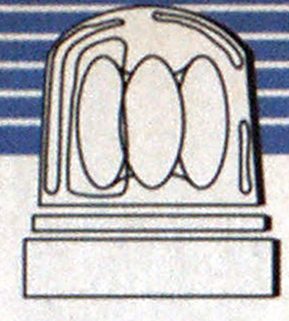
APPARATUS DESIGN FOR DRIVER/OPERATOR SAFETY
VOLUNTEERS CORNER

Recent changes in the standards for fire apparatus, coupled with manufacturers’ design options and technical innovations, have greatly improved safety conditions for fire apparatus pump operators/drivers. The location chosen for the pump operator’s controls also will play a part in safety. Currently, pump control panels most often are located midship on the left side; occasionally, they are located on the right side. Manufacturers offer a number of other position options; and with the developing technology of the microprocessor, the pump operator’s panel can be located anywhere.
Regardless of pump panel location, several safety items should be considered. They include improved nonslip working surfaces and running boards, large steps, and better handrails, all of which reduce the possibility of slipping. Ground lights can be placed below the running board, front bumper, and rear step to aid moving and working around the vehicle, especially when tools or fittings are dropped or footing is unsure. In the cab, the spring brake (air brake) control should be placed in a location accessible to both the driver and the officer. A speedometer on the right side and an open compartment light also may add to the operator’s well-being. A foot switch in place of a pull chain will allow the driver to keep both hands on the steering wheel when operating the air horn. All cab instruments and controls should be within easy reach of the driver.
SAFETY WHILE PUMPING
Several improvements can be made to enhance safety during pumping. A shift interlock and “pump-engaged” indicator light must be installed in the cab. A light on the pump panel itself must be present to indicate that the pump is in gear before the throttle is opened. All intakes and discharges must be equipped with caps tested to 500 pounds per square inch. As per NFPA 1901, Pumper Fire Apparatus, discharges three inches or larger in diameter no longer are permissible on the pump panel and must be equipped with slowclosing valves that take at least three seconds to go from fully open to fully closed. Relief valves are now required on the intake as well as the discharge side of the pump, to prevent water hammers from damaging the pump or plumbing, especially while using large-diameter hose.
Flowmeters that accurately measure discharge may be provided for attack lines, limiting the chance that a hose will burst or a coupling will be blown off (especially when the call of “More pressure. more pressure!” is made). Flowmeters also will ensure proper water delivery’ to the nozzle and save the pump operator from the wrath of the firefighter at the nozzle. Due to the lower working pressure of large-diameter hose, some departments prefer to have a pressure gauge on these discharges as well.
PUMP PANEL LOCATION
Top-mounted pump panels can enhance safety by removing operators from the hazards of traffic. They also give the pump operator a better vantage point from which to observe operations. Since there are no intakes or discharges on the panel, there are no hoselines to trip over or cross-mounted preconnects to duck. There is, however, an additional slipping hazard created from having to climb up to and down from the top-mounted position. In some instances, the operator can become the moving target of a top-mounted master stream device.
An inside-mounted panel in a command or extended cab is similar to a topmounted panel. It may have reduced visibility, but it keeps the pump operator out of temperature extremes and inclement weather. It also affords increased protection for the operator in unruly neighborhoods and against civil disturbances. A well-insulated cab also provides a quieter work area.
An intercab location at the front of the apparatus (not the same as a front-mounted pump) may not have discharges but will have an intake. There may be a single preconnected “bumper line” in a well, but this is not an obstruction to instrumentation and does not require the operator to duck around it. It could, however, be a tripping hazard for firefighters.
One of tiie simple changes that could be made to improve the operator’s safety is to remove all intakes and discharges from the pump panel. On conventional side-mounted panels, they can be placed on the opposite side of the unit, in the front, in the rear, or in any combination of these locations. Some departments have initiated this trend by removing only the discharges. Since many departments have an operating procedure of pulling past the fire building with the attack pumper to observe three sides, relocating all preconnects to the rear of the vehicle may provide for smoother operations.
With a rear pumping station, the intakes and discharges can be located at the sides or front. From this position, however, operators may have to contend with rear preconnects, including heavy attack (connected to 2’/2-inch hose) and master stream devices (connected to three-, four-, or five-inch hose). Problems may arise when hoselines or ladders are removed from the rear. One advantage of this location is that the pump operator is accessible for pulling hoseline, breaking couplings, and making connections without having to run around the apparatus to help with these chores.
OTHER CONSIDERATIONS
Regardless of where the pump panel is located, the pump operator should have breathing apparatus available. An SCBA mounted in an easily accessible compartment is recommended. In addition, hearing protection should be provided. In many cases, this can be done through the use of radio earphones. If the pump operator is expected to make available or put in service any heavy equipment (portable monitors, fans, etc.), that equipment should be mounted in a low and convenient place. Since the pump operator is still responsible for the firefighters on the end of the hoseline while performing these additional duties, everything possible should be done to expedite them.
In the case of apparatus equipped with a water tower, aerial ladder, or aerial platform. the pump operator must be protected from becoming a ground if the device comes in contact with electrical wires. This can be done by providing at the pump controls a platform for the operator.
Many of the options described above depend on where the pump is placed in the apparatus. As specifications are developed, maximum consideration should be given to this factor, since it greatly impinges on the safety of the pump operator. Pump panels that are front-mounted, under the cab fore and aft, behind the cab, and at the rear of the vehicle are all possible with today’s technology.
A properly designed chassis will enhance the overall safety of the unit during response and operation. This includes everything from tires to axles, suspension, frame rails, weight distribution, center of gravity, engine size, brakes, and electrical systems. Consider antilock braking systems and nonslip rear ends.
Due to the vast array of electrical equipment on modern apparatus, electrical loads may exceed alternator output. Some modern diesel engines will stop if the voltage becomes too low. Thus, alternator output should be compared with electrical load requirement and appropriate load management devices installed, including low-voltage alarms (audible and visual) and an amp meter to monitor battery conditions. Both should be installed on the operator panel.
Think pump operator safety when your department purchases a new apparatus. It makes for a safer vehicle and safer fire department. Injuries are costly.