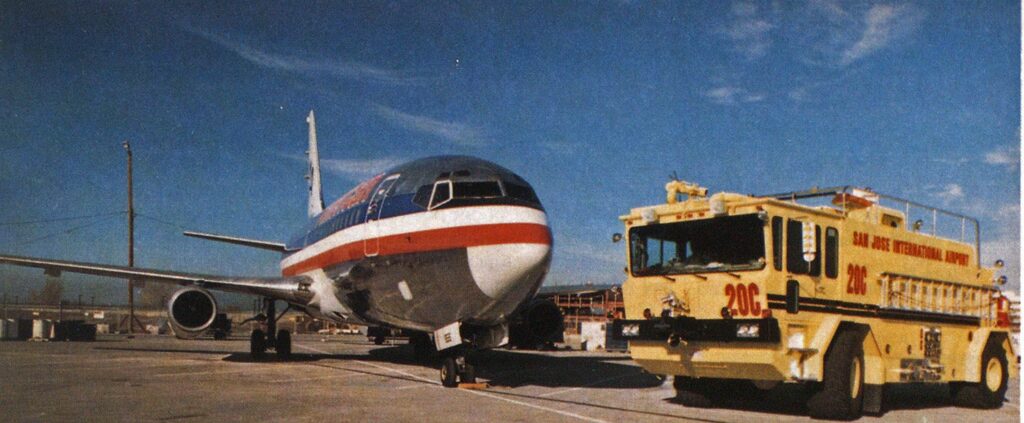
WRITING SPECIFICATIONS OFR ARFF VEHICLES

Just when you begin to get comfortable in your position as airport fire commander, it happens: You are assigned the task of writing the specifications for a new aircraft rescue and firefighting (ARFF) vehicle. You accept the assignment willingly, of course, but with some reservation. You know that, unlike conventional structural firefighting apparatus, an ARFF vehicle is unique. It specifically is designed to have a high horsepower-to-weight ratio for rapid acceleration and a high top speed. It also is designed to be extremely mobile and carry large quantities of firefighting agents and gp appropriate complement of auxiliary equipment.
This article is a guide to writing ARFF vehicle specifications in one of two situations: when the vehicle is being funded with federal grant-in-aid assistance (Airport Improvement Planning, or AIP) or when there is no federal participation.
THE PROCESS
How do you begin writing ARFF vehicle specifications? First, you must have a thorough understanding of what your new assignment involves. To make your task easier, use the following questions as a guide throughout the spec writing process.
- How will the vehicle be funded?
- How do you contact the Federal Aviation Administration (FAA) office responsible for providing federal funding?
- What current reference materials are available, and how do you obtain them?
- How many vehicles are required?
- What size vehicle is required?
- What type vehicle is required?
- Who are the leading manufacturers and how can you draw on their expertise?
- What are the manufacturers’ track records relative to after-sales service and parts support?
- Have similar-sized airports recently been through this process?
- What are the average industry lead times for the type of vehicle you require?
With these questions in mind, let’s divide the process into two parts. We’ll first look at a situation in which AIP grant-in-aid assistance is available.
THE AIP-FUNDED PROJECT
First, determine whether you want to take on the project by yourself or use the committee approach and call on various technical and administrative experts for their input and advice. Then it’s time to answer the questions listed above (in no special order).
You can obtain the phone number of the responsible FAA office by asking someone in airport administration, looking in the phone book under the heading “U.S. Government,” or contacting some other federal agency and asking for assistance.
Once you have made contact with the appropriate office, you should ask for the safety/compliance division officer assigned to your airport. This individual is extremely important: He or she will give final approval for any unique optional items you may request. Ask that individual for a copy of the FAA’s Advisory Circular (A/C) 150/5220-10A, the mandatory Guide Specification for Water/Foam Aircraft Rescue and Firefighting Vehicles (7/3/91), which must be used if FAA funding is involved. The purpose of this A/C is to define the performance standards, specifications, and recommendations for the design, construction, and testing of a family of ARFF vehicles with water capacities of 1,000, 1,500, 2,500, and 3,000 (and over) gallons.
Next, obtain a copy of Federal Aviation Regulation (FAR) Part 139, which will determine the size, type, and number of ARFF vehicles required for your airport’s “index” rating. The index is determined by a combination of the length of the passenger-carrying aircraft, expressed in groups, and the average daily departures of the aircraft. The size of the vehicle is determined by the airport’s index.
For example, an Index B airport requires either one vehicle carrying at least 500 pounds of sodium-based dry chemical or Halon 1211; 1,500 gallons of water; and a commensurate quantity of AFFF for foam production or one vehicle carrying 500 pounds of sodium-based dry chemical or Halon 1211 (or 450 pounds of potassiumbased dry chemical and water with a commensurate quantity of AFFF to total 100 gallons) and a second vehicle carrying an amount of water and a commensurate amount of AFFF so that the total quantity of water for foam production carried on both vehicles is at least 1,500 gallons. (To determine your airport’s index, see box on page 88.)
Next, you must review the Advisory Circular in detail. Table 1, chapter 1, page 1 in the A/C (see box on page 90) will determine the class of vehicle needed to meet your requirement.
The A/C is divided into four chapters.
Chapter 1. This covers general characteristics, ergonomics, and design criteria. This chapter can be used verbatim after considering several options. Paragraph 5 c allows the purchaser to specify radio operating equipment for compatibility with existing equipment. The note in paragraph 14 on page 4 of the specifications permits the purchaser to specify a winterization system (as described in paragraph 50 in section 6 of chapter 2) if the climatic conditions combined with the normal operational procedures warrant its use. Finally, paragraph 14.j allows the purchaser to specify specific lighting equipment, which may include an on-board AC generator, if desired.
Chapter 2. This covers the vehicle’s automotive system. It describes mandatory minimum requirements for the frame, body components, cab and accessories, driveline and controls, electrical system, engine and accessories, and automotive performance. Again, all of the wording can be used verbatim, and the purchaser has the ability to specify the following optional items, if desired.
- Paragraph 22 allows a pintle hook to be specified as an alternative to the rear towing hooks.
- Paragraph 28.a permits additional crew positions to be specified if a local operational requirement.
- Paragraph 30 references an amber (yellow) beacon indicator. This beacon can be provided as an option, if desired.
- Paragraph 32.a(3) allows the purchaser to specify a vehicle-mounted auxiliary air compressor to include a pull-away or auto-eject 110V electri-
- cal connection mounted on a readily accessible external portion of the vehicle. This compressor would be provided in addition to the normal engine-driven air compressor and would maintain vehicle air system pressure at an operational level while plugged in to station electricity.
- As an alternative to the auxiliary air compressor, a pull-away or autoeject air connection for charging the vehicle’s air system from an external air source may be specified per paragraph 32.a(4).
- Paragraph 39.c allows the purchaser to specify lighting as may be required by local operational conditions.
- The 110V connection described in paragraph 40.d may be mounted as specified by the purchaser. If the optional auxiliary air compressor is selected, two connections may be necessary because of amp draw considerations.
- Paragraph 45.c allows the purchaser to specify a muffler, particularly if the vehicle is to be started and run inside an enclosed area.
Chapter J. This covers the vehicle’s fire extinguishing systems, including the foam concentrate and water systems as well as the optional dry chemical and Halon 1211 systems. It also defines the requirements for handlines and hose reels, ground sweeps, bumper turrets, primary (roof) turrets, and undertruck nozzles. Agent system performance also is defined in this chapter. Section 1 describes a dry chemical system option, while section 2 describes an alternative Halon 1211 system option. Halon 1211 is a CFC that has been shown to be ozone depleting.
When specifying the Halon 1211 option, exercise care in determining federal, state, and local regulations regarding its present use and any future restrictions that may be imposed.
Section 5 may appear somewhat confusing, as it does not specifically address all of the handrail/hose reel combinations that could be provided. The key points to remember are:
- There shall be a minimum of two
- reeled or woven jacket handlines for the discharge of foam and water, and they shall not be on the same side of the vehicle.
- Either two reeled or two woven jacket handlines or one of each will satisfy this requirement.
- If the optional dry chemical or halon fire extinguishing system is specified, the handline for that agent may be “twinned” with one of the foam/water handlines. Otherwise, a separate handline for the agent would be provided.
In Section 6, the purchaser may specify several options. In paragraph
83, either a fixed ground sweep or a movable bumper turret may be specified.
Paragraph 84.a gives the purchaser the option to select either a manually operated primary (roof) turret where operating forces are less than 30 pounds or a turret where higher flow’ rates would require a power-assist feature to meet the 30-pound maximum operating force (paragraph 84.d). Paragraph 85 allows the purchaser to select the option of undertruck nozzles, if desired.
Chapter 4. This covers quality assurance and is to be used verbatim. There are no purchaser-selected options or unique vehicle requirements in this chapter. Section 7 of chapter 4 describes the minimum agent performance that must be met. This is a good time to order additional agent for training and reservice.
After you have determined which FAA-permitted options will be used, you must decide whether you want to add any “unique vehicle requirements” that are not specified in the A/C. Remember, however, that any of these “unique” items must be adequately justified to the FAA for it to issue approval. Examples of these items are a limited structural system (to combat structure fires within the airport boundaries), air-conditioning, an elevated waterway with piercing applicator (to fight interior airport fires and fires in tail-mounted engines), antilock braking systems, and robotic-type turrets.
Another important area associated with this vehicle is the recommended equipment for rescue operations section of the Advisory Circular Table A3-1. Let’s discuss this table and highlight areas that can present problems. For example, say you did not elaborate on the item “forcing tool, hydraulic or pneumatic” (you assumed this was a power-operated rescue tool.) When your vehicle arrives and you start unpacking the equipment, you may be quite surprised to find that your forcing tool is a piston-driven, hand pump-type spreader instead of what you actually need. Remember, careful research, planning, and justification are the keys to acquisition within this table.
It is to your advantage to contact as many manufacturers of this type of vehicle as possible. Ask if they are aware of any performance-enhancing options or features not included in the A/C that still would be fundable by the FAA.
After-sales service and parts support is a very important issue. If the vehicle is funded by the FAA, a manufacturer’s record relative to after-sales service and parts support cannot be a factor in making an award. This is unfortunate, because FAR Part 139 limits ARFF vehicle downtime to a maximum of 48 hours. Subsection 139.319(h)(3) of FAR 139 states, “Any required vehicle which becomes inoperative to the extent that it cannot perform as required shall be replaced immediately with equipment having at least equal capabilities. If replacement equipment is not available immediately, the certificate holder shall so notify those FAA’s regional Airports Division Managers and each air carrier using the airport in accordance with sub-section 139 339. If the required index level of capability is not restored within 48 hours, the airport operator, unless otherwise authorized by the administrator, shall limit air carrier operations on the airport to those compatible with the index corresponding to the remaining operative rescue and firefighting equipment.”
This means that if a vehicle is out of service for more than 48 hours, the airport may see a reduction in service, as the model of aircraft servicing the airport may have to be downsized (for example, 727s to DC-9s). Because of the 48-hour rule, you may want to include optional items or services that may not be fundable by the FAA but that will give you peace of mind. Such items include factory maintenance training, service inspections, and recommended spare parts kits.
Look to airports of comparable size as important allies in completing your project. They can provide valuable information to help you make sure that you have not overlooked anything, such as any “unique” items previously discussed.
Perhaps one of the most important but often overlooked considerations is the standard lead time for this type of specialized vehicle. It can take up to 300 calendar days from the time a manufacturer receives the order until the vehicle is delivered. It is critical, therefore, that consideration be given to this fact at every step in the procurement process from the time the project is conceived.
AIRPORT INDEX

Whether working on this project alone or as a member of a committee, it is imperative that you follow these procedures:
- Elect a committee chairperson (if you’ve chosen the committee route).
- Define the scope of the project.
- Set your goals.
- Determine potential problem areas.
- Develop a timetable.
- Establish reasonable meeting intervals.
- Support all changes or additions with documentation in the form of addenda.
- Document and distribute to the appropriate individuals all information pertinent to the project.
Preliminary rough draft specifications. Once the draft specifications incorporating all changes have been completed, send copies of the document to the FAA district office and to the leading manufacturers for their comments prior to issuing a formal bid package. Providing the opportunity for the FAA and manufacturers to review the preliminary specifications may minimize or eliminate potential problem areas and avoid protests. In reality, if you fail to solicit the manufacturers’ input about what they can or cannot build or provide, you just may have precluded some of them from competitive bidding. On receipt of input from all concerned, revise the specifications, if appropriate.
Final rough draft. When you are confident that you have a complete set of technical specifications that comply with the A/C, you then can attach any special conditions or other federal, state, or local requirements that apply and send this package to the FAA for the final approval.
VEHICLE CLASS, MINIMUM USABLE WATER (RATED CAPACITY)

This is where consistent documentation is important. Generate file copies of all correspondence and documents throughout the process. On FAA approval, send out copies of the specifications to all interested bidders. Allow at least 30 calendar days between the time you send the invitation-to-bid package and the bid opening date. This enables each manufacturer sufficient time to prepare a comprehensive and responsive proposal.
Bid opening. On the bid opening date, the sealed bids are opened and the prices read. This is public information and you, your committee, and all concerned should attend. Manufacturer representatives may be present to review competitors’ proposals unless local laws or ordinances prohibit their attendance. After the individuals) responsible for making the recommendation have determined that the lowest bidder also has submitted a responsive proposal (meets FAA A/C 150/5220-10A), an award can be issued subject to FAA concurrence.
PRIVATE FUNDING
This type of funding is used when FAA funding either is unavailable or an airport chooses not to use it. Privately funded purchases issue no mandates to utilize A/C 150/5220-10A as a guide for wTiting specifications. (Its use is mandatory only when FAA funds are involved.) However, you always should use the A/C as a reference companion.
Basically, the process used is identical to that used for an FAA-funded vehicle. The main difference is that with private funding you can use the A/C as a model and modify and/or add to it, depending on your airport’s needs and, of course, budget constraints. Any type of special option or piece of auxiliary equipment can be considered; however, if the option is too rare, manufacturers may elect not to bid on it and may propose an alternative.
Ultimately, bids will be submitted and opened, and prices read. You will determine if a bid is responsive based on the number of exceptions and alternatives presented. Under private funding, you can specify state-of-theart features, such as antilock brakes for 4 X 4 vehicles, that are not addressed in the A/C. The paramount advantage of ordering a vehicle using private rather than FAA funding is that you can specify exactly what you w’ant, including all items you believe necessary for the vehicle to accomplish its mission. You must, however, be realistic. There is a tendency to order too many “bells and whistles,” which can impact axle capacities and exceed the gross vehicle rating of the chassis.
Regardless of how the vehicle is funded, manufacturers are an excellent source of information and should be consulted on a regular basis from the time the project is initiated and approved until the final specifications are sent out.
When the bids are opened, you will make the final determination as to which bidder best meets your requirements. Clearly understand that the lowest bidder may not be the most responsive to your needs.
Writing specifications for an ARFF vehicle need not be a complex issue. As with any project, the keys to success are an understanding of and thorough preparation for the process.*