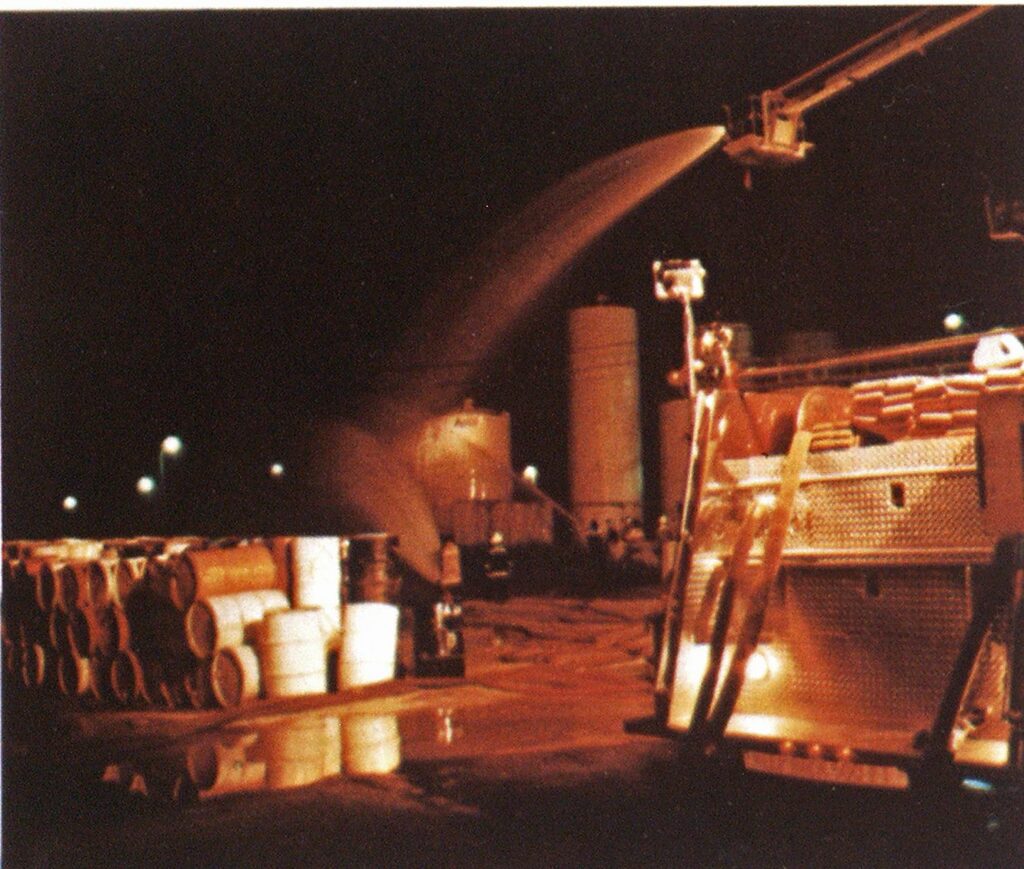
Plan Works, Leak Stopped In Liquid Nitrogen Tank
features

After receiving a report of a large amount of smoke at the Freeman Chemical Corp., the Saukville, Wis., Fire Department responded and found vapors leaking from a pressurized tank of liquid nitrogen.
The tank measured about 30 feet in height and 12 feet in diameter. It was located in a diked tank farm containing about 30 tanks of various types of polar solvents and petroleum-based chemicals.
This call, around 3 a.m. Sunday morning last Aug. 31, came on the heels of a July 25 call when an acid tank of thallic anhydride caught fire after being struck by lightning. That incident forced the evacuation of over 150 area residents.
Most important
We feel the most important part of handling this incident occurred years ago when a pre-fire plan was developed for Freeman Chemical. The company is a large manufacturer of synthetic resins, foams and polyesters and it is Saukville’s largest industry. The prefire plan consists of a three-alarm, 10fire department response plus a special call of the Ozaukee County Rescue Squad specialty unit which handles any necessary evacuation. The first alarm calls for an automatic response from the Port Washington Fire Department.
For this incident, the Saukville Fire Department responded with Engine 365, a 1000-gpm attack pumper; Engine 366, a 1000-gpm pumper; Engine 364, a 1500-gpm pumper (which was placed in service only one week prior and was on its first call); Unit 356, an equipment truck and command post; and Squad 352, an ambulance. The Port Washington Fire Department responded with Engine 461, a 1500-gpm pumper; Engine 462, a 1250-gpm pumper; and Unit 460, an 85-foot elevating platform with a 1000-gpm pump.
Stop and think
The pre-fire plan has been practiced and used many times. Frequency and training gives everyone knowledge and experience on standard operating procedures. Radio communications are kept to a minimum and confusion is avoided. The most important thing we did was to stop and think. A spontaneous action could endanger the lives of our fire fighters. The incident posed enough problems without our becoming a part of it.
Our personnel who have completed hazardous materials training took our DOT Hazardous Materials Guide and looked up liquid nitrogen. It was listed as a nonflammable gas. It is poisonous as a concentrated vapor cloud and seals off oxygen.
I live two blocks from Freeman and upon my response the vapor cloud had enveloped two streets. Liquid nitrogen is also very cold in nature. This caused us major problems because the vapors being expelled from the tank formed a large layer of ice and frost over the valves that needed to be closed. Also, if water were to be directly applied to the tank we would actually have added relative heat to the tank and liquid nitrogen, causing even more leakage. It is of utmost importance to secure proper information about an incident before acting.
Upwind approach
All units’ were ordered to approach the incident upwind. We were concerned about the dispersal of the vapor cloud.
Engine 365, our attack pumper laid a 4-inch line from a preselected spot. For 365’s water supply, Engine 364 then laid its own 4-inch line from 365’s split lay to a plant hydrant supplied partially by the municipal and Freeman’s own system. Engine 365’s crew of eight men stretched a preconnected 2 ½-inch hand line and two 2 ½ -inch lines to a deluge set with a fog nozzle to start dispersing the vapor cloud.
Engine 366’s assignment is to enter the rear entrance of the plant and then lay parallel 2 ½ and 3-inch lines to a hydrant on Linden St. adjacent to the plant and supply another deluge set. However, a call for a house fire was received upon our arrival at Freeman, and Engine 366 could not be committed at this time. Unit 356 set up as a command post, and Rescue 352 stood by as an EMS unit. It left to answer another call at 3:35 a.m.
Water relay
Port Washington’s Engine 461 arrived and reported to a hydrant on Tower Drive with a 12-inch main. Three hundred feet of 4-inch line was laid from a hydrant that feeds a main running to Freeman’s plant system. Then 461 pumped from the municipal water system into this hydrant and relayed to Engine 364 to supplement its supply. Engine 364 then relayed to 365. This unique system is similar to pumping into a sprinkler Siamese and can yield a combined flow of over 2000 gpm.

Photos by Jim Carrier, Saukville F.D. photographer
Unit 460, the 85-foot elevating platform, set up upwind near 365 and operated a 750-gpm stream using a fog nozzle. Engine 462 laid 600 feet of 4inch hose to a hydrant on Rail Rd. and Church St. and supplied Engine 460. This operation was successful in totally dispersing the vapor cloud and eliminated any further need of evacuation. Our actions could now be turned to stopping the leak.
In the meantime, we had notified Paul Schaefer, Freeman Chemical plant manager, and he had arrived at the plant. The tank was owned by Airco Industrial Gases of Milwaukee. Liquid nitrogen is used at Freeman for sealing off moisture in many of the chemical batches Freeman manufactures. Airco was called for instructions on how to stop the leak. Instructions were received to turn off a set of valves.
Visibility zero
A three-man crew in full turnout gear, including SCBA, took a 1’/a-inch line from 365 and entered the vapor cloud and tank area. Prior to this time, no one was permitted near the vapor cloud and everyone was kept upwind. Upon entering the area of the tank, visibility was almost zero, but the men found the control valves and closed them.
Airco asked for a tank reading on the amount of pressure, but this was impossible due to the low visibility. The men then retreated from the area.
Unfortunately, these actions did not stop the leak. Airco was recalled for more instructions. They determined that the tank was overcharged when it was refilled prior to the weekend. Since Freeman had been shut down for the weekend and no liquid nitrogen was being used, the pressure had built up to a point where the safety valve should have functioned.
Later inspection showed that there were two safety valves: a valve which bleeds off periodically when extensive pressure develops and a safety disk which is designed to rupture when the bleed-off valve does not expel enough pressure. However a valve leading to the bleed-off valve was not reopened after refilling the tank.. When excessive pressure developed, the safety disk worked properly and ruptured.
Disk worked .. . and ruptured
Our instructions then were to close the valve leading to the safety disk that ruptured. In order to continue relieving the excessive pressure so the tank would not heat up and BLEVE, the liquid nitrogen was routed into the plant to waste, so that the tank’s pressure would continue to be relieved after the safety disk valve was closed.
We were two hours into the incident. All master streams were still operating and dispersing the vapor cloud. The liquid nitrogen vapor had built up a large layer of ice and frost on the valves and piping. It was decided to melt the ice formation from the valves and pipes with a 1 ⅛ -inch line on straight stream. Again, it was imperative that we not put any water on the tank, because that action would actually heat the tank.
Defrosted the valve
The master streams continued to operate, and the defrosting with the 1 ½ -inch line commenced. After a half hour, it appeared the icing had melted. A 24-foot roof ladder was raised to the tank where the valve shutoff was located. Three men in full turnout gear and SCBA ascended the ladder to close the valve. It wouldn’t budge.
They descended and the defrosting with the 1 ½ -inch line continued. After 20 minutes, they again ascended the ladder armed with a pipe wrench. This time they were able to free the valve and ultimately stop the leak.. The incident was under control at 5:50 a.m. and all lines were shut down. Sixty fire fighters were used to control this incident.
We feel that we learned several important things and the pre-fire plan provided for much of the success we gained from this incident. We also feel that it is necessary to list them.
- Nearly 500,000 gallons of water was used in this incident. We knew in advance that we had a good water system and that we could easily get all the water we needed. “Know your resources.”
- All fire fighters must use full turnout gear and SCBA near the incident. After an extended period of time, some fire fighters lost their respect for the hazard. Our chief officers kept close tabs and control of the area so that our personnel did not become casualties.
- Cooperation from and between Freeman’s supervisory personnel was excellent. They know what to expect. Let the experts provide the technical advice before acting on a hunch. If they don’t have the answer, they usually know where to get one.
- Have a plan formulated for automatic move-up if all your equipment is committed. If the call for the house fire had been received five minutes later, our third engine would have been committed. Our second-alarm response provides for a standby engine in our station from a neighboring community.
- The use of the hazardous materials guide enabled us to make an immediate decision and list the priorities we should follow. With this information were able to control the incident. With the technical advice of Freeman and Airco, we were able to eliminate the hazard.
- Have plenty of filled replacement air tanks available. Know where to get more. Establish a location upwind where they can be gathered and changed, but nearby so you do not go far for changing.
- Be careful. Don’t do something that could ruin your whole day!