
By Len Garis and Karin Mark
Wood construction is reaching new heights around the world, and we can expect to see the same in the United States thanks to anticipated changes in legislation and building codes. The trend might make some fire service professionals shake their heads: high-rises constructed from a combustible material?
On closer inspection, however, we can see that this new class of high-rise is a distant relative of the typical wood construction methods seen in modern mid-rise or low-rise buildings. In fact, these towering hybrid wood structures can be built to be as safe as and, in some respects, safer than other types of construction.
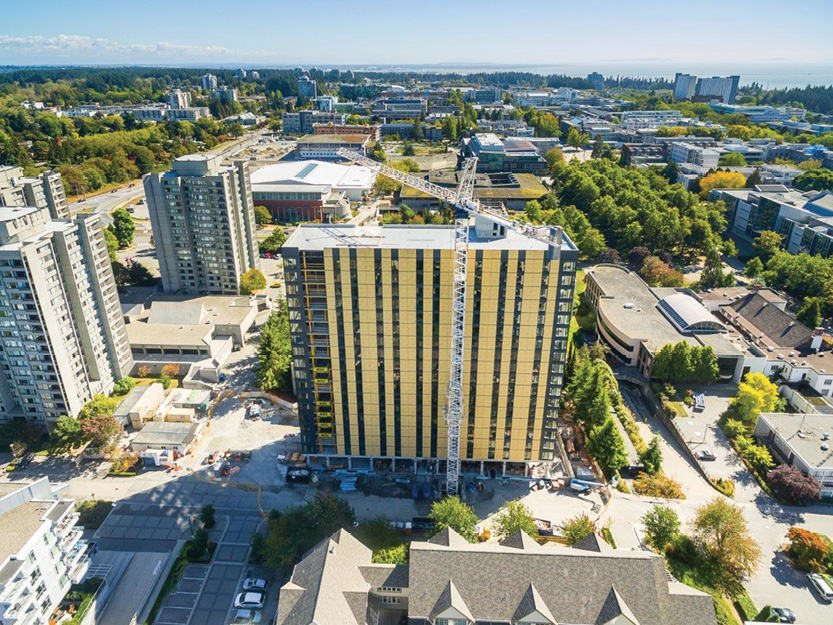
(1) The world’s tallest mass timber building opened this past summer in Vancouver, Canada. What does the tall wood trend mean for the U.S. fire service? (Photos 1-5 courtesy of Naturallywood.com; photo 6 courtesy of the American Wood Council.)
A prime example is Brock Commons Tallwood House, a 173-foot-tall, 18-story student residence at the University of British Columbia (UBC) in Vancouver, Canada. As of the time of this writing, it is the tallest mass wood building in the world. The building, which opened this past summer, consists of 17 stories of mass timber atop a one-story concrete base. Two concrete cores run the full height for elevators, stairs, and service conduits. The building will house 404 students in 272 studios and features 33 four-bedroom units.
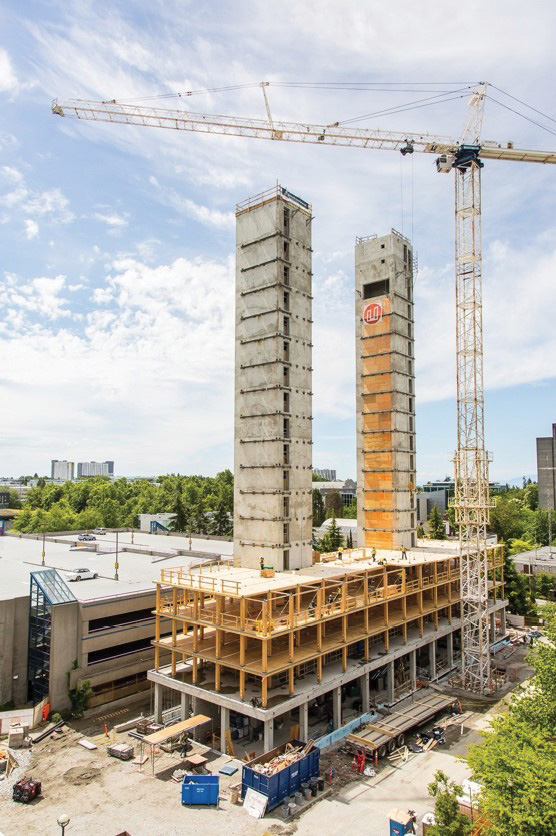
(2) The concrete cores rise above the floors of the Brock Commons Tallwood House, constructed in 2016.
Mass Timber Construction
Mass timber construction differs from its traditional wood-frame relative, which is often comprised of 2× wood members. Mass timber uses solid and “massive” wood products, combinations of large panels made of cross-laminated timber (CLT) or nail-laminated timber (NLT) for floor and wall framing, and glue-laminated timber (glulam) for columns and beams:
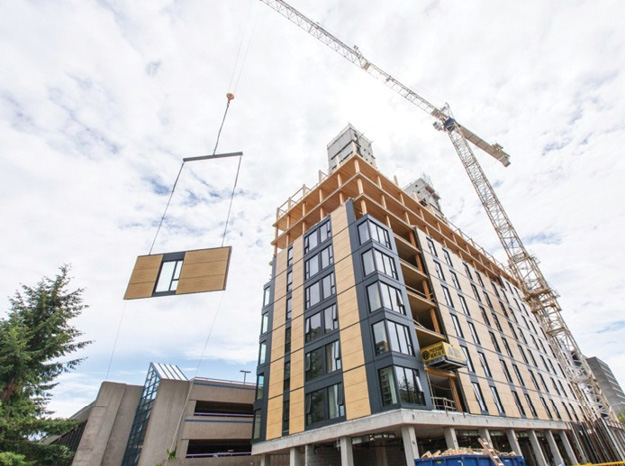
(3) A cross-laminated timber panel is lifted into place.
- CLT panels are constructed of layers (typically three, five, or seven) of dimensional lumber or similarly sized wood products. Each layer is oriented at right angles to the adjacent layers and bonded together.
- NLT panels are created from dimensional lumber (such as 2×4s, 2×6s, or 2×8s) stacked on edge and fastened with nails or screws.
- Glulam timber is composed of bonded dimensional lumber; all layers run in the same direction and are parallel to the beam’s length.
Mass timber has natural fire resistance and structural integrity that have been proven through scientific testing. In a demonstration in Quebec, Canada, in 2016, a compartment was built with five-ply CLT panels protected with gypsum wall board and then set on fire. Even with peak temperatures of more than 2,000°F, the fire was contained to the compartment and burned itself out in two hours except for some glowing coals.Similar results are expected from fire tests this year on a multistory mass timber structure at the Bureau of Alcohol, Tobacco, Firearms and Explosives lab in Maryland. The tests are sponsored by the U.S. Department of Agriculture.
Like many of the other mass timber high-rises going up around the world, the Brock Commons project blends a variety of building technologies and materials. The hybrid system includes prefabricated 6.7-inch-thick five-ply panels of CLT and glulam columns with steel connectors encapsulated in gypsum board and topped by a steel and metal roof. The exterior is clad in decorative wood fiber high-pressure laminate panels.
In addition to these fire-resistant materials, built-in fire safety measures include the following:
- The project required a site-specific regulation (SSR) because it exceeds the six-story limit for wood construction in the British Columbia Building Code. The SSR’s fire and seismic standards surpass those for steel and concrete buildings, and they also restrict building uses to primary residential; limited-occupancy occupancies are permitted in the concrete first story—a student lounge but not a restaurant or retail, for example.
- Three layers of 5⁄8-inch Type X gypsum board cover every mass wood ceiling and column surface on the stories with the living units.
- The floors are topped by a layer of concrete.
- The building is fully sprinklered and has a backup water and electrical supply.
- The building has a highly compartmentalized design and no combustible concealed spaces, minimizing the risk of fire spread.
The building’s structural components achieve a two-hour-plus fire rating, as is required for any building of this height in British Columbia. One of the project consultants, Canadian building code and fire engineering specialist Andrew Harmsworth, said at a recent workshop at the UBC that the extremely conservative approach was intended to deal not only with real risk but also the perception of risk. “The building had to be equal to or better than a noncombustible building, and I’m satisfied it is,” he said at a Timber Pre-Fabrication Construction Workshop held in November by the Canadian Wood Council’s Wood WORKS! Program.
In addition, the panelized building method meant the construction site was clean; there was little hot work; and the building structure and envelope went up quickly, in 66 days, an average of two stories per week.
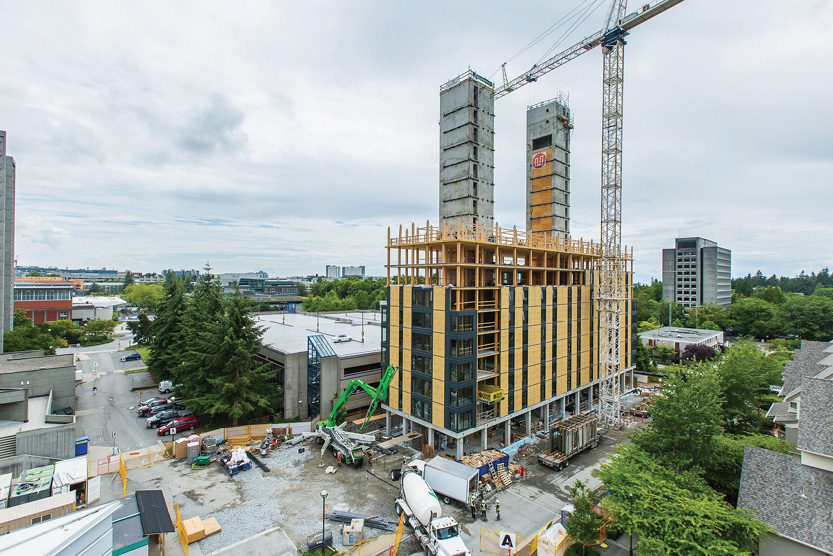
(4) The prefab building method used for mass timber made it possible for the Brock Commons building structure and envelope to go up in fewer than 70 days, an average of two stories per week.
The ultra-conservative approach to fire protection may help ease concerns about this type of construction, but research shows that typical fire safety systems already offer superior protection, regardless of building material.
A 2016 study of 42,700 residential fires in British Columbia conducted by the University of the Fraser Valley (UFV) between 1988 and 2015 showed that most fire deaths happened in buildings without adequate fire safety measures. The study examined all residential occupancy types and found that 85.4 percent of the 512 fire fatalities occurred in buildings without working sprinklers and smoke alarms. It further found that buildings with working sprinklers and smoke alarms required less fire department intervention (22.4 percent vs. 54.8 percent) and had more instances of the fire being contained to the room of origin (92 percent vs. 59.7 percent).
This confirmed the results of a 2014 UFV research study that demonstrated that wood-frame buildings are as safe as steel or concrete buildings once fire safety systems are in place. “Fire Outcomes in Residential Fires by Construction Type” examined almost 12,000 building fires reported in British Columbia between 2008 and 2013 and found no deaths and similar injury rates from fires in buildings with working sprinklers and smoke alarms regardless of construction type. Fire spread was also remarkably similar: Most fires in all construction types were confined to the room of origin.
The Future of Wood
Mass timber prefab systems are driving up building heights in demonstration projects around the world. Brock Commons Tallwood House is slightly taller than the 14-story timber-framed apartment building in Bergen, Norway, which previously held the record as the world’s tallest wood building at 52.8 meters (173.2 feet). Before that, a 32-meter-tall (105-foot) apartment building in Melbourne, Australia, held the record.
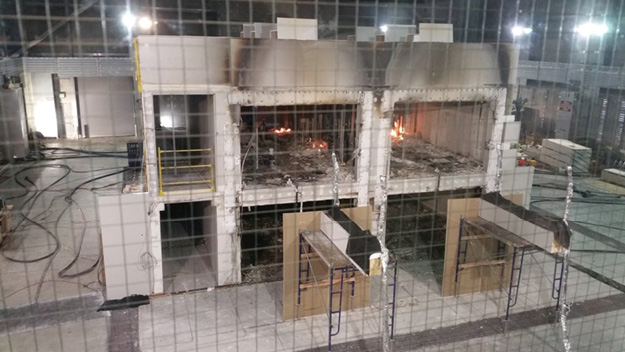
(5) During large-scale fire testing of mass timber, little fire remains within a two-story CLT structure that withstood a nearly 20-MW peak fire exposure for four hours. For the test, contents were placed and ignited only in the second-floor, one-bedroom apartment. In each room, an 8- × 10-foot portion of the CLT ceiling was left exposed. The remainder of the mass timber surfaces were protected by two layers of 5⁄8-inch Type X gypsum wall board.
Although there is a growing interest in tall wood construction in the United States, the enabling codes and legislation are proceeding at a more cautious, deliberative pace than in other parts of the world, according to Robert Glowinski, American Wood Council (AWC) president and CEO.
In the United States, work began last year for a submission to include provisions for taller wood buildings in the 2021 International Building Code. The International Code Council’s Tall Wood Building Ad Hoc Committee consists of code officials, stakeholders, and other interested parties (including fire service representatives) who are studying tall wood construction and developing recommendations for code changes in time for the January 2018 deadline. Research being conducted for the committee includes the large-scale fire testing in Maryland noted earlier.
In January 2018, construction is slated to start on what will be the tallest all-wood CLT building in North America: the 148-foot, 12-story Framework mass timber demonstration project in Portland, Oregon. The project was a winner in the 2014 U.S. Tall Wood Building Prize competition sponsored by the U.S. Department of Agriculture, the Softwood Lumber Board, and the Binational Softwood Lumber Council.
Fire tests in 2016, funded by the $1.5-million prize, found CLT panels fully complied with building code requirements for flame spread and fire rating; the glulam beam-to-column connection achieved a two-hour fire rating that exceeded results conducted anywhere in the world. Framework was approved through the alternative means approach recognized by the code for projects that can demonstrate equivalent performance.
The special permitting process is similar to that used for Canada’s tall wood projects, including Brock Commons and a 13-story, 134-foot residential building under construction in Origine, Quebec. Changes to Canada’s codes may come faster than in the United States, however, since encapsulated mass wood timber construction of up to 12 stories is being considered for Canada’s 2020 National Building Code.
While regulations catch up with practice, the AWC’s Glowinski noted that the United States is “marching inexorably” toward tall wood being recognized as a building material option. He urged members of the fire service to learn more about mass timber and how it differs from traditional wood construction. He noted that U.S. building officials who visited the Brock Commons project when it was under construction came away with a very positive impression. “It’s important to realize that mass timber is very different from traditional wood construction,” explains Glowinski. “When you think of wood construction, what comes to mind is the traditional 2×4, 2×6 platform construction. However, when people see mass timber buildings under construction and going up, they get a very different understanding.”
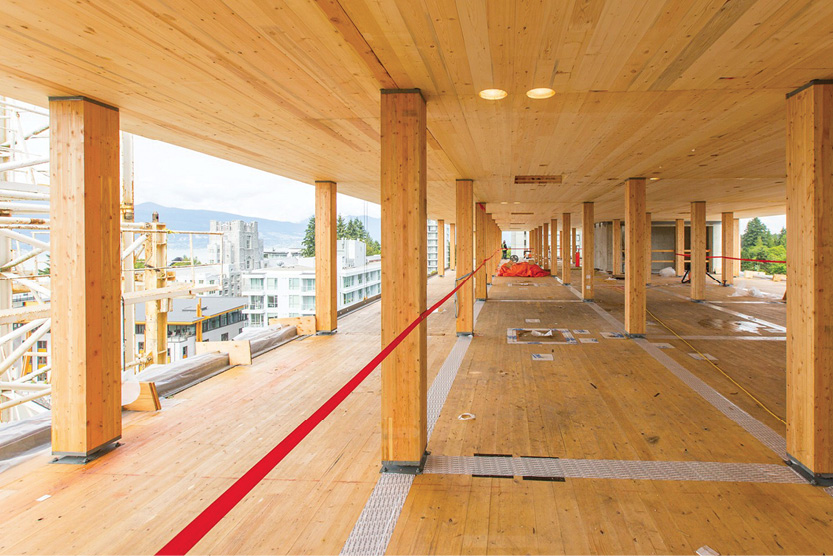
(6) During construction of Brock Commons, only six stories at a time could be constructed before the exposed timber was encapsulated with gypsum board.
Vancouver Fire and Rescue Services Perspective
The Vancouver Fire and Rescue Services (VFRS), a career department with approximately 800 members, took some time to adjust to the news that an 18-story tall wood building was going up at the UBC. Assistant of Community Safety Chief Ray Bryant put it bluntly: “When I first heard the building would be 18 stories, to be honest, I thought it was an insane idea.” He then learned more about the project and mass timber construction and now says, “I can’t believe how safe it is.”
VFRS management was introduced to the Brock Commons Tallwood House project early on and was involved in the initial approval process. After the SSR was in place, a robust Construction Fire Safety Plan (CFSP) was developed (discussed below).
While that work was in progress, word of the project spread through the rank and file and was met with varying degrees of concern, in part because of the assumption that Brock Commons would be the same “stick-built” construction as mid-rise wood-frame buildings and would put firefighter lives needlessly at risk. “There was fear and misunderstanding among the firefighters,” says Acting Training Officer Martin Rusticus. “We knew we needed to address those concerns.”
An educational presentation was made at the department’s fall captains’ meeting in November 2016; the presentation was captured in an e-learn video that became required viewing for all VFRS members. The education made a difference. Following the training sessions and viewing of the video, Rusticus noted, there was a greater understanding that “because of the built-in safety measures, it’s actually safer than some of the other projects.” Members were also impressed by the redundancies of the fire safety measures and the cleanliness of the construction site because of the prefab methods. “They’ve sealed every floor and every compartment. If a fire does start somewhere, it will not spread beyond the compartment,” notes Chief Training Officer Chuck Stanford.
Bryant agrees: “I would call this extremely safe from a fire perspective. It’s a very safe building, once completed.” He adds that during construction, it was safer than a stick-built mid-rise building.
But what about after the building is occupied? Assistant Chief Scott Morrison, who leads the department’s captains’ meeting, says a common concern he’d heard was the potential for interior changes that could compromise the building’s fire safety in the future. “It’s tough keeping track of whether they will create poke-throughs and change things on the inside. The concern, moving forward, is that it keep its integrity,” he explains. Building changes undertaken without obtaining the proper permit is a problem in many cities, Morrison notes. “That’s why we’re still in business—human error, that kind of thing.”
At the UBC, its building department has jurisdiction over issuing building permits and has been overseeing the Brock Commons project since the concept stage. The UBC’s Chief Building Official Edmond Lin doesn’t anticipate any work will take place at Brock Commons without a permit, given that the building is owned and operated by the university and that students are unlikely to make major changes to their rooms. “The fact that it’s a consistent owner that obviously has the objective of making sure the building is safe helps a lot in terms of the overall fire safety of the building,” says Lin. “Unlike the city, where you may have owners that perhaps have less focus on this.”
In terms of fire safety inspections, Bryant said Brock Commons will join the annual rotation with Vancouver’s other high-rise residential buildings. No unique provisions will be in place; the building will be treated like any other fully sprinklered high-rise. Like other new buildings, Bryant says the most intense focus will be in the first few years as the department watches to see how well the owners continue to comply with fire regulations. As the department moves toward risk-based inspections, the track record and built-in fire safety provisions will be evaluated to see if a different inspection schedule should be considered.
Fire Chief John McKearney, who was at the table during the building’s early approval stages, says he understands why firefighters may initially have concerns about tall wood buildings before they are fully educated about them, considering the fire service’s long history of battling fires in wood structures. “There’s definitely a learning curve. The fact is that mass timber buildings cannot be compared with typical wood construction,” McKearney says. “From a fire standpoint alone, the building’s fire-resistant materials, sprinklers, and layering of fire protection systems will make Brock Commons one of the safest buildings in the city.”
The CFSP
The VFRS worked with the UBC to create a robust CFSP for the Brock Commons Tallwood House student residence. The CFSP treated the project like a high-hazard construction site; key among the requirements was to limit exposed timber to six stories at a time before the mass timber was encapsulated with gypsum board. Plan approval was required before construction could begin, as is the case now with mid-rise wood-frame buildings in Vancouver. Measures included the following:
- Special attention was paid to ensure standpipes were installed progressively during construction. Per the B.C. Building Code and Vancouver Fire By-law, functioning standpipe and hose valves were required no more than one story below the level under construction.
- The contractor was required to provide an air or water gauge at the fire department connection point to ensure the system is ready for use. Positive pressure in the gauge will indicate that the piping system is closed, with no open valve or missing fitting. These gauges are also required for mid-rise wood-frame construction in Vancouver.
- Although the stairs are encased in concrete, temporary fire doors with a latching mechanism were also required to be installed progressively as the building rose.
- An on-site 24-7 security presence was required, with roving security after hours. Cameras were not permitted as a substitute.
- A site attendant was required to ensure the CFSP was being adhered to.
- Hot work permits were required for the limited hot work that took place.
As is necessary for any project of this size, the fire department had access throughout the construction and the occupancy permit stage. Orientations were also conducted for suppression crews at the two nearby responding fire halls so members could become familiar with the building and fire protection systems.
Lessons Learned
- Get your training in place as early as possible. “We could have done it earlier. Having gotten ahead of it, we might have quelled a lot of fears,” Stanford says. “After you see the training video and how it’s built and the fire safety measures in place, you have a much higher level of comfort.”
- Having a comprehensive CFSP with fire department sign-off is critical to both ensure site protection and alleviate concerns, says Assistant Chief and Fire Protection Engineer Rick Cheung. “Let’s put it this way. We had more comfort after a good CFSP was in place, and the method of construction and housekeeping on the site also provided a good deal of comfort.”
- Bryant noted that a good working relationship with the developer and site personnel also makes enforcement of CFSP provisions easier. “Get involved early, and work with the developers,” he suggests. “We inspected the building regularly and watched them build it, and we even got to know the workers on a first-name basis. It helped.”
References
• Large Scale Fire Demo video (tall mass timber building in Quebec, Canada): http://cjr.ufv.ca/videos/
• American Wood Council’s construction fire safety site: www.constructionfire.com
• reThink Wood: www.rethinkwood.com/tall-wood-mass-timber
• Tallwood Design Institute: http://tallwoodinstitute.org
• Vancouver Fire & Rescue Services training videos: http://cjr.ufv.ca/videos/
• University of the Fraser Valley reports quoted in this article: http://cjr.ufv.ca
Len Garis is the chief for the City of Surrey, British Columbia; an adjunct professor in the School of Criminology and Criminal Justice; and an associate to the Centre for Social Research at the University of the Fraser Valley. He is a member of the Affiliated Research Faculty at John Jay College of Criminal Justice in New York and a faculty member of the Institute of Canadian Urban Research Studies at Simon Fraser University.
Karin Mark, based in Metro Vancouver, British Columbia, is a former award-winning newspaper reporter who writes for publications and corporate clients and provides graphic design and other communications services.
Related training:
http://emberly.fireengineering.com/articles/pt/2017/03/report-no-timber-high-rise-for-nyc.html