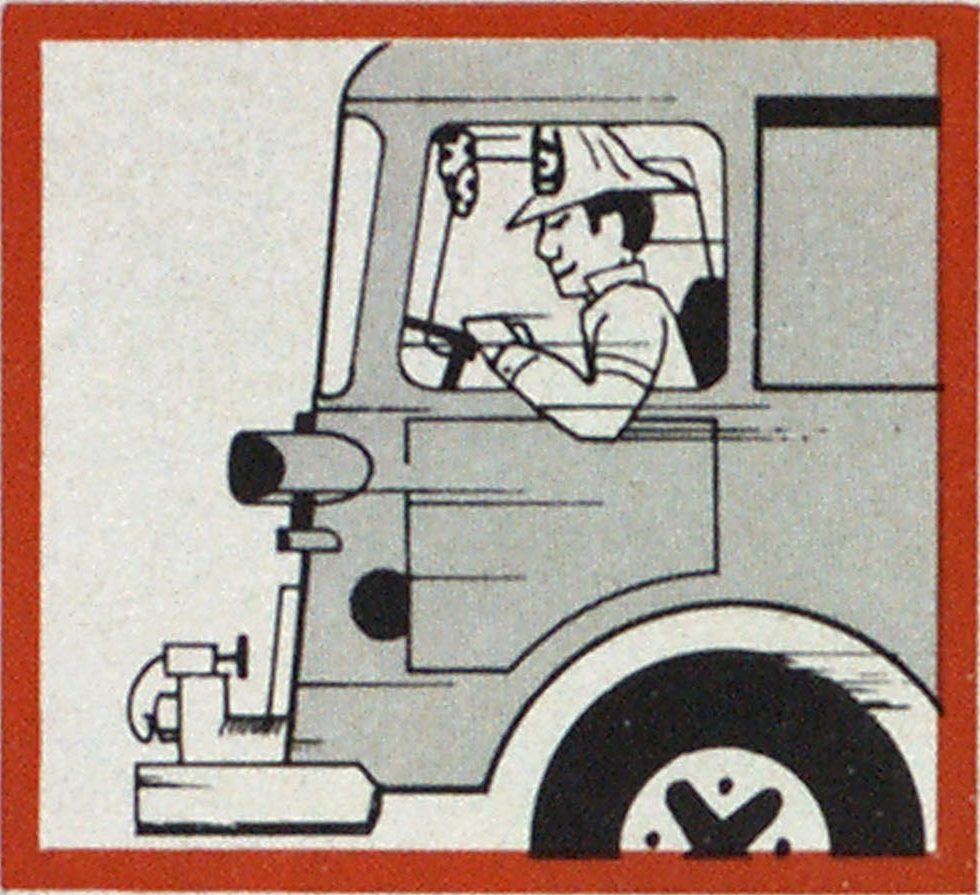
AUTOMATIC TRANSMISSIONS
APPARATUS/EQUIPMENT
Making the fire apparatus driver’s job a little less complicated

If we look back at a typical pumper response in 1925, we would see a driver/ engineer fighting a big wooden steering wheel as he dodges ruts and chuckholes and horse-drawn carts while shifting through his three gears. If he is lucky, his officer is hand-cranking the siren while holding Spot, the dalmatian, on the basket of booster hose behind the seat. There is no power steering, no sequential red lights, no traffic signal controllers, no radios or mechanical sirens to operate. Oh yes, there are also no air horns, windshield wipers or turn signals to worry about.
In 1983, much is changed. Our typical engineer now has at his control (hopefully) a 35,000-pound, 1500-gpm pumper with 350 or more horsepower that is capable of 60+ mph. Not only does he have to steer the unit, he now has to listen for changes in orders on his radio, be cognizant of the side or cross streets for our senior citizens who don’t hear or see well, while at the same time read and understand the multitude of gages we have added to the dashboard. Air horns and red, green and yellow warning lights also require his attention.
Let’s stop and regroup. Why have all this in an article on automatic transmissions?
The point is we, all of us who have had a say in fire apparatus design – users and manufacturers alike—have complicated the driver s job to the point we now must find ways to simplify his task. The automatic transmission is one way to accomplish this goal. With no shifting required and no clutch to operate, the driver can now concentrate on other areas in order to ensure his safe arrival on the fireground.
HORSEPOWER & TORQUE LIMITATIONS
I trust that everyone understands the automatic transmission’s basic function. But you may not realize that there are many different models to choose from. You, as a user, may not always be the one to make the choice because the engine you select will determine which automatic transmission you can use. This market is somewhat limited because Allison Division of General Motors is the only U.S. manufacturer of heavy-duty truck-type automatic transmissions. The chart shows some of the restrictions on Allison transmissions.
Allison also manufacturers other trucktype automatic transmissions that are not recommended for the fire service, namely, the MT-650 and the HT-750 series. These series have five forward speeds with a very low ratio which gives high rpm and horsepower at low speed for hill climbing. These also incorporate a torque converter which in some cases provides at 3:1 torque multiplication factor. Couple this with a low or reverse ratio that can go to 10.76:1 and you could end up with a torque multiplication that can exceed 30 to 1! If you pass that kind of torque along the driveline and through most midship pump gear cases you could have serious overload problems. This is the main reason that the MT-650 and HT-750 series are not recommended for fire apparatus.
In addition to the above, GMC, Ford and Chrysler offer their own automatics for pickups and small trucks. These smaller transmissions are found in up to 11,000pound GVW vehicles such as a K-35 Chevy or W-400 Dodge, commonly used as minipumper chassis. If the vehicle is twowheel drive (no transfer case), powering a power takeoff (PTO) booster pump can be a problem because these smaller transmission series have no PTO openings. As a user you now must specify a separate engine-driven pump or be faced with the expensive and sometimes very difficult task of installing a split shaft PTO. This size vehicle in a four-wheel-drive version can normally drive a PTO pump from the transfer case.
Vehicles of 15,000-pound GVW and larger will be using the Allison AT-545, MT-640 and HT-740 series. A PTO installation with these transmissions present no particular problems.
SPLIT SHAFT PUMPS & AUTOMATICS
When using a split shaft pump and an Allison transmission, a lockup system must be installed in order to ensure that the transmission will not move through the gears as you start your pumping operations, i.e., you want to be in direct drive for all pumping.
Lockup is achieved by an electrical signal being sent from a sensing device to a solenoid valve in the rear or converter section of the transmission. This valve opens and redirects the flow of hydraulic oil in the transmission. The pressure of this redirected oil shifts the transmission to fourth gear and prohibits any further shifting.
Proper lockup has been a problem area particularly in the 640 series. For the most part, these problems have been solved by Allison and the chassis and fire truck builders.
However, there are a good many pumpers that have a lockup sensing system which, when an operator is not careful in setting the apparatus in the pump mode, could contribute to a runaway fire truck.
OPERATOR ERRORS CAUSE RUNAWAY FIRE TRUCKS
What does this mean? Exactly what it says. Through operator error, a fire truck could rumble down the street striking objects in its path such as the chief’s car, the burning building or even worse! It has happened and nobody is happy when it does!
To understand what causes a runaway, we need to look at the drive train of a typical pumper.
Power is transmitted from the engine to the automatic transmission and to the pump gear case. When the pump is in a “road” mode, power is directed to the rear axle. A shifting mechanism system, usually a sliding gear and a collar or fork, moves the gear or collar from the rear or drive position to the front position for pumping.
Runaways occur when the gear does not move forward and the operator does not understand this. He has several signs to watch for: On new pumpers an “OK to Pump” green light on the dash and on the pump panel will illuminate when the shift occurs. With most pumps the speedometer also registers when pumping. If the proper shift sequence is followed and if the apparatus is standing still and the speedometer registers 1015 mph, the operator should be assured the pump shift has occurred and he can move to the pump panel for a safe pumping evolution.
But what about those occasions where the shift has not taken place, the operator ignores the telltale signs and moves to the pump panel to open the throttle. He is now an accident looking for a place to happen! Let’s examine what could have caused the situation.

Most experts agree that a great deal of torque can be applied to the drive train system if the apparatus’ parking brake is applied prior to the unit coming to a full stop. When this torque is not released, even though the dashboard pump shift control is moved to the proper position for pumping, the actual shift cannot take place. Shifting the truck transmission to neutral before engaging the pump and pausing 3 to 5 seconds should give the drive train sufficient time to be released from the torque bind and therefore allow proper pump shift.
Caution: Automatic transmissions have an inherent shift delay. If an operator rapidly shifts from drive to neutral, engages the pump and shifts immediately back to drive there is a possibility that without a 3 to 5-second pause in neutral, the drive train torque cannot be released and the pump shift cannot take place. When the operator at the panel starts to increase the throttle, at some point he will overcome the parking brake system and then … the unit starts to move.
How do we prevent this? The first and foremost method to prevent runaways is to provide better operator training. We must stress and reemphasize the methods that one should use and the telltale signs one should recognize when making a shift from road to pump.
The second way the fire service can help is to ensure that the method used to sense lockup is automatic and that lockup is called for just as soon as the operator engages the pump mode. Why is this so important? It is generally felt that if lockup is accomplished and the pump doesn’t make the proper shift, the apparatus will be in fourth gear and will probably stall rather than overcome the parking brake as the rpm is increased. Almost every fire truck builder today uses a system that, when the operator activates the pump mode, lockup is immediately called for. This has not always been the case because little was known about the hazards of apparatus runaways in the early days of automatic transmissions.
If you have older units that don’t have the “OK to Pump” lights, you should have them installed as soon as possible. All of the midship pump manufacturers offer a light kit which can be easily retrofitted by any competent mechanic.
Next you should very carefully determine the method that is used to tell the transmission to go into lockup mode. If your lockup sensor is using the in-gear indicating light switch, or a manual lockup valve, you should have this converted to the new automatic method as soon as possible. We need to stop fire truck runaways and we need to do it now!
WHAT ARE THE COSTS?
Just in case you are wondering, there is an additional cost when you specify an automatic transmission over a manual version. This additional cost is: AT-545, $1500; MT-643, $4500; MT-644, $5000; and HT-740, $8500. These figures are approximate but they could be used in budgeting for your next apparatus.
There is no question that the automatic transmissions have simplified the operation of our apparatus. Obviously, we have recognized this because approximately 95 percent of custom apparatus and well over 60 percent of commercial apparatus are currently being equipped with automatic transmissions. I think they are good for the fire service and I think they are here to stay. Learning to live with automatic transmissions will enable us to get the most from our apparatus and manpower for many years to come.