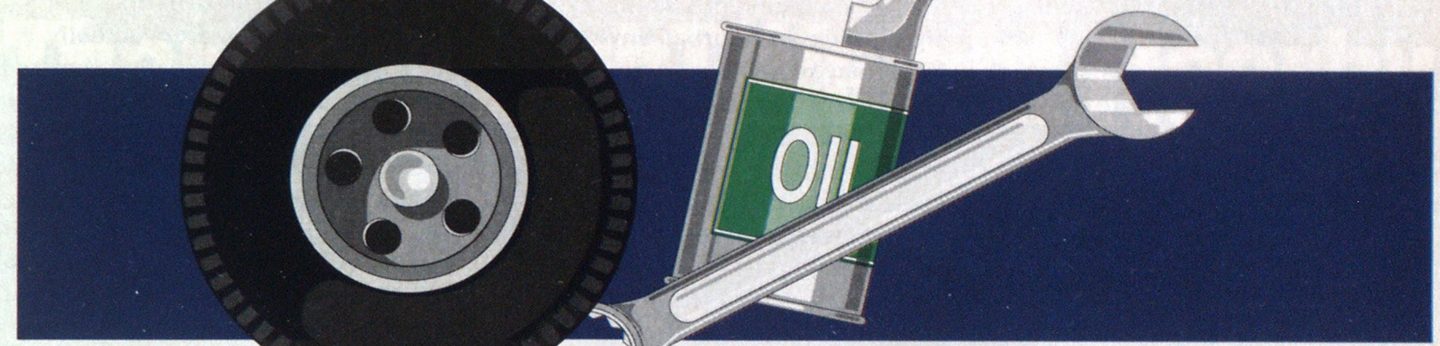
APPARATUS PREVENTIVE MAINTENANCE PROGRAM

A preventive maintenance (PM) program for apparatus may not seem as exciting as the extinguishment of a fire, but it nevertheless plays a vital role in accomplishing our mission of saving lives and protecting property. The critical nature of our service demands that fire apparatus always be in top condition and ready to perform at a moment’s notice.
The safety of the crew and the general public could be significantly affected by the condition of an emergency vehicle’s brakes, tires, and steering and mechanical equipment, which must be maintained according to factory specifications at all times.
A PM apparatus program also helps to extend a vehicle’s working life and protect a major capital investment.
THE OPERATOR
Every PM program, whether it be for the family automobile or the largest fire department fleet, begins with the vehicle operator. Routine maintenance checks of the levels of fuel, oil, and coolant and the conditions of lights, wipers, and warning devices are an absolute must. Observing gauges when the vehicle is in operation and detecting problems by sight and sound also are part of the operator’s maintenance functions.
This first-echelon maintenance phase should be established on a local level and developed with frequency of use, personnel qualifications, and manufacturers’ recommendations as the criteria.
A daily/weekly apparatus maintenance checklist should be available to guide the operator. The program also should include the proper procedures for documenting and reporting serious deficiencies that require immediate attention as well as routine items not considered urgent.
THE SHOP
The apparatus periodically must report to the shop for scheduled servicing. Whether the work is performed by an outside contractor or fire department mechanics, a specific list of required procedures should be followed to ensure that the rig is properly maintained. The manufacturer can help you establish an acceptable program, which is especially important if the unit is still under warranty.
The shop visit should include the following at the minimum:
- complete chassis lubrication.
- oil change.
- filter changes (oil, fuel, and transmission).
- brake adjustment.
- a general safety inspection including tires, front end, driveline, and brakes.
- inspection of belts, hoses, batteries, and air filter.
- a complete general inspection and correction of any deficiencies found such as leaks or worn parts.
Servicing other special maintenance items such as the pump, generator, and aerial device should be included in the program according to manufacturer recommendations.
The shop visit provides the mechanic with an excellent opportunity to examine the operator’s daily reports to detect warning signs such as excessive consumption of oil or coolant, which could indicate a more serious problem.
DETERMINING A SCHEDULE
How often a vehicle should be given a maintenance check depends on the amount of work the vehicle performs in a given period of time. The work can be measured in miles or engine hours or averaged based on calendar days.
Unless the apparatus is used in a rural setting where long responses are normal, mileage is a poor indicator of the apparatus workload. For example, the apparatus might travel only six or eight blocks in an urban environment, but it may pump at capacity for several hours.
The engine-hour system is a better method for determining a proper PM cycle; however, it too has some drawbacks that should be considered. First, if a fleet service program is being considered, all apparatus must have the same type of hour meter so that valid readings can be obtained. Electrical units that measure the actual time the engine runs represent one type of metering mechanism; their main disadvantage is that the readings do not tell whether the unit was idling, driving, or pumping at full bore during the indicated hours.
Another “hour meter” actually is a tachometer that usually registers 100,000 engine revolutions as one hour. This device more accurately measures the work being done by the engine. My experience has been that the readings from a variety of hour meters do not logically correlate so that a PM cycle can be determined.
Another problem that can arise when using the hour-meter system is lack of control over when the units will become due for service. In the case of a fleet consisting of multiple apparatus, this situation creates a scheduling problem for shop personnel and also may affect the availability of reserve units for apparatus being serviced.
A more logical scheduling method is one based on calendar days. Each apparatus in my fleet is serviced semiannually. This gives the shop mechanics five or six units per month to maintain and allows them to schedule other repair work in between. Some fleet managers might feel that the busier companies should be maintained more often than the slower ones, but experience has shown that the use factor eventually evens out. The United States military uses a calendar-day system to schedule maintenance on its enormous fleets of vehicles and equipment.
Staff vehicles are scheduled for shop servicing every 3,000 miles. Because they do not idle or pump as excessively as apparatus, mileage is a fairly accurate measurement of their work output.
MAINTAINING THE SCHEDULE
Marking the calendar may be the only reminder needed to maintain the PM schedule for a small fleet. Scheduling maintenance for larger fleets is easier if a personal computer is used. A simple data-base program that lists the vehicle with a brief description, the month it is due for service, and the two previous servicing dates is adequate. This system instantly indicates the apparatus approaching their PM due dates or overdue for service and provides a view of the entire fleet’s six-month preventive maintenance schedule. The computer printout also can be used as a shop schedule.



(Photos by author.)
Flexibility must be built into the PM program. Occasionally, the PM schedule must be adjusted, such as when too many units inadvertently become due during the same month. This condition could develop over a period of time because of personnel vacations, sick days, or a heavy workload of repairs that causes a backup. When this situation occurs, review the dates of previous service. I nits that were serviced later in the month could have their servicing postponed until the next month without any adverse impact. The adjustments can be made easily on the personal computer.
We use a separate data base to track the mileage of stall vehicles. The odometer reading at the time of PM is logged, and a second entry —consisting of an addition of 3,000 miles— establishes the “miles-due” reading. The current mileage is updated monthly with information contained in a report from each staff section. Any vehicle passing its “due” reading is directed to the shop.
ENGINE OIL ANALYSIS
One method you can use to verify the effectiveness of your PM schedule is establishing a program for routinely sampling the motor oil. When you visit your doctor for a complete physical, samples of your blood usually are taken for laboratory analysis. This diagnostic tool tells your doctor far more about the functioning of your body systems than could be determined from an office examination alone.
The same principle applies to motor oil, the lifeblood of the engine. A proper analysis of the oil can extend the life of the engine by helping the mechanic detect early signs of developing problems. Conditions such as diesel fuel dilution or antifreeze contamination in the oil result in costly repairs and downtime. Discovering and correcting a minor condition early could delay or eliminate the need for a major engine overhaul.
The oil analysis, performed by a laboratory, uses a spectrometer to detect wear elements (metals), additives, and other contaminants such as silicon (dirt). An electrical arc in the spectrometer burns a small quantity of oil. identifies the composition of the sample in less than one minute, and relays the information to a computer terminal for evaluation.
Other physical and chemical testing techniques are used to identify’ contaminants such as fuel, water, and antifreeze. The viscosity and lubricity, a measurement of crankcase deposits and depletion of detergents in the sample, also are determined and recorded.
All test data are entered on the computer and read by a technician, who identifies the possible sources of any abnormal readings and recommends corrective actions that might be taken. This comprehensive report is then sent to the fleet manager.
Reading the report. When the oil analysis report is received by the maintenance supervisor, it should be carefully evaluated. In most cases, the results of a previous sampling, if they are on file, precede the current readout. This comparison indicates whether an original abnormal condition has improved, remained unchanged, or deteriorated.
The severity code is an overview of any problems that may have been discovered in the sample. The laboratory we use rates the vehicle’s status as one of the following: satisfactory (1); moderate, normally acceptable (2); mild/acceptable (3) —units showing moderate wear; moderately high (4) —needs close watch or corrective action; high/unacceptable (5) —unit needs immediate attention, take corrective action or monitor closely; or excessive/unacceptable (6) —critical, must take action before continued use.
If the sample is returned with a severity code of 2 or higher, a summary explaining to the department the conditions and their possible causes is included.


The first group of readings for wear elements (metals) is expressed in parts per million (ppm). Usually a guide showing normal limits of each engine wear metal is supplied. The reports also indicate the origins of the metals: bearings/bushings, pistons, valves, rings, and liners. It should be noted that a new or rebuilt engine usually indicates high wear-metal readings as it breaks in.
The oil contaminants reading is expressed in ppm or percent by volume. Coolants, dirt, water, and sludge also are indicated in this section.
The lubricity code, indicating crankcase deposits and depletion of detergents, is expressed as A (acceptable), P (poor), or B (critical).
Taking the sample. Oil samples can be obtained in two ways. A sample can be secured from the dipstick tube of the engine using a small pump or syringe prior to the end of the apparatus preventive maintenance cycle. The other method requires waiting until the apparatus is in the shop tor scheduled PM. When the crankcase oil is drained, take a sample when about half of the oil is removed from the pan. In this manner, you will get a true sample of the floating contamination.
I prefer the first method of sample taking because the laboratory reports usually are returned in a few days and prior to the time the apparatus reports to the shop for PM service. This method enables the mechanics to investigate the causes of any abnormal or unusual readings indicated in the report. In addition, if contamination is found in a sample taken during a PM, the oil and filters that had just been changed will have to be drained and replaced after corrective measures are taken.
Cost. At the present time, each sample analysis costs between S10 and S20, and if the services of a fieldtesting company are acquired for taking the dipstick sample, a small service charge is assessed for drawing and processing the samples.
Some clients use the results of the oil sampling to extend their service intervals, thus reducing PM costs. This extension is more easily accomplished in a commercial fleet where the truck performs the same routine duties daily. With the unpredictable service cycle of fire apparatus, a regularly scheduled PM program is the best course of action: An engine can never be damaged by changing clean oil.
Transmission fluid and hydraulic oils used in aerial devices also can be analyzed for contamination. Early detection of contamination could be critical in avoiding scored hydraulic pistons and pump failures.
In addition to helping the maintenance supervisor detect problems before they develop into apparatus failures, routine oil samplings can be used to substantiate and justify the cost of a good preventive maintenance program and to demonstrate to taxpayers that their substantial investment in expensive fire apparatus is being protected