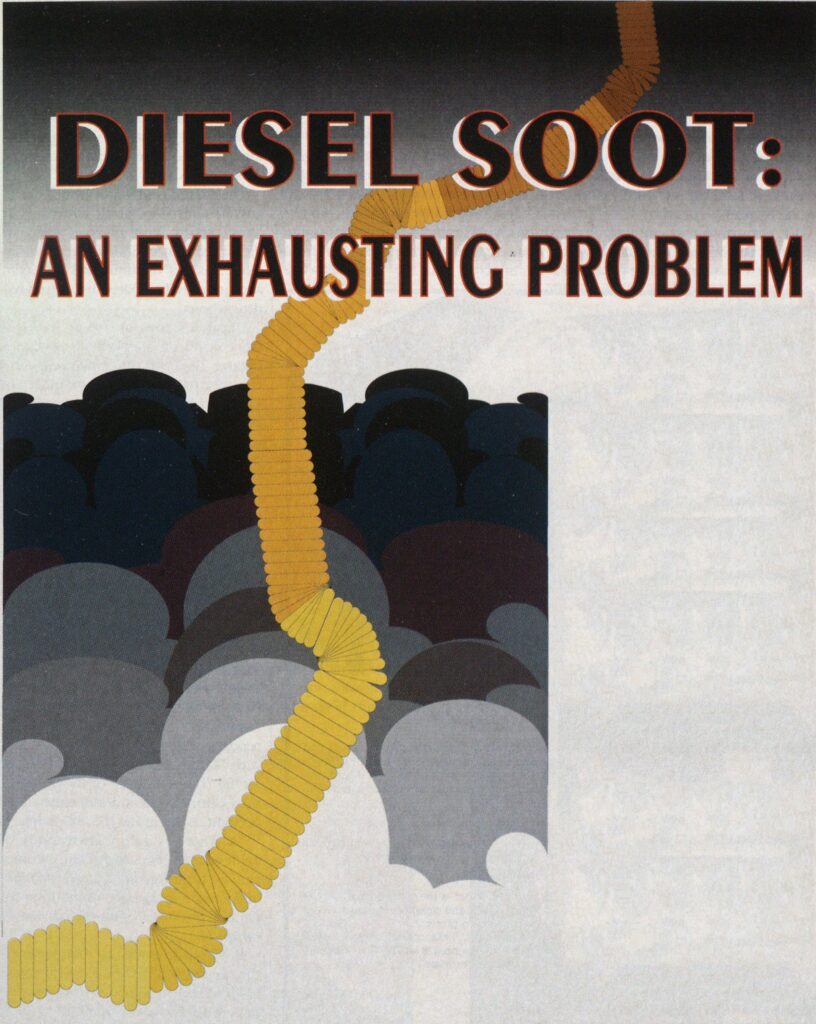
DIESEL SOOT: AN EXHAUSTING PROBLEM

On a brisk winter morning, the members of Engine 15 and Truck 9 arc busy performing their routine committee work when suddenly the calm is broken by a P.A. announcement: “District 5-2-1 being transmitted for a fire reported at…”
All members abandon their cleaning equipment and report to the apparatus floor, donning personal protective equipment as they mount the two pieces of apparatus. The rigs’ diesel engines rumble to life, and the apparatus clear the firehouse apron with great dispatch.
As the overhead door slowly closes, the bright sunlight shining through the windows highlights a thick plenum of diesel exhaust hanging in the cavern-like atmosphere of the empty firehouse. The soot-stained walls and ceilings attest to the fact that this scenario has been played out many times before.
In their haste to turn out for the alarm, members inadvertently leave doors leading to the kitchen and bunkroom open, allowing the fine black specks of diesel soot to find their way to the surfaces of the kitchen table, counters, and bunks where the members sleep.
The companies are informed via radio that the box is a false alarm, and they return to quarters. The potential for danger that they physically and mentally had prepared for now has passed, but the living quarters where they spend many of their working hours may pose another type of risk.
DIESEL EXHAUST
Unlike a gasoline-powered engine that uses an electrical spark for ignition, a diesel engine functions by compressing intake air in the combustion chamber and, at a precisely timed moment, introducing diesel fuel from an injector into the chamber. The heat of the compressed air ignites the atomized fuel, instantly driving the piston down, which produces the power stroke. This process is repeated thousands of times per minute, producing the power to operate the vehicle and accessories but generating a volume of potentially dangerous diesel exhaust as well.
The exhaust emissions from a diesel engine consist of gases and particulates (soot). The gaseous form of diesel exhaust contains carbon monoxide, oxides of sulfur and nitrogen, and unburned or partially burned hydrocarbons.
Diesel engines also emit particulates in an amount 50 to 80 times greater than gasoline-powered vehicles. The particulates are composed of solid carbon cores that are produced during the combustion process and tend to form chains or clusters. More than 95 percent of these particulates are less than 1 micrometer (1/1,000 of a millimeter) in size and easily inhaled. One group of chemicals found on diesel particulates is polynuclear aromatic hydrocarbons (PAH). It is estimated that as many as 18,000 different substances from the combustion process can be absorbed into the diesel exhaust particulates.
HEALTH EFFECTS
Tie Department of Occupational Health and Safety of the International Association of Fire Fighters issued a report entitled “Diesel Exhaust Exposure Within Fire Departments” (July 1990). The summary’ of its views on the health effects of diesel exhaust on firefighters includes the following:
- There is a conclusive body of evidence that documents the carcinogenic, tumorigenic [tumor-producing] and mutagenic [mutation-producing] potential of diesel exhaust in animals.
- There is evidence that supports the conclusion that human exposure to diesel exhaust may have an association with the development of lung cancer.
- Nitropolycyclic aromatic hydrocarbons (nitro-PAHs), specifically nitropyrenes, dinitropyrenes and nitrohydroxypyrenes, together account for much of the mutagenicity observed.”
The IAFF report indicates that there has been documentation of a sharp rise in total airborne dust particulate concentrations in firehouses when diesel vehicles are used.
CONTROL METHODS
In light of the potential health risks, fire departments have several methods available to them for limiting or eliminating exposure to diesel soot. First —and often least effective —is adjusting the normal ambient ventilation by opening doors and windows and operating area exhaust fans. These procedures may help to a limited degree by diluting the exhaust fumes, but they could create complications in colder climates as well as in areas where security is a problem. The other two basic systems that have demonstrated success in reducing the problem of diesel emissions are exhaust ventilating systems (direct exhaust) and engine exhaust filtering mechanisms.
Three manufacturers of direct exhaust systems are: Nederman Company of Westland, Michigan; PlymoVent of Edison, New Jersey; and Tykron of North Tonawanda, New York. They offer three basic systems for dealing with this problem.
The first system incorporates a ceiling-mounted exhaust blower with a length of flexible exhaust hose attached to its inlet. The hose is supported in the middle by a springloaded balancer. The nozzle end of the hose then is attached to the vehicle’s exhaust pipe. As the apparatus leaves the station, the balancer moves down a track toward the door and at a predetermined point triggers the hose to release. The spring-loaded balancer lifts the hose away from the vehicle and allows it to hang off the floor and out of the way. On return to quarters, personnel stretch the hose to the door and reattach it to the apparatus before backing in, to catch the fumes created while backing in.

(Photo courtesy of PlymoVent.)

Photo courtesy of PlymoVent.)

(Photo courtesy of Nederman.)
The second system uses the same hose and attachment to the vehicle; however, the exhaust blower is attached to an exhaust rail that is mounted on the ceiling along the full length of apparatus travel. This rail is designed as a hollow metal box with an opening at the bottom. The opening is covered with split neoprene. Traveling along the length of the exhaust rail is a collection box that transfers the exhaust gases from the hose to the exhaust rail. The advantage of this system is that the length of hose remains short and does not need to stretch great lengths at release. This system also allows more than one collection box to be operated from the same rail so that apparatus parking behind each other in the same station do not present a problem.
The third system is a ceiling-mounted exhaust rail as previously described; however, the forward end is open in a wide “V” configuration. This allows an apparatus with a vertical exhaust stack to engage the bottom of the exhaust rail and direct the smoke to the blower. A special adapter is installed on the top of the stack to facilitate the connection.
There are differences in equipment and methods of attachment and activation among these manufacturers. Nederman offers two ways to attach the hose to the exhaust pipe: a vise grip-type clamp that releases when an internal cable reaches the end of its travel and an electromagnetic principle to secure the hose to a contact plate on the side of the apparatus. When the hose reaches its release point, the magnet disengages and the hose releases. The Nederman system activation can be accomplished by manual control or an optional pressure switch that detects exhaust pressure in the system and starts the blower.
Tykron’s and PlymoVent’s systems use a pneumatic nozzle that is inflated with compressed air to secure it to the tailpipe. When the hose reaches its release point, the air is instantly exhausted from the bladder and the nozzle slides off the pipe. The PlymoVent unit is activated automatically by a sensing device, while Tykron’s activates by attachment to the station response alarm, with manual overrides available.
The Ammerman Company, located in Hopkins, Minnesota, also offers a ceiling-mounted direct exhaust system that utilizes the electromagnetic release principle.
OTHER SYSTEMS
The Sefac Corporation of Columbia, Mary land, offers a variety of overheadmounted reel units that keep the exhaust hose off the floor and out of the way. Systems arc available in the passive mode, which allows the exhaust to be directed via ductwork to the outside, and the active mode, which uses a gas extraction ventilator (this appears to be more suitable for fire service use).
A series of options such as motordriven reels and spring-loaded hoses as well as quick disconnects are available for installation. Several reels can be operated from one exhaust ventilator fan, depending on the purchaser’s needs. This system also is well suited for a fire department’s maintenance garage, where exhaust from apparatus undergoing repairs contaminates the workplace.

(Photo courtesy of Sefac.)

(Photo courtesy of Exhaust Track.)

(Photo courtesy of Ward Diesel.)
Note: With all of these units that require personnel to manually attach an exhaust hose on return to quarters, it is essential to vigorously enforce SOPs requiring personnel to attach the hose before the apparatus backs in, to receive the system’s full benefits.
The system manufactured by Exhaust Track, Inc., of Warminster, Pennsylvania, involves a different method of connecting the apparatus to the exhaust-removal mechanism. It has a vertical exhaust stack on the apparatus that mates with an exhaustcollection box. This box travels the length of a ceiling-mounted track and is connected by flex hose to a blower unit. As the apparatus leaves the station, the pipe and box move together as a unit and disengage at the end of the track. When the apparatus returns, the stack is guided into the opening and the collection box backs down the track with the apparatus. The system is self-adjusting and allows for an eight-inch, side-to-side deviation while pulling out and backing in.
To allow apparatus to relocate to other stations, the manufacturer recommends that the exhaust stack be located in the same side-to-side position on all units. The manufacturer also points out that the stack method directs the exhaust up and away from personnel operating at the scene of a fire or other emergency.
Activation is accomplished automatically by a pressure switch sensing incoming exhaust. This system also is offered as a kit; however, the customer’s self-installation must be inspected by a company representative prior to its use.
The Ward Diesel Filtration Company of Elmyra Heights, New York, manufactures a unique self-contained filtering system that requires no attachment to hoses or cables in the station and no manual activation. The entiresystem is mounted under the apparatus and functions as follows: When the engine is started, an electronic control unit signals a diverter valve to direct the exhaust through a porous ceramic filter. This filter unit removes the particulate from the diesel exhaust and allows the apparatus to run without visible smoke. After a preset period of time, the exhaust is directed back through the muffler in normal fashion. The control panel allows for an adjustable time period when the apparatus starts and activates the filter at all times when the vehicle is in reverse. By using the filter only on starts and in reverse, filter time is not wasted when the apparatus is outside of quarters. The manufacturer estimates that the filter element is good for 30 to 60 hours of filtering operation, depending on the size and type of engine as well as the amount of particulate being produced. Using a 43-second cycle to exit the firehouse, several thousand filter cycles are possible before the unit needs to be changed. A warning light in the cab indicates that the filter is approaching full and should be changed. The dirty filter then is returned to the manufacturer for regeneration.
In addition to using exhaust handling equipment such as described above, using quality fuel, establishing proper preventive maintenance (PM) intervals, and properly maintaining the diesel fuel injection system will help reduce the diesel emissions at the source. Recent innovations in the use of computer-controlled electronic fuel injection systems offer increased diesel engine efficiency while helping to reduce pollution.
The results of animal studies confirm the link between the induction of cancer and whole diesel exhaust, suggesting that a potential carcinogenic hazard exists when humans are exposed to diesel exhaust.
Methods to alleviate this problem are available; it is up to each department to research them thoroughly and select the method that best suits its needs
Endnotes
“Carcinogenic Effects of Exposure to Diesel Exhaust,” NIOSH Bulletin 50, August 1988.
“Diesel Exhaust in Eire Stations,” NJ Dept, of Health (PEOSH) Information Bulletin, September 1986; and Addendum, October 1989.