel-piped sprinkler system in the attic of the unburned west section of the building. (Photo by Mat Chibbaro.)
Fire Apparatus Access
Apparatus access in a finished building is typically dictated by a balance of building size and the percentage of accessible perimeter. Under the concept of “frontage increase,” the individual building can be larger if there is an increase in the percentage of perimeter accessible to fire apparatus. Conversely, fire wall separations can reduce the building’s size and thereby reduce the amount of fire apparatus access needed.
The fire apparatus access required during the construction stage can be more stringent. NFPA 241 requires all-weather perimeter roads within 150 feet of the remote point of the first-floor perimeter. The Fuse 47 building had more than 700 feet of perimeter without approved apparatus access roads (photo 9).
Sprinkler Systems
The sprinkler systems in the Fuse 47 building were installed and hydrotested, but the floor control valves were in the closed position. NFPA 241 requires that sprinkler systems be in service “as soon as practicable.” The common practice is to keep the sprinkler valves closed until the water flow alarms are in service to provide notification of water flowing.
At the Fuse 47 fire, the sprinkler systems’ status was unknown to the fire suppression forces. As such, valves were left shut so as not to divert water from the manual suppression effort. If the fire department had known that the systems were intact, they could have opened the control valves during the incident to help gain control of the fire. In particular, the attic sprinkler system with steel piping (photo 10) would have remained effective in the fire’s early stages. Formally notifying the fire department that the sprinkler systems were operational, advising it early in the response or posting signs on the sprinkler valves to that effect could have made a significant difference in the fire’s outcome.
The FDC was on side A inside the perimeter security fence, resulting in a small delay in accessing it. However, some jurisdictions prefer or require that FDCs be outside fences to meet the NFPA 241 requirement that they be “readily accessible.” Also, although the Fuse 47 building was code compliant with a single FDC, it is a single potential point of failure. Falling debris at this fire became an issue, and hoselines had to be protected with covers.
Standpipe Systems
The building’s standpipe system was also installed and hydrotested, but several control valves were closed at the time of the fire. When personnel became available, they located and opened the riser isolation valves. A nonrequired control valve in the bulk main downstream of the FDC and the fire pump was also found closed and then was opened. The FDC was then able to supply all standpipes, but this occurred long after the east side attic was lost. The delay resulting from having to backfeed the standpipe during the initial interior attack may have been when the fire spread into the attic.
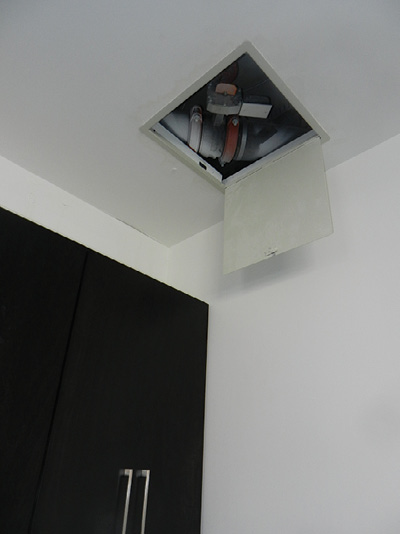
(11) A standpipe riser isolation valve above a small unmarked access panel. (Photo by Mat Chibbaro.)
Building codes and NFPA 241 require that at least one standpipe riser be in service during construction. Although all risers were shut down during this fire, having one riser in service at one extreme end of a building meets the minimum requirement. In such a scenario, the standpipe system may be of no use for a fire on the opposite side of the building because of the excessive hose lengths needed. There is no reason all standpipe risers can’t be in service as soon as they are hydrotested.
The locations of the Fuse 47 standpipe riser isolation valves made them hard to find and access (photo 11). Rather than locating them within the stairway, where they would be accessible and protected, they were above unmarked ceiling hatches in nearby rooms. It is crucial that all valve locations be clearly marked and quickly accessible to firefighters. Valves feeding stair risers are best located within stairways. Valves feeding other risers should be clearly marked and accessible from corridors.
The larger a building footprint, the longer the hoselines needed to reach the remote point from the single riser. A code change in the 1990s increased the maximum travel distance before remote hose connections are needed outside stairs. As the Fuse 47 fire spread, firefighters needed multiple standpipe packs and dead load hose to extend hoselines from several hose outlets on various levels in the east stairway.
Typically, in a fully sprinklered building, the total required standpipe design flow is reduced. Both stairway standpipes were pushed beyond their design limits at the Fuse 47 fire—the east riser during the interior attack and the west riser during the trench cut operation. The Fuse 47 fire demonstrated that this fire safety trade-off breaks down during construction before sprinkler systems are in service.
Other Features
NFPA 241 contains many other provisions designed to help prevent incidents, minimize damage, and assist the fire service during incident operations. The main focus is establishing a fire safety program and designating a program manager. The manager has several key roles related to on-site safety, security, and coordination with the fire service. One program requirement that was a factor in the Fuse 47 fire was ready access to a telephone to prevent a delay in fire reporting.
Another critical firefighter access feature that NFPA 421 requires is at least one stairway be provided as the building rises. The stair must be lighted, have identification signs at each level, and be enclosed as the building exterior is enclosed.
A new edition of NFPA 241 is expected in 2018; it contains several improvements. If approved as proposed, they include temporary sprinkler protection, designated cooking areas, and provisions specific to tall timber buildings. Future editions of NFPA 241, building codes, and fire codes hopefully will take into account the lessons learned in the Fuse 47 fire as outlined below.
Preincident Planning
The Fuse 47 fire highlighted the following considerations for preincident planning firefighting in a large, tall combustible building under construction.
• Create relationships with permit and inspection authorities, developers, and general contractors.
• Understand all phases of construction and the fire protection system installation.
• Building heights can approach the high-rise threshold and can require high-rise tactics.
• Fire crew safety is paramount, especially after construction workers are evacuated or rescued.
• Expect the unexpected in buildings in their incomplete stage.
• Plan the need for a significant water supply.
• Plan for alternatives to standpipe systems.
• Fire-rated roof/ceiling assemblies can shield fire from above and impede access from below.
• The structure’s height can limit aerial master stream reach.
• The weight of water becomes an issue over time.
Enforce NFPA 241
Proactively enforce the following required NFPA 241 provisions during construction:
• Provide a fire safety program with a designated program manager.
• Provide apparatus access within 150 feet of the remote point.
• Provide access to hydrants and FDCs.
• Equip stairways with lighting and signage.
• Enclose stairs when exterior walls are in place.
• Put sprinkler systems in service as soon as practicable.
• Ensure at least one standpipe per building is in service.
• Exterior trash chutes must be noncombustible or sprinklered.
Future Fire Code Improvements
Consider improving or amending the fire codes when adopted with the following provisions:
• Require fire department notification and appropriate signage when sprinkler systems have been tested and valves are available to be turned on during incidents.
• Place all standpipe risers in service after testing.
• Locate standpipe riser isolation valves in stairway corridors for rapid access.
• Require a backup hose connection or an additional FDC on standpipe systems with pressure-reducing valves (which cannot be backfed).
• Prohibit the installation of extra shutoff valves that are not required by code.
Building Reconstruction
As of February 2018, the entire Fuse 47 building was demolished above the podium. The reconstruction has begun with some fire safety improvements. The entire standpipe system will be installed as the building rises and will remain in service. As sprinkler zones are hydrotested, they will be placed in service, fed by a temporary preaction valve. These steps and others that exceed the code requirements will provide improved fire protection and assist firefighters. They also represent some additional ideas for code development organizations to consider as improvements (photo 12).

(12) The Fuse 47 building reconstruction above the podium. (Photo by Mat Chibbaro.)
BILL CORRIGAN is a life safety manager with the University of Maryland and chief of the College Park (MD) Volunteer Fire Department, which serves the main University of Maryland campus and surrounding areas. He has served 24 years in the volunteer fire and rescue service and was the incident commander for the Fuse 47 fire.
MAT CHIBBARO is the deputy fire marshal for the National Institutes of Health and a life member of the College Park (MD) Volunteer Fire Department. He is a licensed professional fire protection engineer in California and in Maryland. Chibbaro has 37 years of experience in fire code application and enforcement and has served 44 years in the volunteer fire and rescue service. The opinions he expresses in this article are his own and do not reflect the view of the National Institutes of Health, the Department of Health and Human Services, or the United States government.