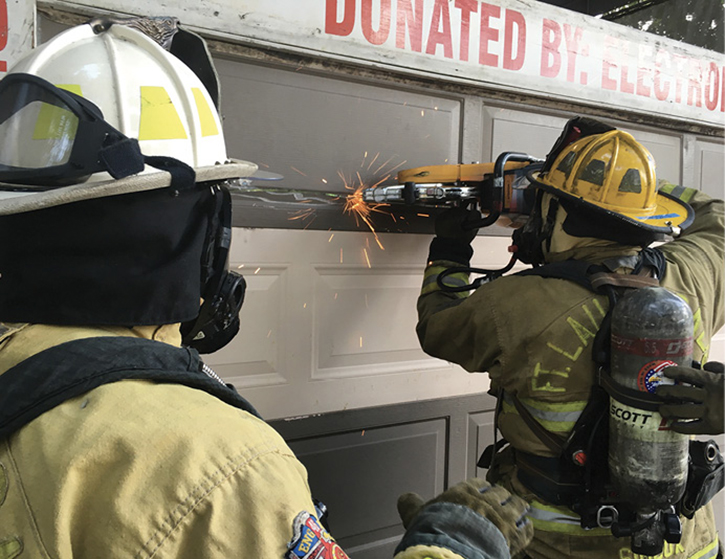
TRAINING NOTEBOOK ❘ By Stephen Shaw
The lessons learned from training are more than just “nice to know” nuggets—they are essential. The Fort Lauderdale (FL) Fire Rescue (FLFR) Training & Special Operations Bureau has developed a comprehensive training program focusing on forcing entry on overhead doors with rotary saws. The content comes from our collective experience on the scene of multiple incidents combined with our ability to train on many commercial and residential acquired structures. We are also fortunate to have developed tremendous relationships with local overhead door companies. These relationships have led to the building of props that can hold doors in place for training purposes. The training has been well received and the lessons learned over such a long time have been amazing. This article covers the most valuable lessons learned from cutting commercial and residential overhead doors.
RELATED FIREFIGHTER TRAINING
Training Minutes Revisited: Rotary Saws
Commentary: The Rookie Doesn’t Know a Trade!?!?!?
Truck Company Operations: Using the Rotary Saw, Part 1
The Importance of Lessons Learned During Training
1. Teach saw etiquette.
If firefighters try to use a rotary saw without proficiency on that tool, they are set up for failure. On the fireground, this translates to delays in tactics; inefficient operations because of poor tool use; and, worse, huge safety concerns for the operator and those in the area. Not having a handle on good rotary saw etiquette leads to firefighters focusing on learning how to use the saw instead of accomplishing the task at hand, whatever it may be.
We recommend that when teaching any skill requiring the use of a rotary saw (e.g., roof ventilation, forcible entry), start by including a module on good saw etiquette. This includes, among other things, how to hold the saw in various positions, listening to the saw, and matching the blade with the material being cut. We have found that introducing this saw etiquette module prior to performing a skill increases the efficiency of the saw operator and enhances the student’s learning.
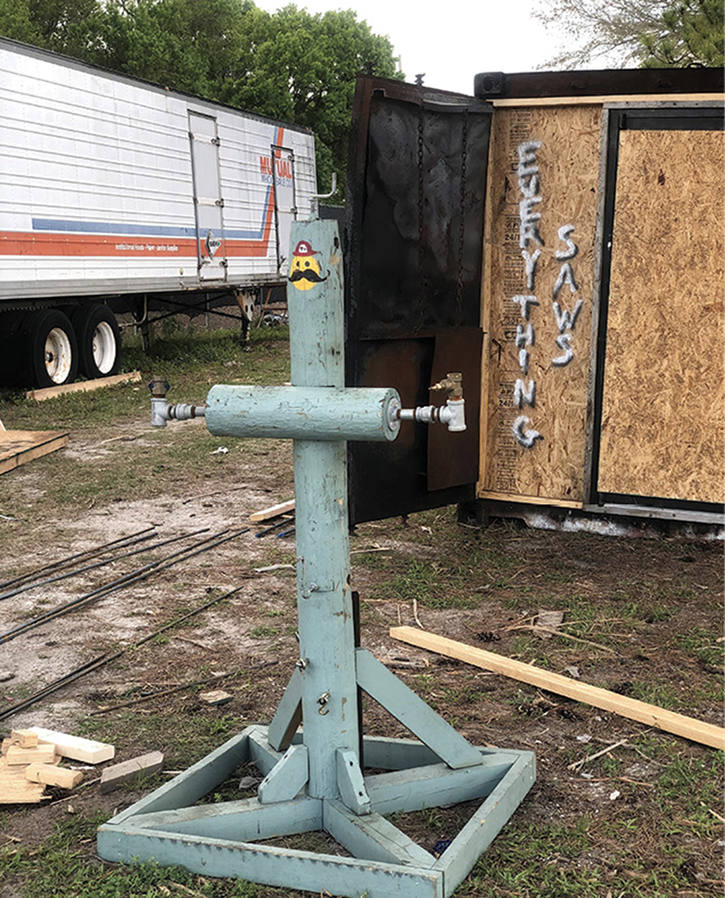
(1) Photo 1 by Julio Ramos; all other photos courtesy of author.
Lesson learned: Training props facilitate saw etiquette. Simple props that allow for basic saw cuts at different angles are great for starters. Once proficient, firefighters can graduate to props that secure overhead and garage doors and practice cuts based on departmental procedures. Commercially made overhead door props are great additions to the cache of fire academies or fire departments. Photo 1 shows a prop built by Driver-Engineer Chris Ramsey [Osceola County (FL) Fire Rescue Department] for practicing basic cuts at all angles and heights and rotary saw etiquette.
2. Safety: Wear full bunker gear.
We know that the situation will always dictate actions. Personal protective equipment (PPE) is no different. Using a rotary saw comes with various safety considerations, such as shrapnel, hazardous dust particles from the material being cut, and the blades themselves.
During a training exercise at a local garage door company, a screen on two sides enclosed the area in which we set up the prop. Since the class was held outside in the fresh air, many of the students and instructors were not wearing their self-contained breathing apparatus (SCBA). It was only after several of us started having throbbing headaches that we realized that the screen, enclosing only two of the four sides, was keeping in much of the exhaust from the saws, leading to carbon monoxide exposure.
On another day, while clear across the bay at a firehouse conducting training, shrapnel from a blade hit a training captain in the eye while he was removing his gear. He thought that he was safe from potential flying debris because he was so far away from the operation.
Lesson learned: Training in full gear while on air provides the maximum level of protection and prepares the students to train as if they were at an actual fire scene. This should be your default setting unless otherwise directed and protected (photo 2).

(2)
3. The fire academy training is not always the same as the fire department’s.
It is fascinating to go through textbooks used at various fire academies, specifically when it comes to techniques taught on overhead door forcible entry. In one popular text, the only method shown is the inverted-V cut. In another, the only technique shown is a box cut. In John Norman’s Fire Officer’s Handbook of Tactics (fourth edition, chapter 8), he goes into much more detail on the various ways in which an overhead door can be cut.1 Norman takes the time to cover in detail the inverted-V and the three-sided cuts and the various advantages and disadvantages of each. Unfortunately, Norman’s text is not often used at the fire academy level. All this being said, don’t assume anything when it comes to your new recruits. One firefighter’s default setting may be totally different from another’s.
Lesson learned: Provide clear direction on how you want your crews to force entry on an overhead door because what is taught at the academy is not the same as what is taught in the fire department.
4. Loud noises!
Rotary saws operate at more than 115 decibels. Per the Occupational Safety and Health Administration (OSHA), the permissible exposure limit for noise is 90 decibels over an eight-hour workday.2 OSHA also states that for every rise in five decibels above 90, the duration for noise exposure is cut in half. Thus, for a saw running at 115 decibels, the time needed to reach the 100-percent noise dose is 15 minutes.
The noise from a running saw also drowns out the alarms coming from your SCBA. Often, it seemed that when working for long periods with saws, the operators were unaware that their SCBA alarm was sounding. This may be more of a nuisance to the operator than to those around him. On the other hand, if someone in the incident command area is operating a tracking unit for integrated SCBA, this may lead to confusion on the part of Command and, at the extreme end of the spectrum, the consideration of deploying a rapid intervention team (RIT) to determine the status of members whose alarms are sounding and who are not responding to Command.
A last note on noise and communication: On lengthy saw operations, the officer often assists the firefighter. The officer must be aware of radio communications during saw operations; he must turn up the radio volume or step back from time to time to hear what’s happening on scene. In some departments’ tactics manuals, one member monitors radio transmissions during saw operations.
Lesson learned: Loud noises from operating the rotary saw interfere with radio communications and drown out other pertinent on-scene sounds. Always wear ear protection when operating saws, but recognize the need to monitor your radios at all times.
5. Don’t deform rolling metal doors, or they won’t slide.
Rolling metal overhead doors consist of multiple steel slats that slide together in a tongue-and-groove pattern to form the door. In south Florida, wind tabs and wind bars are commonly found on the ends of rolling metal doors. When you make a vertical cut in these doors, these slats will often slide easily apart from one another. Captain Dan Troxell (D.C. Fire) wrote an article “Forcible Entry Techniques for Roll-Down Security Gates” (Fire Engineering, March 2012).3 He covers three methods (slash cut, tee-pee cut, and box cut) to cut steel slats found on security gates. For each cut, he recommends using the pike end of a halligan tool to create purchase points, which can be used after the cut to help slide the slats apart.
I like this idea, with one caveat: Make sure your halligan has a sharp pike. I watched some of our crews attempt this tactic while forcing entry on a rolling metal door at a firehouse that was going to be demolished. The pike of the halligan in use was so dull that all the crew did was deform the door, not make a purchase point. When the purchase point was finally created, the slats would not slide because of the damage done. The only remaining method to complete the cut was to cut horizontally with the rotary saw. On a broader scope, if you run into a rolling door that has been damaged, deformed, or otherwise beat up, assume that the slats will not slide easily. The same applies to a door discolored by high heat; you will most likely need to cut it.
Lesson learned: If overhead doors are secured with padlocks, there are several ways to defeat them; Troxell details them in his article. In any case, keep your tools sharp so you don’t deform the rolling metal door if you intend on sliding the slats.
6. Match the right blade to the right material.
It is not uncommon to see crews at an incident or at training using blades to cut materials for which the blades were not primarily designed. For example, crews were cutting a ventilation hole on the roof of an acquired structure during a live fire exercise with a rotary saw with an impregnated diamond-tooth blade, which is usually used for concrete operations. Although they were making progress, it was less efficient than if they had employed a carbide-tipped roof blade. The finished vent hole looked as if it had been burned through, not cut with a proper wood-cutting blade. Similarly, on arrival at a house fire several years ago, my engine was assigned to vertically ventilate a house with a wood roof covered with tiles. Prior to ascending to the roof, we quickly changed out the rotary saw’s diamond blade, with which it is normally equipped to use on metal overhead doors and at car fires. We substituted a carbide tooth blade that, after the roof tile was removed, made quick work of the wood roof underneath. The time it took to change out the blade was definitely less than the time needed to tackle the wood roof with the diamond blade.
Regarding overhead doors, we have seen similar situations where crews use diamond-matrix blades most efficient for cutting concrete (e.g., “FEMA blades”) to force entry. Though the blade will work, it will be much less efficient than diamond-coated blades or abrasive wheels. It is even less effective when the blade penetrates the metal skin of a reinforced garage door and the crew is then met with multiple 2 × 4 wooden horizontal wind braces ( a common finding on many commercial and residential sectional doors). Again, as discussed above, the blade “burns” through the wood reinforcements as opposed to cutting through them.
Lesson learned: Do not assume that all crew members know what blades were designed for which purpose.
Identify the different types of blades with distinct colors or markings, especially if your department uses multiple types (photo 3).
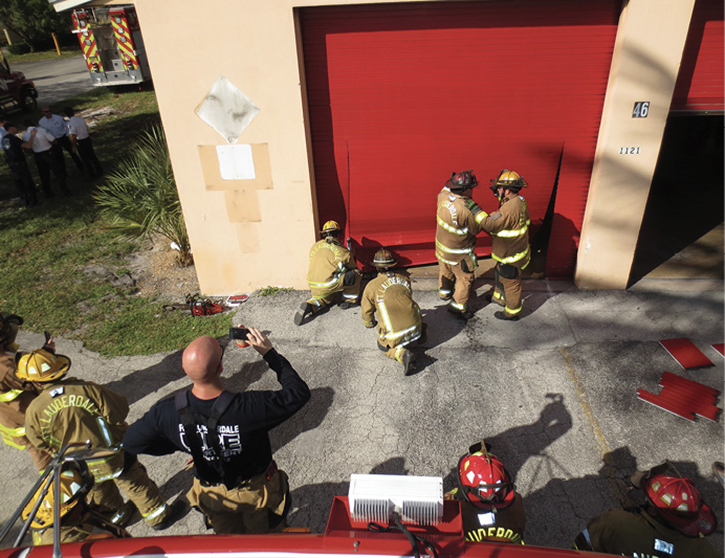
(3)
7. Overhead doors are HEAVY!
We often forget how heavy overhead doors can be. The new homeowner or firefighters with little building construction expertise may not be aware that overhead doors are counterbalanced by springs to aid in opening them. Extension springs (sectional overhead doors) or tension springs (sectional and roll-up overhead doors) help balance this weight, allowing an individual to manually raise a door easily. Hence, one may not realize the actual weight of an overhead door.
In March 1995, a San Francisco firefighter lost his life when he was trapped behind a 250-pound 3⁄8-inch-thick plywood garage door during a house fire.4 The heaviest sectional garage door I have ever seen was a 200-mile-per-hour wind-rated 16-foot-wide insulated door with multiple six-inch-wide sections of horizontal wind bracing covered by a 3⁄8-inch-thick decorative wood veneer. This behemoth required the largest tensioning springs I’d seen up until that time. I don’t recall what it weighed, but I can only imagine the surprise in store for our crews if they ever confront this monster unprepared. Worse yet, what if this is the door trapping our crews who find themselves in the wrong place at the wrong time when Murphy’s Law is going into high gear? In photo 4, this massive hurricane-rated, insulated, reinforced sectional garage door greeted FLFR firefighters on a recent structure fire.

(4)
Lesson learned: Make sure that along with training on forcible entry and saw etiquette, you don’t forget building construction, especially how overhead doors normally operate. The various springs used to counterbalance these often very heavy doors can give a false sense of security to those who may not be familiar with their true weight.
8. Self-storage facilities’ corrugated steel doors usually don’t slide apart!
Self-storage facilities house multiple units that are rented for commercial or residential use and may contain numerous hazards.5 These units are most often secured by a single door, which usually consists of a single sheet of corrugated steel of varying thickness. At one fire, I witnessed crews trying to “slide” the cut section of a door as if it were a slat in a metal rolling door. After pointing out to the crew the door’s construction, they proceeded to make a horizontal cut to fully remove the door.
I have since had many discussions with firefighters who will routinely make this assumption when observing similar doors at these facilities. It is a great opportunity to stop and discuss the various construction methods featured in overhead doors. It is also a great opportunity to discuss the various ways these types of doors are secured (e.g., padlock, slide lock). By default, we should first try to open the door the way it was designed to be opened and then secure it in place somehow. Other times, attacking the locking mechanism may not work (see item 10 below).
Lesson learned: Know your territory and be familiar with the different types of roll-up overhead doors that are out there and prepare to deal with them (photo 5).
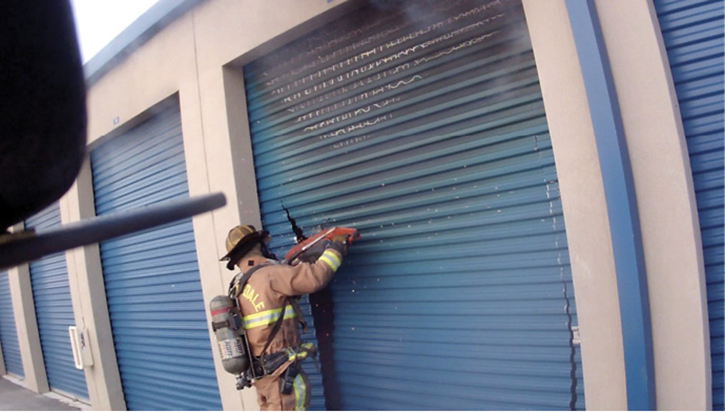
(5)
9. Location, location, location: Geography dictates tactics.
This is Forcible Entry 101. When it comes to overhead and garage doors, one cannot teach a class without heavy consideration on where they are teaching. When I first started gathering information on overhead and garage doors, I literally walked from business to business in the commercial area just northwest of our downtown district. More than 95 percent of those businesses secured their doors (mostly sectional) by latching one or both side latches at the second panel from the bottom. This validated the techniques outlined in Captain Bill Gustin’s article, “Fire Tactics for Attached Garages” (Fire Engineering, March 2011).6 Thus, in Fort Lauderdale, we present the option to cut one or two small triangles at the level of the second panel up to release these latches, allowing crews to raise the door with the least cutting.
When it comes to sectional garage doors, whether residential or commercial, the geographical location can be directly proportional to the robustness of the door. Sectional garage doors in Florida are built to meet wind speed and impact standards that were implemented after Hurricane Andrew in 1992. These wind standards have since been adopted in Nevada, California, Utah, Kansas, and Missouri because of winds caused by the local weather and terrain. We have found that the inverted-V cut does not work well with the doors mentioned above for multiple reasons, mainly the increased thickness of these doors along with the additional amount of material behind them.6 It often takes many additional cuts to make the appropriate opening, even for smaller purchase points.
Lessons learned: Geographical location has a huge influence on tactics. Traditional tactics used to cut sectional doors (inverted V) do not work well with reinforced sectional garage doors. Preferred methods include the barn-door cut, the door-within-a-door cut, and the box cut. These cuts provide the largest opening short of opening the door itself. The articles referenced here detail each of these cuts, along with their advantages and disadvantages.
10. Sometimes, it’s better to pry before you try.
When I was a lieutenant on a busy engine company, a division chief asked why I cut a rolling metal door at a storage unit fire rather than attempting to cut the locking mechanism and simply roll it up. I explained that the fire had already heavily damaged and warped the door so that it could not be used in the future. Second, the weight of the door in its now-weakened rolled-up position above our heads would present a greater hazard vs. leaving it pulled down and performing a box cut.
After we had cut the door, a third reason concerning the door’s locking mechanism further justified the decision. Instead of a simple padlock and slide latch, the lock was a cylinder lock combined with a sliding latch plate, requiring a key similar to that used for a soda machine. Initially, we had tried to obtain a key from the management company on scene, but it could not find one. After the fire was out, we had to check the adjacent units for extension. For training purposes, the chief directed us to try to cut the sliding lock mechanism with the rotary saw on adjacent doors. During each cut, the blade warped and shredded the mechanism such that it would not slide open at all, thus justifying the decision to cut the door rather than attempt to roll it up (photo 6).
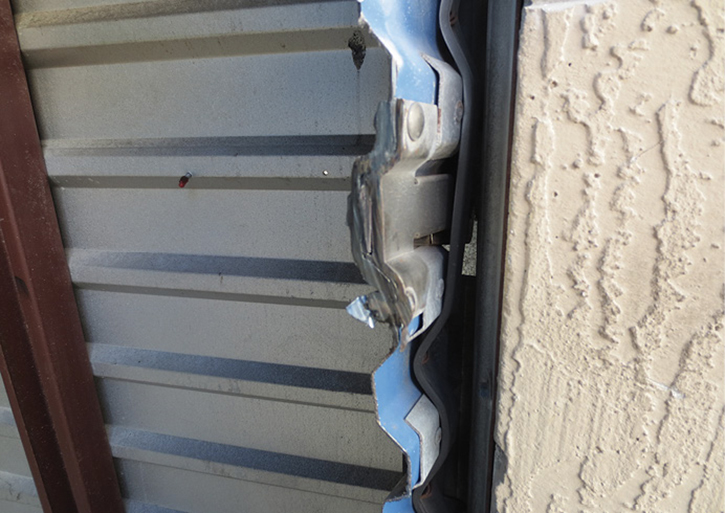
(6)
All things considered, I still prescribe “trying before we pry.”7 It’s common sense and usually the professional tactic to deploy. But more and more, as we continue to learn from incidents and from training, I keep finding reasons to “pry before we try.”
If you’re like me, you’ve seen the videos online of residential garage doors weakened by heat closing on crews during an incident or during training. You may also have read the report on the 1995 line-of-duty death mentioned above when a firefighter was trapped behind a large 250-pound garage door. In 2016, a firefighter in Utah sustained neck and back injuries when the residential garage door, in an open position, collapsed because of an attic fire that caused the trusses above the garage to fail.8
Lesson learned: Based on these and several other incidents, the evidence strongly suggests that cutting the door altogether may be the safest method rather than traditionally raising the door, whether commercial or residential construction.
In any case, if you choose to open the overhead or garage door normally, it must be secured so it does not come down inadvertently—for example, for a sectional door, deforming the track or gripping the track with a pair of locking pliers or using a New York hook to secure the door in the open position. In a March 2016 “Training Minutes” video, Captain Joseph Alvarez shows several methods for securing garage doors9 (photo 7).

(7)
11. Consider cutting horizontally first.
The most difficult cut to make when cutting an overhead door is the horizontal cut, for several reasons. First, elevating the saw to cut at head height is more physically demanding than cutting near your feet or vertically downward. Second, the leverage gained when holding the saw at a lower height is not there when the saw is elevated. How would you hold the saw above or at the level of your head? You grab the bar at the side of the saw vs. the top of the motorhead. The saw operator thus has less of a “push” into the material being cut.
Third, if the saw operator has already expended energy in making vertical cuts, he has less energy when making the horizontal cut. It is also important to cut so as not to overreach the height at which the operator is comfortable. Trying to make a cut that forces the operator to place the saw in an unsafe overhead position is a recipe for disaster.
Lesson learned: Although on-scene conditions will dictate whether to use this tactic (e.g., the need to get water on the fire immediately), making the more difficult horizontal cuts on an overhead door first make the successive cuts much easier to perform, making the operation more efficient (photo 8).
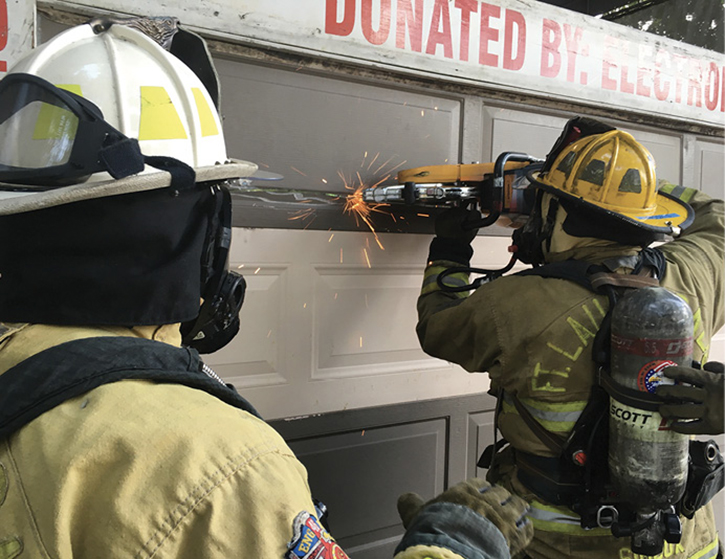
(8)
Although I have always been taught to “Pass It On,”10 it is still an honor to be able to share our lessons learned with our fire service brothers and sisters. Even though I focused on a very specific tactics and strategies niche, you can glean abundant knowledge by paying attention, recording observations, and adhering to a learning culture.
Endnotes
1. Norman, John. (2012) Fire Officer’s Handbook of Tactics (fourth edition). Fire Engineering. https://bit.ly/3dEWrdF.
2. National Institute for Occupational Safety & Health. (2018). “Noise and Hearing Loss Prevention.” Retrieved from https://bit.ly/2xyxgZO.
3. Troxell, D. (March 2012). “Forcible Entry Techniques for Roll-Down Security Gates.” Fire Engineering. https://bit.ly/2UJVjNj.
4. United States Fire Administration. (1995). “Entrapment in Garage Kills One Firefighter.” Retrieved from https://bit.ly/2WUexT9.
5. Berry, J. (October 2016). “Storage Unit Fires: Hazards Unknown.” Fire Engineering. Retrieved from https://bit.ly/2QU4xoW.
6. Gustin, B. (March 2011). “Fire Tactics for Attached Garages.” Fire Engineering. Retrieved from https://bit.ly/2JpukRR.
7. Hoevelman, J. (April 2018). “Attached Garage Fires: Strategies and Tactics.” Fire Engineering. Retrieved from https://bit.ly/2QT7kP5.
8. ABC4-TV. (September 28, 2016). “Rookie Firefighter Injured Weeks Before Baby’s Birth.” Acb4.com. Retrieved from https://bit.ly/2QV7o12.
9. Fireengineering.com. (March 2016) “Training Minutes: Securing Garage Doors.” Retrieved from https://bit.ly/2UwxVE9.
10. Goldfeder, W. (2014). Pass It On. Fire Engineering: Tulsa, Oklahoma. Retrieved from https://bit.ly/33UqVns.
Stephen Shaw is the battalion chief of emergency medical services with Fort Lauderdale (FL) Fire Rescue, where he has spent more than 20 of his 25 years in the fire service. He served five years as the battalion chief of Training & Special Operations. Shaw is an accredited chief training officer, the department hazmat coordinator, and a hazmat specialist with USAR FL-TF2.