By LEONARD H. GUERCIA JR. and BOB HOLDSWORTH
Every day, fire and emergency medical services (EMS) professionals around the world respond to the medical needs of the sick and injured. An increasing number of patients being treated are infected with contagious diseases such as Ebola, the plague, and drug-resistant viruses. Federal worker safety regulations require that these emergency workers be protected from exposure to these and other diseases by limiting exposure to the patient’s blood and bodily fluids.
In the daily delivery of fire and EMS transport services, field crews also face the potential of patients contaminated from contact with hazardous materials or exposure to industrial accidents. For decades, the industry standard has been to use plastic wrap and duct tape to protect the inside of ambulances.
On average, getting the patient compartment of a unit completely covered and sealed with plastic sheeting and duct tape takes about two hours (on a good day). Of course, removing all the sheeting in a disposable suit and decontaminating the unit after a transport can take at least that long; duct tape and nitrile gloves never work well together.
Pursuant to Federal Occupational Safety and Health Administration standards, emergency departments should establish a decontamination procedure for EMS units that states, “If decontamination can be performed without interfering with essential life-saving techniques or first aid, or if a worker has been contaminated with an extremely toxic or corrosive material that could cause severe injury or loss of life, decontamination must be performed immediately.”1
Per this procedure, we created a one-size-fits-all product that could minimize confusion; simplify training; and eliminate the need to match the product with specific makes, models, or brands of ambulances, keeping costs down and making EMS agency inventory easier to manage. The final product is Biocell, a U.S.-patented, one-piece protection system made of lightweight, translucent plastic that slides into the patient compartment of an ambulance, creating a 360°-encapsulated patient environment.
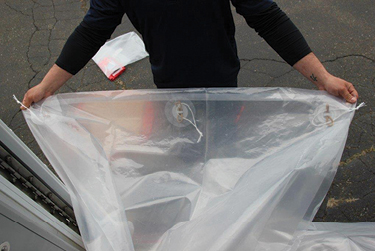
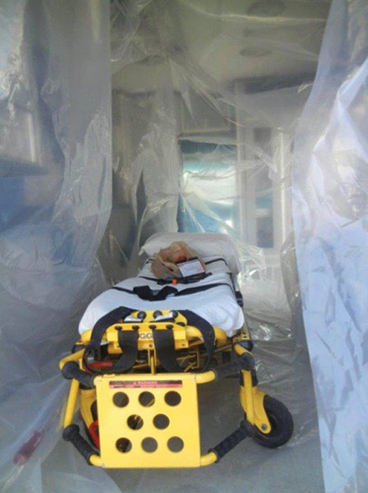
(1-2) Photos courtesy of Biocell APS.
To start its development, we met with a few local departments and showed them our prototype; the feedback was very positive. Fire- and hospital-based and investor-owned EMS providers all operate different types and brands of ambulances and could easily adapt the interior of their units to accommodate an identical prototype.
Next, we enlisted the help of former Old Saybrook (CT) Fire Department Chief J.T. Dunn as a consultant, and a plastics engineer from our group created, tested, and photographed several prototypes for proper fit and ease of deployment in several types of ambulances. Two of the biggest challenges we faced were how the various ambulance interiors would affect installation and determining the securing points for the corners and walls of the product. So, we went “back to the drawing board” and changed the location and number of installation connection points.
You can fasten Biocell easily to any interior surface with zip ties. It is made from skid-resistant, precut, translucent 0.6 millimeter-thick plastic (exceeding Centers for Disease Control and Prevention standards) and has a rear flap you can pull down after the patient is loaded.
In certain patient-condition dependent circumstances, you can use the transport’s heating and cooling system to improve the patient’s and crew’s comfort levels because the venting systems are outside the patient treatment environment. (You cannot accomplish this when using plastic sheeting and duct tape.)
In every prototype demonstration, emergency medical technicians (EMTs) deployed the Biocell unit in less than 20 minutes with minimal training on its initial use. Once a transport is completed, an EMT or a medic must remain in his disposable suit while a second EMT stays on the “clean” side of the Biocell; they then release the connection points, and the crew member in the disposable suit collapses the Biocell onto itself and pulls it into the biohazard box that comes in the kit. The biohazard box is then sealed and safely transported to the biohazard handling facility at the destination hospital for destruction.
You can also deploy the Biocell in trailers, rescue vehicles, and urban search and rescue tents and even on free-standing frames to deploy to decon and treatment facilities quickly.
Reference
https://www.osha.gov/SLTC/hazardouswaste/training/decon.html.
LEONARD H. GUERCIA JR., M.A., EMT-P, is a 29-year emergency medical services (EMS) veteran and the chief operating officer of Ambulance Protection Systems, LLC. Guercia was the director of EMS and public health preparedness for the Connecticut Department of Public Health for nine years and is the deputy emergency manager for Wallingford, Connecticut.
BOB HOLDSWORTH is a veteran paramedic and entrepreneur and founder of the Holdsworth Group. He is the author of Wading into Chaos: Inside the Life of a Paramedic and is a co-author of Secrets of Peak Performers Wealth Creating Strategies from the World’s Most Successful Entrepreneurs.