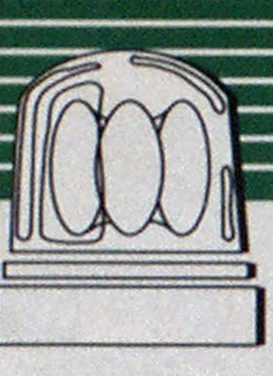
VEHICLE MAINTENANCE
VOLUNTEERS CORNER

A potential major problem for many fire departments is the inability to keep apparatus properly maintained and ready to respond. This problem is especially prevalent in departments that do not respond at least weekly. Infrequent use can lead to conditions, such as the drying out of valve seats and pump packing, that can affect vehicle efficiency. Apparatus not regularly maintained may fail to start, break down en route, or fail to function properly on the fireground. In many cases, regular maintence is not done because personnel do not know what to do or the rate of personnel turnover is high.
(iood leadership entails delegating maintenance responsibility to a qualified officer who will establish and implement at least a simplified prevention maintenance (PM) program that includes measuring fluid levels, checking the air system, and inspecting for leaks. Such a policy will alleviate numerous problems for the department (and sleepless nights for the chief)-
An established PM program also will eliminate solo maintenance by individual self-proclaimed experts, the ‘Til fix that, 1 weld ’em all the time” set. If a department not have trained personnel to regularly work on its apparatus, it should consider an outside maintenance contract for services beyond minor maintenance. Major pump and component manufacturers can recommend reliable maintenance companies.
COMPONENTS OF A MAINTENANCE PROGRAM
A good maintenance program in larger departments entails having on-duty personnel perform daily apparatus checks; in smaller departments, at least weekly checks should be scheduled.
Among other recommendations for developing an apparatus maintenance program are the following:
- Thoroughly inspect the apparatus after each alarm.
- Drive units that have not responded during the week at least 10 miles to ensure road worthiness. A test drive enables the driver to test the steering, braking, and shifting systems as well as heats up the oil to evaporate any condensation.
- Perform more comprehensive PM inspections quarterly, semiannually, and annually. Include a pump service test and aerial device inspection in the annual PM program.
- Have the engine oil of all units analyzed semiannually, in the fall before the first freeze and in the spring before the hot weather.
- The simplest inspection should include checking all fluid levels, belts, tire air pressure, the air system, and battery condition. Many fire departments use check sheets, which are filled out after each inspection and kept on file to establish a maintenance history for each unit.
- Exercise pump and hydraulic systems, such as those for operating the aerial ladder and valves or ladder racks, weekly.
- Institute procedures for inspectors’ reporting to individuals in authority situations that need immediate repairs. Also, develop a policy for taking a vehicle suspected of being unsafe out of service. Personnel should be instructed to notify the individual responsible for maintenance and make a
- written notation if a problem is suspected.
- Each time a unit is driven, the operator should be aware of how the entire unit is functioning. After an emergency response, making a shake-down drive can help determine existing problems when symptoms or malfunctions are suspected. While performing the test drive, check the steering linkage and vehicle alignment. How are the bushings in the steering mechanism? Telltale signs of trouble are dead spots in the steering, clunking, and excessive play in the steering wheel.
- Check apparatus electrical systems on a regular basis—before a serious problem develops. A landor chassis-based battery monitoring or charging system may have to be installed. Conduct an electrical analysis that determines total electrical use before a serious problem develops. Also, consider the following: Have electrical draws been added, and has the system become overloaded since the apparatus was delivered? Can the alternator keep up, or is there a constant drain on the battery when responding with the warning devices activated?
Alternator. Check alternator output annually or if trouble is suspected. A good time to do this is during the annual pump service test. The alternator should be checked with all warning lights and auxiliary electrical systems operating to stress-load the alternator as it would be when used during an emergency. The electrical draw can then be balanced with the alternator output. Since some newer-model diesel engines shut down on low voltage, the use of electrical output may have to be limited and should not rely on the battery as a working source. Otherwise, the battery could become discharged and cause the engine to die during an emergency. If the engine has a separate dedicated battery to address this situation, it should be added to the maintenance checklist. Another possible solution for an overloaded electrical system is to establish an on-board portable generator or alternator that can run some of the warning lights or nonpriority electrical accessories independently. This procedure will relieve the alternator and stop any drain on the battery.
Battery. Check the specific gravity and electrolyte level of the battery at least weekly. While doing this, check the tightness of the battery cables, remove any excessive terminal corrosion, and observe the overall condition and cleanliness of the battery box. Even with sealed batteries, the cable connections and cleanliness must be checked. This is also a good time to inspect the condition and adjustment of the fan belts.
- Check the brakes to see that the vehicle stops within recommended distances; if not, the brakes may have to be adjusted or replaced. Keep in mind, however, that some brake fade is normal after a run with numerous stops. Check for leaks in the air-brake system, condensation in the tank bleed-off, and the bleed-down time. Washing tires, wheels, or wheel-well areas with cold water while the brake drums or disks are hot could damage metal components.
- Is the transmission shifting properly and at the correct rpms? Is it time to change the transmission fluid and filter or to make adjustments? Are there leaks in the transmission or differential? Have the driveline bolts been inspected and torqued according to the manufacturer’s recommended specifications? This is especially significant when the pump packing drippage falls on the front companion flanges in the drivetrain. This driveline problem will cause rust and premature bolt failure. Are the bolts the correct hardness?
- The cooling system is another major area often overlooked. Do not run plain water in the system; it is not good for the engine or the radiator. Maintain the proper coolant level with a good water conditioner/antifreeze product. Use enough to protect the system to the lowest possible temperatures in which the vehicles will operate. Inspect the belts and hoses connected with the cooling system, especially the small heater hoses, which are susceptible to heat. Replace older hoses with the new silicon type. Watch for leaks in the system.
- Since the fire pump is the heart of the fire apparatus, all its components should be included in quarterly maintenance. Operate the pressure-regulating devices (both on the intake and discharge sides of the pump) and the changeover valve, if one is provided, weekly. Check all hose gaskets and lubricate threads. Clean quarterly all strainers (including the one on the right side of the pump). Test gauges at least annually, during the
- pump test, and alter any repair. They may require recalibration. The master drain is at the lowest part of the pump; often it collects grit or dirt. This dirt can block a drain line and in freezing weather possibly damage the pump, drain line, or valve. Trained personnel should disassemble and clean it semiannually or anytime a problem develops. While pumping, monitor the transmission lockup. Is it holding properly, or is it allowing the transmission to drop to a lower gear, decreasing pump discharge pressure? If this happens during an emergency, keep the rpm’s at a higher rate and continue operating. This will not damage any components, and repairs can be made after an incident has been concluded. The department may wish to install hour meters on the pump panel and in the cab to record pump time and engine hours (idling, driving, and pumping total) necessary to establish pump and motor lubrication schedules.
Many areas need constant maintenance to ensure the quick response and proper ojieration of a vehicle during an emergency. Also, don’t forget the portable equipment during the scheduled maintenance checks. Engines must start easily and tools must operate properly. With all of these areas in mind, the Apparatus Maintenance Section of the International Association of Fire Chiefs has requested that the National Fire Protection Association (NFPA) develop a document on emergency response vehicle maintenance. This project has been assigned to the NFPA Fire Department Apparatus Committee (developers of the 1900 series of standards), which currently is working on developing a Recommended Practice pertaining to emergency vehicle maintenance.
New apparatus may have a number of items included in the specifications that will enhance preventive maintenance. For those in a purchasing cycle, the book Fire Apparatus Purchasing Handbook by William C. Peters (Fire Engineering Books, 1994) should be a must. Options to consider on new apparatus include large-access doors to the pump, hinged gauge panels, grouping together of fluid-level checks, oil-filled wheel seals, larger alternators, auxiliary braking systems, and conveniently located battery compartments, to mention only a few.
Fire department units must get to the scene to function at the emergency. If your department does not have a good maintenance program, organize one immediately. If you have one in place, make sure it is carried out. Your and your coworkers’ lives, as well as the future of your loved ones, may depend on it.