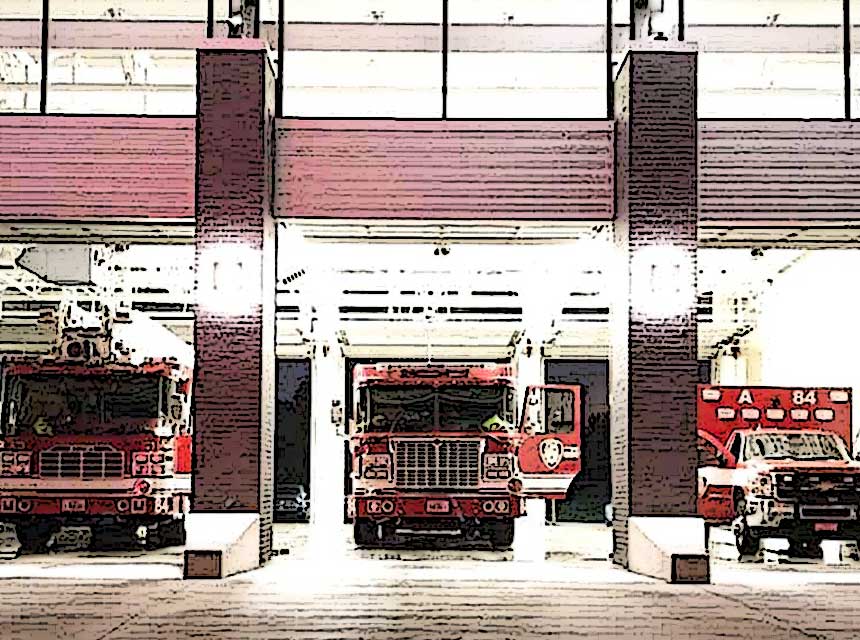
By Ruy Lozano
Prior to COVID-19, supply chains for personal protective equipment (PPE) for the third-largest municipal fire department in the country were predictable. Our economies of size gave the Houston (TX) Fire Department a strategic position with vendors that allowed not only preferential pricing but priority in product allocation.
Most city contracts are for three years with the possibility of a two-year extension. During that time, you could carefully renegotiate terms, ensuring your fiduciary responsibilities with your stakeholders (taxpayers). This process, although considered arduous, ensures quality control of products and terms that were protective of the city’s interest. Contracts would take several months to negotiate and the checks and balances in the city would ensure that we abided by purchasing laws and reduced the opportunity for impropriety.
RELATED FIREFIGHTER TRAINING
COVID-19: New Tools for a Different Type of Response
Fire Department Response to Healthcare Facilities During the COVID-19 Pandemic
COVID-19 and Its Psychological Effects on Firefighters and First Responders
When the pandemic became a global reality, the processes of the past became the obstacles of today. When disruption occurs, as logistic leaders, we must sound the alarm. Being able to clearly communicate new barriers to financial decision-makers is not only prudent but table stakes.
Re-establishing Your Demand
In any firm, the goal is to know your demand and limit your capacity to that demand. Any excess capacity becomes waste it must be eliminated to compete in today’s markets. Unfortunately, years of lean applications have become a challenge when a significant surge erupts. PPE for example was a normal inventory item for any major metropolitan fire departments. Unofficially, gloves were the industry standard for prehospital body fluid isolation among first responders unless there were indicators such as dispatch information that stated that the call could involve blood splatter or a preidentified contagious infectious disease risk. This resulted in exceedingly low burn rates for eye protection, face masks, and gowns. With perpetual stocktaking, most agencies’ inventories for certain PPE items were far below what should have been inventoried. The low industry burn rate traveled upstream to manufacturers as they established capacity.
COVID-19 shifted the demand curve to the right, creating scarcities with markets unable to meet demand. For the initial two to three months, it seemed everyone was trying to take advantage of market opportunities. Promises by new entrants were made with few able to deliver. Established manufacturers could not retool their warehouses and plants quickly enough to meet the insatiable demand and lead times increases from one to two weeks to two to three months.
Meanwhile, first responders on the front line are concerned about the level of protection their agencies are able to provide. The surge in demand for the use of all PPE (gloves, masks, gowns, and eye protection) thrust logistics to the forefront in the COVID response models for most healthcare and government agencies. A growth mindset during disruption separates an effective logistics leader from one dwarfed by the moment. Being able to quickly adopt or establish new purchasing processes, pursuing off-contract leads to potentially available PPE, and making the case for purchases of opportunities is critical.
Speed became a true measure of success in logistics. Many products during the pandemic are only available for hours or minutes before another more nimble agency secures the product. An open checkbook does little when purchasing protocols become speed bumps in a rapid transaction environment and national strategic stockpiles are found inadequate to meet newly established burn rates.
Quality Control
Consolidation of all PPE purchases must be married with strong quality control. Like many cities, consolidating your procurements adds weight to your economies of size. Making a citywide purchase for quantities in the millions will bring significant vendor attention as opposed to the hundreds or even thousands of units at the department level. The only challenge is ensuring your buyers are aware of PPE performance expectations.
Consider a gown’s performance expectation for a person taking temperature readings as you enter a temperature-controlled building as compared to that of a paramedic who will be performing CPR in that back of a moving ambulance. Having a clear line of communication with buyers and well documented PPE specs is essential when working with a cross-departmental procurement team.
In the COVID era of market disruptions, a growth mindset when positioning your agency’s strategic intent adds leadership value to your decision-making model.
Ruy Lozano is the assistant fire chief for the Houston (TX) Fire Department in charge of public information/logistics. He has an executive MBA from Rice University. He manages the department’s social media messaging and served as the public information officer and logistics officer for local and national disasters, including Hurricane Harvey and the COVID-19 pandemic.