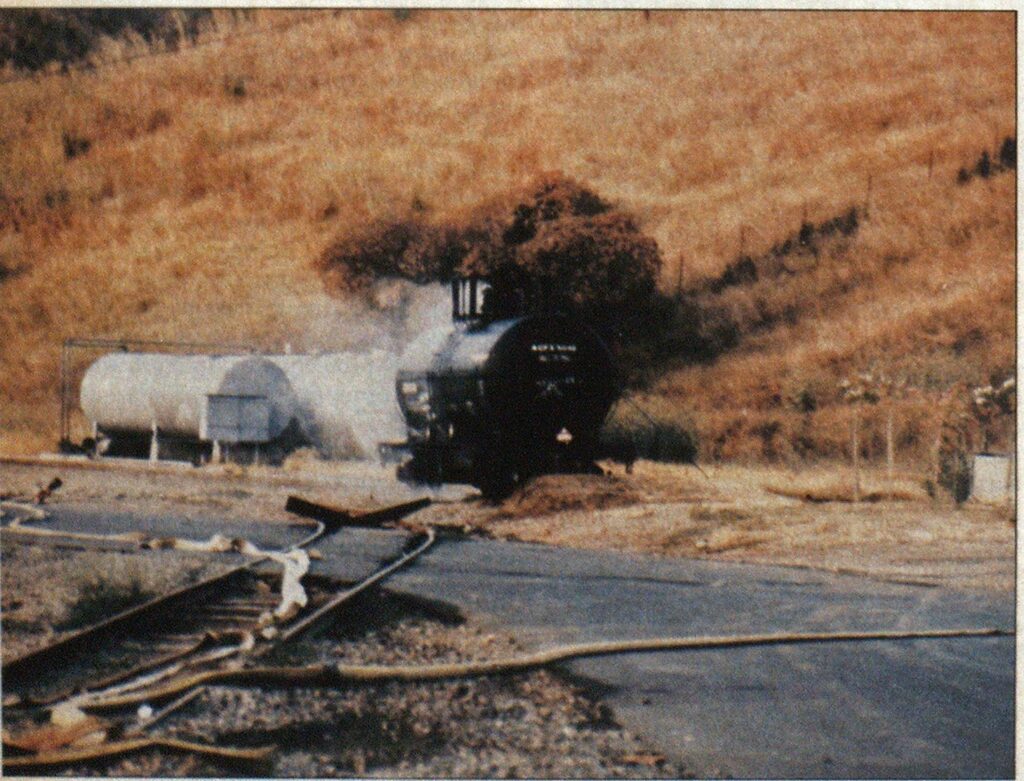
Chemical Protective Suits: A Fire Chief’s Followup
HAZARDOUS MATERIALS
On August 12,1983, a tank car loaded with dimethylamine* (DMA) located on an industrial railroad track at A. J. Chemicals (AJCHEM) in Benicia, CA, began leaking vapor from its sample line. The Benicia Fire Department was summoned four hours after the initial discovery. Of the many lessons that we were to experience during the mitigation process, the most frustrating and dangerous was the failure of the four chemical protective suits (CPS) that were used by the Benicia and San Francisco Fire Departments.
A few hours into the incident and after relatively little exposure time to the suits, the facepieces shattered, seams opened, gloves began to break down, boots began to come apart, and, what is most important, the encapsulation integrity was broken and the chemical hazard was allowed to enter the envelope and attack the firefighters.

I wish to give a brief overview of what has been a costly lesson for our departments’ firefighters, but what could result in sweeping changes and the establishment of standards by which these suits will be manufactured and measured in the future.
We put blind trust in the CPS we purchased. When you buy safety clothing costing $700 to $1,300 per item, you expect that the equipment will protect the firefighter from chemical risk factors. Some of the manufacturers neatly package away liability disclaimers inside the suit or into documents denying any responsibility after the suit is purchased. This basically says, “You bought it, you used it, now it’s your problem.”
The cost of CPS has doubled in the last 14 months. It’s ironic that costs escalated after fire departments became involved in hazardous materials. Many fire equipment vendors who sell the CPS suits to fire departments have little or no training in the donning, use, inspection, and care of CPS. The manufacturers are even remiss in producing videotapes to instruct the departments in proper use. Again, the manufacturers are more concerned with the liability side of a program.
Often fire departments will specify modifications to suits. These modifications are not tested or certified by an independent testing agency. Zippers and interlocks that seal the CPS shut have always been a problem. No improvements are being made to this feature. Cooling and ventilation is often forgotten in the sales process, and purchasers are often affected by dollar constraints and will overlook the environmental factors.
The shelf life of suits, whether they’re on apparatus, in storerooms, or on the vendor’s shelf, has not been determined. Is the suit good for five to ten years? The durability and temperature limitations of fabric characteristics are unknown. How will the fabric stand up against cryogenics (liquid oxygen, liquid nitrogen)? What is its heat resistance to oxidizers and other heat generating chemicals? How will a suit hold up against venting pressure from a gaseous atmosphere or a railcar’s vapor pressure release? What happens to a CPS after decontamination by an industrial cleaner? Is the suit safe? How many times can you decontaminate a suit and still use it in the field?
* Dimettiylamine (DMA) is a colorless gas in vapor form, brown in liquid form, very flammable, extremely toxic and corrosive. DMA is shipped in the liquefied gaseous pressure mode, under a vapor pressure of 50 to 60 pounds. The chemical is used in rubber production, vulcanizing, tanning, soaps, and detergents. At AJCHEM, it is used to make a tan ning debilitating chemical, dimettiylamine sulfate.
DMA boils at 45°F, and the vapor has a very pungent odor of fish at low concentrations and of ammonia at high concentrations. The vapor is extremely irritating to the eyes, skin, and mucous membranes. Skin contact could produce burns. The chemical is anhydrous, and mixing with water would cause increased vapor dispersion. It is extremely corrosive to copper, zinc alloys, aluminum, and galvanized surfaces.


CPS training
Training with CPS is one area that shouldn’t be taken lightly. Every member of a department should have a basic understanding of CPS operations with classroom and practical applications. Personnel should be trained in donning and removing CPS. They should also learn how to assist other personnel in donning and removal.
Training should also cover emergency removal of CPS, emergency hand signals, and the decontamination process. How other personnel will support the operation if an air line mask is used or an air bottle is exchanged needs to be addressed as well. Videotape is an excellent method for standardization and repetitive training.
What type of suit to use
The major choice of what type of suit to use is either encapsulated CPS or nonencapsulated CPS. The U.S. Coast Guard conducted a study of 985 chemicals and found that 41% required encapsulated CPS, 44% required nonencapsulated CPS, and 15% required rain gear (disposable gear).
One of the major concerns with the non-encapsulated CPS has to be with self-contained breathing apparatus (SCBA) contamination. The National Institute of Occupational Safety and Health (NIOSH) issued a strong warning (after the Benicia incident) that breathing apparatus contain numerous plastic parts, harnesses, straps, and working parts that can become contaminated in a vapor release.
Double protection versus singular protection
The encapsulated CPS allows SCBA to be worn internally, while the nonencapsulated CPS exposes the SCBA to the hazardous environment. In the Benicia AJCHEM incident, we used both types of CPS. The facepieces on two encapsulated CPS failed and vapors entered one suit. The 4.5 Scott facepiece inside the suit received moderate damage. If the firefighter did not have the double protection, I firmly believe he would have received major injuries. The mask of the non-encapsulated suit also failed on the San Francisco CPS units. The safety margin for using the encapsulated CPS should be evaluated in lieu of the need to change air bottles on non-encapsulated CPS.
What type of fabric?
Rubber butyl appears to be the most widely used and manufactured CPS. Butyl is compatible with about 70% of all chemicals. The other fabrics are propylene and Viton. Also, a wide range of fabrics are used in disposable suits.
Damage to suit
During the chemical vapor release incident, four CPS suits lost integrity. The facepieces on all suits failed when exposed to anhydrous DMA in vapor form. The facepieces fractured and the cracks penetrated completely through the CPS facepieces. The DMA chemical attacked anything made of polycarbonate material. The chemical attacked the CPS rubber gloves. Nearly one year later, even after decontamination, the gloves remain sticky and unusable. Fire boots failed at the heels where they joined the soles. Seams failed where glue was used to join the fabric.
The knees and elbows of CPS are particularly susceptible to damage. CPS were not designed with either the firefighter or all-risk situation in mind. The zippers often jam and fail, and the cost to repair the built-in zipper is exceptionally high. Air line fittings and vents are made of plastic and can be damaged quite easily.
Problems with CPS suits
The purchaser usually buys a suit to be used in a number of chemical atmospheres. The manufacturers’ brochures only address the chemical and the type of suit fabric that it is compatible with. The listings fail to discuss the compatibility of other CPS related components, such as gloves, facepieces, SCBA view windows, and boots. A compatibility matrix needs to be developed to discuss these as well.
CPS should be stored according to manufacturer’s recommendations. Needless to say, probably the worst thing to do with suits is to cram them into a bag where creases and unwanted folds will set in. Suits are sized to a person’s height. Most manufacturers do not make suits for people over six feet, three inches. The fit factor makes selection important for smaller departments that can only afford two to four CPS. Tall people usually don’t qualify as suit wearers.
Communications inside CPS are almost impossible. Hand signals for users are not always established in order to alert someone that a problem is in progress inside the CPS. The Benicia and San Francisco Fire Departments use a throat microphone and an amplifier module called a “loud mouth.”
The proper donning procedure takes a considerable amount of training time. Anyone who is required to use the suit should have some plan on how to get out of it in a hurry if necessary. It is reported that some personnel carry hunting knives inside the CPS for quick exit.
Air bottle exchange can be tricky if the suit is encapsulated. The suit must be decontaminated properly so that the handlers changing air bottles do not become harmed from chemicals on the suit. This exchange feature should also be practiced with team members.
Presently, suits are not certified by any agency. Many people felt NIOSH had this responsibility, but this was untrue. The National Transportation Safety Board (NTSB) has suggested in Safety Recommendation 1-84-1 through 1-84-5 that collateral fire association work with the National Fire Protection Association (NFPA) and the American Society for Testing and Materials (ASTM) in the development of standards for design and construction of chemical protective suits.

Decontamination process
Any department that owns a CPS should have a standard operating procedure (SOP) established for CPS decontamination procedures. Decontamination is much more than using a 1 3/4-inch charged hoseline to wash down an exposed suit. It will not do the job properly and will discharge too much water. Runoff from decontamination should be contained. Some departments are using old-fashioned washtubs or kiddie pools with low flow shower heads to reduce water use. Toilet brushes are used to scrub down the CPS.
Personnel should step from the catch basins into a plastic bag and remove the CPS into the bag. The bag should then be tied and secured until the CPS can be properly cleaned. Suits should be sent to firms that specialize in commercial cleaning and inspection. Most manufacturers do not provide specifications on procedures or training in decontamination.
Fire departments have a lot more to learn in this area. One of the best ways is to discuss the decontamination process with experienced hazardous material teams.
Recommendations
The following are some recommendations for those using CPS:
- Double gloving. A double gloving process is highly recommended
- since the CPS gloves are one of the weakest areas. The choice of a sacrificial arms-length glove is very cost effective. This second glove is then taped down with duct tape to prevent liquid or vapor from entering between the two sets of gloves. A small rip in the CPS integral glove disables the suit. The sacrificial glove gives an additional layer and an added safety margin.
- CPS post accident inspection and cleaning. This function is imperative after CPS is used in a hazardous material environment and when it has been exposed considerably in vapor concentrations. Many agencies are choosing to have the CPS cleaned and inspected by a commercial firm.
- Acid suit marking. A method should be developed whereby suits are
The following is an excerpt from the National Transportation Safety Board’s (NTSB) safety recommendations issued after a study of the facts surrounding the Benicia chemical spill and the failure of the fire department’s chemical protective suits (CPS):
“… In its investigation of the CPS suit failures during this emergency, the Safety Board contacted other fire departments and fire-related associations. Those contacted related many similar problems with CPS suits. Several fire departments reported firefighter injuries resulting from hazardous materials entering the CPS suits through seams. Others related their concern about firefighter injuries as a result of the facepiece losing its transparency, or as a result of chemical vapors entering the CPS suit through cracks in the facepiece, resulting in short-term or long-term exposure of emergency response personnel and others to health hazards. Moreover, the Safety Board learned that the U.S. Coast Guard, the Environmental Protection Agency, the U.S. Fire Administration, and the National Institute for Occupational Safety and Health have concerns about the adequacy of existing protective equipment used in chemical emergencies. Each has programs directed at improving certain aspects of these suits and at better defining the conditions under which they can be used safely . . .
“The Safety Board believes that standards are needed for the construction and testing of CPS suits and protective face masks used by emergency response personnel in the handling of transportation and other hazardous material emergencies. There are projects underway to improve the usefulness of CPS suits, but the efforts are not fully coordinated. Because most fire departments, as well as many other emergency response agencies, look to the National Fire Protection Association (NFPA) for guidance concerning protective clothing, the Safety Board believes that the NFPA is the logical place for such standards to be developed.
“Therefore, the National Transportation Safety Board recommends that the National Fire Protection Association:
“Develop and issue standards for the design and construction of chemical protective suits, including facepieces whether or not they are an integral part of a suit. (Class II, Priority Action) (I84-1)
“Assist the American Society for Testing and Materials F23.5 Committee in developing and issuing standards for both initial certification and periodic recertification of chemical protective suits. (Class II, Priority Action) (I-842)
“Establish standards for both the content and format of chemical compatibility information which should be provided by manufacturers of chemical protective suits. (Class II, Priority Action) (I-84-3). . .
“Therefore, the National Transportation Safety Board recommends that the International Association of Fire Fighters and the International Association of Fire Chiefs:
“Work with the National Fire Protection Association and the American Society for Testing and Materials in the development of standards for design and construction of chemical protective suits. (Class II, Priority Action) (I84-4). ..
“Therefore, the National Transportation Safety Board recommends that the United States Coast Guard, the Federal Emergency Management Agency, the Environmental Protection Agency, and the National Institute for Occupational Safety and Health:
“Work with the National Fire Protection Association and the American Society for Testing and Materials in the development of standards for design and construction of chemical protective suits. (Class II, Priority Action) (I84-5).”
- marked with numbers so that the team members can be identified inside a hazardous environment. Special considerations should be given to the use of reflective tape or fabric for nighttime operations.
- Purchase delays. Fire departments should be aware that CPS are not routinely stocked in quantity on ven-


- dors’ shelves. Extended delays of four to six months are not uncommon when modifications are requested.
- Acid suit view windows. I recommend that the CPS view window be covered with the main fabric of suit construction. This area is highly suspect of damage and requires close routine maintenance checks.
- Double knees and double elbows. I recommend that the CPS used by hazardous material teams be purchased with the added double knee and elbow features to give additional material strength. Firefighters must work in hostile environments and often kneel on rungs, grates, or surfaces that can abrade the suit fabric.
- Suit zippers. Store suits with zippers in the closed position. Have talcum powder available to aid in sticky zipper problems.
- Fire boots/chemical compatibility. Some types of fire boots may not be compatible in a liquid spill or hazardous materials and can fail.
National Transportation Safety Board recommendations
The NTSB believes that standards are needed for the construction and testing of CPS suits and protective face masks used by emergency response personnel in the handling of hazardous material emergencies. There are projects underway to improve the usefulness of CPS suits, but the effects are not fully coordinated.
Most fire departments, as well as emergency response agencies, look to the NFPA for guidance concerning protective clothing. The NTSB believes that the NFPA is the logical place for such standards to be developed. Therefore, the NTSB recommends that the U.S. Coast Guard, the Federal Emergency Management Agency (FEMA), the Environmental Protection Agency (EPA), and NIOSH work with the NFPA and the ASTM in the development of standards for design and construction of chemical protective suits.