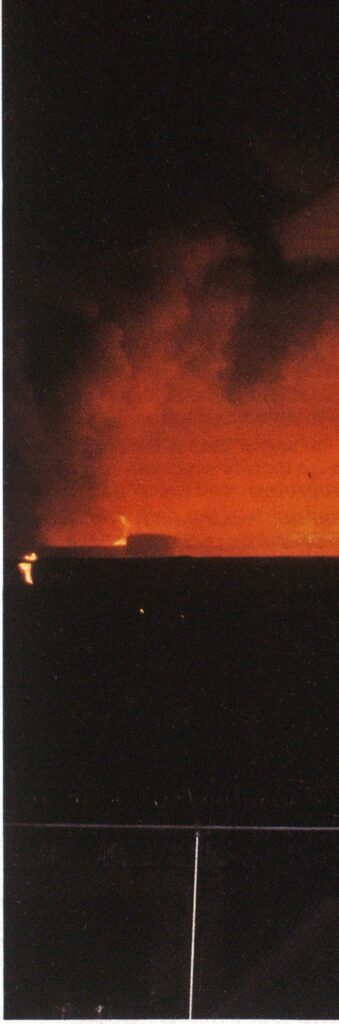
SAVING BY THE CODE
HAZARDOUS MATERIALSLS
Code enforcement, multiagency cooperation, and effective fireground operations paid off during this Philadelphia chemical fire.
ON WEDNESDAY, September 27, 1989 at 2023 hours, the Philadelphia Fire Communications Center received notification of a fire at the Purolite Chemical plant. The fire, which would rapidly expand to six alarms and be fought by approximately 200 firefighters utilizing 30 fire apparatus, was not exceptionally voluminous or beyond the resources of any large metropolitan fire department. In fact, Philadelphia firefighters have fought many conflagrations of equal or greater magnitude in recent years. However, given the large number of chemicals present including, among others, bromine, divinyl benzene, hydrochloric acid, propylene dichloride, styrene, and sulfuric acid, the blaze posed a significant hazard for everyone present. Before bringing the fire under control, the experience and expertise of the fire department and several support agencies would be severely tested.
The successful mitigation of this emergency was due to a great extent to groundwork laid long before the fire occurred. To fully understand how enforcement of the Philadelphia Fire Code figured in averting this near disaster, a historical background of the facility and corrective actions taken is necessary.
HISTORICAL PERSPECTIVE
Purolite began operations in 1982 and initially employed only 18 people. It leased a section of the facility and shared it with several other tenants. Purolite quickly grew to a 24-hour-aday, seven-day-a-week operation and in 1987 purchased the entire facility. Only one tenant, in the process of relocating, remained at the time of the fire.
The complex consisted of three buildings that were all interconnected by 15-foot horizontal openings protected by sliding doors with fusible links. It measured approximately 650 feet in length and 150 feet at its widest point. The buildings each were two stories high. Building A, built near the turn of the century, was of ordinary masonry and wood construction and measured roughly 100 feet by 400 feet. It was utilized as the production area and contained the majority of the chemicals. Buildings B and C were additions of combined masonry, metal, and wood construction. Although they were of a less combustible nature, these two buildings were used for warehousing and storage and contained a heavy fire load. Two tanks containing sulfuric acid and bromine were also located in these buildings. All three of the aforementioned structures were protected by a combination automatic wet and dry sprinkler system.


The Philadelphia Fire Department’s first emergency response contact with Purolite occurred late in 1988 when a haz-mat team responded to a sodium hydroxide vapor leak that was traced to a malfunctioning scrubber. During the next few months there were three additional haz-mat responses to this location, the third of which involved a 3,900-gallon release of divinyl benzene into the city sewer system. This spill resulted in the evacuation of water department employees from one of the city’s ultramodern sewage treatment plants.
(Photos by Philadelphia Fire Department.)
From December ’88 to March ’89 the facility was inspected on several occasions and fire code violations were issued. It should be noted that the fire department did not possess any enforcement power at this time. Rather, this authority came under the domain of a separate city agency, the Department of Licenses and Inspections (L & I). This has since been amended and now both the fire department and L & I can issue cease operation notices if conditions warrant such actions.
After the divinyl benzene spill, the fire department requested a large-scale inspection of the facility. The lead inspectors were from the Fire Marshal’s Office, the Hazardous Material Administrative Unit, and L & I, but several other city agencies and environmental officials from the state and federal government also attended. Based on existing conditions at the time of the inspection, an immediate notice of cease operations was posted. Although the facility was closed only for a brief period, the desired effect was achieved as management moved quickly to bring the complex into compliance.
Some of the violations that existed were nonlabeling of tanks and pipes as to their contents, improper storage of hazardous materials, an inoperative sprinkler system, and noncompliance with SARA III—specifically, failing to provide MSDS forms for hazardous materials stored or used. Besides correcting these and other violations, the company hired an environmental consultant and devised emergency operating plans. The facility was in compliance with all existing regulations at the time of the September 27 incident. In fact, at the request of the Hazardous Material Administrative Unit, the U.S. Environmental Protection Agency conducted a complete chemical safety audit just two weeks prior to the fire. All parties agree that Purolite’s conformance with the necessary requirements and implementation of improvements in the overall plant operation made the goal of controlling the fire more attainable.
RESPONSE
Fire was already spreading rapidly through building A as the fire communications center transmitted the first alarm. Earlier that day, both the wet and dry sprinkler systems had been shut down due to a malfunctioning clapper valve. After repairing the valve, the company’s maintenance team started repressurizing the system with air. Since it would be close to 2200 hours before they’d have sufficient air pressure to bring up the system, the team left the premises, planning to return later in the evening. This information was not immediately passed on to the fire department.
A thick column of smoke in the night sky was visible to responding units several blocks away. Once on the scene, firefighters made a quick assessment entry into building A. All employees were accounted for and had exited the building. Fire was evident in the first and second floors. A handline was stretched and interior size-up indicated that fire involved the rear one-third of building A. Because of the possibility of collapse and the amount of fire threatening chemical storage, a defensive strategy was ordered. Interior firefighting forces were withdrawn. As additional alarms were struck, numerous support agencies responded and Fire Commissioner Roger M. Ulshafer arrived to take command of the fireground.
Hoselines were stretched and unmanned monitors placed into service. These streams were directed on the tanks of propylene dichloride, styrene, and divinyl benzene that were located directly outside building A. This section was heavily involved with fire, threatening the three tanks. The monitors prevented the fire from reaching the tanks and kept their contents cool.
To the south, 10 yards from the facility, was a below-grade railroad line utilized by Amtrak as part of its Northeast high-speed corridor. This line was temporarily shut down as a precaution. A residential area two blocks away was directly in the path of a plume of smoke carried by northwest winds. With the fire still spreading, Commissioner Ulshafer ordered an evacuation of several square blocks of homes. The Philadelphia Police Department coordinated the evacuation and the Philadelphia Office of Emergency Management made arrangements with a nearby church for sheltering the hundreds of evacuees.
Supply to the sprinkler Siamese was ineffective because the second-floor collapse destroyed the system’s integrity. The fire continued to spread and by now building A was almost totally involved. Two significant results of Purolite’s compliance with code requirements now became apparent: First, when the company first started operations at this location L & I had ordered the production area enclosed with a masonry wall. Several chemicals were stored there in 20 tanks of various sizes. The fire wall achieved its optimum goal, as this section of the building was the only area spared from total destruction. Second, the cylinders containing highly toxic bromine, initially positioned in the rear of building A, had been relocated to a special storage area in the rear of building C, which was not endangered.


Firefighters had completely surrounded the burning building and were engaged in strictly defensive actions. Due to the difficult terrain conditions, including the railroad tracks to the south and numerous industrial buildings to the north and west, long leads were required.
At this point, the water department played a major role. First, by opening a nearby grid control valve it was able to divert additional water to the scene for firefighting. Second, due to the large volume of water being utilized and the impossibility of diking the runoff, crews began monitoring nearby sewers for signs of chemical contamination. As building A became heavily involved, the crews detected hydrochloric acid in the sewers; later, sulfuric acid became evident. This was attributed to a complete meltdown of two fiberglass tanks containing hydrochloric acid and sodium hydroxide. Additionally, one waste water holding tank failed, and there was believed to be a failure in piping containing sulfuric acid as well.
The water runoff from firefighting to the sewer system was dangerously acidic. The water department called on a nearby chemical plant for assistance. This plant treated its discharge water with neutralizing lime (basic solution) and directed it into the same sewer line as the firefighting runoff. This effectively reduced the dangerous acidic levels and the environmental threat was abated.
With flames now visible for miles against the evening sky, the fire department’s communication van was a hub of activity. Fire officers, officials from support agencies, and management personnel from Purolite assembled there. Valuable information concerning the chemicals involved, the location of products within the building, and environmental conditions in the surrounding community was exchanged.
By this time the entire roof of building A had collapsed and metal I-beams began to twist and fail as they were exposed to the intense heat. This, in turn, led to failure of huge sections of the exterior walls. With chief officers carefully watching for any additional signs of impending wall collapse, fire crews moved in and out quickly to redirect streams from their monitors.
The main exposure problems facing firefighters were the interconnected structures at the rear of the complex. Due to the inaccessibility of this area, it required several engine companies combining all of their hose to place just one line into service. The stretch required that firefighters walk across rooftops and place ladders between voids. In answer to these difficulties, Commissioner Ulshafer deployed the largest number of firefighting personnel to this section. At one point, as a section of rear wall tumbled down, the fire began extending into a large pile of combustibles in building B. Crews using mobile lines moved in quickly and extinguished the fire. No further extension occurred in this critical exposure and the fire was confined from that point on.
At 2359 hours the fire was declared under control. With the exception of the production area enclosed by the masonry wall, building A was reduced to a pile of smoldering rubble.
A technical assistance team from the EPA, augmented by technicians from the Air Management Division of the Philadelphia Health Department, monitored the air in the surrounding community. After finding negative readings, they allowed the evacuees to return home.
With the fire under control, the arduous task of overhaul and site restoration began. It took six days for the final hot spot to be extinguished and the last pumper to leave the scene. In the days immediately following the fire, air and water sampling continued to ensure the safety of the community and the firefighters still on location. No additional hazards were detected.
Although some sections of the building were in imminent danger of collapse and thus too dangerous to access, other areas had been so totally devasted that they were safe for entry. However, fire marshals were not permitted to enter the area of fire origin until a team of EPA technicians, wearing Level B entry suits, had tested the area and found it safe from any hazardous substance residue.
Purolite management met with city and federal officials to discuss proper cleanup, disposal of the fire-generated hazardous waste, and demolition of the remnants of the building.
LESSONS REINFORCED
- Judicious enforcement of fire codes and environmental regulations can prevent catastrophes.
- Cooperation between private industry and the fire service is essential. It is noteworthy that in the months preceding the fire, during the emergency itself, and in the postincident period, Purolite cooperated fully with the fire department.
- Segregating high-risk sections of buildings with fire walls is a major factor in control of fire. It increases the probability of successful offensive attack.
- Quick response and assistance from support agencies is vital at industrial facility fires. This is especially true in those areas dealing in large quantities of varied chemicals. The water department’s alert and imaginative thinking prevented what could have been a serious environmental threat.
- Once the initial emergency has been controlled, planning and logistics should account tor lengthy postcontrol operation.
- Fire officials should be notified immediately whenever a sprinkler system is placed out of service for any reason and for any length of time. Notification of inservice also must be required.