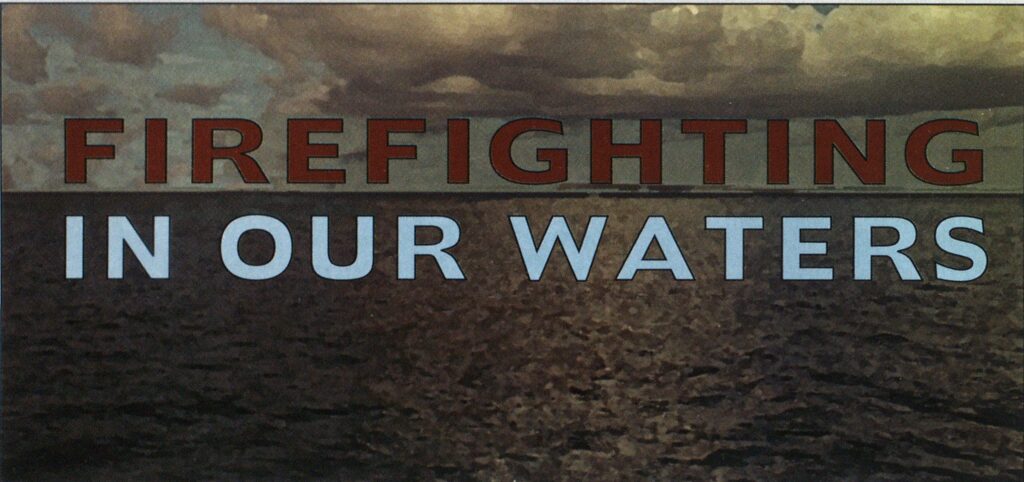
The Drillboat Algonquin Fire
FIREFIGHTING IN OUR WATER

The Great Lakes-American Joint Venture is under contract with the Army Corps of Engineers to deepen the Kill Van Kull waterway connecting Ports Newark and Elizabeth with New York Harbor. The contract calls for the drilling and blasting of bedrock on the channel bottom to facilitate dredging by mechanical means. Three drill barges—the Drillboat Algonquin, the Drillboat Hudson River, and the Drillboat #8— accomplish this drilling and blasting. Each of these drillboats consists of three independent drillframes that travel on a rail on one side of the barge. Holes are drilled in the bedrock and filled w ith a Class B explosive called Pourvex® (a line of water gel explosives whose performance is equal to or better than dynamite). A high detonation-pressure (HDP) booster, a Class A explosive, is placed on top of the Pourvex and then detonated using electric blasting caps.
On June 10. 1993, the City of New York Fire Department (FDNY) experienced a fire on the drillboat Algonquin involving machinery. diesel fuel, and hydraulic oil. This fire was directly impinging on a 1,000-gallon tank approximately half-filled with Pourvex.
INITIAL RESPONSE
Shortly before 1400 hours, a fire w>as discovered on drillframe A of the Algonquin. operating approximately 2,000 feet west of the Bayonne Bridge. The drillboat crew attempted to extinguish the fire using portable C0 fire extinguishers. This proved ineffective on the rapidly spreading fire. The drillboat crew abandoned the drillboat using the Joint Venture’s crew boat. FDNY was notified.
Three engine companies, two ladder companies. one battalion chief, one marine company, and the tactical support unit were dispatched. As additional information was being received by the Richmond (Staten Island) communications office, the supervising dispatcher added the hazardous-materials unit and an additional marine company to the response assignment.
The U.S. Coast Guard, with assistance from the New York Police Department’s (NYPD) Harbor Unit, closed the channel to traffic. While awaiting the arrival of the two -marine companies, FDNY’s Division 8 formulated a plan of attack using information being processed on shore by the hazardousmaterials unit. Flames were seen impinging on the storage tank containing the Pourvex liquid, and it was known that “day boxes”— containers holding small working amounts of blasting caps and HDP boosters removed from the explosives magazines—were in the vicinity of the fire but were not yet involved. The fire, fed by ruptured fuel lines that supplied diesel fuel to the compressor, engulfed the air compressor and the control cab. All responding units were informed of the conditions on the barge.
ATTACK STRATEGY
The incident commander implemented the following strategy:
Marine Company 9 (the Firefighter) would cool the explosives magazines on the barge using the reach and large capacity of its forward monitor and one monitor located above the pilot house. After cooling the magazines, it would circle the barge and attempt to extinguish the fire on drillframe A and simultaneously cool the Pourvex storage tank.
While this was being accomplished, Marine Company I (the Harvey), would be supplied with firefighters from an engine company, the hazardous-materials unit, and Rescue 2. A launch would transfer firefighters and equipment from shore to the Harvey.
After the fire was knocked down and the explosives magazines and surrounding areas on the barge were sufficiently cooled, the fireboat Harvey would come astern of the Algonquin and place the haz-mat and rescue companies aboard the barge. Two handlines would be stretched by those units from manifolds located on the tireboat. The hazmat unit would stretch a foam handline and extinguish remaining fire in and around the compressor and the control cab, while the rescue unit would stretch a 2M-inch handline as protection for the haz-mat and also to cool down adjacent surfaces, if necessary.
A battalion chief was to supervise operations on board the Algonquin. The operations officer maintained his position aboard the Firefighter, which remained on station approximately 150 feet off the starboard side of the Algonquin, prepared to use its monitors to protect the members operating on board the barge, if necessary.
The strategy proved successful. The fire was knocked down and the explosives cooled; handlines deployed from the Algonquin were effectively used for mop-up and member protection; and the fuel supply to the compressor and the hydraulic supply line from the hydraulic storage tank were shut down, aiding the final extinguishment of the fires. After consultation with the officer of the haz-mat unit, it was decided to allow representatives of the Great LakesAmerican Joint Venture board the Algonquin to shut down the electric generators on the barge. The noise level created by these generators severely hampered effective verhal communications between members operating on the barge.


(Photos by Tony Carannante, Staten Island Advance.)

After the noise level was reduced, members of the Army Corps of Engineers, the NYPD’s bomb squad, and the FDNY’s explosive unit were permitted access to the barge. They inspected the magazines and day boxes; and while they were deemed to be in a safe condition, the FDNY explosives unit ordered that the Pourvex be removed from the barge and all caps and boosters returned to their appropriate magazines and removed as well. The fire department explosives unit coordinated the removal of the explosives with Joint Venture personnel. FDNY stood by until the Pourvex was removed.
These actions were completed on June 10. The next day, however, a loaded hole had to be detonated after a crane freed the drill steel from the bottom and a diver inspected the loaded shot. This detonation was supervised by members of the FDNY explosives unit. The detonation concluded fire department operations at the Algonquin drill barge incident.




(Photos by author.)
CAUSE OF FIRE
Two theories have been proposed relative to the cause of the fire. One theory is that the fire began with a leak in a diesel fuel line at the air compressor. A charred fuel line that appears to have been split was found at this location. Ignition could have been caused by any of several hot elements within the air compressor. The fire then spread to the hydraulic equipment located in the front of the frame, possibly igniting residual hydraulic fluid and burning through the two-inch hoses, providing a rapidly flowing fuel supply from the elevated hydraulic fluid storage tank.
The second theory has the fire starting in the hydraulic system underneath the control cab and being spread by wind to the air compressor. This theory is still being examined because the hydraulic equipment in the forward portion of the frame has no obvious source of heat such as an engine exhaust manifold, as is the case in the first theory. The cause of the fire was still under investigation at the time of this writing.
DISCUSSION/LESSONS REINFORCED
- Material safety data sheets for Pourvex and HDP boosters indicate that fires involving these materials should not be fought. However, the tank containing the Pourvex was wrapped with an insulating blanket, and it appeared to be protecting the tank shell from flame impingement. It was felt that by using the large volumes of water from the fireboat, operating a safe distance away, the tank could be sufficiently cooled and the flames could be driven away from the tank. This strategy was successful; the fire affected only the insulating blanket. The HDP boosters were in a location unaffected by the fire. Had they been involved, no attempt would have been made to board the barge or place personnel within 2,500 feet of it. Careful evaluation of all of the conditions present and the gathering of all of the information available are prerequisites when dealing with fires in or around explosives. Remember: Caution and restraint are musts.
- Incident command and planning were established on the shore, and operations were established on board the Firefighter, staffed by a deputy chief and a battalion chief. The Algonquin became a sector under the command of a battalion chief. Staging was also established on the shore. It is interesting to note that under the incident command structure utilized at this incident, the hazardous-materials unit was split between two functions. The majority of the company was utilized within the operations function on board the Algonquin, and two members of the company remained on shore and operated, under the planning function, as resource and technical specialists. In addition, technical specialists from the FDNY explosives unit and the NYPD bomb squad, while under the planning function, operated with sector Algonquin, reporting to the sector commander.
- Communications were difficult at this operation since portable radios could not be operated within 150 feet and marine mobile transmitters within 300 feet of the barge because of the presence of the blasting caps. Instructions had to be relayed to responding units via radio prior to their arrival at the scene or verbally when they arrived. When messages of a critical nature are transmitted to responding units, the message should not be acknowledged only with a “10-4,” but it also should be repeated to the sender to verify
- its proper receipt. Safety can be assured only if messages are received properly.
The loud noise levels on board the Algonquin created a very hazardous condition during the initial operations. Verbal communications were almost impossible; hand signals had to be used. If a heavy smoke condition had been present, one can only imagine the additional difficulties that would have been encountered. It is imperative that any unnecessary noise be eliminated as soon as practical to ensure effective communications.
- A thermal imaging camera carried by units of the Special Operations Command was used to monitor heat conditions of the explosives magazines and the Pourvex tank, determining hot spots and evaluating the cooling effect of the hose streams. It also was used to check compartment covers located beneath the drillframe for hot spots. It was feared that some of the burning diesel fuel may have entered these compartments through faulty hatches. The camera was used to determine if high heat was present in these compartments, indicating the possibility of fire, prior to opening the covers. The camera was used to check the decking around the compartment cover. No unusually high heat levels were indicated; and when the compartments were opened, it was confirmed that no fire had entered.
- Safety. Construction sites pose various safety problems, among them tripping hazards. These hazards should be identified; cordoned off w ith barrier tape, if necessary; and called to the attention of all responders. It may be necessary to position personnel at the hazards that pose serious threats. Aboveground safety hazards may include low clearance areas or protrusions, which also should be identified and marked, and live, unprotected electric lines that may be present in the immediate fire area. A safety officer should survey the site and make safety recommendations to command.
Units should familiarize themselves with the signals construction companies within their response areas use to indicate that blasting is to take place. This information should then be conveyed to other units within the department.
- Progress reports. Progress reports should be transmitted at frequent intervals. Departments should have guidelines stipulating the frequency of these reports. These reports w ill provide chief officers and department officials, as well as responding units, with a clear and accurate verbal picture of the conditions existing at the fire or emergency. Units monitoring radios while in quarters will find the information contained in these progress reports valuable should the unit be ordered to the incident. Progress reports should contain the following information:
— description of the fire building or emergency area.
— description of the exposures,
— life hazard and status of the searches,
— description of strategy and tactics and the deployment of the forces being used to control the situation, and


(Photos by author.)
— appraisal of probable results of the efforts to control the situation; if no estimate is given, it should be assumed that the outcome is in doubt.
• Corrective actions. The following steps are being taken by the Great Lakes-American Joint Venture to prevent similar situations from arising in the future:
— Remote fuel shutoffs have been installed on all three drillboats.
— Daily documented inspection of all fuel and hydraulic lines is now conducted.
— Automatic fire extinguishing systems are being installed on each air compressor. This system consists of ABC dry chemical containers activated at 300 degrees. In addition, a manual activation is provided.
— Fusible links have been installed on the diesel fuel supply lines. These links will activate at 165 degrees and shut off the supply of fuel to the compressors.
— Synthetic hydraulic fluid is now being used, eliminating the use of a petroleumbased product.
— Electricians have inspected all three drillboats and have rewired areas where necessary.
— Pressure washing to remove oily residues on all drill frames and surrounding deck areas has been completed.
— Remote activation of the drillboat’s horn is now provided. Buttons are being installed on the deck of each drillboat. These buttons will be used to signal fires or emergencies on board.
— Remote starting of fire pumps is to be accomplished by the use of a button located on deck. During the fire, smoke permeated the pump room, forcing the engineer to flee before starting the pumps.
Bibliography
1. C. W. Bahme. Fire Officer’s Guide to Dangerous Chemicals (Boston. Mass., National Fire Protection
Association, 1978). 133.
2. Communications Manual. New York Fire Department (New York. N.Y.. 1986) 8.4.5.
3. “Drillboat Algonquin Fire. Great Lakes Dredge and Dock Company Incident Report.” Great LakesAmerican Joint Venture, June 1993.