
By Mike Giroux
If you go into any American city these days, you will notice larger buildings are being built and several other buildings in the city are being rehabbed, not only on the interior but also the exterior. Most of the time, when the renovations on the outside are being done, they are commonly using a suspended scaffolding system, more commonly called a swing stage scaffold.
RELATED
Scaffolding on Buildings and its Effects on Firefighting Operations
Ray Downey: TIMES SQUARE SCAFFOLDING COLLAPSE
Impalement Response Considerations
Partial Collapse of a Building Under Construction
False Facades: Older Structures’ Facelifts
There are several methods of suspending a swing stage system on a building. The most common ways in today’s construction is by the use of roof hooks and outrigger beams. For the purpose of this article, we will only speak about a two- point anchor system. There are several other types out there in the real world, but we are just taking a small picture of swing stage scaffolding and expanding it so we can understand how it is rigged.

Roof hooks come in two different “flavors,” and both are used in different applications. The hooks are both used over the parapet wall and then tied back to a substantial object or structural member of the building or roof. The first type of roof hook is called a forged hook. It is made from a single piece of mild iron and is forged into the shape and size needed. (1). A loop is forged at the suspension end in which the scaffold wire rope is attached and then attached to the stirrup. The other end of the hook has an iron ring attached through a forged hole, which is used for the tie back of the hook. A very important thing to understand regarding forged hooks is that it is not designed to handle the forces associated with today’s electric swing stage systems. It does not meet the required safety factors and therefore can only be used for rope fall protection anchors or manual swing stage systems. These hooks range in size openings of 9 to 60 inches.

The second type of roof hook which is more commonly used is the flame-cut hook. This type of hook is acetylene-burned from a sheet of steel. It can be cut from different thicknesses and also different alloys. Unlike the forged hooks, these hooks are designed to handle the forces that may be associated with electric swing scaffold. These hooks are also much heavier than their counterpart forged hooks, therefore the practical application of these hooks only range from 9 to about 42-inches for their openings. (2).

Regardless of which type of hook you use, there are certain criteria that should be adhered to when using these types of anchor systems. First and foremost, use the correct hook for the proper scaffold system. Remember, the forged hook can ONLY be used on manual operating systems and rope fall protection. The flame-cut hook can be used on all suspended systems regardless if manual or electronic, because it meets all the required safety factors associated with both systems. Secondly, when we use the hooks, regardless of which type, we need to maintain three points of contact between the hook and the parapet wall. These contact points are the face, the top edge of the hook and the rear edge of the hook. (3). The diameter of the hook is dictated by the structural engineer with the help or recommendation of a licensed rigger. Lastly, with two-point anchor systems, we need to make the two “sides” identical. What does this mean? If I use as flame-cut hook on one side of the scaffold, I need to use the flame-cut hook on the second anchor point. I cannot use a flame-cut hook on one side and forged on the other side for an electronically operated swing scaffold. Remember, the forged type hook does not meet the safety factors for electric scaffold systems, therefore we must use the flame-cut hooks. Now we can use flame-cut on a manual system and the rope fall protection, but it would be more expensive and heavier to haul up. Again, we won’t be rigging these systems, but we should be aware of the type of materials and devices that are being used.
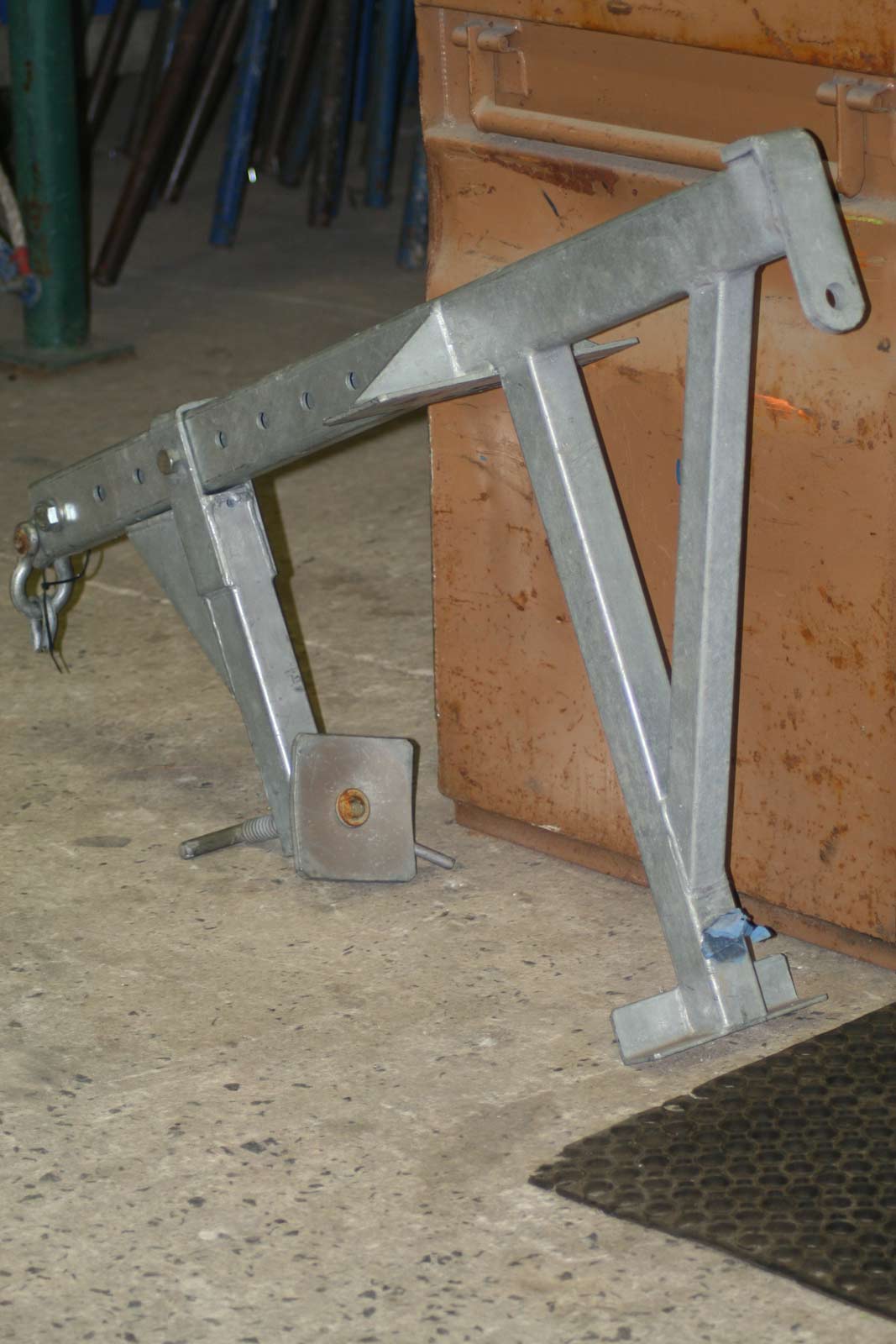
In addition to using roof hook for anchor devices, some master riggers could also use devices called parapet clamps. (4). These clamps do exactly as you would suspect. They clamp onto the parapet wall and are also tied back to a substantial object. When riggers use these clamps they will pad out the parapet for a few reasons: first, so the clamp does not damage the parapet, and secondly so they can get as much surface contact as possible.

Hooks and clamps are very easy to use and not very hard to bring up to the top of the roof. However, every building that we respond to does not have a parapet wall or the parapet wall is not structurally sound to use these devices. In this case, you will see another anchor system called outrigger beams. These beams may be made from steel or some type of aluminum alloy. They can come in either one-piece, spliced sections, or telescopic sections. These beams may be I-beams, H- beams, or even square or rectangular tube. (5). One-piece beams usually come in lengths of 12-20 feet and can be difficult to transport both to the job site and up to the roof through the building, particularly if the beam is made of steel and not an aluminum alloy. Aluminum -spliced telescopic sections usually come in eight-foot sections which can be assembled to reach 32 feet in length.
All outrigger beams are professionally made by manufacturers and are designed by their engineers. Based on the situation, the building, and the manufactured system, the engineer will recommend how far the outreach should be and how much counterweight is needed to anchor the system. Depending on where you live and the requirements for outrigger beams, the counterweight could be heavier or lighter based on what governing body you use. In New York State, they require a 4:1 safety factor. However, the Occupational Safety and Health Administration (OSHA) requires a 4:1 factor or 1.5 times the stall torque value of the scaffold hoist used. Some stall torques could be 3000 lbf. Therefore, the New York State Code would use less counterweight than the OSHA Code. In this situation, they should follow the most stringent rule that applies. (see diagram 1A). However, after speaking to several master riggers for swing stage scaffold, I was informed that most manufacturers do not state their stall torque values. In this case, and in most cases, they use the 4:1 factor.
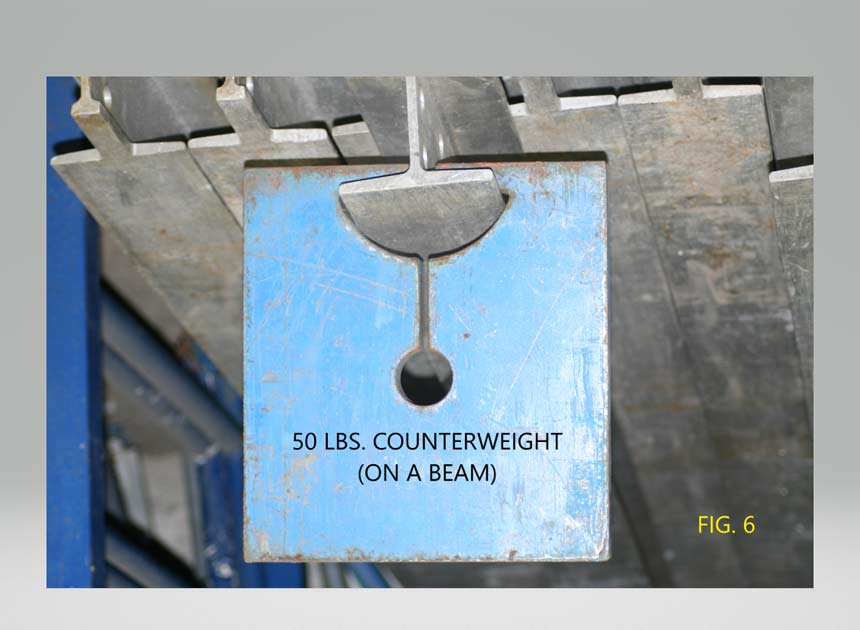
In addition to the counterweights, the outrigger beam will also need to be tied back, just as like the roof hooks. The counterweights need to be labeled with their individual weight, must be made of essentially metal or concrete, a non-flowable material. This means that they cannot use sand, water, or concrete chips as a counterweight. Most counterweights are available individually in 50-pound plates. (6). The plates can be rigged in several fashions. They can slide onto the end of the beam, they can be suspended from a 5/16th wire rope from the beam, they could use a turnbuckle (7), or they could be anchored in a combination of both. The way that the counterweights are rigged really depends on the master rigger’s philosophy, the layout of the roof, the structure components of the roof, and of course the length of the beam itself.

Just for our information, we should know if there is enough counterweight on the outrigger beam to make sure that if we do have an incident, we know that the whole system will not fall down on us and create a more serious situation, or create more of a problem for our victims. There is a very simple formula to find out how much counterweight is needed for the system. Regardless if the outrigger beams are steel or aluminum alloy, finding how much counterweight remains the same. If you look back at diagram 1A, you will see the formula:
CTWT= L x D1 x SF/D2
What this means is the counterweight (CTWT) is equal to the load times the length of the beam from the center front fulcrum to the end that is cantilevered. Then multiply that by the safety factor, which we said would be four unless a governing body has a more stringent safety factor. We then take that number and divide by the length of the beam from the center of the front fulcrum to the end of the beam. That will give us the total counterweights needed for that beam. This same formula would have to be done for the other outrigger beam. This formula is very simple and can be done very quickly to see if the counterweights on the beams are enough to hold the system in place while we perform a rescue. Common weight for counterweights on each outrigger beam is between 1,000-2,500 lbs.
Now I know there is a lot of technical information that may or may not be useful to us when it comes to a swing stage scaffold incident. The point here is that if we do have this type of emergency, we need to send someone to the roof to see if we have any failure in the rigging or counterweights or if it is due to the electric hoist on the scaffold. If we understand how things are rigged and works, we will be able to better help our victims. We can come up with a plan faster and act on that plan with more confidence.
I hope this gave you some insight into the workings of rigging swing stage scaffold. Whenever this type of emergency occurs, use all your resources on scene. These include the master rigger, workers, and foremen. Never be afraid to ask questions to these folks if you don’t understand. Remember, they are the experts in this field, use them to your advantage.
Until next time, stay safe and keep training.
![]() |
Mike Giroux is a lieutenant and 19-year veteran with the Yonkers (NY) Fire Department. As a nationally certified Fire Instructor I and fire officer, he has taught all aspects of technical rescue for the Yonkers Fire Department, including rescue school, probationary school, and personal escape. He also teaches around the country as a Senior Chief Instructor for Wright Rescue Solutions, Inc. based out of Panama City, Florida. His specialties include high-angle rope rescue, confined space, and structural rope rescue. |